Having the right product idea in mind and a huge investment in place can all go in vain when you haven’t partnered with the proper manufacturer for metal roll forming services. Finding a manufacturer is unavoidable when quality metal roll forming is needed. Roll forming is one of the most affordable and demanded metal fabrication processes across several industries, including commercial refrigeration, power distribution, warehouse, and data storage. Hence, it should be outsourced to a supplier who understands your time-sensitive and quality needs and delivers the optimal results you seek.
In this blog, we’ll learn about the 15 ways to find the right metal roll forming services near you.
What is Metal Roll Forming?
- Metal roll forming is a highly efficient and versatile manufacturing process that produces various metal components and profiles. It involves continuously shaping flat metal sheets or coils into desired shapes and profiles by passing them through a series of precisely engineered rollers. These rollers gradually bend and form the metal to the desired cross-sectional shape, creating channels, angles, tubes, and custom profiles. Metal Roll Forming services are preferred for industries requiring long, uniform lengths of metal components, such as construction, automotive, aerospace, and appliance manufacturing.
- The roll-formed steel channel process begins with a coil or sheet of metal being fed into a roll forming machine. This machine typically consists of multiple rollers designed to perform a specific bending or forming operation. As the metal travels through the machine, it undergoes a sequence of bends, curves, and other shaping operations, ultimately taking on the desired profile. Roll forming allows for precise control over the dimensions and tolerances of the final product, ensuring consistent quality and tight tolerances throughout production.
How to Find the Right Metal Roll Forming Services Near You?
Define Your Requirements
Before you start searching for a roll forming manufacturer, defining your project’s requirements is essential. This includes specifying the type of material you need, the desired cross-section, tolerances, and any additional features or coatings required. Understanding your project’s requirements will help you narrow down potential manufacturers and ensure they can meet your needs.
Industry Experience
Look for roll forming manufacturers with a track record of working in your industry or a similar one. Industry-specific experience can be invaluable because the manufacturer understands your field’s unique challenges and requirements. They will likely have the expertise to suggest design improvements and offer solutions tailored to your industry’s demands.
Reputation and References
Check the manufacturer’s reputation within the industry. Search for feedback, endorsements, and success stories shared by past customers. Additionally, don’t hesitate to ask for references or reach out to other companies that have worked with the manufacturer. Hearing about their experiences firsthand can provide valuable insights into the manufacturer’s reliability and performance.
Quality Assurance and Certifications
Ensure the roll forming manufacturer has a robust quality assurance process. Seek out certifications like ISO 9001, showcasing their dedication to maintaining high standards in quality management. Certifications relevant to your industry, such as those for automotive or aerospace, can also positively indicate a manufacturer’s capabilities.
Equipment and Technology
Review the manufacturer’s equipment and technology capabilities. Modern roll forming machinery and roll formed steel channels equipped with advanced technologies can offer higher precision and efficiency. Additionally, inquire about their maintenance practices to ensure minimal downtime during your project.
Customization and Flexibility
Consider how flexible the Roll Forming services are regarding customization. Your project may have unique requirements that demand a tailored approach. A manufacturer willing to adapt their processes and tooling to accommodate your specific needs can be a valuable partner.
Location and Logistics
Consider the manufacturer’s location concerning your project’s site or distribution network. A closer location can reduce shipping costs and lead times. To ensure a smooth supply chain, evaluate their logistical capabilities, including packaging, shipping, and inventory management.
Cost and Pricing Structure
Request detailed quotes from multiple roll forming manufacturers and compare their pricing structures. While cost is essential, it should not be the sole determining factor. Consider the overall value, which includes factors like quality, lead times, and the manufacturer’s ability to meet your project’s unique requirements.
Communication and Collaboration
Effective communication is critical in any manufacturing partnership. Evaluate the manufacturer’s communication skills and willingness to collaborate throughout the project. Transparency and open dialogue can prevent misunderstandings and ensure your project runs smoothly.
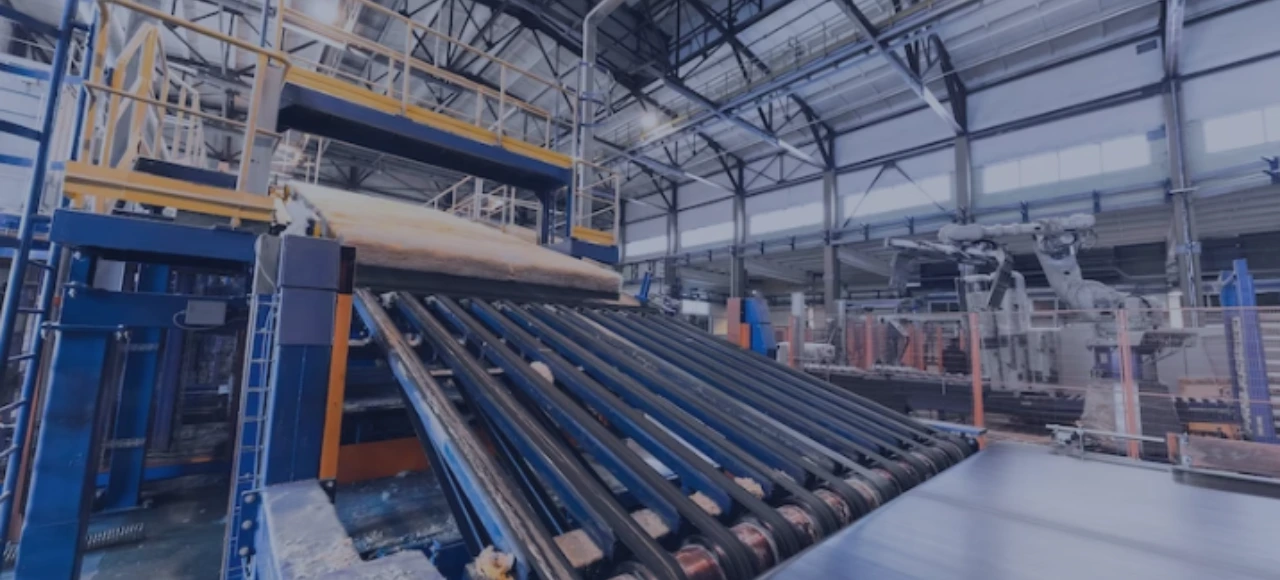
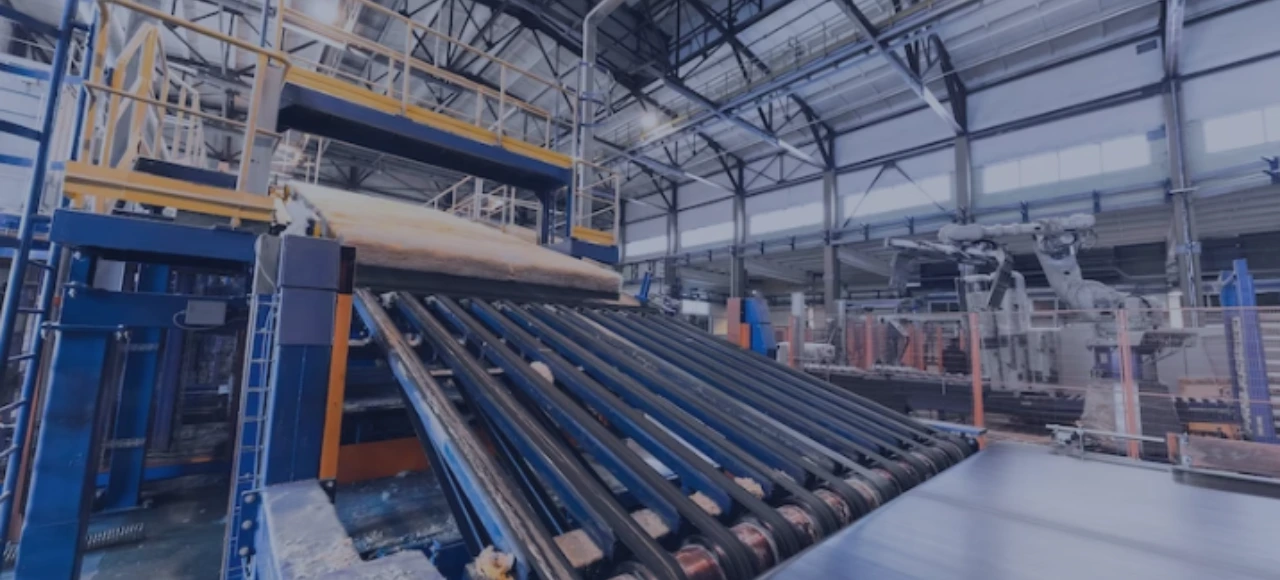
Sustainability and Environmental Practices
In today’s environmentally conscious world, consider the manufacturer’s sustainability practices. Look for companies prioritizing eco-friendly materials, energy-efficient processes, and responsible waste disposal. This aligns with your corporate social responsibility goals and can lead to cost savings in the long run.
In-House Tooling and Design Capabilities
Check if the manufacturer has in-house tooling and design capabilities. The ability to design and fabricate custom tooling for your project can lead to cost savings and faster lead times. It also allows for greater control over the quality and precision of the roll-formed products.
Capacity and Scalability
Consider the manufacturer’s production capacity and scalability. Ensure they can handle your project’s volume requirements now and in the future. Manufacturers with room for expansion or multiple production lines can accommodate your growing needs without delays or disruptions.
Lead Times and Turnaround
Discuss lead times and turnaround with potential manufacturers. Timeliness is often critical in manufacturing projects, so choose a manufacturer with a track record of meeting deadlines. Additionally, inquire about their contingency plans in case of unexpected delays.
Material Sourcing and Procurement
Ask about the manufacturer’s material sourcing and procurement practices. Ensure they have reliable sources for your project’s specific metals or materials. Efficient material management can reduce costs and minimize potential delays due to material shortages.
Post-Production Support and Warranty
Consider what post-production support the manufacturer offers. A reputable manufacturer should provide warranties or guarantees for their products. Knowing they stand behind their work can give peace of mind and product quality assurance.
Roll forming services are preferable for industries seeking medium to high-volume projects. Partnering with the right manufacturer, like Zetwerk, will offer you great value from the beginning to the end of the project. From design consultation to finished goods, Zetwerk provides the output worth your money.




FAQs
Roll forming is a metal fabrication process that creates complex shapes from metal strips. Choosing the right manufacturer is crucial as it directly impacts product quality, cost-efficiency, and project timelines. The manufacturer’s expertise and capabilities can significantly affect the success of your project.
Start by defining the material, cross-section, tolerances, and any additional features or coatings needed for your project. Consult with engineering and design experts if necessary to understand your project’s unique requirements clearly.
When assessing industry experience, consider the manufacturer’s past projects, client testimonials, and case studies related to your industry. Look for manufacturers that have successfully delivered projects similar to yours, as this experience can be invaluable.
To evaluate a manufacturer’s quality assurance, inquire about their certifications, such as ISO 9001, and their commitment to industry-specific standards. Additionally, ask about their inspection and testing procedures to ensure product quality meets your standards.
Effective communication is vital. Ensure the manufacturer is responsive, transparent, and willing to collaborate throughout the project. Good communication helps prevent misunderstandings, keeps the project on track, and fosters a productive working relationship.