Roll forming is a cost-effective and flexible process that helps various industries acquire metal profiles for different applications. This process involves running the metal sheet through rollers to flatten, bend, and shape it in the desired profile. Nearly any metal, steel, aluminum, titanium, copper, and others can be roll-formed as long as the materials possess enough properties to tolerate the roll forming without incurring damage. Roll forming stainless steel is highly versatile and allows you to cut, punch, or weld in the line and perforate, emboss, or perform any finishing processes for the end product.
Once the required shape is achieved with the roll-forming process, the metal is cleaned, anodized, detailed, and cut into the required length. In this blog, we’ll explore the advantages of roll forming and its application across various industries.
Understanding Roll Forming
Before delving into its applications, let’s first understand roll forming. Roll forming is a continuous metal shaping process that involves feeding a metal strip through a series of contoured rolls. These rolls gradually shape the metal into a desired cross-sectional profile. The process is highly precise and efficient and can be used with various metals, including steel, aluminum, and copper.
The primary components of a roll forming line include an uncoiler to feed the metal strip, a series of forming rolls, and a cut-off press or shear to cut the profile to the desired length. Roll forming machines can have numerous roll stations, producing complex shapes in a single pass.
Advantages of Roll Forming
- Cost-Effectiveness: Roll forming offers significant cost savings, especially for long production runs. The efficiency and speed of the process reduce labor costs and tool wear, making it an economical choice for businesses looking to optimize their manufacturing processes.
- Reduced Secondary Operations: The precision achieved through roll forming often eliminates the need for secondary operations such as welding or additional machining. This reduces production time and lowers the overall cost of manufacturing.
- Material Utilization: This process helps minimize material waste since it generates minimal scrap. This contrasts with other fabrication methods like stamping or machining, where material wastage can be much higher.
- Reduced Lead Times: The efficiency and speed of roll forming contribute to shorter lead times, which can be crucial for meeting tight production schedules and customer demands.
- High Strength and Structural Integrity: Metal parts re-shaped through roll forming exhibit high structural integrity due to the cold-forming process, which maintains the material’s inherent strength properties. This makes them suitable for applications that require durability and load-bearing capabilities.
- Customization and Innovation: Manufacturers can innovate and create custom shapes and profiles to meet unique requirements, allowing for product differentiation and competitive advantages. Therefore, roll forming is not limited to standard profiles.
- Complex Shapes and Profiles: Experts can create a wide range of complex shapes and profiles through light gauge steel roll forming, from simple channels and angles to intricate, custom designs. This versatility makes it suitable for various applications and industries.
- Consistency and Precision: From ensuring precision to consistency in shapes along the entire part length. This consistency is crucial for industries where tight tolerances and uniformity are paramount, such as construction, automotive, and aerospace.
- Quick Tooling Changes: The roll forming setups are adaptable and allow for relatively quick tooling changes. This means manufacturers can switch between profiles or adjust without significant downtime or costly retooling.
- Scalability: Roll forming can accommodate various production volumes, from small batches to large-scale runs. This scalability makes it a versatile choice for companies of all sizes.
- High Production Efficiency: The advantages of cold-formed steel over hot rolled Steel always win regarding high-volume production. It can produce large parts with minimal downtime, making it an ideal choice for industries requiring mass production. The continuous nature of roll forming minimizes interruptions and increases overall productivity.
- Material Variety: Manufacturers can use roll forming with various materials, including steel, aluminum, copper, stainless steel, alloys, and composites.
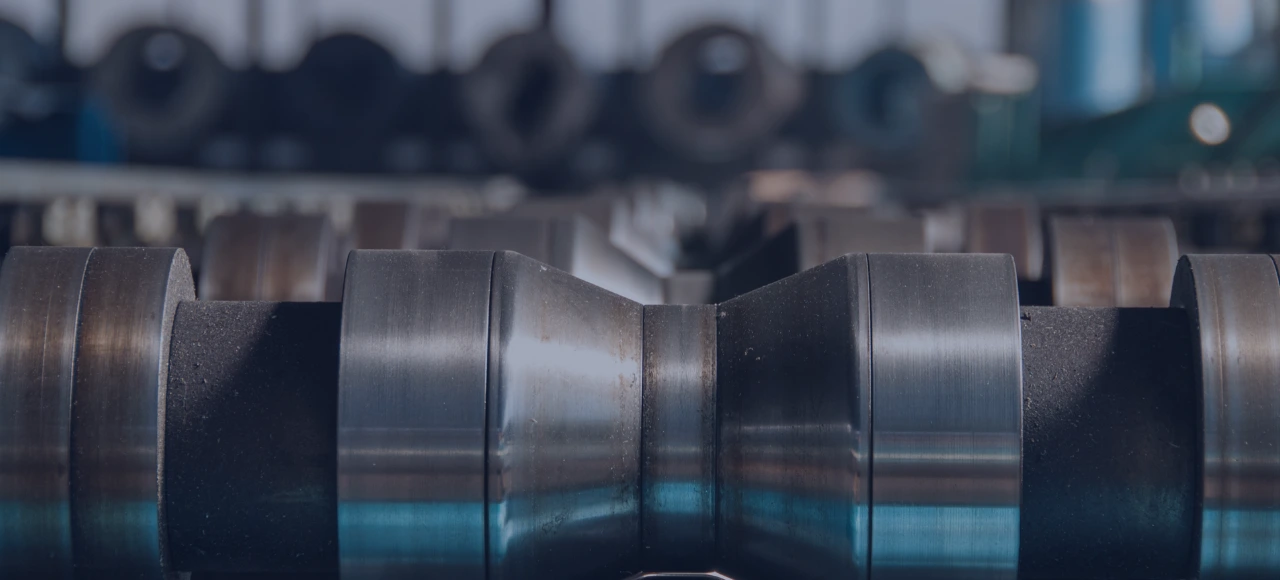
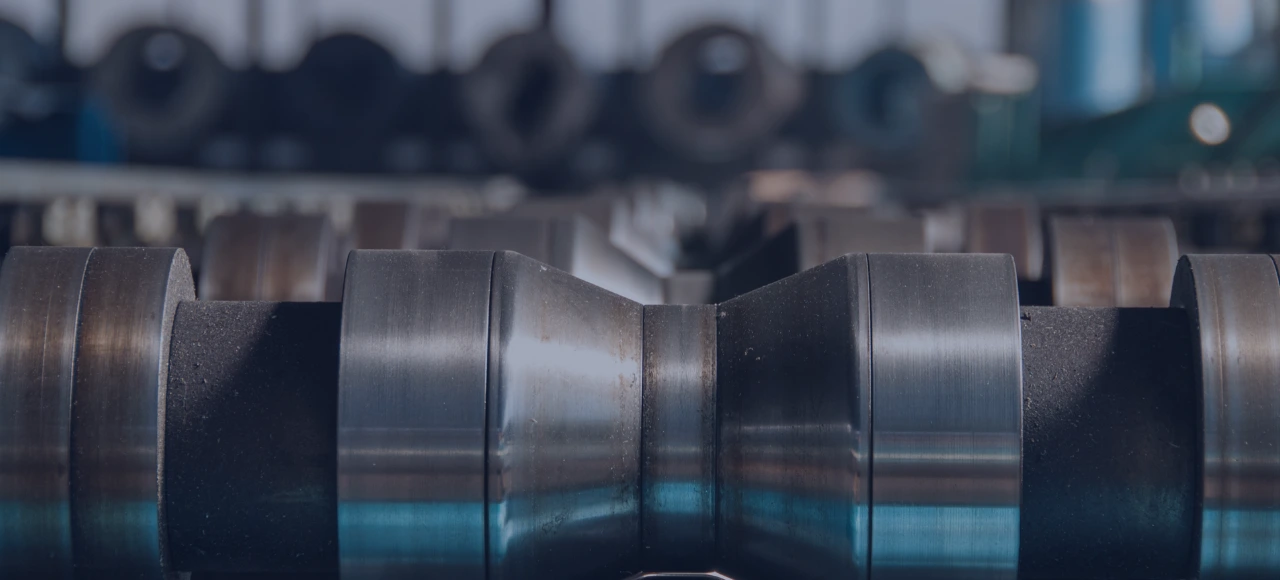
Roll forming Applications Across Industries
The roll forming process addresses the needs of desired metal shape requirements of a plethora of industries. This includes
In the Automotive Industry
The automotive industry is one of the most significant beneficiaries of roll-forming technology. It is used extensively for manufacturing various components, such as:
- Bumpers: Roll formed steel channels are commonly used for automotive bumpers. The process allows for creating precise shapes and contours, enhancing aesthetics and functionality.
- Door Frames: Door frames made through roll forming are lightweight yet sturdy, providing structural integrity while minimizing vehicle weight. This helps improve fuel efficiency and overall performance.
- Roof Rails: Roof rails on cars are often produced using roll forming. They must be durable and weather-resistant, making roll-formed profiles an ideal choice.
- Chassis Components: Steel sections with roll forming are used to construct vehicle chassis, contributing to rigidity and safety.
In Construction
The construction industry relies heavily on roll forming for various structural and architectural elements. Some key applications include:
- Metal Roofing and Siding: Roll forming creates corrugated and standing seam metal roofing and siding panels. These materials are durable, weather-resistant, and easy to install.
- Studs and Tracks: Roll forming stainless steel studs and tracks are essential in framing interior walls. Roll-formed sections provide the necessary strength and dimensional stability.
- Purlins and Girts: In metal building construction, roll-formed purlins and girts are favored components. They combine cost-efficiency with impressive load-bearing capacity, contributing to the structural integrity of such buildings.
- Flashings and Trim: Customized flashings and trim components are roll-formed to fit specific architectural designs, providing functionality and aesthetics.
Aerospace Applications
In the aerospace industry, precision is paramount, and roll forming meets this demand exceptionally well. Some applications include:
- Aircraft Frames: Roll forming produces lightweight yet strong profiles for aircraft frames, reducing fuel consumption and enhancing performance.
- Seat Tracks: Seat tracks made with roll forming provide adjustability and strength for passenger and crew seats in aircraft.
- Aerospace Tubing: Roll-formed tubing is used to construct hydraulic and fuel lines, ensuring reliable performance under extreme conditions.
Consumer Goods and Appliances
Roll forming extends its reach to consumer goods and appliances, where it plays a vital role in shaping components for various products, including:
- Shelving Systems: Metal shelves made from roll-forming processes are commonly used in retail and warehouse settings due to their durability and adjustability.
- Garage Doors: Roll forming stainless steel creates the tracks and panels for garage doors, ensuring smooth operation and longevity.
- HVAC Components: Ductwork, brackets, and other HVAC components are often roll-formed, providing efficiency and reliability.
Light gauge steel roll forming could be the perfect solution if your fabrication, construction, or engineering projects demand a consistent supply of precision-formed components derived from sheet metal. In addition to this, Zetwerk can meet all of your rolling needs. We bring our years of excellence to your table to meet your needs quickly and efficiently. Please contact us to see how we can help with your roll forming project.




FAQs
Roll forming is a metalworking process that shapes various metals like steel, aluminum, copper, and stainless steel into desired profiles. It can also be adapted for specific plastics and composite materials, making it versatile in manufacturing.
It is a continuous and highly efficient process, making it ideal for producing long lengths of profiles with consistent shapes. Stamping and forging, while suitable for some applications, may involve more material waste and require secondary operations.
Roll forming is widely applied across automotive, construction, aerospace, consumer goods, and renewable energy industries. Its adaptability to different engineering requirements makes it a versatile and indispensable manufacturing process in modern production.
Roll-formed products often contribute to sustainability efforts. For example, lightweight roll-formed components in the automotive industry can improve fuel efficiency, while metal roofing made through roll-forming is durable and has a long lifespan, reducing the need for replacements.
Yes. Roll-formed profiles can be highly customized to meet specific engineering requirements. The number of roll stations, material choices, and tooling adjustments allow for precise shaping and tailoring of profiles to unique designs and functions.