Sheet metal is a metal type that comes in thin, wide plates. The sheet metal itself is usually not the final product – manufacturers use it to create various other products for different industries, including but not limited to automotive, aerospace, construction, military, computing, electronics, communications, pharmaceutical, and food processing.
Custom sheet metal services can make a wide variety of parts and products using their skills, including stainless steel furniture (pantries, cabinets, shelves, and more), stair railings, fences, cages, and industrial HVAC parts.
What Is Sheet Metal Fabrication?
Sheet metal fabrication is a process by which sheet metal is cut and bent into a desired shape or form. The sheet metal is usually thin, which involves cutting, punching, bending, and assembling the metal into the desired shape. Sheet metal can be made from a variety of materials, including steel, aluminum, brass, copper, and stainless steel. Aluminum and stainless steel are two common materials used to make precision sheet metal parts.
Sheet metal fabrication services can create a wide range of products for auto parts manufacturers, aircraft parts for the aviation industry, medical equipment, and electronic enclosures. Fabrication services often include design and engineering support, metal prototyping, and producing the finished product.
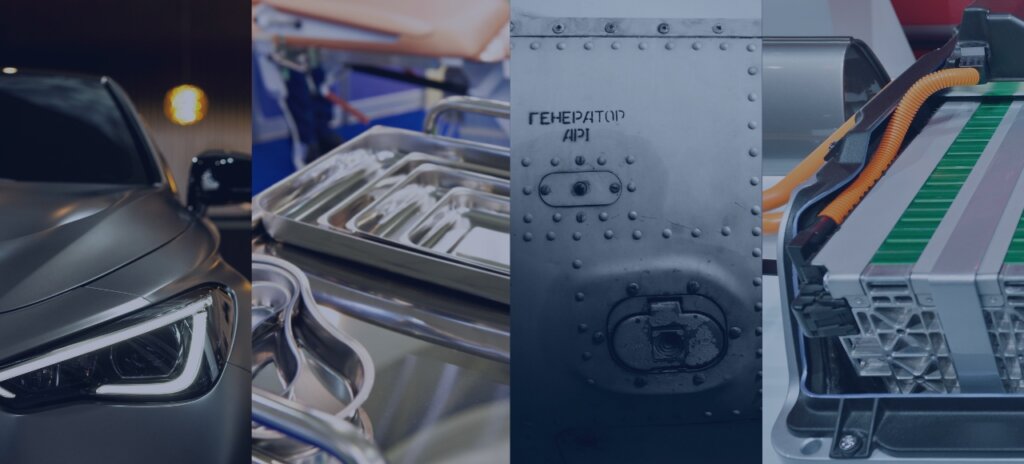
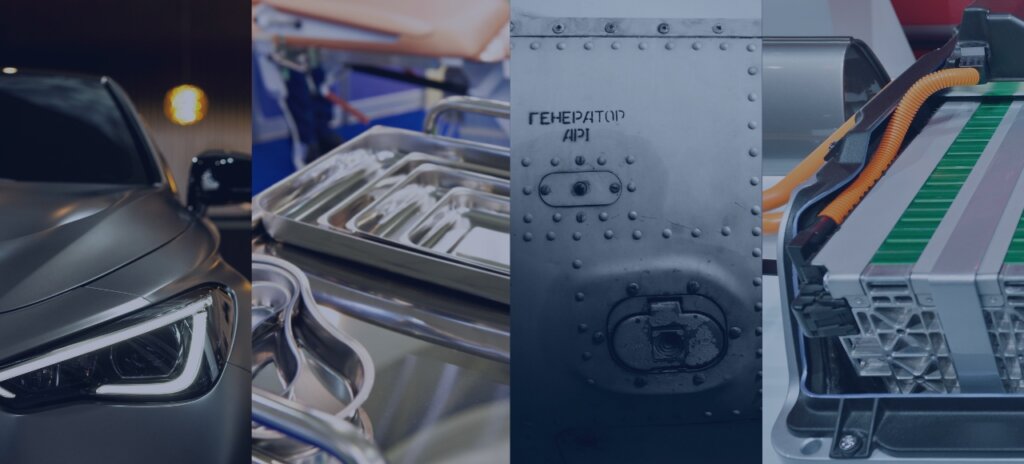
Sheet Metal Fabrication – How Does It Work?
The sheet metal fabrication process generally consists of the following steps:
- Design: The product’s design is the first step in the sheet metal fabrication process. This may involve creating a 3D model using computer-aided design (CAD) software or a physical prototype.
- Welding: If the product requires multiple pieces of sheet metal to be joined together, welding may be used to join the pieces.
- Assembly: If the product requires multiple parts, it may be assembled using fasteners, adhesives, or other methods.
- Bending: The sheet metal is then bent into the desired shape using a press brake or other bending equipment.
- Cutting: Once the design is complete, the sheet metal is cut to the desired size and shape using various techniques, such as laser cutting, water jet cutting, or shearing.
- Finishing: The product may be finished with coatings or surface treatments such as painting, plating, or powder coating.
- Punching: Holes and other features may be added to the sheet metal using a punch press or laser.
- Quality Control: Before the product is shipped to the customer, it is inspected to ensure it meets the required specifications.
Applications of Sheet Metal Fabrication Services
Sheet metal fabrication is forming sheet metal into structures, equipment, or machine parts using various tools and techniques. It is a typical manufacturing process used to create a wide range of products, including automotive parts, aircraft components, medical equipment, and household appliances. Some specific applications of sheet metal fabrication include:
- HVAC (heating, ventilation, and air conditioning) systems – Sheet metal is often used to create ducts, vents, and other components for HVAC systems.
- Structural framing – Sheet metal can create a structural frame for buildings, bridges, and other structures.
- Consumer products – Sheet metal is used to manufacture various consumer products, including appliances, furniture, and sporting goods.
- Medical equipment – Sheet metal is used to create a variety of medical equipment, including MRI machines, x-ray machines, and hospital beds.
- Transportation – Sheet metal is critical in manufacturing cars, trucks, buses, and other vehicles.
- Aerospace – Sheet metal is used to construct aircraft, satellites, and spacecraft.
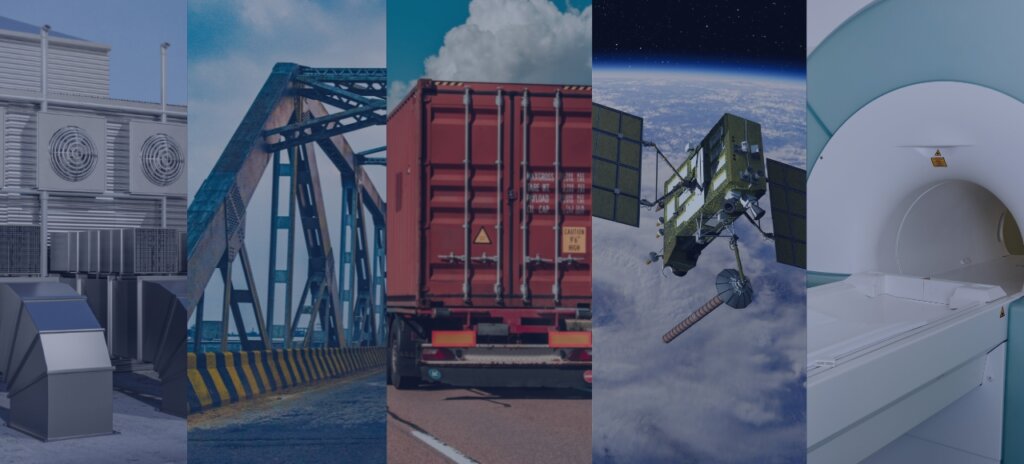
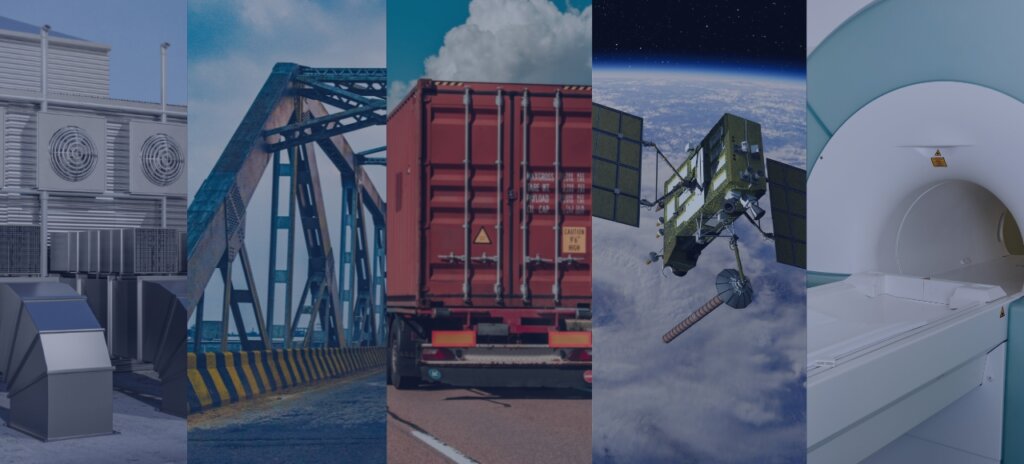
How Do You Find The Right Sheet Metal Service Providers?
There are a few key factors to consider when choosing a sheet metal fabrication service:
- Quality : Look for a provider with a track record of producing high-quality products and meeting your requirements for tolerances and finishes.
- Capacity : Ensure the provider can handle your volume and lead time requirements.
- Equipment : Consider the types of equipment and technologies the provider uses.
- Cost : Get quotes from multiple providers to compare pricing and ensure you’re getting a competitive price.
- Capabilities : Make sure the provider can produce the needed parts, including any special finishes or assembly requirements.
- Location : A local provider may be a better choice if you need to receive the finished parts quickly.
- Reputation : Look for a provider with a good reputation in the industry and positive reviews from past customers.
- Communication : Good communication is key to ensuring that your project runs smoothly. Choose a provider that is responsive and easy to work with.