In the world of manufacturing, precision is more than just a buzzword – it’s the cornerstone of excellence. When it comes to sheet metal companies, precision isn’t a luxury; it’s an absolute necessity. In this comprehensive exploration, we will delve into the paramount importance of precision in sheet metal manufacturing. We’ll cover everything from understanding precision in sheet metal to real-life examples of its applications, all while shedding light on current trends, innovative processes, and the advantages that precision manufacturing brings to various industries.
Understanding Precision in Sheet Metal
Precision in sheet metal manufacturing refers to the meticulous attention to detail and the ability to consistently produce components or products that meet exact specifications, tolerances, and quality standards. In simpler terms, it means getting it right, every time. This level of precision is non-negotiable for sheet metal companies because their products serve as vital components in diverse industries.
Applications Across Industries
Sheet metal components find applications across a multitude of industries. Their versatility and durability make them indispensable in:
- Automotive Industry: In the automotive sector, precision sheet metal parts are used in the fabrication of vehicle bodies, chassis, and engine components. These parts must conform precisely to design specifications to ensure safety and performance.
- Aerospace Industry: In aerospace, precision is a matter of life and death. Sheet metal components are used in aircraft structures, engines, and interior fixtures. Precision is critical to maintain structural integrity and aerodynamic performance.
- Electronics Industry: From computer casings to smartphone components, precision sheet metal plays a pivotal role in the electronics industry. Tight tolerances are essential to ensure the functionality and reliability of electronic devices.
- Medical Industry: In medical equipment manufacturing, precision is paramount. Sheet metal components are used in diagnostic devices, surgical instruments, and healthcare infrastructure. Precision ensures the accuracy and safety of medical procedures.
- Architectural and Construction Industry: Sheet metal products find applications in architectural cladding, roofing, and structural elements. Precision manufacturing ensures that architectural designs are realized accurately.
Types of Precision Manufacturing Processes
Achieving precision in sheet metal manufacturing requires the utilization of advanced processes and technologies:
- Laser Cutting: Laser cutting is a precise and efficient method for shaping sheet metal. A focused laser beam melts, vaporizes, or blows away the material, creating intricate shapes with minimal material wastage.
- CNC Machining: Computer Numerical Control (CNC) machining involves the use of automated machines to precisely remove material from sheet metal, creating highly accurate components.
- Bending and Forming: Precision bending and forming machines allow sheet metal to be shaped into complex geometries with tight tolerances.
- Welding: Welding processes like TIG and MIG are used to join sheet metal components with precision, ensuring structural integrity and leak-free seams.
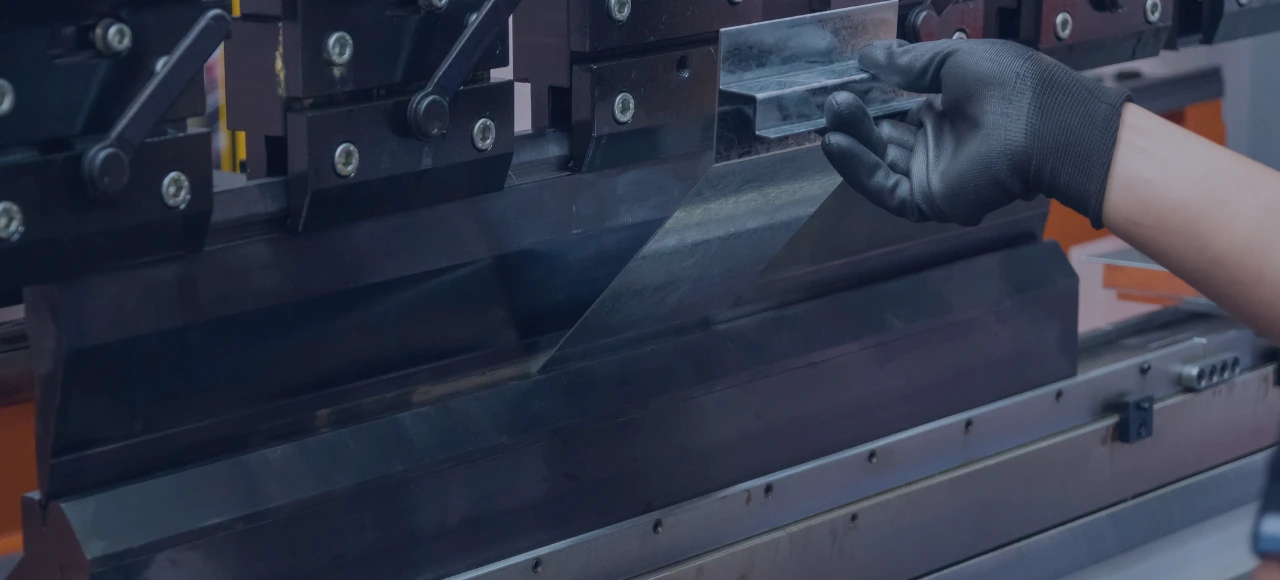
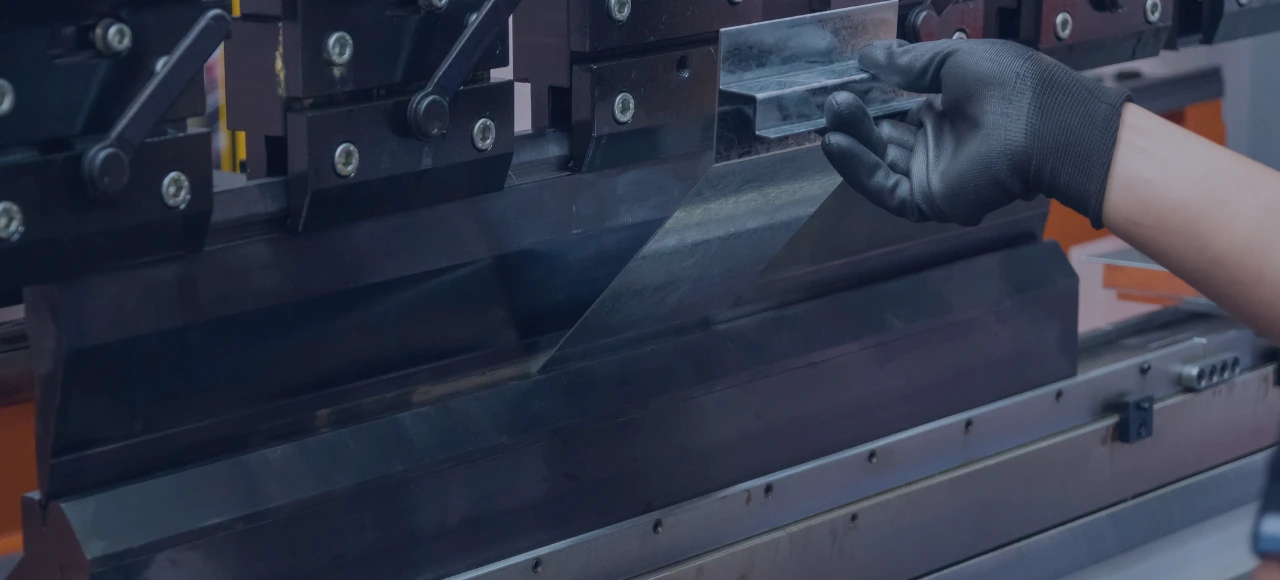
Challenges in Achieving Precision
While precision is a top priority, sheet metal companies encounter several challenges along the way:
- Material Variability: Sheet metal comes in various grades and thicknesses, each with its own properties. Managing these material variations is essential to maintain precision.
- Tool Wear: Tools used in sheet metal fabrication, such as dies and punches, wear over time. Regular maintenance and replacement are necessary to prevent deviations in component dimensions.
- Environmental Factors: Temperature and humidity fluctuations can affect the dimensions of sheet metal. Controlling environmental conditions within the fabrication facility is crucial.
- Quality Control: Maintaining consistent quality throughout the manufacturing process requires stringent quality control measures and inspections.
Measures to Overcome Challenges
To address these challenges effectively, sheet metal companies implement several measures:
- Material Testing and Selection: In-depth material testing helps select the right sheet metal grade for a specific application, ensuring that it meets the required specifications.
- Tool Maintenance and Calibration: Regular tool maintenance and calibration routines prevent variations due to tool wear and ensure precise manufacturing.
- Controlled Environment: Maintaining a controlled manufacturing environment minimizes the impact of temperature and humidity fluctuations on sheet metal dimensions.
- Quality Assurance Protocols: Stringent quality control protocols, including visual inspections and precise measurements, are integral to maintaining precision.
- Material Selection for Precision: Material selection is a critical aspect of precision sheet metal manufacturing. Different materials are chosen based on their properties and suitability for specific applications:
- Stainless Steel: Stainless steel is corrosion-resistant and ideal for applications where hygiene and durability are paramount, such as medical equipment and kitchen appliances.
- Aluminum: Aluminum’s lightweight nature and corrosion resistance make it a preferred choice in industries like aerospace and automotive.
- Corten Steel: Corten steel’s weathering properties and distinct appearance find applications in architectural cladding and outdoor sculptures.
Current Trends and Innovations
The precision sheet metal manufacturing industry is undergoing a remarkable transformation, driven by technological advancements and changing market demands. Staying ahead of these trends is essential for companies to maintain a competitive edge and deliver top-notch products. Let’s explore some of the most prominent trends and innovations, supported by data and real-world examples:
Automation Revolution
According to a report by MarketsandMarkets, the global sheet metal fabrication services market is projected to grow at a CAGR of 3.7% from 2021 to 2026.
- Trend: Automation is reshaping the sheet metal manufacturing landscape. Robotic arms, CNC machines, and automated systems are increasingly replacing manual labor, resulting in enhanced efficiency and precision.
- Example: A leading aerospace manufacturer implemented robotic welding and laser cutting systems, reducing production time by 40% and achieving precision within microns.
Digitalization and Industry 4.0
A survey by PwC found that 72% of industrial companies have either started to implement Industry 4.0 solutions or plan to do so within the next five years.
- Trend: The integration of digital technologies, such as the Internet of Things (IoT) and data analytics, into sheet metal manufacturing processes is on the rise. Real-time monitoring and data-driven decision-making are becoming industry standards.
- Example: A sheet metal fabrication facility introduced IoT sensors to monitor machine performance. Predictive maintenance reduced downtime by 30%, ensuring consistent precision.
Advanced Materials
The global advanced materials market is expected to reach USD 1,514.2 billion by 2028, growing at a CAGR of 8.9% from 2021 to 2028.
- Trend: Innovations in materials, including lightweight composites and high-strength alloys, are expanding possibilities in precision sheet metal manufacturing. These materials offer improved strength-to-weight ratios and corrosion resistance.
- Example: A leading automotive manufacturer adopted advanced aluminum alloys in their precision sheet metal components, reducing vehicle weight by 15% while maintaining structural integrity.
Sustainability and Eco-Friendly Practices
A survey by McKinsey found that 67% of consumers consider sustainability when making a purchase.
- Trend: The industry is increasingly focused on sustainable manufacturing practices, from eco-friendly materials to energy-efficient processes. Precision manufacturing with minimal waste aligns with sustainability goals.
- Example: A sheet metal company implemented a closed-loop recycling system, reducing material waste by 20% and earning certifications for eco-friendly manufacturing.
Additive Manufacturing Integration
According to SmarTech Analysis, the global market for 3D printing in metals is projected to reach USD 4.5 billion by 2026, with a CAGR of 23.7% from 2021 to 2026.
- Trend: Additive manufacturing, including 3D printing of metals, is being integrated into precision sheet metal processes. This allows for intricate designs and rapid prototyping.
- Example: An aerospace manufacturer utilized 3D printing to create complex sheet metal components with internal channels for improved airflow, reducing fuel consumption by 8%.
Customization and Design Innovation
Deloitte reports that 36% of manufacturers say customization is a key driver for adopting advanced manufacturing technologies.
- Trend: Customers increasingly demand customized sheet metal components tailored to their specific needs. Advanced design tools and flexible manufacturing processes enable high levels of customization.
- Example: An architectural firm collaborated with a precision sheet metal manufacturer to create a bespoke cladding system with unique geometric patterns for a landmark building.
Supply Chain Resilience
- The COVID-19 pandemic exposed vulnerabilities in supply chains. As a result, many manufacturers are investing in resilience measures.
- Trend: Companies are diversifying their supplier base and implementing digital supply chain solutions to mitigate disruptions and ensure a steady flow of materials.
- Example: A medical equipment manufacturer partnered with multiple precision sheet metal suppliers in different regions to ensure a continuous supply of critical components during the pandemic.
In conclusion, the importance of precision in sheet metal companies cannot be overstated. It’s the key to delivering high-quality, reliable, and cost-effective products across various industries. As technology and innovation continue to advance, precision manufacturing will remain at the forefront of sheet metal fabrication, shaping the world in which we live and work.
Zetwerk, a leader in precision manufacturing, can be your strategic partner in achieving precision in sheet metal manufacturing. With access to a vast network of experienced fabricators and cutting-edge technology, Zetwerk ensures that your sheet metal components meet the highest standards of precision. Whether you’re in aerospace, automotive, or any other industry, Zetwerk can help you manufacture sheet metal components that adhere to the most demanding specifications.




FAQs
Precision ensures that sheet metal components meet exact specifications, contributing to product quality and reliability.
Common materials include stainless steel, aluminum, and Corten steel, chosen based on their properties and applications.
Achieving precision requires material testing, tool maintenance, controlled environments, and stringent quality control.