Introduction
The evolution of custom sheet metal enclosures in modern manufacturing has transformed the way industries design and produce components for various applications. From precision cutting techniques to advanced joining methods, manufacturers have continually pushed the boundaries of what is possible. This article explores the advancements in sheet metal fabrication, highlighting key techniques and design considerations that have revolutionized the industry.
Advancements in Custom Sheet Metal Enclosures
From sheet metal manufacturing to its joining, every process has observed a massive evolution with the development of technologies. Below are few areas where the development has changed the concept of sheet metal enclosures.
Evolution of materials used in sheet metal fabrication
Over the years, there has been a significant evolution in the materials used for custom sheet metal enclosures. Traditionally, steel was the primary material choice due to its strength and durability. However, advancements have led to a wider range of options such as aluminum and stainless steel. Aluminum offers lightweight properties while maintaining sufficient strength, making it ideal for applications where weight reduction is essential. Stainless steel provides excellent corrosion resistance, making it suitable for environments with high moisture or chemical exposure.
Precision cutting techniques and their impact on enclosure design
Precision cutting techniques play a crucial role in achieving intricate designs and precise dimensions for custom sheet metal enclosures.
- Laser cutting has emerged as one of the most popular methods due to its ability to provide clean and accurate edges. This thermal process uses focused laser beams to cut through various metals with exceptional precision.
- Waterjet cutting is another technique that utilizes a high-pressure stream of water mixed with abrasive particles to effectively cut through different metals. It offers greater flexibility by allowing complex shapes and designs to be easily achieved.
- Plasma cutting uses a plasma torch to swiftly cut through metal sheets, enabling manufacturers to create intricate shapes quickly and accurately.
Bending and forming innovations for complex enclosure shapes
Custom sheet metal enclosures often require complex shapes and forms that cannot be achieved through traditional bending methods alone. To meet these demands, manufacturers have developed innovative bending and forming techniques.
- CNC machining and bending involves using computer numerical control technology to accurately bend sheet metal into desired shapes and angles. This automated process ensures consistency and precision, resulting in high-quality enclosures.
- Press brake forming and stamping utilizes a hydraulic or mechanical press brake to create bends and folds in sheet metal. This technique allows for the production of multiple bends in a single operation, improving efficiency and reducing lead times.
- Roll forming gradually shapes sheet metal into a continuous and uniform profile by passing it through a series of rollers. This method is ideal for creating enclosures with consistent cross-sections, such as tubing or channels.
- Hemming involves rolling over a sheet metal edge onto itself to create an area with two layers. This technique offers improved strength and aesthetics, making it suitable for enclosures that require a seamless appearance.
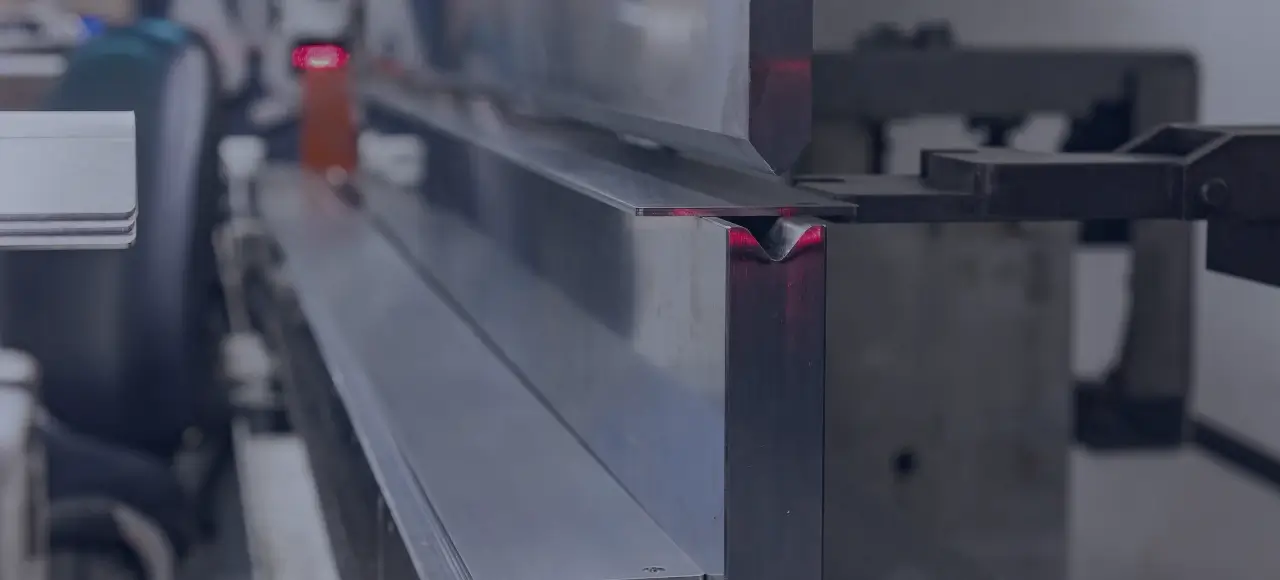
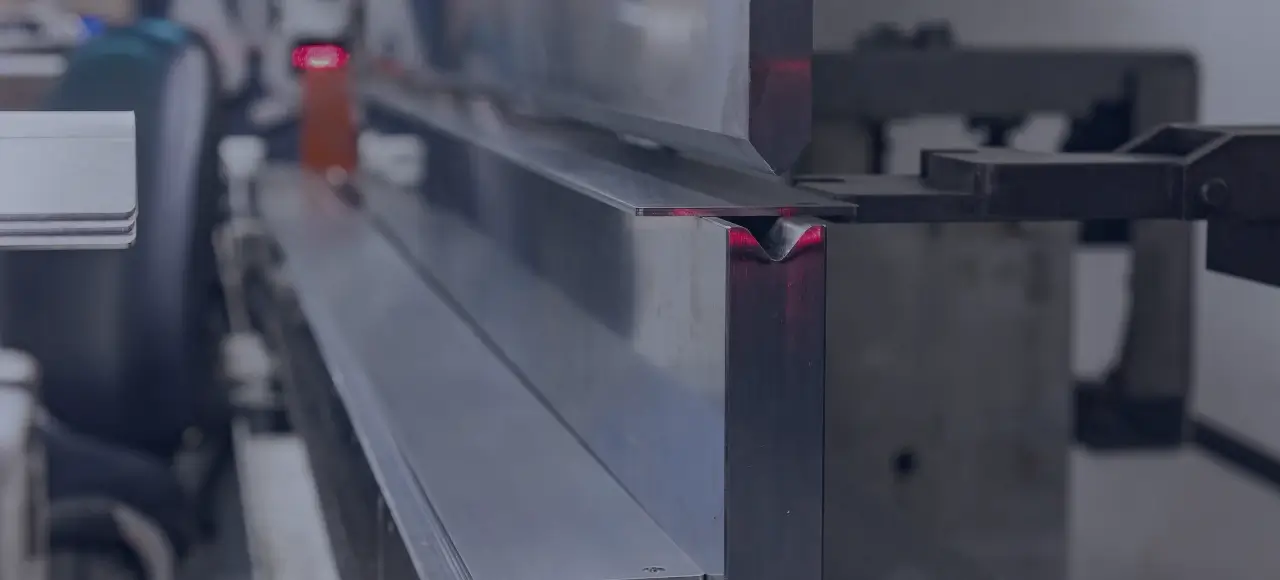
Joining Techniques for Enhanced Enclosure Strength
- Welding: Advancements in welding techniques have revolutionized the industry by allowing manufacturers to achieve seamless joints with exceptional strength. TIG (Tungsten Inert Gas) welding uses a non-consumable tungsten electrode to produce the weld. MIG (Metal Inert Gas) welding is another commonly used technique that utilizes a continuous wire electrode and shielding gas to protect the weld from atmospheric contamination. Spot welding is often employed for joining thin sheets of metal together, typically using electrodes on opposing sides of the joint to generate heat through resistance when an electric current passes through them.
- Riveting: Riveting is a popular method used in custom sheet metal enclosures for its ability to securely join two or more metal sheets together. Blind rivets are commonly used in sheet metal enclosures as they provide a strong connection without requiring access to both sides of the assembly. Solid rivets offer increased strength and reliability compared to blind rivets but require access to both sides of the assembly for installation. They are commonly used in heavy-duty or high-stress applications.
- Adhesive bonding: Adhesive bonding has gained popularity in custom sheet metal enclosure fabrication due to its ability to create lightweight yet durable connections. Specialized adhesives are used to bond metal components together, eliminating the need for traditional fasteners.
Finishing Options for Customized Enclosure Aesthetics
- Powder coating: Powder coating is a popular finishing option for custom sheet metal enclosures due to its durability and versatility. It involves applying a dry powder coating to the surface of the sheet metal, which is then cured through a heat process.
- Anodizing for enhanced corrosion resistance: Anodizing is another finishing technique commonly used in custom sheet metal enclosure fabrication. It involves creating an oxide layer on the surface of aluminum through an electrochemical process.
- Plating: Plating is a finishing option used to improve both aesthetics and protection against corrosion in custom sheet metal enclosures. It involves covering the metal surface with a thin layer of another metal through electroplating or electroless plating processes.
Design Considerations in Modern Sheet Metal Enclosure Manufacturing
When designing custom sheet metal enclosures, considering manufacturability is crucial to optimize production efficiency. A few factors must be considered while designing such objects.
- Designing for manufacturability to optimize production efficiency
- Importance of designing with tolerances in mind
- Streamlining assembly processes through thoughtful design choices
Final Thoughts
Sheet metal enclosures are now essential for every infrastructure and industrial set-up. With many options and significant customizations, it can serve various purposes. With the right design considerations and material selection, organizations can make the most of these products.
Looking to procure custom sheet metal enclosures? Explore Zetwerk’s comprehensive manufacturing services, including precision machining, fabrication, casting, forging, surface treatment, and more. Visit the Zetwerk Knowledge Hub to access articles on related topics that enhance your understanding of custom sheet metal enclosures.




FAQs
Sheet metal fabrication offers durability, cost-effectiveness, versatility in manufacturing processes, high-quality precision parts, repeatability, and automation possibilities. Custom sheet metal enclosures provide flexibility in design and control over the end product.
Design considerations such as material selection, tolerances, simplifying assembly processes, self-locating features, and thermal management greatly impact the quality of custom sheet metal enclosures. They ensure strength, durability, efficiency in production, accurate alignment during assembly, and proper heat dissipation.
Yes! Custom sheet metal enclosures can be designed to withstand harsh environments. With proper material selection and finishing options like powder coating or plating for corrosion resistance, they can protect sensitive components from extreme temperatures, moisture, dust, vibration, and other challenging conditions.
Various industries can benefit from custom sheet metal enclosure fabrication. These include electronics for PCB enclosure designs with specific requirements, construction for durable housing solutions, aerospace for lightweight yet robust components, energy for equipment protection, automotive for precision-engineered assemblies; and more.