In the modern engineering, precision isn’t just a virtue; it’s a necessity. Enter metal stamping parts, where precision craftsmanship intertwines with efficient component designs to shape industries and revolutionize products. From aerospace innovations to everyday consumer goods, this comprehensive guide unveils the prowess of metal stamping parts. With a deep dive into manufacturing intricacies, and sector-specific applications, let’s explore how precision metal stamping parts leave an indelible mark on engineering excellence.
Precision in Metal Stamping Parts
Metal stamping parts are the epitome of precision engineering. The process involves crafting intricate components by pressing or stamping metal sheets into desired shapes. With a fusion of technology, skill, and meticulous planning, metal stamping parts emerge as the backbone of various industries, contributing to product functionality, aesthetics, and reliability.
Stamped Parts: Process Overview
At the heart of metal stamping lies precision craftsmanship. The journey begins with detailed design engineering, where components are meticulously planned using Computer-Aided Design (CAD) software. Every contour, curve, and dimension is calibrated to perfection, ensuring that the finished product adheres to exact specifications. These digital blueprints guide the stamping process, enabling the precise transformation of raw metal into intricately designed components.
Metal Stamping Techniques: Mastering Precision at Every Turn
The world of metal stamping encompasses a variety of techniques, each tailored to specific applications and design requirements. Let’s delve into some prominent metal stamping techniques that exemplify precision in action:
Progressive Die Stamping
Progressive die stamping is a multi-step process that efficiently produces complex components. The technique involves a series of sequential operations, with each step adding a new feature to the part. This technique is ideal for high-volume production of parts with intricate designs, such as connectors and fasteners. Progressive die stamping not only ensures precision but also boosts production efficiency by minimizing material waste and downtime.
Deep Drawing
Deep drawing is employed to create cylindrical or box-like components with significant depth. The process involves pulling a metal blank through a die to form it into a desired shape. Deep drawing is widely used in industries like automotive (for components like fuel tanks), household appliances (sink bowls), and aerospace (fuel cell casings). The precision achieved in deep drawing ensures uniform thickness and accurate dimensions throughout the component.
Blanking and Piercing
Blanking and piercing are fundamental metal stamping processes used to cut and punch holes in metal sheets. Blanking involves cutting out a desired shape from a larger sheet, while piercing involves creating holes within a sheet. These techniques are crucial for creating components like washers, gaskets, and brackets. The precision in blanking and piercing directly impacts the fit, function, and integrity of the final product.
Bending and Forming
Bending and forming are employed to create components with specific angles, curves, and contours. Precision bending ensures that the component conforms precisely to the intended design. Industries ranging from electronics (creating casing components) to furniture (metal brackets) benefit from bending and forming techniques. The precision in these techniques guarantees that components align accurately during assembly, contributing to the overall structural integrity of the end product.
High-Speed Stamping
In an era where speed is of the essence, high-speed stamping emerges as a game-changer. This technique employs specialized equipment capable of delivering rapid and precise stamping operations. High-speed stamping is favored for high-volume production of components where time-to-market is critical. The precision maintained at high speeds ensures that each component meets stringent quality standards, even in demanding industries like automotive and consumer electronics.
Materials preferred in Stamping
In the intricate dance of metal stamping, the choice of materials plays a pivotal role in shaping the final product’s performance, durability, and aesthetics. From steel to specialized alloys, each material brings its unique properties to the manufacturing stage. Let’s explore the world of materials for stamping and how their selection contributes to crafting excellence across various industries.
- High-Strength Alloys: Industries requiring components to withstand extreme conditions often turn to high-strength alloys. These alloys, often containing elements like nickel, titanium, and cobalt, offer unparalleled mechanical properties. In aerospace applications, superalloys like Inconel and Hastelloy withstand high temperatures and corrosive environments, contributing to the efficiency and safety of aircraft engines.
- Aluminum: The lightweight champion of materials, aluminum’s low density makes it an attractive choice for industries aiming to reduce weight while maintaining strength. Aluminum alloys like 6061 and 5052 are commonly stamped, finding application in automotive body panels, aerospace components, and electronics casings. Aluminum’s excellent conductivity also makes it a preferred material for heat sinks and electrical connectors.
- Stainless Steel: Stainless steel’s allure lies in its corrosion resistance and aesthetic appeal. This alloy of iron, chromium, and other elements is available in various grades, each tailored to specific requirements. Austenitic stainless steel is a favorite for its formability and corrosion resistance, making it suitable for applications in the medical, electronics, and food industries. Martensitic stainless steel offers increased strength, while ferritic stainless steel finds its place in automotive exhaust systems and decorative elements.
- Copper and Copper Alloys: Copper’s exceptional electrical conductivity and thermal properties make it indispensable in industries reliant on efficient heat transfer and electrical connectivity. Copper alloys like brass and bronze combine copper’s conductivity with enhanced durability and aesthetics. Stamped copper components are found in electrical connectors, automotive radiators, and decorative elements.
- Carbon Steel: Carbon steel is a stalwart choice in metal stamping due to its versatility and affordability. It comes in various grades, each offering a balance between strength and formability. Low-carbon steel is ideal for intricate designs requiring deep drawing, high-carbon steel excels in applications demanding higher tensile strength. From automotive components to household appliances, carbon steel’s availability and adaptable nature make it a staple in stamping processes.
- Specialized Alloys: Certain applications demand materials with specialized properties. For instance, electrical contacts may require beryllium copper for its exceptional electrical conductivity. Magnetic properties lead industries like electronics to use silicon steel for transformer cores. These specialized alloys cater to specific needs, underscoring the diversity and adaptability of materials in metal stamping.
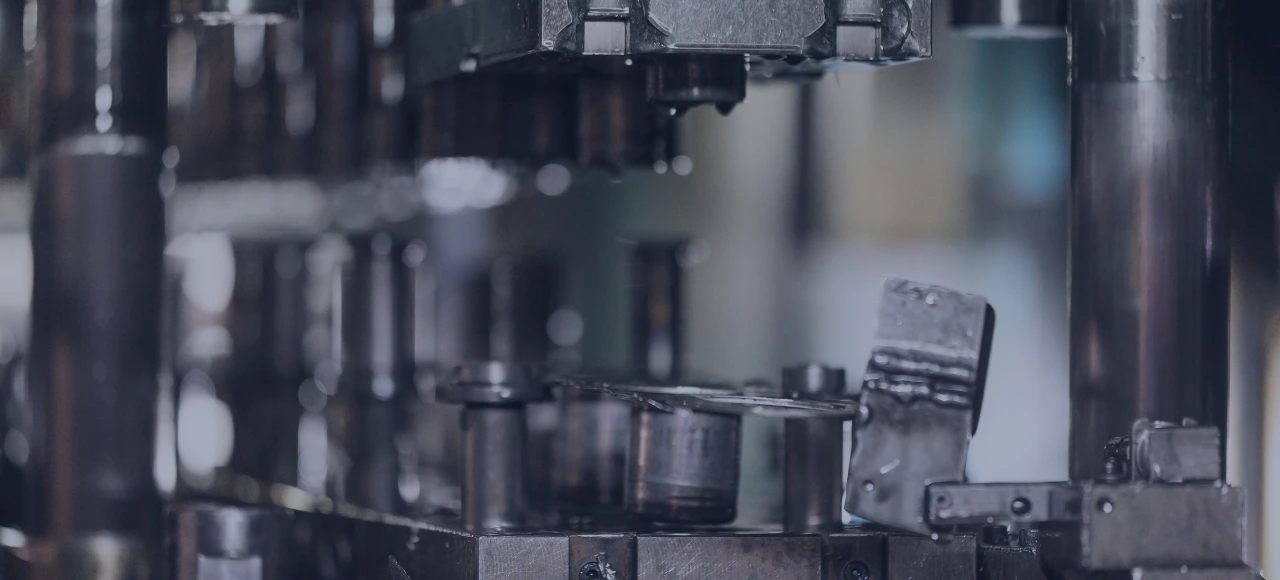
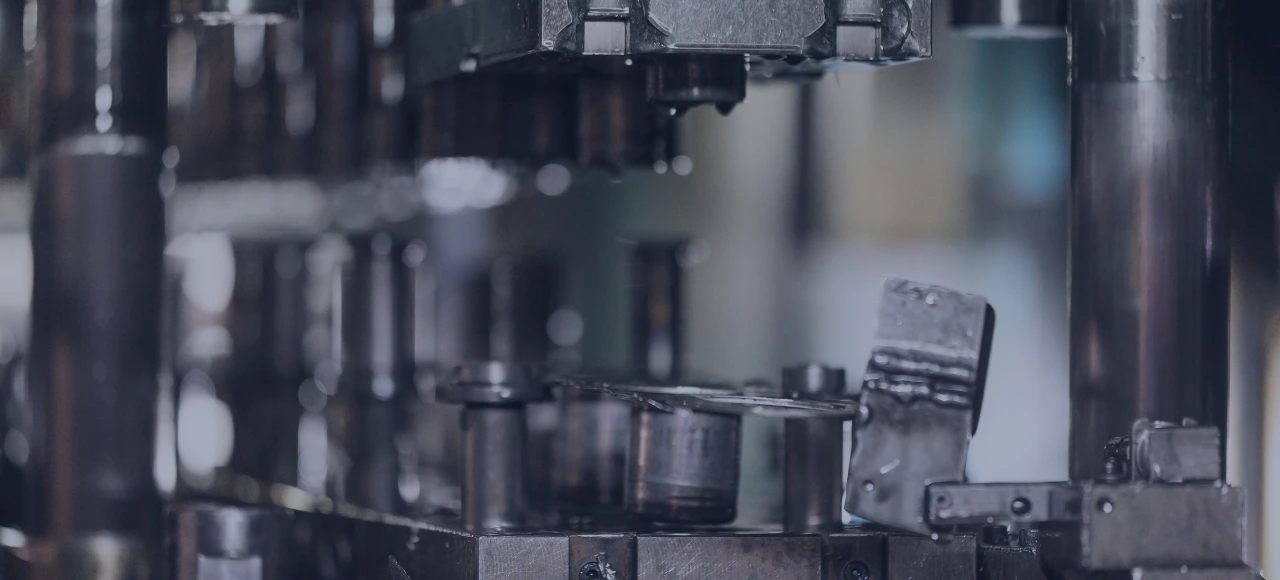
The choice of material is a delicate balance between mechanical properties, cost considerations, and environmental factors. Engineers meticulously evaluate the requirements of each component and select the material that best aligns with the application’s demands. Whether it’s the high-stress environment of an aircraft engine or the precision requirements of a medical device, material selection is a critical step in ensuring that stamped components perform flawlessly.
Advantages of Metal Stamping Parts
The advantages of metal stamping parts ripple through the engineering landscape, creating a profound impact across various industries:
Aerospace Advancements:
- In the aerospace industry, where weight, strength, and reliability are paramount, metal stamping parts shine. Components like aircraft panels, brackets, and engine housings are meticulously stamped to achieve lightweight yet sturdy structures that endure the rigors of flight.
- Examples in Detail: In the aerospace sector, stamped components like brackets and support structures are designed with aerodynamics and strength in mind, contributing to fuel efficiency and flight safety.
Consumer Goods and Beyond:
- From kitchen appliances to consumer electronics, metal stamping parts are omnipresent. Their precision ensures that everyday products function flawlessly, enhancing user experiences while maintaining cost-effectiveness.
- Examples in Detail: Consider a smartphone’s SIM card tray. This seemingly small component requires precision to ensure a snug fit for the SIM card. Metal stamping achieves the necessary dimensions and tolerances, facilitating effortless insertion and removal.
Automotive Precision:
The automotive sector benefits from metal stamping parts, creating components ranging from body panels to intricate engine parts. The precision and consistency achieved through stamping ensure that every part aligns perfectly, contributing to vehicle performance, safety, and aesthetics.
Electronics Evolution:
In the electronics realm, metal stamping parts give life to connectors, terminals, and shielding components. The precision of these parts is crucial for ensuring seamless connections, electromagnetic compatibility, and optimal functioning of electronic devices.
Medical Marvels:
Medical devices demand precision beyond measure. Metal stamping parts play a pivotal role in crafting surgical instruments, implantable devices, and specialized components that require exacting measurements and biocompatibility.
Conclusion
Metal stamping parts are the embodiment of precision in engineering. From the smallest electronic components to the largest aerospace structures, their impact resonates across industries and applications. The fusion of precision craftsmanship, technology, and versatility makes metal stamping parts the unsung heroes of modern engineering. As industries evolve and innovation continues, the role of metal stamping parts will remain steadfast, contributing to products that define excellence and elevate human progress.
As you navigate the realm of precision metal stamping parts, Zetwerk stands as your ally. With a commitment to innovation, precision, and a diverse range of stamping capabilities, Zetwerk streamlines the process of bringing your designs to fruition. By harnessing advanced techniques and rigorous quality controls, Zetwerk ensures that the components produced through metal stamping meet industry standards and exceed expectations.




FAQs
A wide range of materials can be stamped, including steel, aluminum, copper, and alloys. The choice depends on factors such as mechanical properties, corrosion resistance, and application requirements.
The metal stamping process utilizes precision tooling, dies, and machinery to ensure that each stamped part adheres to exact specifications, minimizing deviations and errors.
Absolutely. Advanced tooling techniques and machinery enable the stamping of intricate and complex designs, allowing for the creation of components with sophisticated geometries.