Roll forming is a versatile metalworking process that finds applications across various industries, from automotive and construction to aerospace and beyond. One of the critical decisions you’ll face when embarking on a roll forming project is whether to use hot or cold roll forming. Both processes have their strengths and limitations, making it essential to choose the right one for your specific application. In this blog, we’ll explore roll forming and its key differences, advantages, and considerations when choosing between hot and cold roll forming.
Hot Roll Forming: The Heat Is On
Hot roll forming is the older of the two methods. It involves shaping metal profiles while the material is heated. Typically, hot roll forming is used for thicker and more rigid materials like steel. Here are some of the notable characteristics and advantages of hot roll forming:
- Forming Heated Materials: The main advantage of hot roll forming is the ability to work with heated materials. When metal is hot, it’s more malleable and accessible to form into intricate shapes. This process is excellent for structural components that require precise and complex designs.
- Reduced Material Hardness: During the hot roll forming process, the material’s hardness is reduced. This means that hot-formed components are often less brittle and more durable.
- Faster Production: Hot roll forming can result in quicker production cycles. The reduced material hardness and increased malleability allow for higher production speeds.
- Lower Force Requirements: Because the metal is heated, less force is required to bend it. This results in reduced wear and tear on the machinery.
Cold Roll Forming: Keeping It Cool
On the other hand, cold roll forming involves shaping the metal without heating it. This process is typically used for thinner materials and offers a distinct set of advantages:
- Precision: Cold roll forming is excellent for achieving precise, consistent shapes. The absence of heat-related expansion and contraction ensures a high degree of accuracy.
- Versatility: Cold-formed sections can be made from various materials, including steel, aluminum, and alloys. This versatility makes it suitable for multiple applications.
- Reduced Material Waste: The lack of heating means no scale or decarburization on the material’s surface, reducing waste and the need for additional processes.
- Cost-Efficiency: Cold roll forming can be more cost-effective with suitable materials and profiles. It’s beneficial for high-volume production.
Choosing Between Hot and Cold Roll Forming
Now that we’ve explored the primary differences between hot and cold roll forming, how do you choose the proper process for your project? Here are some key considerations:
- Material Selection: The choice of material often dictates the roll forming process. Hot roll forming is preferred for complex and thick materials, while cold roll forming works well with a more extensive range of metals.
- Complexity of the Profile: Hot roll forming may be the way to go if your project involves intricate and complex profiles. Cold roll forming is excellent for simpler designs requiring precision.
- Production Volume: For high-volume production, cold roll forming is generally more cost-effective. Hot roll forming might suit lower volume runs due to higher tooling costs.
- End Use: Consider the final application of the roll-formed components. Hot roll forming may be the better choice if strength and durability are paramount.
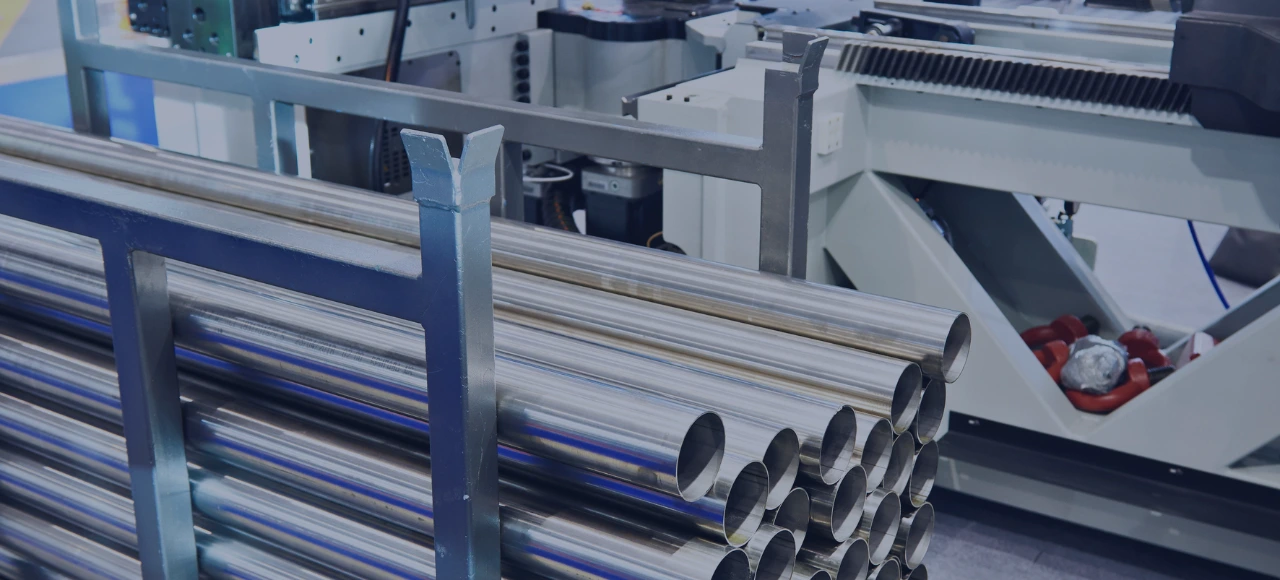
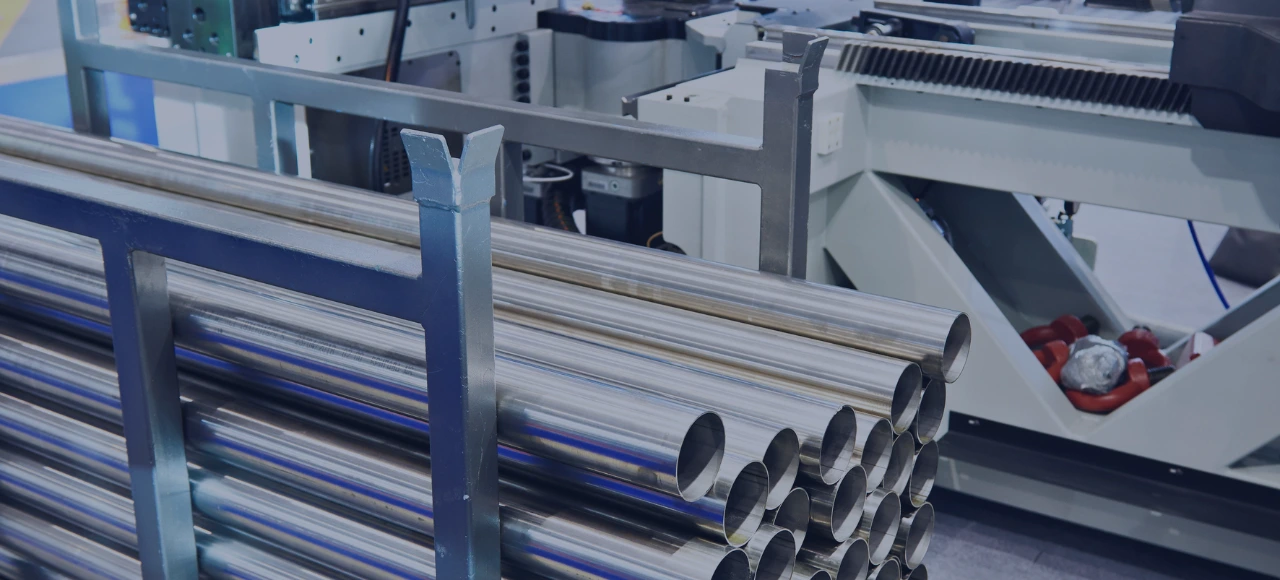
Hot Rolled vs. Cold Formed
Hot rolling and cold forming are two distinct methods used in metalworking, each with advantages and applications. Hot rolled steel is processed at high temperatures, making it more malleable, while cold-formed steel is shaped at or near room temperature, resulting in improved dimensional control and surface finish. The choice between them depends on the specific requirements of a project.
Cold Formed vs. Hot Rolled
Cold-formed and hot-rolled sections differ in their mechanical properties and production methods. Burning sheets at room temperature produces cold-formed sections, resulting in increased strength and dimensional accuracy. In contrast, hot-rolled sections are manufactured at high temperatures, making them less precise but more cost-effective for specific applications.
Cold Formed vs. Cold Rolled
These terms are sometimes used interchangeably, but they refer to different processes. Cold-formed typically involves bending metal sheets into shapes, while cold-rolled refers to reducing the thickness of metal sheets through rolling without changing their shape. Both methods have their uses, with cold-formed being more about shaping and cold-rolled focused on thickness reduction.
Cold Form vs. Hot Rolled
Choosing between cold-formed and hot-rolled steel depends on your project’s requirements. Cold-formed steel offers better control over dimensions and is often used in applications requiring precise shapes, while hot-rolled steel is more cost-effective and suitable for projects where dimensional accuracy is less critical.
Hot and cold roll forming each offer unique advantages and are best suited for particular applications. Choosing the proper process is crucial to achieving roll forming excellence. So, whether you’re crafting structural steel beams, automotive components, or something entirely different, remember that the heat, or lack thereof, can make all the difference in your roll forming success. Make your choice wisely, and roll on to success!



FAQs
When deciding between hot and cold roll forming, consider factors like material strength, precision, surface finish, and the specific requirements of your project. It’s essential to match the process with the application’s needs.
Cold roll forming is ideal for products requiring tight tolerances and precise shapes. Some examples include automotive components, window frames, and parts for solar panel installations.
Yes, hot roll forming is generally more cost-effective due to the reduced energy requirements and faster production. Cold roll forming, while offering higher precision, may be more expensive.
It’s advisable to consult with a roll forming expert or engineer who can assess your project’s requirements and recommend the most suitable process based on factors like material properties, tolerances, and surface finish.