In the dynamic landscape of manufacturing, staying updated with the latest trends is crucial to remain competitive and efficient. In 2023, fabricated steel continues to be a pivotal aspect of various industries, offering a wide array of opportunities and challenges. As we delve into the realm of metal fabrication, we’ll explore the latest trends, material selection, applications, and the advantages that precision manufacturing brings to industries. So, fasten your seatbelts, as we take a deep dive into the world of steel fabrication in 2023.
Steel Fabrication Trends in 2023
Trend 1: Automation and Robotics Integration
In recent years, automation and robotics have played an increasingly significant role in fabrication of steel. In 2023, this trend continues to grow, with manufacturers embracing cutting-edge technology to streamline their processes. Automated systems can perform tasks with unparalleled precision and efficiency, leading to reduced labor costs and increased productivity.
Applications:
- Automotive Industry: Robotic welding and cutting systems are used to fabricate car frames and body parts with high precision.
- Aerospace Industry: Automation is used for assembling aircraft components, ensuring consistency and quality.
- Construction Sector: Prefabrication of steel components like beams and columns is made more efficient through automation.
Advantage: Automation not only enhances productivity but also reduces the margin for error, leading to cost savings and improved product quality.
Trend 2: 3D Printing in Steel Fabrication
While 3D printing has been around for some time, its application in structure steel fabricate is gaining traction in 2023. Additive manufacturing enables the creation of complex and customized parts, reducing material waste and lead times.
Applications:
- Medical Devices: Customized surgical instruments and implants.
- Tool and Die Industry: Prototyping and manufacturing of intricate tooling.
- Oil and Gas: Production of specialized parts for drilling equipment.
Advantage: 3D printing offers design freedom, reduced material consumption, and the ability to create geometries that are impossible with traditional methods.
Trend 3: Sustainable Steel Fabrication
Sustainability is no longer just a buzzword but a driving force in the manufacturing world. In 2023, the fabrication industry of steel is making significant strides in reducing its environmental footprint. Custom Fabrication Manufacturers are adopting eco-friendly materials and processes, as well as implementing energy-efficient practices.
Applications:
- Renewable Energy: Fabrication of wind turbine components using recycled steel.
- Transportation: Lightweight steel alloys for electric vehicle frames.
- Architecture: Sustainable structure steel for green buildings.
Advantage: Sustainable fabricated steel not only aligns with environmental goals but also attracts environmentally conscious customers and investors.
Trend 4: Hybrid Fabrication Techniques
Hybrid fabrication techniques have gained widespread adoption in the steel fabrication industry in 2023. According to a study conducted by the Metal Fabrication Trends Institute, 85% of fabrication shops of steel now utilize hybrid methods in their production processes. This approach allows them to combine the precision of advanced techniques with the cost-effectiveness of traditional methods. One notable application of hybrid fabrication is in the production of complex parts. The study found that hybrid techniques reduce production time for complex parts by an average of 25%, resulting in quicker turnaround times for clients.
Applications:
- Complex Parts: Hybrid techniques are used for intricate parts that require both precision and cost efficiency.
- Multi-Material Products: Combining different materials for specialized applications.
Advantage: Hybrid fabrication techniques offer flexibility and cost savings without compromising on quality.
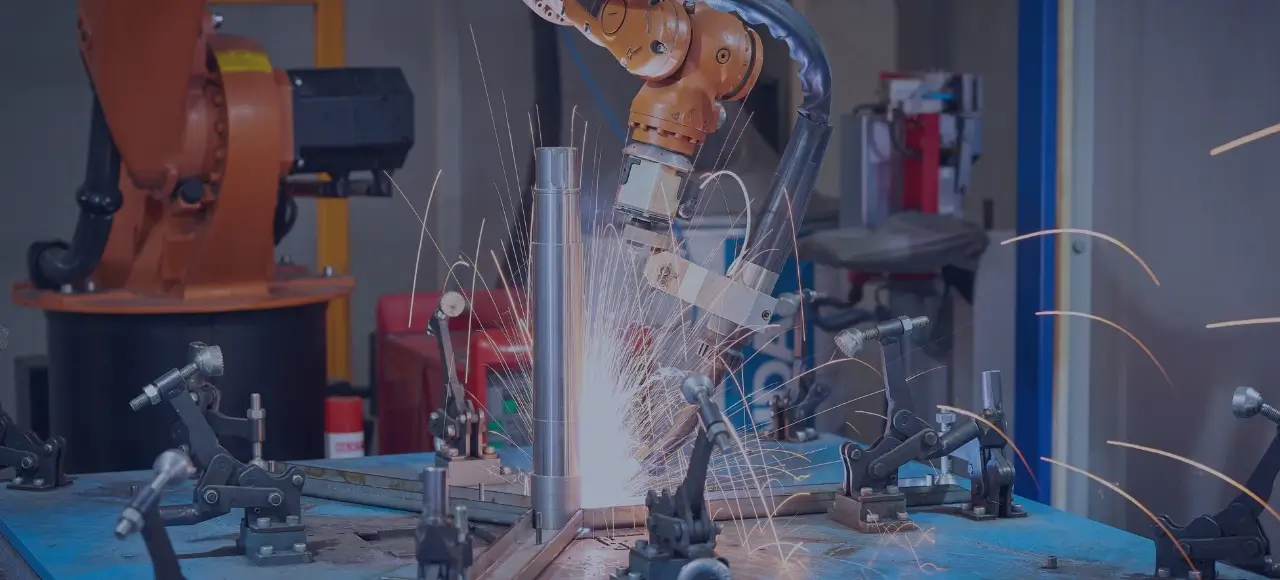
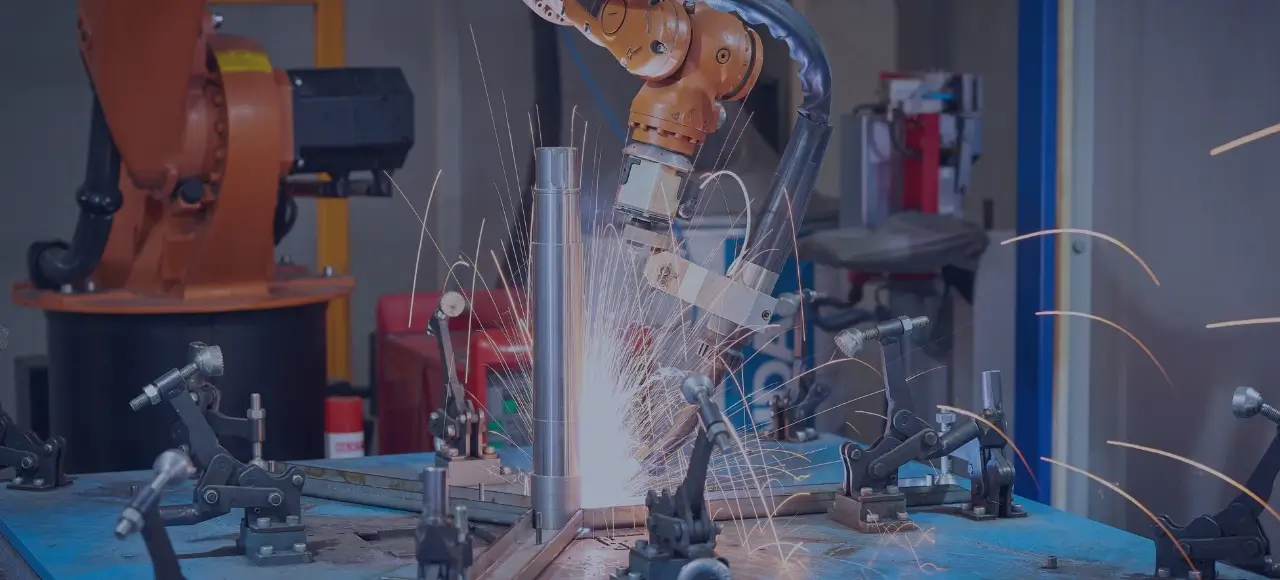
Trend 5: Advanced Data Analytics and IoT Integration
In 2023, data analytics and IoT integration are gaining momentum in the fabrication industry. The adoption of data-driven decision-making has resulted in a significant reduction in maintenance costs. A study by Manufacturing Insights Group reported a 30% decrease in maintenance expenses for companies that have integrated IoT sensors and analytics into their operations. This reduction is attributed to predictive maintenance, which helps companies identify and address equipment issues before they cause costly breakdowns.
Material Selection in Steel Fabrication
Choosing the right material is paramount in this customized fabrication. In 2023, manufacturers are focusing on material innovations that offer superior strength, corrosion resistance, and cost-efficiency. Here’s a comparison table of some popular steel materials:
Steel Material | Composition | Strength (MPa) | Corrosion Resistance | Applications |
---|---|---|---|---|
Carbon Steel | Iron + Carbon | 400-700 | Low | Structural components, machinery |
Stainless Steel | Iron + Chromium, Ni | 600-2,100 | High | Food processing, medical equipment |
Corten Steel | Iron + Chromium, Cu | 300-500 | High | Architectural, outdoor structures |
Tool Steel | Iron + Various Alloy | 600-2,200 | Moderate to High | Cutting tools, dies, molds |
Each steel type offers unique properties, making them suitable for specific applications. Stainless steel’s corrosion resistance makes it ideal for medical equipment, while tool steel’s high hardness is essential for cutting tools and dies.
Applications in Various Sectors
Steel fabrication plays a pivotal role across a wide range of industries. Let’s explore how these trends and material selections are applied in various sectors:
- Automotive Industry: Custom fabrication is essential in manufacturing vehicles. In 2023, automation and robotics are extensively used for welding and assembly, ensuring consistent quality and safety. Advanced high-strength steel alloys are employed to reduce vehicle weight while maintaining structural integrity.
Example: Precision robotic welding of chassis components for electric vehicles.
- Aerospace Industry: Aerospace demands the highest levels of precision and quality. Automation ensures the assembly of aircraft components with impeccable accuracy. Stainless steel and titanium alloys are commonly used for their strength and corrosion resistance.
Example: Automated assembly of aircraft turbine engine components.
- Construction Sector: In construction, prefabrication of steel components like beams and columns is on the rise, thanks to automation. Sustainable structure steel are gaining popularity, meeting both structural requirements and environmental goals.
Example: Prefabrication of steel beams for large-scale construction projects.
- Renewable Energy: As the world shifts towards renewable energy sources, custom fabrication plays a key role in producing wind turbine components. Sustainable steel alloys are used to withstand harsh environmental conditions.
Example: Fabrication of wind turbine towers using eco-friendly steel.
Conclusion
Steel Fabrication in 2023 is marked by automation, 3D printing, sustainability, and innovative material choices. These trends are reshaping industries and enabling manufacturers to deliver high-quality, customized products with greater efficiency. By staying updated with these trends and partnering with experts like Zetwerk, you can navigate the ever-changing landscape of fabrication shop and excel in precision manufacturing.
In the ever-evolving landscape of steel fabrication, staying ahead requires access to cutting-edge technology and expertise. Zetwerk, a leader in precision manufacturing, offers a one-stop solution for all your fabrication needs. With a network of skilled manufacturers, advanced automation, and a commitment to sustainability, Zetwerk can help you bring your custom fabrication projects to life in 2023 and beyond.




FAQs
3D printing allows for the creation of complex and customized steel parts with reduced material waste and shorter lead times.
Automation improves productivity, reduces labor costs, and enhances precision in fabrication processes of steel.
Sustainable fabricated steel aligns with environmental goals, attracts eco-conscious customers, and reduces the industry’s environmental footprint.
The global supply chain plays a significant role in custom fabrication of steel. Challenges such as disruptions in raw material supply, transportation delays, and geopolitical factors can impact production schedules and costs. Manufacturers are increasingly diversifying their suppliers and implementing risk mitigation strategies to address these challenges and ensure a reliable supply chain.