Structural steel fabrication is a highly specialized process requiring precision and expertise. It begins with procuring raw steel materials, usually steel plates, sheets, or sections, which are cut, shaped, welded, and assembled to create structural components. These components are later transported to construction sites, where they are erected to form the framework of buildings, bridges, and other structures. The success of any construction project depends on the quality and accuracy of structural steel fabrication. Therefore, employing the proper methods and adhering to best practices is essential to ensure the final product’s safety, durability, and structural integrity.
Structural Steel Fabrication Methods
Design and Detailing
- This stage involves creating detailed plans, drawings, and specifications that outline the structure’s dimensions, load-bearing requirements, and other critical parameters.
- Design engineers and detailers use specialized software tools to model the structure and generate precise fabrication drawings.
- Advanced Building Information Modeling (BIM) software has revolutionized this stage, enabling multidisciplinary collaboration, clash detection, and accurate quantity take-offs.
- BIM allows stakeholders to visualize the entire structure and identify potential issues before fabrication starts.
Material Selection
- Choosing the right type and grade of steel is crucial for structural integrity and longevity.
- Structural steel is available in various grades, each with specific mechanical properties suitable for different applications. Engineers and fabricators must carefully select the steel material that meets the project’s requirements, including load-bearing capacity, corrosion resistance, and environmental factors.
- Common structural steel grades include A36, A572, A588, and A992. The choice of steel grade should consider factors such as the structure’s intended use, location, and exposure to environmental conditions.
Cutting and Shaping
- Laser cutting: Utilizes a high-powered laser beam to cut steel with precision, creating smooth edges.
- Waterjet cutting: Utilizes a high-pressure stream of water mixed with abrasive particles to cut through steel materials.
- Saw cutting: Employs circular or band saws to cut steel sections efficiently.
- Plasma cutting: Uses a high-velocity jet of ionized gas to cut through steel quickly and accurately.
Welding
- Shielded Metal Arc Welding (SMAW): Stick welding uses a consumable electrode coated in flux to create an arc that fuses the steel components.
- Gas Metal Arc Welding (GMAW): Also known as MIG welding, GMAW uses a continuous wire electrode and shielding gas to create a stable arc.
- Flux-cored Arc Welding (FCAW): Similar to GMAW, it uses a flux-filled wire electrode, eliminating the need for an external shielding gas.
- Submerged Arc Welding (SAW): Involves a granulated flux that blankets the welding area, protecting it from atmospheric contamination.
Quality Control and Inspection
- Visual inspections to identify surface defects and imperfections.
- Dimensional checks to ensure components meet design specifications.
- Non-destructive testing (NDT) methods, such as ultrasonic testing, magnetic particle testing, and dye penetrant testing, to detect hidden flaws or discontinuities.
- Welding inspections to verify the quality of welds, including weld size, penetration, and continuity.
- Material testing, including tensile and hardness testing, to verify the mechanical properties of the steel.
Surface Preparation and Coating
- Paint: Offers essential protection against corrosion and can be applied in various colors for aesthetic purposes.
- Galvanizing involves immersing steel components in molten zinc, creating a durable, corrosion-resistant coating.
- Powder coating: Provides a durable and aesthetically pleasing finish by electrostatically applying dry powder to the steel surface and curing it with heat.
Assembly and Erection
Once all components are fabricated, inspected, and coated, they are assembled into more significant sections or modules. These assemblies are then transported to the construction site for erection. Proper assembly and erection procedures are critical to ensure the structure’s stability and safety. This phase may involve using heavy machinery, such as cranes and lifts, to position and secure steel components.
Testing and Commissioning
After the structure is fully erected, it undergoes tests and inspections to verify its integrity and functionality. These tests may include load testing, deflection testing, and structural integrity assessments. Once the structure passes these tests, it is ready for commissioning and use.
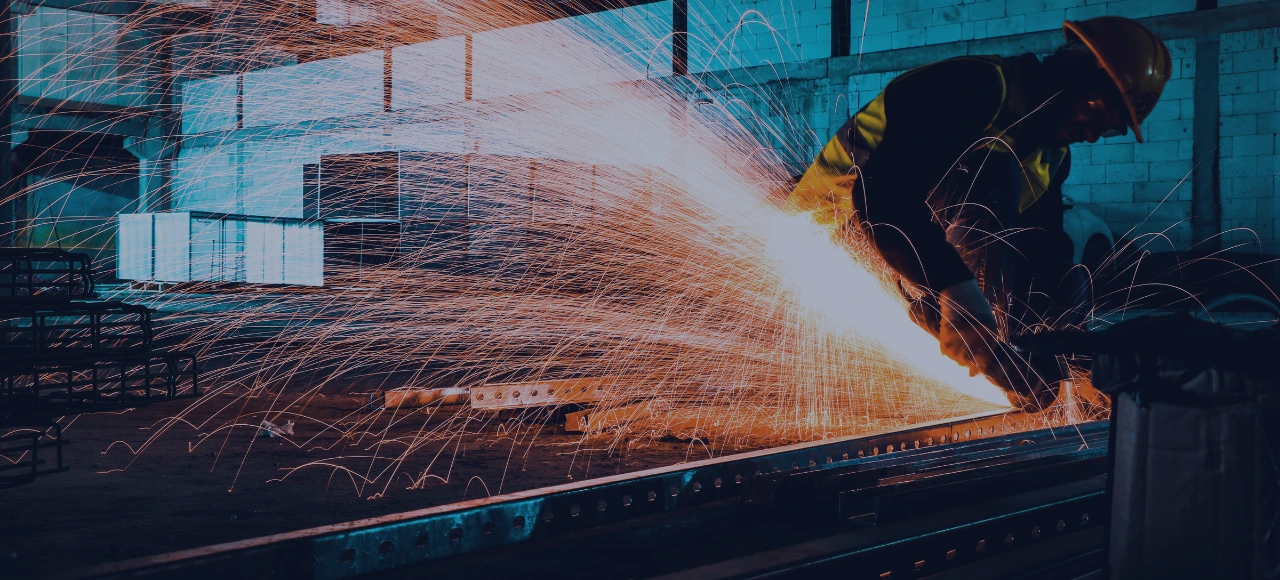
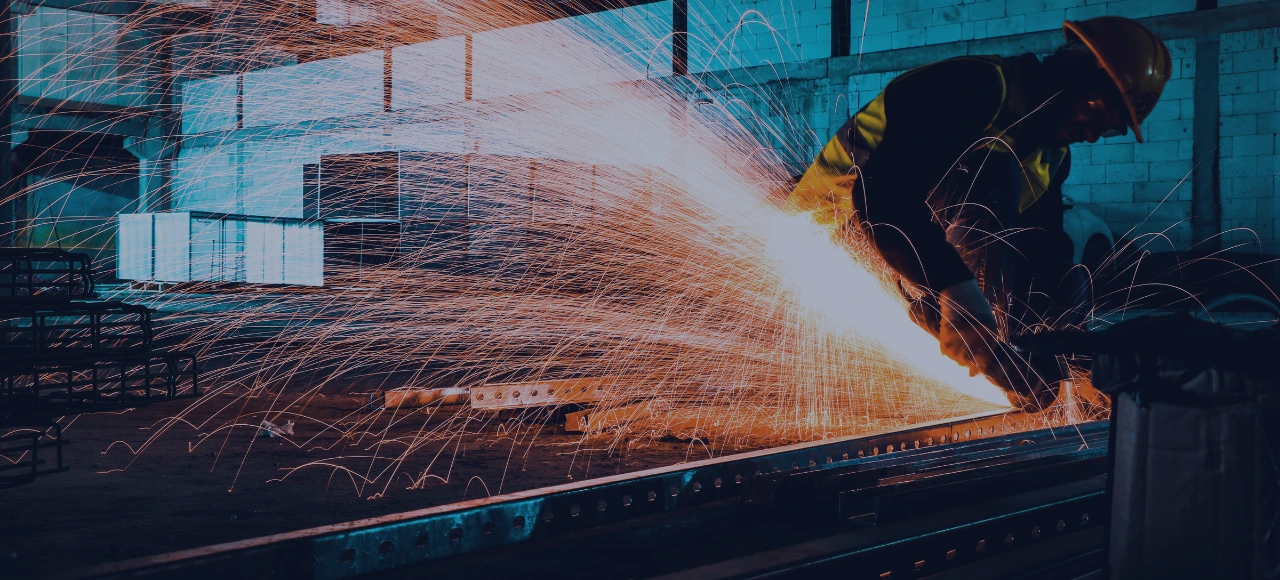
Best Practices In Structural Steel Fabrication
Quality Control
- Implement a comprehensive quality control program to ensure that every step of the fabrication process meets industry standards and project specifications.
- Inspect and verify the quality of incoming steel materials, including checking for proper certifications and documentation.
Skilled Workforce
- Employ skilled and certified welders, fitters, and fabricators trained and experienced in working with structural steel.
- Provide ongoing training to keep the workforce up to date with the latest industry standards and techniques.
Detailed Planning and Design
- Begin with a well-defined, detailed design with accurate measurements, material specifications, and assembly instructions.
- Plan the fabrication process carefully, including sequencing, scheduling, and logistics.
Material Handling and Storage
- Handle and store steel materials properly to prevent damage or contamination.
- Maintaining a clean and organized work environment reduces the risk of accidents and injuries.
Safety Measures
- Prioritize worker safety by providing appropriate personal protective equipment (PPE) and enforcing safety protocols.
- Regularly inspect and maintain equipment to minimize the risk of accidents.
Quality Assurance
- Conduct inspections at various stages of fabrication to catch and address defects early.
- Implement non-destructive testing (NDT) techniques such as ultrasonic testing or magnetic particle testing for quality assurance.
Documentation and Traceability
- Maintain detailed records of material certifications, welder qualifications, and inspection reports.
- Ensure full traceability of materials and processes to track any issues or defects.
Environmental Considerations
- Implement environmentally friendly practices, such as recycling steel scraps and properly disposing of hazardous materials.
- Comply with local environmental regulations.
Testing and Load Certification
- Perform load testing and certification for critical structural elements to verify their strength and integrity.
Transportation and Installation
- Ensure safe transportation and handling of fabricated steel components to the construction site.
- Follow industry standards for proper installation and connection of steel structures.
In conclusion, structural steel fabrication is a cornerstone of the construction industry, and its adherence to best practices is paramount to the safety and longevity of our built environment. As technology and methodologies continue to evolve, companies like Zetwerk, known for their innovative approach to steel fabrication and commitment to quality, are at the forefront of advancing the industry, ensuring a brighter and more resilient future for construction projects worldwide.




FAQs
The choice of structural steel grade depends on factors such as the structure’s intended use, load-bearing requirements, environmental conditions, and design specifications.
Prefabricated steel buildings offer rapid construction, cost savings, and design flexibility and can be easily expanded or modified.
Distortion control measures, such as tack welding and controlled cooling, help minimize undesirable changes in the shape and alignment of steel components during welding.
Stress-relief heat treatment removes residual stresses in welded components, enhancing their structural integrity and preventing distortion.
Design considerations include selecting appropriate materials, using bracing and moment-resisting frames, and adhering to local building codes and standards for wind and seismic loads.