In the realm of precision manufacturing, heavy structural fabrication stands as a pillar of strength. It encompasses the creation of large, complex structures that form the backbone of various industries. In this comprehensive guide, we’ll delve deep into the intricate world of heavy structural fabrication. We will explore the various fabrication processes, the complexity involved, challenges faced, material selection, applications across industries, and how precision engineering is transforming this sector. So, tighten your hard hat, as we embark on a journey into the heart of heavy structural fabrication.
Heavy Structural Fabrication: An Overview
What Is Heavy Structural Fabrication?
Heavy structural fabrication is the process of manufacturing large and complex structures from metal components, often involving the assembly of beams, columns, trusses, and other structural elements. These structures serve as the foundation for a wide range of industries, from construction and infrastructure to oil and gas, aerospace, and more.
Different Types of Heavy Fabrication Processes
Heavy structural fabrication involves several specialized processes, each tailored to meet specific project requirements. Let’s explore some of the key fabrication methods:
Welding
- Process: Welding involves the fusion of two or more metal pieces to create a strong, cohesive joint. Common welding methods include MIG (Metal Inert Gas), TIG (Tungsten Inert Gas), and arc welding.
- Complexity: Welding large, heavy structures requires precision to ensure the integrity of the welds, especially in critical load-bearing components.
- Challenges: Controlling heat input, avoiding distortion, and ensuring consistent quality across long seams are common challenges.
- Measures to Overcome: Advanced welding techniques, automated systems, and stringent quality control checks help overcome these challenges.
- Applications: Shipbuilding, bridges, industrial machinery, and oil rigs.
Cutting and Machining
- Process: Cutting and machining involve shaping metal components through techniques such as plasma cutting, laser cutting, and CNC (Computer Numerical Control) machining.
- Complexity: Achieving precise cuts and intricate shapes is essential, especially when fabricating components that must fit together seamlessly.
- Challenges: Maintaining tight tolerances and minimizing material wastage can be challenging in large-scale projects.
- Measures to Overcome: Advanced cutting and machining equipment, computer-aided design (CAD), and optimization software help enhance precision.
- Applications: Structural steel components, heavy equipment parts, and aerospace components.
Forming and Rolling
- Process: Forming and rolling involve shaping metal plates and sheets into curved or bent components using hydraulic presses and rolling machines.
- Complexity: Achieving the desired curvature while maintaining structural integrity is crucial.
- Challenges: Controlling springback (elastic recovery after bending) and ensuring uniform curvature are common challenges.
- Measures to Overcome: Precision tooling, computer simulations, and iterative testing are employed to overcome challenges in forming and rolling.
- Applications: Curved steel beams for architectural structures, tanks, and pressure vessels.
Material Selection in Heavy Structural Fabrication
Selecting the right material is a critical aspect of heavy structural fabrication, as it directly impacts the structure’s strength, durability, and performance. Below is a comparison table of common materials used in heavy structural fabrication:
The choice of material depends on factors like structural requirements, environmental conditions, and project budget.
Material | Composition | Strength (MPa) | Corrosion Resistance | Applications |
---|---|---|---|---|
Carbon Steel | Iron + Carbon | 250-700 | Low | Construction, bridges, machinery |
Stainless Steel | Iron + Chromium, Nickel | 520-2,100 | High | Chemical plants, food processing, tanks |
Aluminum | Aluminum | 70-700 | High (Aluminum alloys) | Aerospace, transportation, marine |
Corten Steel | Iron + Chromium, Copper | 350-500 | High | Architectural, outdoor structures |
Complexity and Challenges in Heavy Structural Fabrication
Heavy structural fabrication projects are known for their intricate nature and significant challenges. These projects often involve the construction of massive structures that serve as the backbone of various industries, from infrastructure to energy production. To gain a better understanding, let’s explore the complexity and challenges in this field:
Complexity involved:
- Size and Scale: Heavy structural fabrication often involves the construction of enormous structures such as bridges, skyscrapers, and industrial facilities. For instance, the Akashi Kaikyō Bridge in Japan, one of the world’s longest suspension bridges, has a main span of approximately 1,991 meters (6,532 feet).
- Precision and Tolerances: Achieving precise measurements and tight tolerances is essential in heavy structural fabrication. For example, the construction of large-scale energy facilities may require welding tolerances as low as 1 millimeter (0.04 inches) to ensure structural integrity.
- Integration of Components: These projects often entail the assembly of thousands of individual components. For instance, assembling a modern aircraft carrier involves integrating over 500,000 components, including steel plates, pipes, and electrical systems.
- Safety Standards: Safety regulations in heavy structural fabrication are stringent. According to the Occupational Safety and Health Administration (OSHA) in the United States, fatalities in the steel erection industry have decreased significantly, from 79 in 2001 to 17 in 2019, highlighting the importance of adhering to safety standards.
Challenges
- Tolerances and Precision: Maintaining tight tolerances is challenging. A study conducted by the American Welding Society (AWS) found that nearly 10% of welding defects are attributed to deviations from specified tolerances.
- Material Handling: Handling and transporting large and heavy components pose significant safety risks. In 2020, the U.S. Bureau of Labor Statistics reported that “struck by object” was a leading cause of fatal occupational injuries, emphasizing the importance of proper material handling.
- Quality Assurance: Ensuring the quality of welds and other critical connections is crucial. Research by the International Journal of Advanced Manufacturing Technology revealed that implementing automated welding systems can reduce weld defects by up to 80%.
- Environmental Factors: Heavy structures often face exposure to harsh environmental conditions. According to the National Oceanic and Atmospheric Administration (NOAA), extreme weather events, such as hurricanes and typhoons, have been increasing in frequency and intensity in recent years, necessitating durable, corrosion-resistant materials and coatings in fabrication.
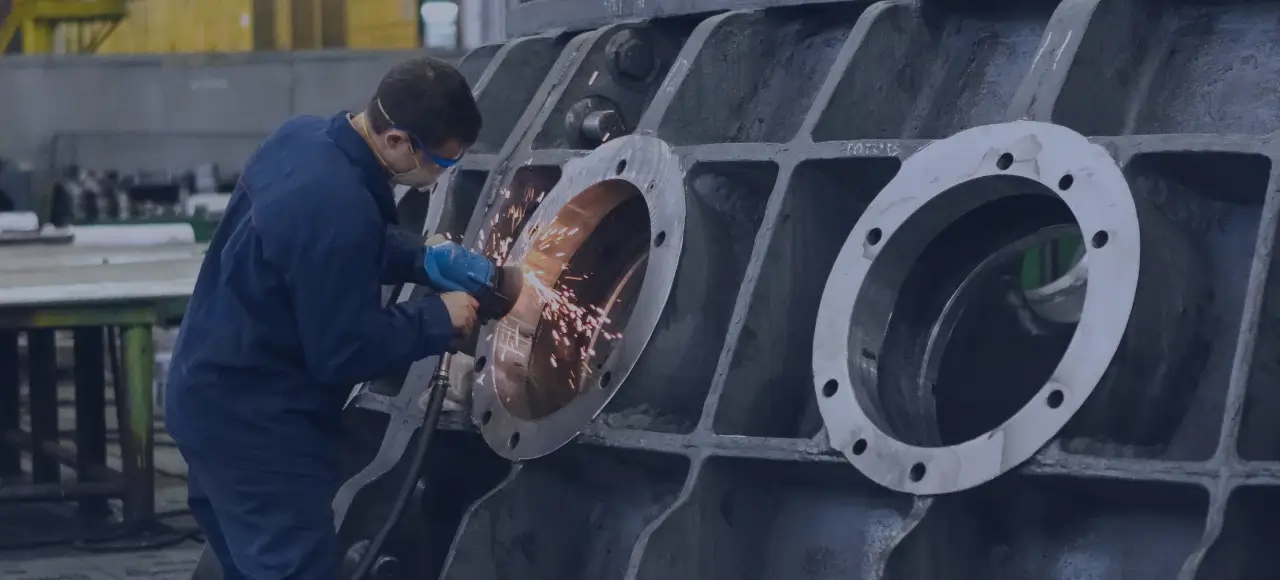
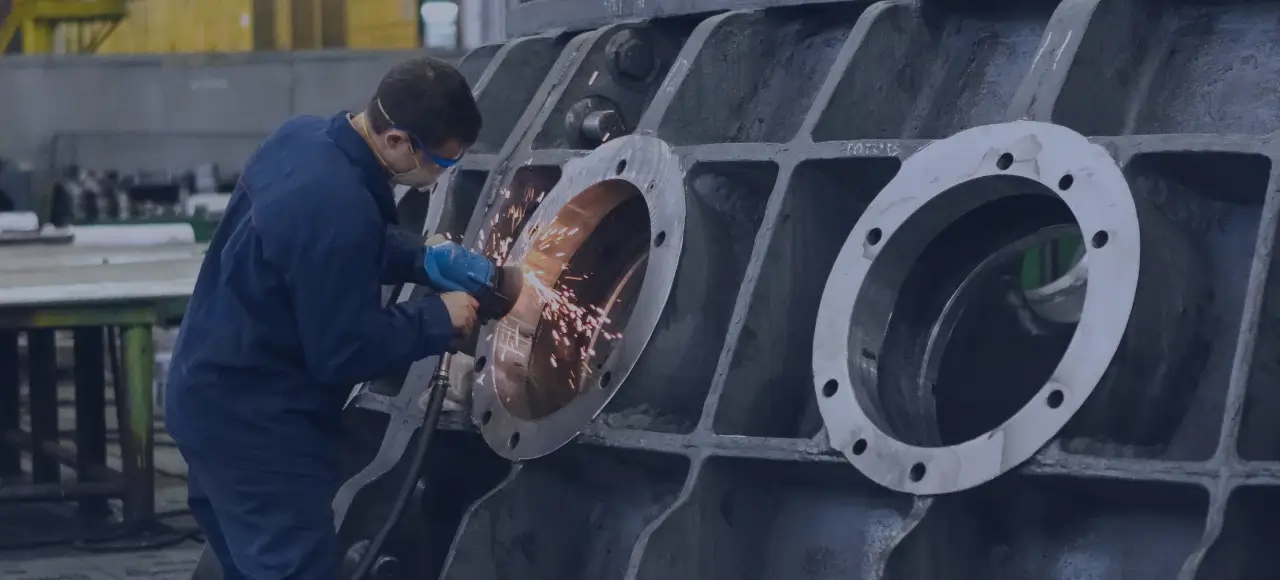
Measures to Overcome Complexity and Challenges
To overcome the complexity and challenges in heavy structural fabrication, manufacturers employ several measures:
- Advanced Technology: Invest in state-of-the-art equipment and technology, such as CNC machines, robotic welders, and CAD software, to ensure precision and efficiency.
- Skilled Workforce: Train and retain skilled welders, machinists, and fabricators who understand the nuances of heavy structural fabrication.
- Quality Control: Implement rigorous quality control processes at every stage of fabrication, from material inspection to final assembly.
- Simulation and Testing: Use computer simulations to predict and optimize the behavior of structures under different loads. Conduct physical testing to validate designs.
- Material Selection: Choose materials that align with project requirements, considering factors like strength, corrosion resistance, and environmental conditions.
Applications of Heavy Structural Fabrication
Heavy structural fabrication finds application in various sectors, each benefiting from the unique capabilities it offers:
- Construction and Infrastructure: Large-scale construction projects, such as bridges, skyscrapers, and stadiums, rely on heavy structural fabrication for their foundational components. For example, steel beams and columns provide the framework for these structures, ensuring stability and durability. Example: The Golden Gate Bridge in San Francisco, California, is an iconic structure constructed using heavy structural fabrication techniques.
- Oil and Gas Industry: In the oil and gas sector, heavy structural fabrication plays a vital role in the construction of offshore platforms and drilling equipment. These structures must withstand extreme conditions, making the choice of materials and fabrication techniques critical. Example: Offshore oil rigs are complex structures fabricated using heavy materials and advanced welding techniques to withstand the harsh marine environment.
- Aerospace and Aviation: Aerospace relies on precision manufacturing, including heavy structural fabrication, to produce aircraft components and structures. These components must meet stringent safety and performance standards. Example: The fuselage of a commercial airliner is an example of a complex aerospace structure fabricated using advanced materials and machining.
Conclusion
Heavy structural fabrication is a cornerstone of modern infrastructure and industry. Understanding the processes, complexities, challenges, and measures to overcome them is essential for successful project execution. By selecting the right materials, employing advanced technology, and partnering with experienced manufacturers like Zetwerk, you can ensure that your heavy structural fabrication projects meet the highest standards of quality and precision.
Navigating the intricacies of heavy structural fabrication requires expertise and resources. Zetwerk, a leader in precision manufacturing, offers a comprehensive solution for your heavy structural fabrication needs. With a global network of certified manufacturers, advanced technology, and a commitment to quality, Zetwerk can ensure that your project meets the highest standards of precision and reliability. Partnering with Zetwerk provides you with access to the latest trends and innovations in heavy structural fabrication, ensuring the success of your projects in the year and beyond.




FAQs
Heavy structural fabrication offers superior strength, durability, and customization compared to other construction methods. It allows for precise engineering and can withstand extreme conditions, making it ideal for critical infrastructure projects.
Quality assurance in heavy structural fabrication involves rigorous inspections, testing, and adherence to industry standards. Choose a reputable fabrication partner with a history of successful projects and a commitment to quality.
In 2023, heavy structural fabrication is seeing increased automation, the use of advanced materials like high-strength alloys, and a focus on sustainability. Digital twin technology and data analytics are also playing a significant role in optimizing fabrication processes.