Roll forming is a fascinating metalworking process that allows manufacturers to shape continuous metal strips or sheets into complex profiles with remarkable precision. Whether you’re in the construction, automotive, or aerospace industry, mastering roll forming design is crucial to achieving high-quality, cost-effective products. In this blog, we’ll embark on a journey to explore the world of roll forming, unveiling the essential tools and best practices that will empower you to master this craft.
Art and Science of Roll Forming
Before we dive into the tools and best practices, let’s take a moment to understand what roll forming is all about. At its core, roll forming is a marriage of art and science. It involves guiding a metal strip or sheet through a series of precisely contoured rollers, incrementally shaping the material into a desired cross-sectional profile. This process can range from producing simple shapes like angles and channels to highly intricate profiles found in architectural trim and complex structural components.
The Foundation: CAD Software
CAD: Where Ideas Take Shape
At the heart of roll forming design lies Computer-Aided Design (CAD) software. This is where your ideas take shape, quite literally. CAD software allows engineers and designers to create intricate digital models of the intended profile. It provides a canvas to sketch, dimension, and experiment with various design iterations. The beauty of CAD is that it’s not only a design tool but also a problem-solving tool. It enables you to simulate the roll forming process virtually, helping identify potential design flaws and refine your vision.
Precision with Finite Element Analysis (FEA)
Strength in Structure
As the saying goes, “Form follows function.” Roll-formed products must not only look good but also possess structural integrity. This is where Finite Element Analysis (FEA) comes into play. FEA software lets you simulate how your roll-formed part will behave under different conditions. It’s like having a crystal ball that predicts your design’s structural strength, durability, and performance. You can optimize your design by running FEA simulations to ensure it meets the required strength and safety standards.
Seeing the Future: Roll Forming Simulation Software
Virtual Roll Forming
Imagine having the power to see the future, to witness how your design will transform into a tangible product. That’s precisely what roll forming simulation software offers. This specialized tool enables you to visualize the entire roll forming process virtually. It’s like having a backstage pass to the magic show, where you can spot potential challenges before the curtains rise. With simulation software, you can identify issues such as material thinning, wrinkling, or misalignment and make necessary adjustments, all without forming a single sheet of metal.
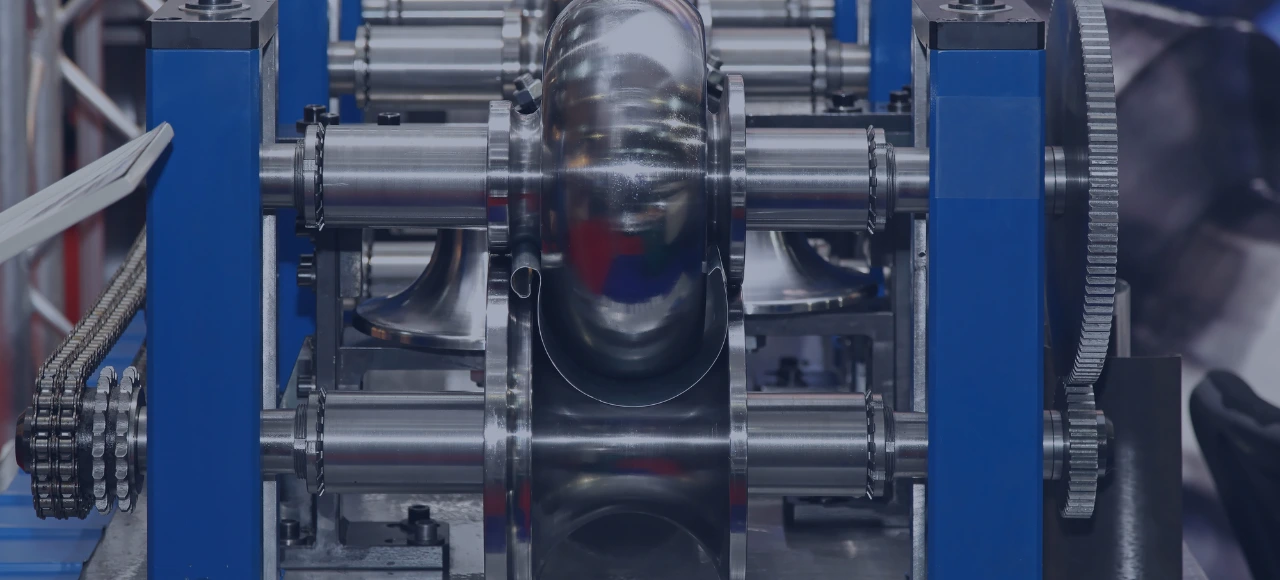
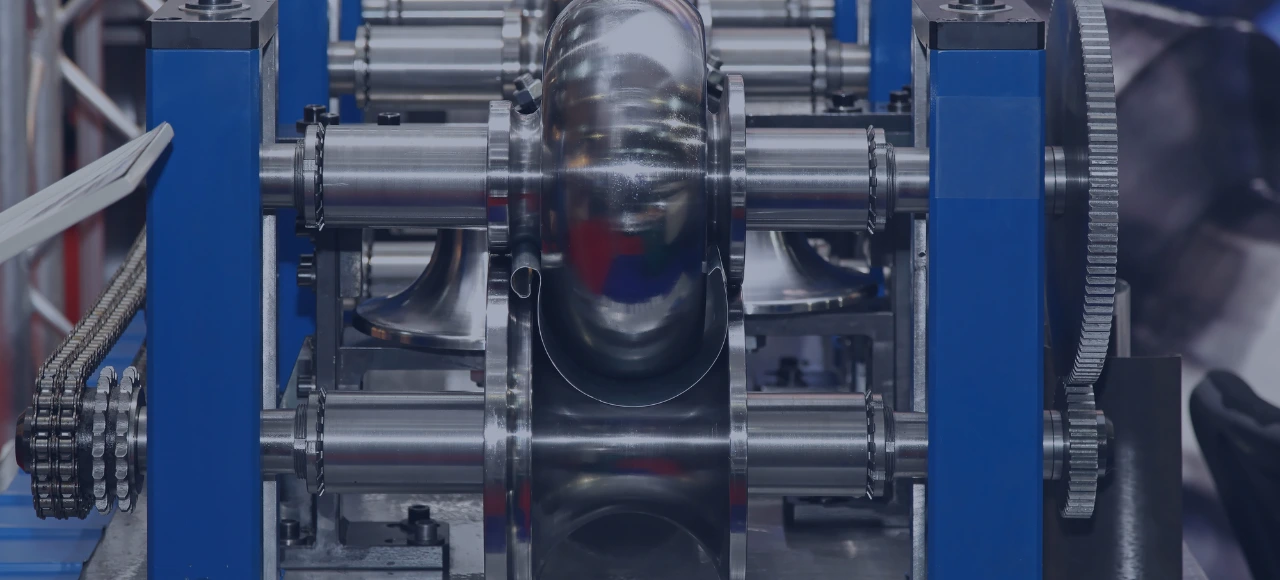
Lean on Design Guidelines
Wisdom from the Masters
Every craft has its masters, and roll forming is no different. There’s a wealth of industry-specific design guidelines and handbooks at your disposal. These resources are a treasure trove of knowledge, offering insights into material selection, bend radii, tolerances, and more. By following these guidelines, you can benefit from the collective wisdom of experts who have paved the way in the world of roll forming.
Best Practices: Navigating the Roll Forming Terrain
As we venture deeper into the realm of roll forming design, it’s essential to embrace best practices. Here are some guiding principles that will help you navigate this terrain:
Material Matters
The foundation of any great roll-formed product is the material itself. Your choice of material—its type, thickness, and strength—should align with the intended application. Understanding how the material behaves during forming is paramount to prevent defects like splitting, wrinkling, or warping.
The Roll Tooling Magic
The magic of roll forming happens in the tooling—the carefully designed rollers impart shape to the metal. Consider factors like roll diameters, spacing, and contour profiles to achieve precision. CAD and simulation tools can help you fine-tune your tooling design.
Thickness Consistency Is Key
Maintaining consistent material thickness is vital. Variations in thickness can lead to product defects. Through proper design and setup, strive to minimize thickness inconsistencies and ensure uniformity in the final product.
Smooth Transitions, No Stress
Avoid stress in your design—literally. Sharp corners or abrupt changes in cross-sectional geometry can lead to stress concentrations in the formed part—design profiles with gradual transitions and fillet radii to reduce stress concentration points.
Tooling TLC
Regular inspection and maintenance of roll forming tooling are essential. Worn or damaged tooling can lead to defects and increased downtime. Keeping your tooling in top shape is an investment in quality and efficiency.
Process Control
Embrace effective process control measures. Monitor roll pressures, speeds, and material temperatures to maintain product consistency. Modern roll forming machines often come equipped with automation features for precise control.
Prototype and Test
Before going full throttle into production, create prototypes and conduct testing. Prototyping allows you to validate your design, identify potential issues, and make necessary adjustments without affecting production schedules.
Roll Form Tooling Suppliers
- Roll form tooling suppliers are the supply chain partners that keep the metalworking industry running smoothly. These businesses offer a wide array of tooling components and accessories, ensuring roll formers and manufacturers can access the essential parts they need. These suppliers maintain extensive catalogs of standard tooling products, from rolls and dies to guides and spacers. In addition to standard offerings, they often provide customization services to meet unique roll forming requirements.
- Roll form suppliers ensure a steady supply of high-quality tooling components, helping manufacturers maintain production efficiency. They also offer valuable technical support and expertise, making them trusted partners in the roll forming industry. Whether you require standard components or customized solutions, roll form tooling suppliers are your go-to source for all things tooling-related.
Final Words
In the world of metalworking, roll forming is a proper art form. It requires a fusion of creativity and engineering precision. By leveraging CAD software, FEA tools, and roll forming simulation software, you can bring your design ideas to life and ensure they are structurally sound. Remember to consult industry guidelines, choose suitable materials, and maintain meticulous attention to detail during production.
FAQs
Roll forming is a metalworking process that shapes flat metal sheets or strips into complex profiles. It’s essential because it allows the cost-effective production of custom-shaped metal products in various industries like construction, automotive, and appliance manufacturing.
Roll forming design is the process of planning and creating the specifications for roll-formed profiles. It matters because a well-thought-out design is crucial for achieving precise and efficient results in the roll forming process.
Several websites and software providers offer free roll forming design software for download. These tools often come equipped with CAD capabilities and can help streamline the design process.
When designing roll-formed profiles, consider material properties, profile complexity, tooling requirements, and potential manufacturing challenges. These elements all play a significant role in the design’s success.
Selecting the right roll forming tools involves collaborating with tooling manufacturers or suppliers who can provide customized solutions based on your project’s specific requirements. Precision and compatibility are key factors to consider.