The demand for versatile and reliable materials and processes is ever-growing in today’s dynamic industrial landscape. Sheet metal, with its exceptional adaptability and precision, continues to play a pivotal role in meeting the requirements of modern industries. This article delves into the innovations and offerings of sheet metal, its applications in various sectors, and the advantages of precision manufacturing processes. We also provide insights into the importance of material selection and current industry trends and conclude with a look at how Zetwerk can streamline your manufacturing needs.
Sheet Metal Applications Across Industries
Sheet metal components find applications across various industries, from aerospace and automotive to construction and electronics. Let’s explore some of the critical sectors where sheet metal is indispensable:
Automotive Industry
- Body Panels: In the automotive sector, sheet metal is extensively used for manufacturing body panels such as doors, fenders, hoods, and roofs. Its ability to withstand the stresses of everyday driving while being lightweight and cost-effective makes it an ideal choice.
- Chassis Components: The chassis of a vehicle is often constructed using sheet metal components. These components provide the necessary structural strength and integrity, ensuring the safety and performance of the car.
Aerospace
- Aircraft Components: The aerospace industry relies heavily on sheet metal for constructing aircraft components. It is commonly used to manufacture wings, fuselage sections, and engine parts due to its lightweight yet strong characteristics. The precise fabrication of these components is essential to ensure the safety and performance of the aircraft.
Construction
- Roofing and Cladding: In construction, sheet metal is used for roofing and cladding on buildings. Its corrosion-resistant properties make it an excellent choice for protection against the elements. Standing seam roofs, in particular, showcase the versatility and durability of sheet metal.
- Ductwork and HVAC Systems: Sheet metal ductwork is used in heating, ventilation, and air conditioning (HVAC) systems. The ducts are designed to transport conditioned air efficiently throughout buildings.
Electronics
- Enclosures and Cabinets: Sheet metal is a preferred choice for creating enclosures and cabinets for electronic equipment. Its electrical conductivity allows for effective shielding and grounding, making it an essential material in electronics manufacturing.
- Heat Sinks: Heat sinks made from sheet metal materials help dissipate heat generated by electronic components. The high thermal conductivity of certain sheet metal alloys enhances heat dissipation, preventing overheating.
Energy and Renewable Energy
- Power Distribution Equipment: The energy sector utilizes sheet metal for manufacturing power distribution equipment. Its robustness and ability to withstand the elements ensure reliable electricity transmission.
- Renewable Energy: In the field of renewable energy, sheet metal is used to create components for solar panels, wind turbines, and other green energy technologies. The durability of sheet metal materials contributes to the longevity and efficiency of these systems.
Medical Equipment
- Diagnostic Devices: Precision sheet metal components are employed in manufacturing medical equipment, including diagnostic devices. The high degree of precision and customization ensures that medical devices meet stringent standards of accuracy.
- Cabinets and Casings: Medical equipment often requires enclosures and casings made from sheet metal. To maintain a sterile environment, these casings must meet stringent hygiene and quality standards.
Food Processing
- Food Conveyor Systems: Sheet metal is used to manufacture food conveyor systems. Its smooth and corrosion-resistant surface is essential for maintaining hygiene in food processing environments.
- Food Storage Containers: Sheet metal containers store food in commercial kitchens and processing plants. Their durability and resistance to corrosion are crucial in food storage applications.
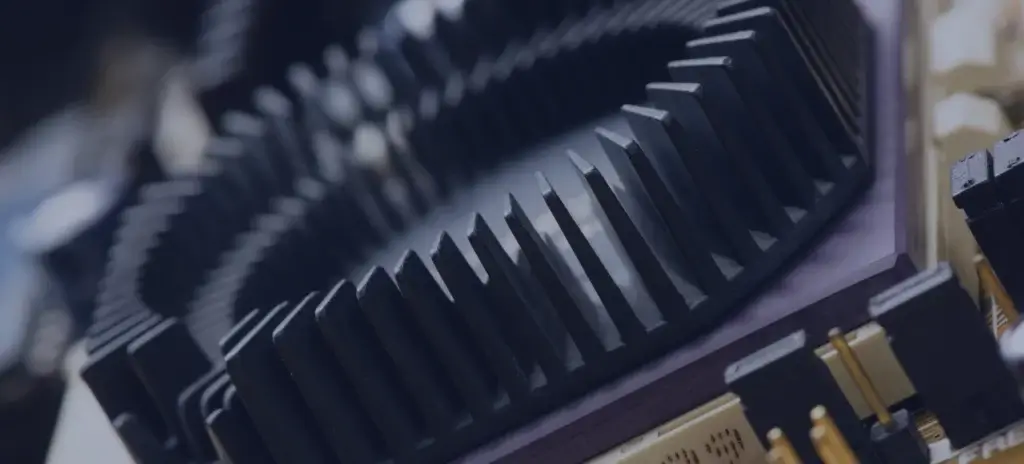
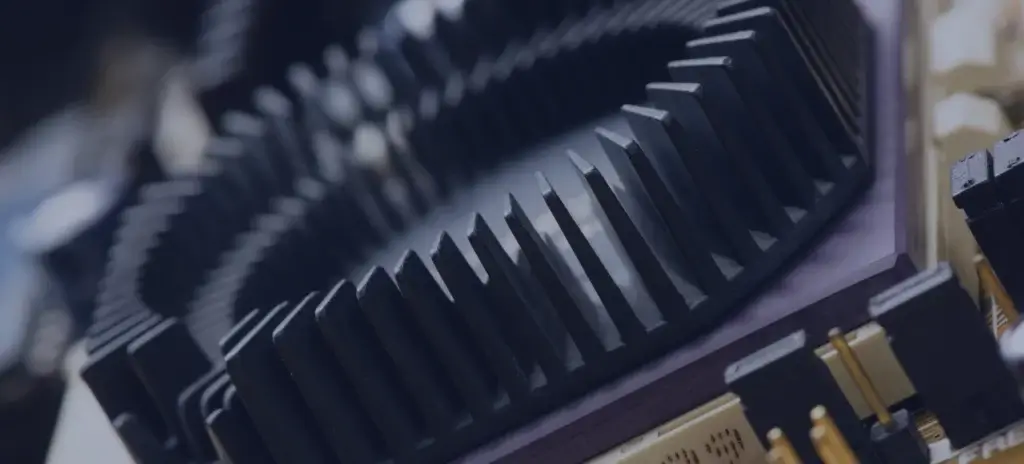
Innovations in Sheet Metal Manufacturing
The field of sheet metal manufacturing is growing; it continually evolves with technological advancements and industry demands. Some notable innovations include:
3D Printing and Additive Manufacturing
- Precision Prototyping: 3D printing has become a game-changer in sheet metal manufacturing. It enables the rapid prototyping of complex sheet metal components, allowing engineers and designers to test and refine designs with unparalleled speed and efficiency.
- Intricate Geometries: Additive manufacturing technologies, such as Selective Laser Melting (SLM) and Powder Bed Fusion, can create sheet metal components with complex geometries that were once difficult to achieve using traditional methods.
Nanotechnology Integration
- Enhanced Material Properties: Nanotechnology is being employed to improve the properties of sheet metal materials. Through nanocoating and nanoscale surface modifications, sheet metal components can exhibit improved characteristics such as increased strength, enhanced corrosion resistance, and excellent durability.
- Advanced Alloys: Nanotechnology is also contributing to the development of advanced alloys. These materials offer unique properties that expand the possibilities for sheet metal applications, especially in high-stress and demanding environments.
Sustainability Initiatives
- Eco-Friendly Materials: The sheet metal industry embraces sustainability by developing and utilizing eco-friendly materials. This includes materials sourced from recycled content and materials designed for easy recycling after their useful life.
- Green Manufacturing Practices: Manufacturers are adopting eco-friendly practices, such as minimizing waste, reducing energy consumption, and optimizing production processes. These green initiatives align with global efforts to reduce the environmental impact of manufacturing.
Digitalization and Industry 4.0
- IoT Integration: Integrating the Internet of Things (IoT) transforms the sheet metal manufacturing landscape. Smart machines and equipment equipped with sensors provide real-time data on the production process, enabling predictive maintenance and quality control.
- Digital Twin Technology: Digital twin technology is used to create virtual models of sheet metal components. These digital twins facilitate design optimization, performance prediction, and efficient quality control.
Customization and Rapid Prototyping
- Diverse Industry Needs: The demand for customized sheet metal components is rising, driven by various industry requirements. Sheet metal manufacturers are adapting by offering tailored solutions that cater to specific designs, sizes, and material preferences.
- Rapid Prototyping: Innovations in rapid prototyping enable manufacturers to produce and test sheet metal prototypes quickly. This accelerates the design and development process, reducing lead times and costs.
Automation and Robotics
- Efficient Production: Automation streamlines sheet metal production, including robotics and Computer Numerical Control (CNC) machining. These technologies enhance efficiency, reduce labor costs, and ensure precision in component manufacturing.
- Quality Control: Automated inspection systems conduct rigorous quality control checks on sheet metal components. This ensures that products meet the highest quality standards with minimal human error.
Hybrid Materials and Composites
Expanding Possibilities: Exploring hybrid materials expands the possibilities for sheet metal applications. These hybrid materials combine the strengths of various metals and non-metallic materials to create components with unique properties and characteristics
Material Selection for Sheet Metal
Material | Properties | Applications | Advantages | Disadvantages |
---|---|---|---|---|
Stainless Steel | – Corrosion resistance – High strength – Excellent durability | – Automotive components- Medical equipment- Food processing- Architecture | – Resistant to rust and staining – Hygienic – Long lifespan | – Higher cost compared to some other materials – Can be heavy for certain applications |
Aluminum | – Lightweight – Good corrosion resistance – High electrical conductivity | – Aerospace components – Electronics enclosures – Automotive parts – Construction | – Low density – Excellent thermal conductivity – Easy to form and weld | – Not as strong as steel – Prone to scratching and dents |
Carbon Steel | – High strength – Cost-effective | – Automotive chassis – Industrial machinery – Construction structures – General manufacturing | – Economical choice – Strong and durable – Easily machinable | – Susceptible to corrosion – May require protective coatings |
Copper | – Excellent electrical conductivity – High thermal conductivity | – Electrical components – Heat exchangers – Plumbing – Roofing | – Superb conductivity – High corrosion resistance – Aesthetic appeal | – Relatively expensive – Prone to tarnishing |
Corten Steel | – Exceptional corrosion resistance – Weathering properties – High tensile strength | – Architectural elements – Outdoor sculptures – Bridges – Shipping containers | – Unique aesthetics – Reduced maintenance – Durability in harsh environments | – Initial cost can be higher – Requires time for full weathering effect |
Titanium | – Exceptional strength-to-weight ratio – Excellent corrosion resistance | – Aerospace components – Medical implants – Chemical processing – Marine applications | – Lightweight and strong – Biocompatible – Non-reactive | – High cost – Difficult to machine – Limited availability |
Conclusion
Sheet metal continues to be a driving force in modern industries, offering versatility, precision, and various applications. As technological innovations and sustainable practices continue to shape the industry, sheet metal remains a resilient and adaptable material. Whether in the automotive sector, architecture, or electronics, the advantages of sheet metal are clear, making it an essential component of modern manufacturing
If you’re looking to harness the advantages of sheet metal in your projects, Zetwerk stands ready to assist in manufacturing high-quality components. Our precision manufacturing services can help you achieve your goals efficiently and precisely. Contact us to learn how we can support your sheet metal requirements and enhance your business endeavors.



FAQs
Yes, sheet metal components can be tailored to precise design specifications, making them highly customizable.
Considerations include the intended application, environmental factors, material properties, and cost considerations.
Quality control measures, including rigorous inspections and testing, ensure that sheet metal components meet the highest standards.
Yes, there is a growing availability of sustainable sheet metal materials and manufacturing processes.
Zetwerk offers precision manufacturing services, including sheet metal fabrication, and can help streamline the production of high-quality components to meet industry needs.