From the construction of ancient weapons and tools to the modern skyscrapers and high-tech machinery of today, metal fabrication has continually evolved to meet the needs of society. In recent years, advanced metal fabrication technologies have pushed the boundaries of what is possible, revolutionizing the manufacturing landscape. This article explores some of the cutting-edge technologies shaping the future of metal fabrication.
Additive manufacturing (3D printing)
Additive manufacturing, commonly known as 3D printing, is a revolutionary manufacturing process that builds three-dimensional objects layer by layer from digital designs. There are several additive manufacturing (3D printing) technologies with characteristics and applications. Here are the types:
Selective laser melting (SLM)
- It uses a high-power laser to melt selectively and fuse layers of metal powder.
- It is ideal for producing high-density, mechanically robust metal parts.
- Used in aerospace and medical industries.
Direct metal laser sintering (DMLS)
- Utilizes a laser to selectively sinter metal powder, layer by layer.
- Known for its precision and fine-detail capabilities.
- Suitable for complex, high-precision metal components.
Binder jetting
- Deploys a liquid binding agent to bond metal powder selectively.
- Speedy and suitable for producing more significant metal parts.
- Requires post-printing sintering to densify the metal.
Material extrusion (Fused Filament Fabrication – FFF)
- Adapts plastic 3D printing techniques for metal fabrication.
- Extrudes metal filament through a nozzle, layer by layer.
- Used for prototyping and small metal part production.
Directed energy deposition (DED)
- Like a laser or electron beam, a focused energy source melts continuously deposited metal wire or powder.
- Helpful in repairing, adding material to, or manufacturing near-net-shape significant metal components.
Continuous Liquid Interface Production (CLIP)
- CLIP is an advanced 3D printing technology developed by Carbon.
- It uses a continuous liquid interface and photosensitive resin that solidifies when exposed to UV light to create objects.
- It is compatible with various materials, including rigid and flexible polymers.
Smart Manufacturing and Industry 4.0
Integrating digital technologies into metal fabrication processes has led to smart manufacturing and Industry 4.0. These advancements involve using sensors, data analytics, and automation to optimize production processes, improve quality control, and reduce downtime.
Internet of Things (IoT)
IoT devices are now commonly used in metal fabrication facilities to monitor equipment health, track inventory, and collect real-time data on machine performance. This data can be analyzed to predict maintenance needs, optimize production schedules, and enhance efficiency.
Artificial Intelligence (AI)
AI-driven algorithms analyze vast datasets and make real-time decisions to optimize production. Machine learning models can predict defects in metal parts, optimize machining parameters, and even control robotic systems for tasks such as pick-and-place operations
Robotics and Automation
Robotic systems have become integral in metal fabrication, handling tasks such as material handling, welding, and quality inspection. Collaborative robots, or cobots, work alongside human operators to enhance productivity and safety in manufacturing environments.
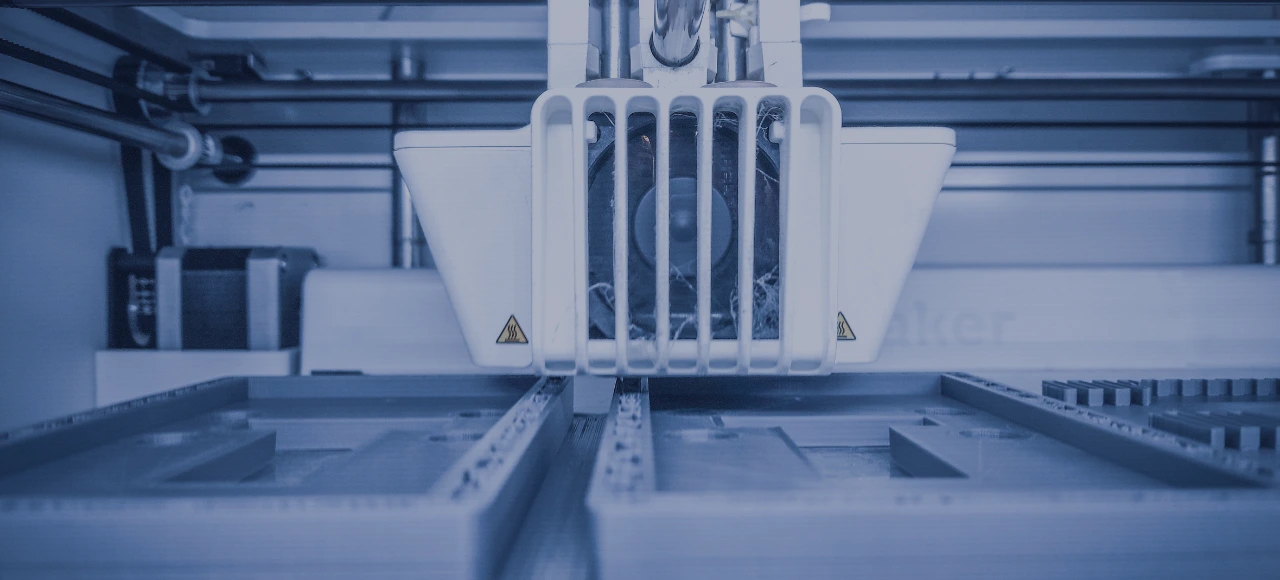
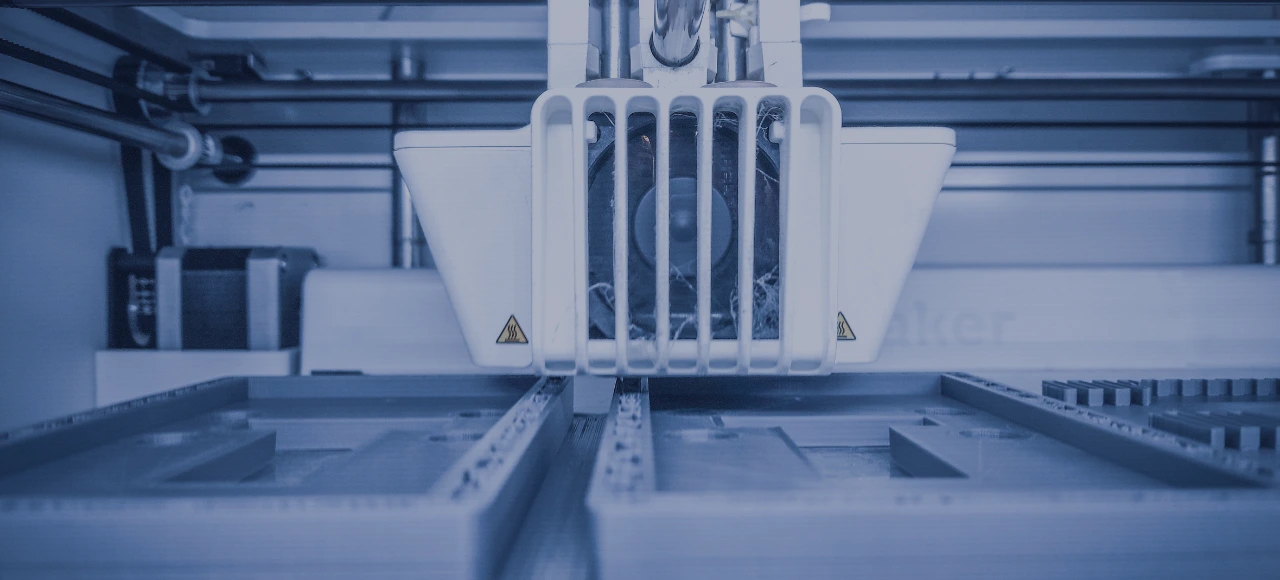
Nanotechnology In Metal Fabrication
It involves manipulating and controlling materials at the nanoscale (typically between 1 and 100 nanometers) on the atomic or molecular level. Here are some key areas where nanotechnology plays a role:
Nanomaterials and Nanostructures
- Nanocoatings: Nanoscale coatings can be applied to metal surfaces to improve their resistance to corrosion, wear, and friction. These coatings can extend the lifespan of metal components, reduce maintenance costs, and enhance performance.
- Nanoparticles in alloys: Nanoparticles can be integrated into metal alloys to improve their mechanical properties, such as hardness and ductility. This is relevant in the aerospace and automotive industries.
Nanofabrication Techniques
- Nanolithography: Nanoscale patterning techniques like electron beam and nanoimprint lithography enable the precise etching and fabrication of nanoscale features on metal surfaces. These techniques are crucial in the production of high-precision metal components.
- Self-assembly: Nanotechnology can facilitate the self-assembly of nanostructures on metal surfaces, creating unique surface properties, such as superhydrophobic or super hydrophilic surfaces.
Nanotechnology in Welding and Joining:
- Nanostructured fillers: Using nanostructured fillers in welding and joining processes can improve the strength and integrity of metal joints. Nanoparticles can also facilitate better control of overheat distribution during welding, reducing distortion and defects.
Sustainable Metal Fabrication
- Recycling and Circular Economy: The recycling of metal scraps and waste materials is becoming increasingly important. Advances in sorting and processing technologies make it possible to recover and reuse metals efficiently, reducing the need for mining and virgin material production.
- Green Energy Sources: Adopting renewable energy sources, such as solar and wind power, for metal fabrication processes reduces greenhouse gas emissions. Integrating these sources into manufacturing facilities lowers environmental impact and cuts energy costs.
- Eco-friendly Coatings: Developments in eco-friendly coatings and surface treatments contribute to corrosion resistance and extend the lifespan of metal products. These coatings are not only protective but also environmentally responsible.
Hybrid Metal Fabrication
Hybrid metal fabrication is an approach that combines traditional metalworking techniques (welding, cutting, bending, machining, etc.) with advanced technologies (3D printing, CNC machining, laser cutting, and robotic automation) to create more efficient, precise, and cost-effective manufacturing processes. This approach leverages the strengths of conventional and modern methods to meet the demands of various industries. Here are some key aspects of hybrid metal fabrication:
- Improved Efficiency: Hybrid approaches can streamline the production process by integrating traditional and modern methods. For instance, additive manufacturing can be used to build up complex metal structures, and then conventional machining can be applied to achieve tight tolerances and surface finishes.
- Material Optimization: Hybrid fabrication allows for the use of different materials and alloys. For example, a part may be fabricated using additive manufacturing with high-strength metals, and then traditional processes can be used to add wear-resistant or corrosion-resistant coatings.
- Rapid Prototyping and Iteration: Hybrid approaches are well-suited for rapid prototyping and iterative design processes. Engineers and manufacturers can quickly create prototypes using additive manufacturing and refine them using traditional methods based on feedback and testing.
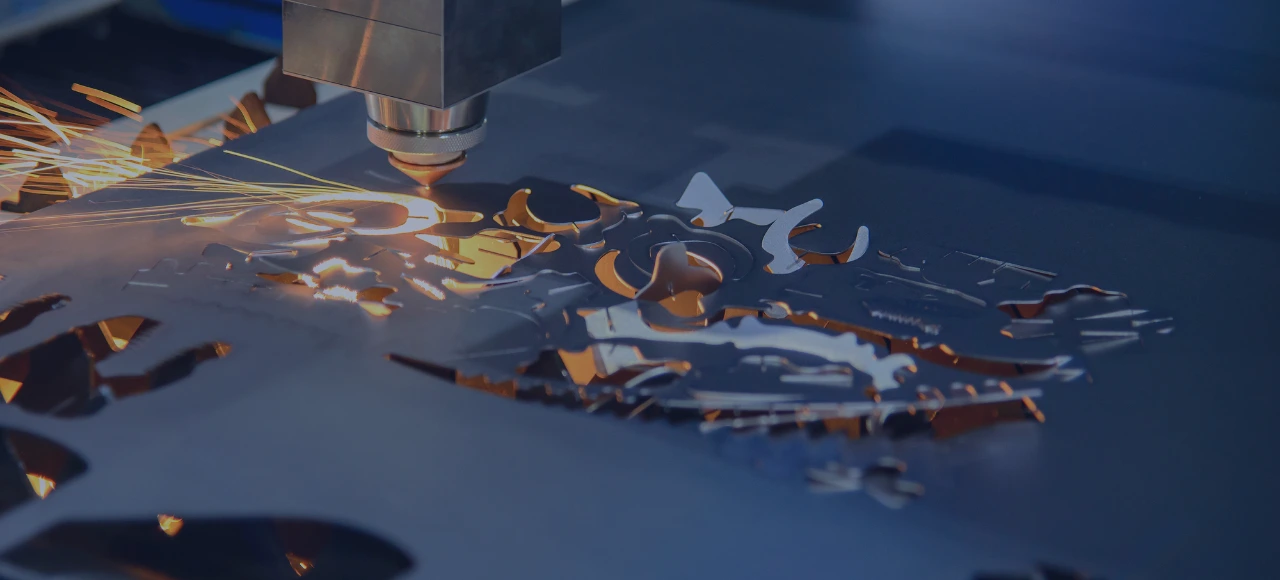
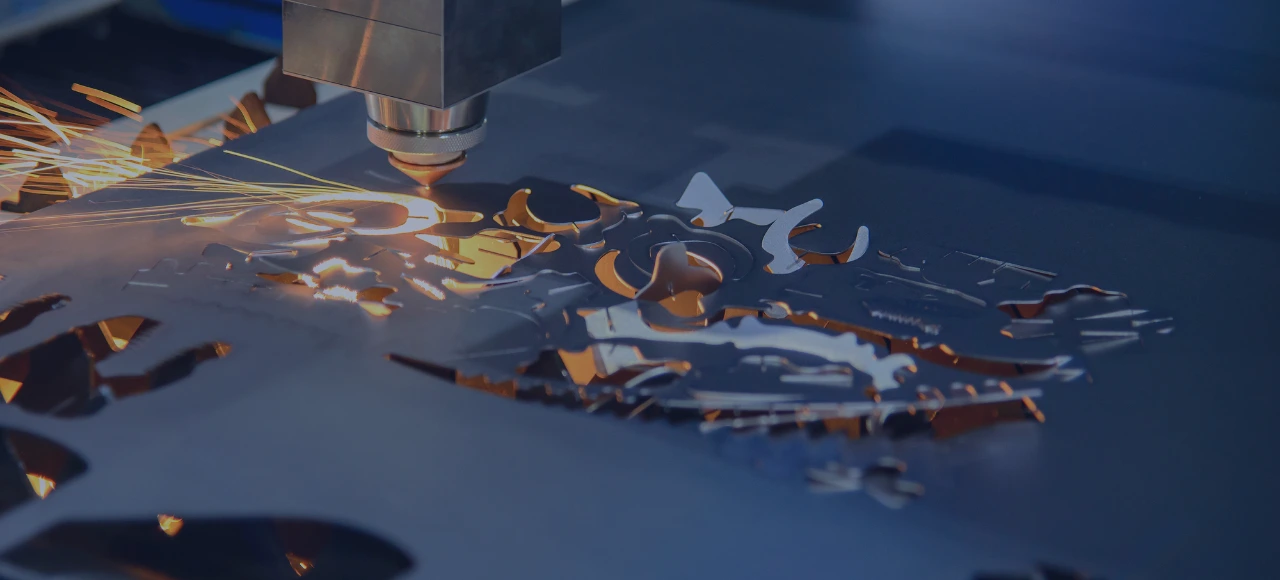
Laser Cutting and Welding
Laser technology has significantly advanced metal fabrication through precision cutting and welding processes. High-powered lasers, such as fiber and CO2, offer various benefits, including speed, accuracy, and minimal material waste
Laser cutting
- It involves using a focused laser beam to cut through metal sheets with exceptional precision.
- They are widely used in the automotive, aerospace, and electronics industries for their ability to produce intricate shapes and reduce material waste.
- It also allows for quick and cost-effective prototyping.
Laser welding
- Utilizes a high-energy laser beam to join metal parts with minimal heat-affected zones.
- They are widely used in industries like automotive and medical device manufacturing.
- It is also used for dissimilar metal joining, enabling the creation of hybrid materials with unique properties.
Waterjet cutting
- It uses a high-pressure stream of water mixed with abrasive particles to cut through various materials, including metals.
- This process is cold and produces no heat-affected zones, making it ideal for cutting materials sensitive to temperature changes.
- They are commonly used in architecture, aerospace, and automotive industries for cutting complex shapes and ensuring minimal material distortion.
Final Words
In the rapidly evolving industry landscape, staying ahead necessitates embracing advanced metal fabrication technologies. The future is wrought with opportunities for those who invest in cutting-edge processes and materials. As we conclude our exploration, remember that innovation is the key to maintaining a competitive edge
FAQs
Factors to consider include material properties (e.g., strength, conductivity, corrosion resistance), cost, weight, and the application’s specific requirements (e.g., aerospace, automotive, medical).
Challenges include scalability, uniformity, and cost. Researchers are working on methods to produce nanomaterials in large quantities, ensure uniform properties, and reduce production costs.
While 3D printing can be used for mass production, it may not be as cost-effective as traditional methods for large quantities. Limitations include slower printing speeds and material costs.
CNC machining generally offers the highest precision, followed by 3D printing, while traditional casting methods may have lower accuracy due to material shrinkage and other factors.
Techniques like Hot Isostatic Pressing (HIP) and surface treatments enhance the properties and aesthetics of metal 3D printed parts.