Stainless steel stands out as an exceptional material with diverse and extensive usability. From kitchen appliances and cutlery to architectural structures and industrial equipment, stainless steel’s durability and corrosion resistance make it a sought-after choice in many industries. Behind the scenes, stainless steel metal fabrication shops are crucial in turning raw stainless steel into functional and aesthetically pleasing products.
In this article, we discuss the art and science behind stainless steel fabrication shops, exploring the processes, techniques, and innovations that make them indispensable.
The Raw Material: Stainless Steel
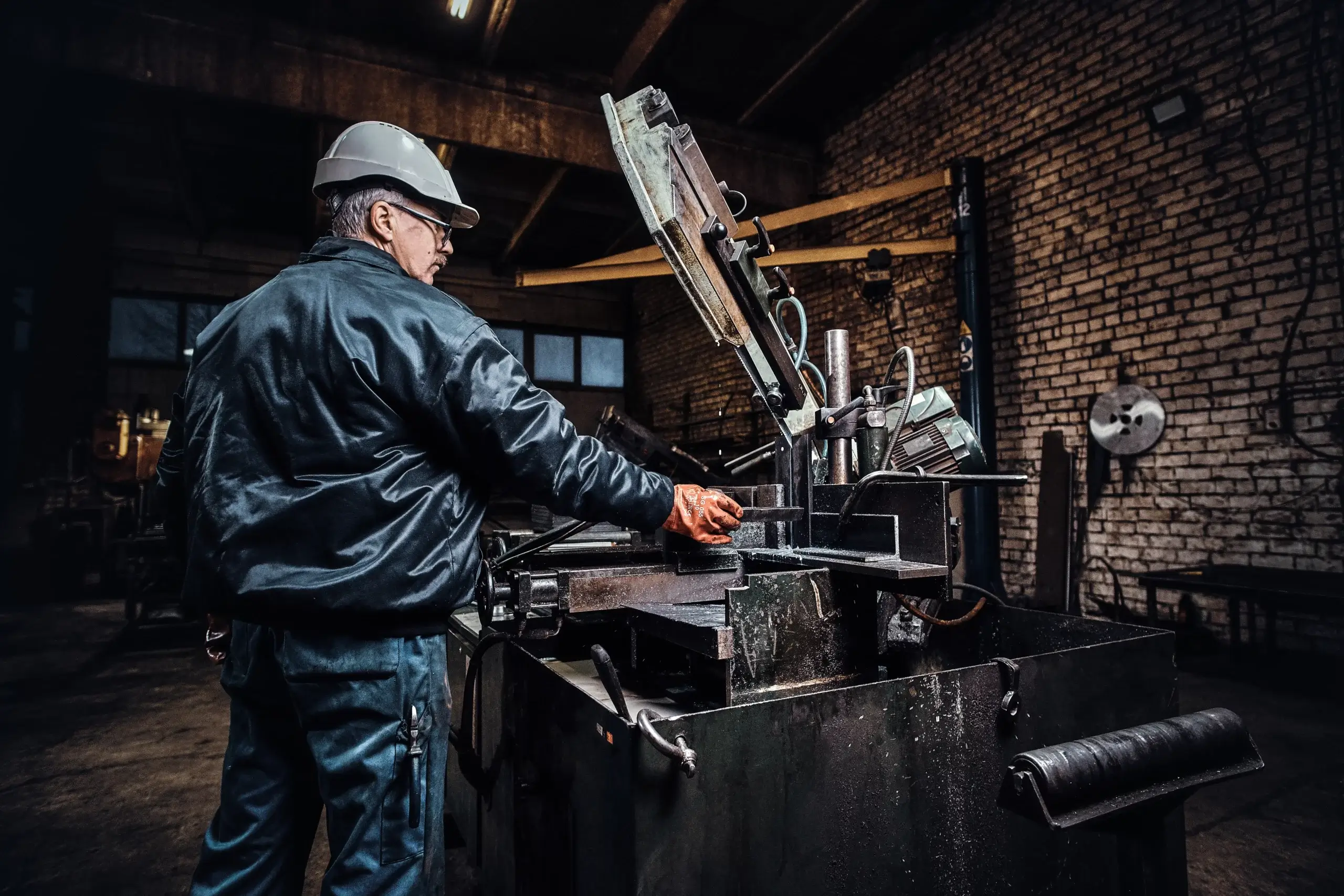
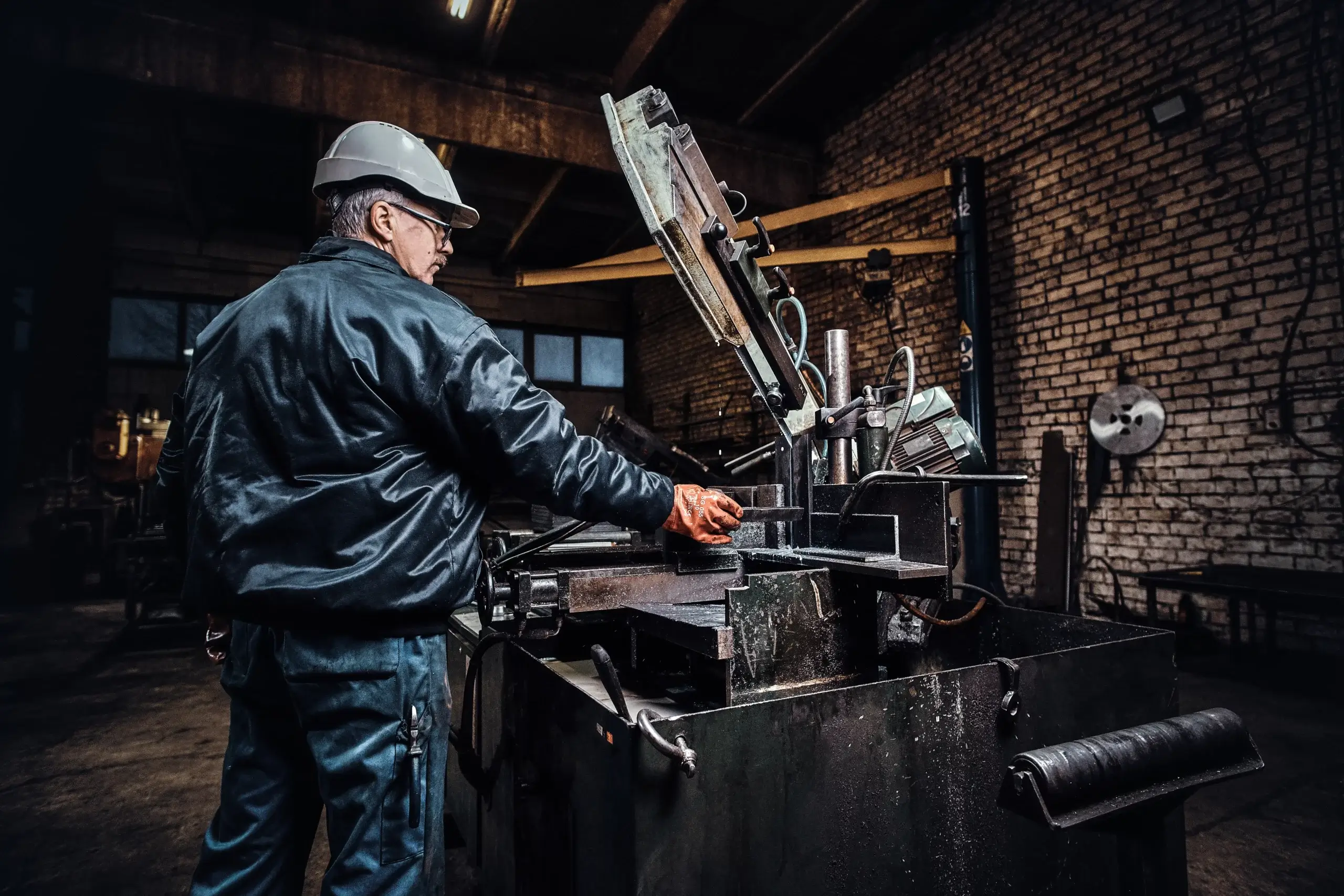
Stainless steel, a corrosion-resistant alloy primarily composed of iron, chromium, and other elements, forms the foundation of the fabrication process. This alloy’s distinct properties make it a favorite in various industries, including construction, automotive, aerospace, and healthcare. The art of stainless steel metal fabrication starts with sourcing the right grade and thickness of stainless steel to meet the specific requirements of the project. The science involves understanding the material’s properties and its behavior under various conditions.
Precision Cutting
One of the essential steps in stainless steel fabrication is precision cutting. This is where a fusion of artistic skill and scientific knowledge takes center stage. Laser cutting, plasma cutting, waterjet cutting, and other techniques are used to create precise shapes and sizes. The art lies in the craftsmanship required to program the machines and handle them carefully, ensuring that the cuts are clean and accurate.
On the other hand, the science involves understanding the material’s behavior during cutting, including factors like heat generation, thermal distortion, and the potential for burrs.
Forming and Bending
Once the stainless steel has been cut into the desired shapes, the metal fabrication shop must often bend and form the material to create three-dimensional structures. This process requires a deep understanding of the metal’s properties, including its elasticity and tensile strength. Artistic finesse is needed in creating complex, aesthetically pleasing forms, while science comes into play when calculating the optimal bend angles and ensuring structural integrity.
Welding
Welding is a crucial step in stainless steel metal fabrication, as it joins different pieces to form a cohesive structure. Artistic welding involves the welder’s skill in creating clean and visually appealing weld seams. The science aspect entails understanding the metallurgy of stainless steel to ensure that the welded joints are solid and resistant to corrosion. Techniques such as TIG (Tungsten Inert Gas) welding are commonly used to achieve precise and high-quality welds in stainless steel fabrication.
Polishing and Finishing
The art of stainless steel metal fabrication continues after the structural aspects. The aesthetics of the final product are equally important. Polishing and finishing processes are essential to give stainless steel products their signature sleek and lustrous appearance. This step involves grinding, buffing, and applying various finishes like brushed, satin, or mirror. Achieving a perfect finish requires skilled artisans who know how to manipulate tools and machines and a deep understanding of the science behind abrasive materials and polishing techniques.
Quality Control and Inspection
Quality control is a critical aspect of stainless steel metal fabrication, blending both art and science. Skilled inspectors meticulously examine the finished products to ensure they meet design specifications and are defects-free. They use various tools and technologies, including ultrasonic testing and X-ray inspection, to verify structural integrity. This step requires a keen eye for detail, but it’s equally rooted in scientific knowledge to detect even the most subtle imperfections.
Innovation in Stainless Steel Fabrication
The world of stainless steel metal fabrication is continually evolving, driven by innovations in materials, technology, and techniques. Here are a few recent advancements that highlight the intersection of art and science in this field:
Advanced Alloys
One of the most significant innovations in stainless steel fabrication is the development of advanced alloys. Engineers and metallurgists have worked tirelessly to improve the material’s properties, creating specialized alloys that can thrive in even the harshest environments. These alloys include duplex, super duplex, and precipitation-hardening stainless steel.
Duplex stainless steels, for instance, offer higher strength and better resistance to stress corrosion cracking than traditional austenitic stainless steels. Super duplex stainless steels take this further, providing greater corrosion resistance and durability. These innovations in alloy development have opened up new horizons for stainless steel metal fabrication in offshore and marine applications, where extreme conditions are the norm.
Precision Laser Cutting
Stainless steel fab shops near me have also benefited from advancements in precision cutting technologies. Laser cutting, in particular, has become a game-changer in the industry. Laser cutting machines use high-intensity lasers to cut through stainless steel, offering unmatched accuracy and intricate detailing. This innovation has transformed how components are manufactured, making it easier to create complex shapes and designs with minimal waste.
Laser cutting is not only faster but also more cost-effective than traditional cutting methods, as it reduces the need for secondary processes like deburring. Moreover, it minimizes the risk of heat distortion, ensuring that the stainless steel retains its desirable qualities even after cutting.
3D Printing in Stainless Steel Fabrication
Integrating 3D printing or additive manufacturing into the stainless steel metal fabrication process has been another groundbreaking innovation. This technology allows for the creation of intricate components and structures that were previously impossible or cost-prohibitive to produce. Using powdered stainless steel and a laser or electron beam, 3D printers can build complex parts layer by layer with incredible precision.
The applications of 3D printing in stainless steel fabrication are vast. From aerospace components to medical implants, this technology opens up new possibilities for lightweight and highly customized stainless steel products. It not only reduces material waste but also shortens lead times, making production more efficient.
Corrosion-Resistant Coatings
While stainless steel is renowned for its corrosion resistance, ongoing innovation has led to advanced coatings that enhance this property even further. Coatings like PVD (Physical Vapor Deposition) and CVD (Chemical Vapor Deposition) have gained popularity for improving the aesthetic and functional qualities of stainless steel components.
PVD coatings create a thin, decorative layer on the stainless steel’s surface, offering a range of colors and finishes. This innovation has favored architectural applications, where stainless steel surfaces can be customized to match the design intent. On the other hand, CVD coatings offer superior wear and corrosion resistance, making them ideal for applications in extreme conditions, such as the chemical and petrochemical industries.
In Conclusion
In conclusion, the stainless steel fabrication shops within proximity represent more than mere workshops; they symbolize the convergence of creativity and technical prowess. These establishments serve as the meeting ground for skilled artisans and engineers, channeling the transformative power of a versatile alloy into a wide array of products that cater to various industries, enhancing the quality of our daily experiences. The fusion of art and science evident in these stainless steel fabrication shops attests to the ingenuity of the human spirit and the boundless potential of this exceptional material.
As an industry leader, Zetwerk remains dedicated to fostering innovation and excellence in stainless steel fabrication, aiming to redefine the standards of craftsmanship and technological advancement. Through our commitment to quality and forward-thinking solutions, we continue to support and elevate the stainless steel fabrication landscape, pushing boundaries and unlocking new possibilities for the industries we serve.




FAQs
Stainless steel fabrication is the process of cutting, bending, welding, and shaping stainless steel to create various products. It differs from other metalworking methods due to stainless steel’s unique properties, including corrosion resistance and durability.
Selecting the appropriate stainless steel grade involves factors such as the project’s environment, desired corrosion resistance, mechanical properties, and aesthetics. The choice plays a crucial role in the success of the fabrication.
Precision cutting and bending techniques involve methods like laser cutting and CNC bending. Understanding these processes is crucial for achieving accurate dimensions and maintaining the structural integrity of the final product.
Welding is vital for joining stainless steel components. Artisans use techniques like TIG welding to achieve clean and visually appealing welds while maintaining the material’s structural strength.
The industry continually evolves with advancements like digital design, CNC machining, 3D printing, and specialized coatings. Understanding these innovations helps fabricators stay competitive and meet the demands of modern projects.