In manufacturing, the ability to tailor products to specific needs is invaluable. Custom metal fabrication is a testament to this, offering bespoke solutions catering to the unique requirements of B2B OEMs and manufacturers.
At the heart of this process lies sheet metal stamping, a technique that has revolutionized how industries approach metalwork.
The Art of Customization in Metalwork
Custom metal fabrication is not just about bending and shaping metal. It’s about understanding the client’s vision and the end product’s functionality and ensuring that every piece fabricated aligns with these parameters. Whether it’s a specific alloy or a unique shape, custom sheet metal fabrication ensures the final product perfectly fits its intended application.
Why Customization Matters?
In today’s competitive market, off-the-shelf solutions often need to catch up. Industries demand components that can seamlessly integrate into their operations. Custom metal fabricators bridge this gap, providing parts that enhance efficiency, reduce wastage, and optimize performance.
Tools and Techniques
Modern custom metal fabrication employs a range of tools and techniques. While sheet metal stamping is a cornerstone, other methods like laser cutting, welding, and forming play crucial roles. The choice of technique often depends on the material used and the desired finish.
Choosing the Right Custom Metal Fabrication Manufacturer
Not all custom metal fabrication manufacturers are created equal. Choosing a partner who understands the industry’s nuances, can offer innovative solutions, and has a track record of delivering quality products is essential. Factors like experience, machinery, and client testimonials can offer insights into a manufacturer’s capabilities.
Sustainability in Custom Metal Fabrication
With growing environmental concerns, custom metal fabricators are adopting sustainable practices. This includes using recycled materials, minimizing waste, and employing energy-efficient methods. Such initiatives benefit the environment, enhance the brand’s reputation, and appeal to eco-conscious clients.
Delving Deeper: Custom Metal Fabrication for B2B OEMs and Manufacturers
Original Equipment Manufacturers (OEMs) and manufacturers in the B2B sector have unique needs. Their products are often at the heart of larger systems or integral components of complex machinery. As such, the demand for precision, durability, and functionality is paramount. This is where custom metal fabrication shines, offering tailored solutions that cater to these industries.
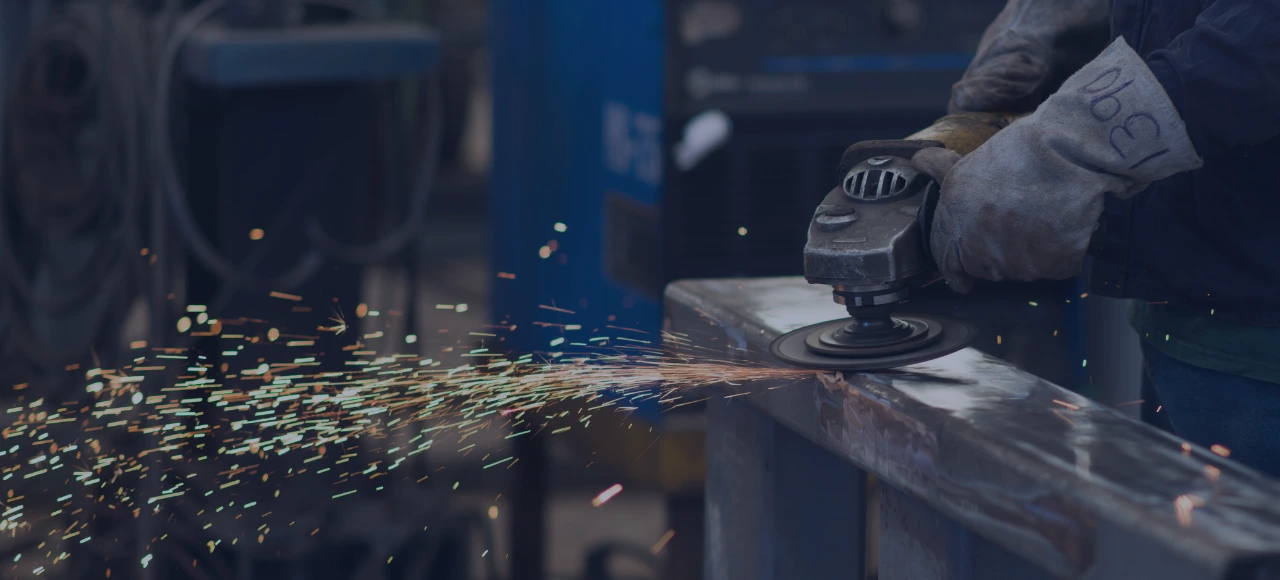
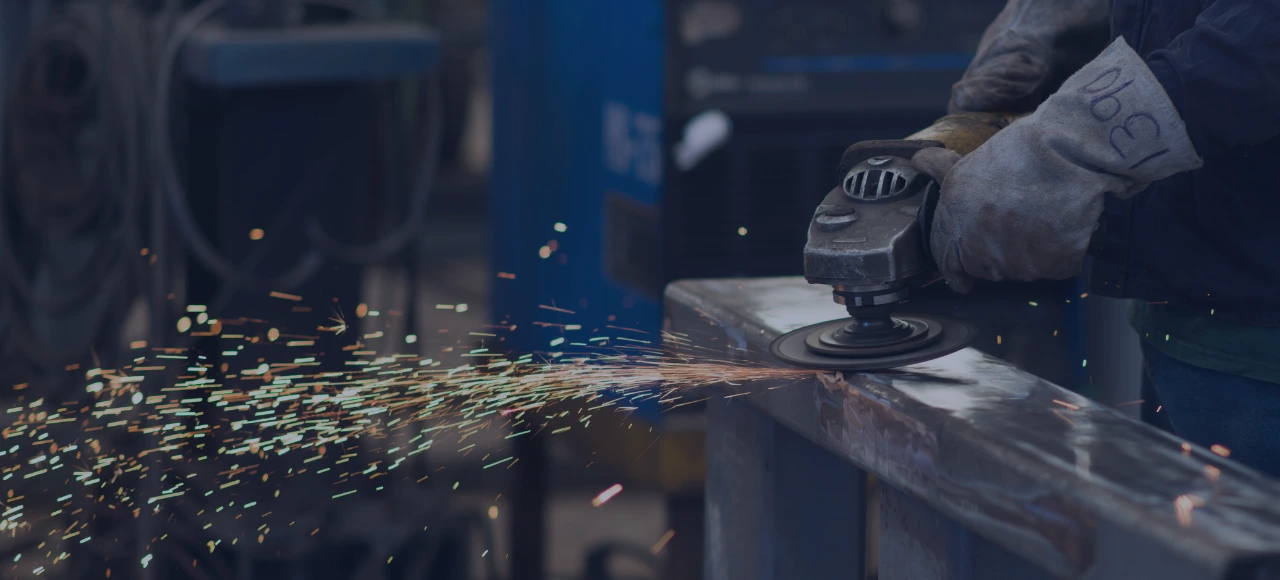
Custom Metal Fabrication: A Necessity for B2B OEMs
For B2B OEMs, the stakes are high. Their products are often part of critical systems, from automotive assemblies to industrial machinery. A slight deviation in a component’s dimensions or a minor flaw can lead to system failures or reduced efficiency. Custom metal fabricators understand these nuances and ensure that every piece they produce meets the exacting standards of OEMs.
The Role of Advanced Technologies
The world of custom metal fabrication has been transformed by technology. Advanced Computer Numerical Control (CNC) machines can produce incredibly precise components. CAD and CAM software allows for intricate designs that were once deemed impossible. These technologies ensure that custom sheet metal fabrication meets the rigorous demands of modern industries.
Material Selection in Custom Fabrication
The choice of material plays a role in custom metal fabrication. Depending on the application, manufacturers might opt for materials that offer strength, corrosion resistance, conductivity, or a combination of these properties. Custom metal fabricators possess the expertise to guide OEMs in selecting the ideal material for their needs.
Collaboration: The Key to Successful Custom Fabrication
One of the most overlooked aspects of custom metal fabrication is the collaboration between the fabricator and the client. Open communication ensures that the fabricator understands the client’s needs and can offer solutions that align with their objectives. Regular updates, prototype testing, and feedback loops are integral to this collaborative process.
Custom Metal Fabrication: Beyond the Basics
While we’ve delved into the processes and advantages of custom metal fabrication, it’s essential to understand its broader implications. For B2B OEMs and manufacturers, it’s not just about getting a tailored component. It’s about enhancing product efficiency, reducing lead times, optimizing costs, and ultimately, gaining a competitive edge in the market.
Future of Custom Metal Fabrication: Embracing Innovation
As industries evolve, so does the space of custom metal fabrication. Integrating advanced technologies like Artificial Intelligence and the Internet of Things paves the way for more innovative, more efficient fabrication processes. These innovations allow for real-time monitoring, predictive maintenance, and even automated design adjustments, ensuring that the final product is tailored to the present needs and future-ready. By embracing these technological advancements, custom metal fabricators are meeting the current demands of B2B OEMs and manufacturers and setting the stage for the next generation of metal fabrication excellence.
Custom metal fabrication emerges as a beacon of tailored excellence in dynamic manufacturing. It’s not merely about crafting metal but about understanding the intricate needs of B2B OEMs and manufacturers and delivering precision-engineered solutions. As industries continue to demand more tailored components, the expertise of custom metal fabricators becomes increasingly invaluable. Zetwerk, with its unwavering commitment to quality and innovation, stands at the forefront of this revolution, ensuring that businesses always have access to top-tier metal fabrication solutions that drive efficiency, reduce lead times, and foster market competitiveness.




FAQS
Custom metal fabrication offers bespoke solutions tailored to the unique requirements of B2B OEMs and manufacturers, with sheet metal stamping at its core.
In today’s competitive market, industries require components that integrate seamlessly into their operations. Customization enhances efficiency, reduces wastage, and optimizes performance.
Advanced technologies like CNC machines, CAD, and CAM software have transformed custom metal fabrication, allowing precision and intricate designs.
Collaboration ensures the fabricator understands the client’s needs, leading to solutions that align with their objectives, facilitated by open communication and regular updates.
The industry faces challenges like complex designs, tight deadlines, and cost constraints, but these can be managed with advanced software, efficient project management, and economies of scale.