The B2B automotive industry has been a vital part of industrialization for over a century and indicates a nation’s economic strength. It is a dynamic sector that is constantly evolving, where precision and efficiency are essential for success. These qualities are crucial for progress and achievement in competitive automotive manufacturing. The industry relies on many pivotal manufacturing processes to create automotive parts to meet these high standards, with sheet metal stamping being the most important among them.
Today, we will explore the vital role sheet metal stamping plays in the complex world of automotive manufacturing. Through this blog, we aim to shed light on how this process enhances the standards of B2B automotive manufacturing, leading to greater levels of excellence and efficiency.
The Art of Metal Stamping
- Metal stamping, often called pressworking, involves using various dies, molds, and presses to shape and cut metal sheets into specific forms and designs. The process is as old as the industrial age itself but has continuously evolved to meet the ever-increasing demands of the automotive industry.
- At first glance, sheet metal stamping may appear to be a simple procedure. However, the precision and intricacy required in B2B automotive manufacturing make it an indispensable tool. Stamping enables the production of intricate components with high repeatability and consistency, allowing manufacturers to meet the rigorous quality standards of the automotive sector.
The Backbone of B2B Automotive Production
- When you think of a car, what comes to mind are the sleek curves, the powerful engine, and the comfortable interior. Yet, beneath the surface are thousands of metal components, each meticulously designed and stamped to fit perfectly into the assembly. These components include everything from body panels and chassis parts to engine and transmission components.
- Sheet metal stamping is used extensively in the creation of automotive body panels. Doors, fenders, hoods, and even the frame are all manufactured through this process. This is where the concept of “stamping” comes into play – the individual metal components produced through stamping are assembled to create the final vehicle.
Achieving Excellence in Automotive Stamping
The Significance of Quality in the Initial Stages
“Fit and finish” remains the gold standard for automotive stamping excellence. Emphasizing the importance of high-quality blanks, finely tuned dies, and consistent oil application at the beginning of the stamping process is critical for maintaining downstream quality management. Starting with high-quality materials and effective processes guarantees superior results throughout the manufacturing process.
The Role of Effective Oil Distribution
The uniform application of oil is crucial for achieving consistently high-quality stamped components. Manufacturers can reduce hydraulic deformation, improve stamping consistency, and ensure a perfect fit for assembled components by providing accurate oil film distribution. This not only enhances the overall quality of the product but also optimizes the cost-effectiveness of the entire operation.
Enhancing Welding Processes
In the context of automotive stamping, controlled oil distribution enhances welding processes. By minimizing oil presence, manufacturers can improve weld consistency, reduce weld smoke, and create a healthier working environment for employees. This sheds light on the often-overlooked connection between oil control and welding efficiency, emphasizing the need for a comprehensive approach to maintain high standards throughout manufacturing.
Streamlining the Cleaning Process
Well-regulated oil film thickness impacts the cleaning process in automotive stamping. Precise control over the oil film enables a more predictable and efficient part-cleaning process, minimizing the use of chemicals and contributing to a more consistent and reliable paint finish. By emphasizing the importance of meticulous oil management, manufacturers can enhance overall efficiency and product quality in the automotive stamping process.
Ensuring Predictable Stamping Consistency
The importance of consistent oil film thickness points to the larger goal of achieving predictable stamping consistency in automotive manufacturing. Maintaining uniform oil application ensures a seamless fit between components, streamlines assembly processes, and reduces scrap and part repairs. Moreover, this attention to detail results in a quieter ride and a superior finish, increasing customer satisfaction.
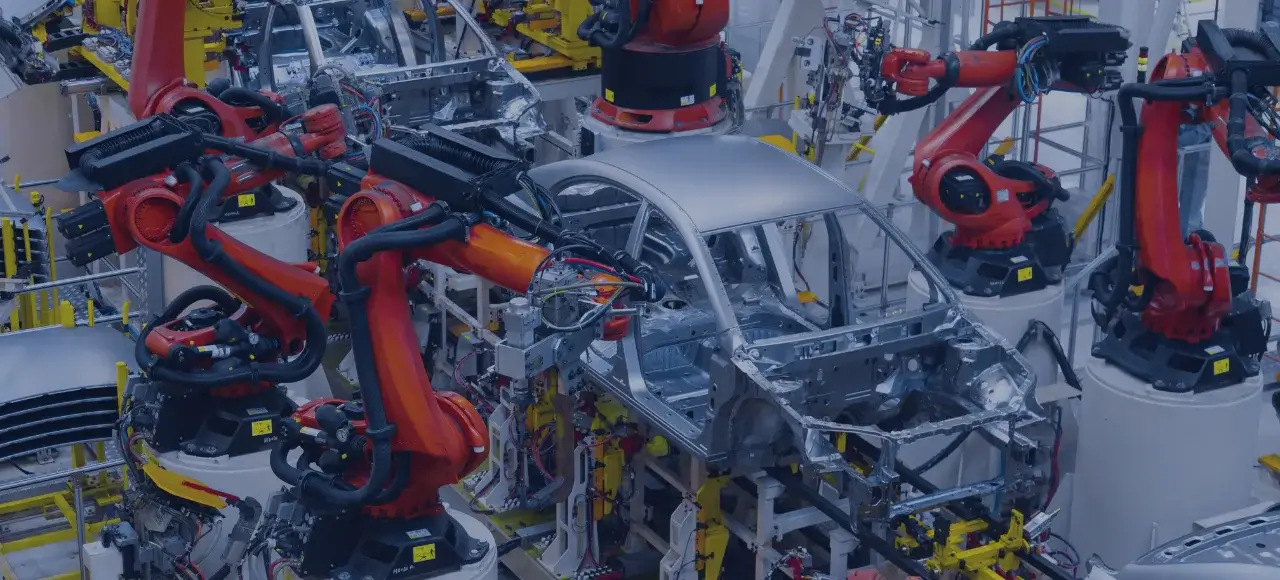
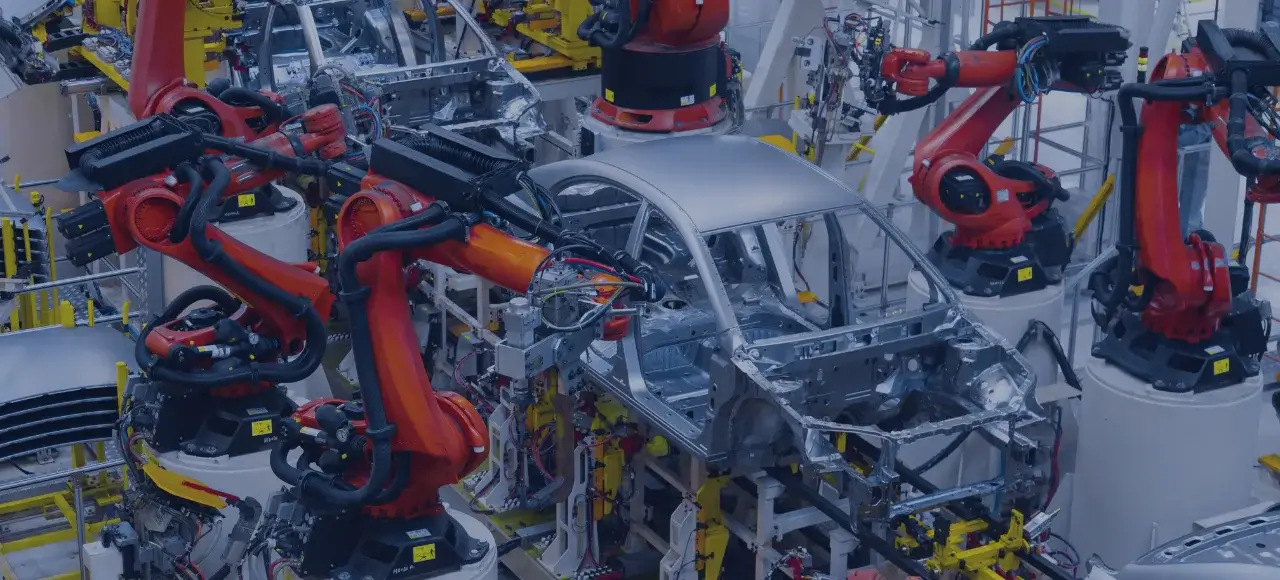
The Role of Innovation
The world of sheet metal stamping is dynamic. It’s a hotbed of innovation. Manufacturers constantly push the boundaries of what can be achieved with this process. Here are some of the key innovations shaping the future of stamping in B2B automotive manufacturing:
- Advanced Materials: As automakers seek to make vehicles lighter and more fuel-efficient, the demand for advanced materials like high-strength steel, aluminum, and composites is rising. Stamping processes are adapting to work with these materials, which often have unique properties and challenges.
- Simulation and Modeling: Digital tools transform stamping by allowing manufacturers to simulate and model the process before physical production begins. This reduces development time and costs and optimizes designs for stamping efficiency.
- Automation and Robotics: Automation has become a cornerstone of modern manufacturing, and stamping is no exception. Robots are now commonly used to load and unload sheet metal stamping presses, increasing production speed and reducing labor costs.
- Sustainability Initiatives: Manufacturers are exploring greener alternatives, such as water-based lubricants and energy-efficient presses, to reduce the environmental impact of stamping.
Challenges and Future Trends
While stamping is a powerful tool in B2B automotive manufacturing, it has challenges. The industry must address issues like tool wear, die maintenance, and environmental concerns associated with stamping fluids. Additionally, as electric vehicles become more prevalent, stamping processes must adapt to produce components specific to these vehicles, such as battery enclosures and electric drivetrain components. Looking ahead, several trends are likely to shape the future of stamping in B2B automotive manufacturing:
- Electrification: As electric vehicles gain popularity, stamping will play a crucial role in producing components like battery enclosures, electric motors, and lightweight body structures optimized for EVs.
- Additive Manufacturing Integration: Integrating additive manufacturing (3D printing) with sheet metal stamping processes could create highly complex and lightweight components that were previously challenging to produce.
- Further Automation: Adopting advanced robotics and artificial intelligence will continue to drive efficiency in stamping processes, reducing costs and lead times.
- Sustainability Focus: Manufacturers will increasingly prioritize sustainability, leading to the development of more eco-friendly stamping processes and materials.
Stamp Your Way to B2B Automotive Excellence!
In B2B automotive manufacturing, sheet metal stamping is a critical process that aims for perfection. It is a dependable means manufacturers utilize to create outstanding, aesthetically pleasing, safe, and efficient vehicles. The industry’s progress is driven by precision and efficiency; vehicles are a testament to human invention.
If you’re a B2B automotive manufacturer needing sheet metal stamping services, Zetwerk is your reliable partner in achieving automotive excellence. They deliver superior quality in producing body panels and automotive sheet metal press parts.




FAQs
Metal stamping is a manufacturing process used in the automotive industry to shape and cut metal sheets into specific forms and designs. It uses dies, molds, and presses to create components crucial for building vehicles, including body panels, chassis, and engine components.
Metal stamping contributes to efficiency by allowing for rapid and precise production of automotive components. With modern technology and automation, stamping can achieve tight tolerances, maintain consistent quality, and reduce lead times, which is essential for meeting the high demand and keeping production costs competitive.
Metal stamping offers several environmental benefits, including material efficiency, reduced waste, and the ability to use lightweight materials. These factors collectively contribute to lower fuel consumption, reduced emissions, and overall sustainability in the automotive industry.
Stamping processes adapt to the automotive industry’s electrification by producing components specific to EVs, such as battery enclosures and lightweight body structures optimized for electric drivetrains. This adaptation ensures that stamping remains crucial to the evolving automotive landscape.
The future of metal stamping in the automotive industry will involve advanced materials, increased automation and robotics, integration with additive manufacturing (3D printing), and a heightened focus on sustainability. These innovations will enhance stamping processes’ efficiency, precision, and environmental friendliness.