In the dynamic world of construction and industrial infrastructure, the art and science of transforming steel into foundational elements are pivotal. Here, we delve into the intricate journey of steel sheet fabrication and how steel fabrication companies transmute raw materials into towering engineering marvels.
The Essence of Structural Steel Fabrication
Structural steel fabrication is the metamorphosis of basic steel into bespoke components ready for assembly. Think of the majestic bridges, towering skyscrapers, and sprawling warehouses. Behind these structural marvels lies the intricate and precision-driven steel fabrication process.
Steps in Structural Steel Fabrication
- Design Preparation: The genesis of any steel fabrication project. Comprehensive blueprints, detailing, and plans are established, ensuring a precise and efficient manufacturing process.
- Material Acquisition: Post-design, the procurement of requisite materials takes place. This involves liaising with suppliers to obtain the correct steel type, shape, and size.
- Steel Cutting and Drilling: Advanced machinery, including CNC machines and laser cutting devices, slice and dice the steel with pinpoint accuracy.
- Bending and Welding: Various bending techniques mold the steel into its desired shape, followed by expert welding, ensuring the individual components merge into a single, cohesive unit.
- Quality Check: Rigorous inspections and tests ascertain the steel components are pristine and up to industry standards.
- Finishing: A protective layer, often paint or another sealant, is applied to shield the steel from potential corrosion.
- Delivery, Assembly, and Installation: The finale! Finished steel components are transported to the construction site, where they are meticulously assembled and installed.
Titans of the Steel Fabrication Industry
In the vast domain of steel fabrication companies, specific names resonate with prominence and excellence:
- Zetwerk
- ArcelorMittal SA
- Tata Steel
- POSCO Holdings Inc
- Nippon Steel Corp
- HBIS Group
- Baowu
- Nucor Corp
- Shagang Group
- Ansteel Group
Collectively, these giants represent the pinnacle of innovation and quality, shaping the trajectory of the steel industry.
Critical Considerations in the Fabrication Process
- Project Planning: A robust plan, replete with schedules, budgets, and detailed blueprints, is the cornerstone of any successful fabrication project.
- Understanding Customer’s Requirements: Effective communication and clarity of purpose are essential. It ensures the end product resonates with the client’s vision and requirements.
- Analyze your Capabilities: Assessing company strengths, weaknesses, and available resources can significantly streamline fabrication. By conducting a SWOT analysis, you’ll identify what’s achievable and what might need external input.
- Shortlisting Vendors: The right vendors play a vital role. Reputed vendors boasting certifications from established authorities can significantly impact the project’s outcome.
- Analyzing Project Progress: Close monitoring and periodic reporting ensure the project remains on track. Every team member’s input is invaluable, from shop floor workers to the foreman.
- Ensuring Quality and Safety: Both are paramount in steelwork fabrication. Regular inspections, adherence to safety guidelines, and a robust quality control plan are non-negotiable.
In steel fabrication, meticulous attention to detail, expertise, and adherence to quality standards distinguish the best steel fabrication companies. As industries and skylines evolve, the significance of steel sheet fabrication will continue to be a linchpin in our architectural and infrastructural advancements.
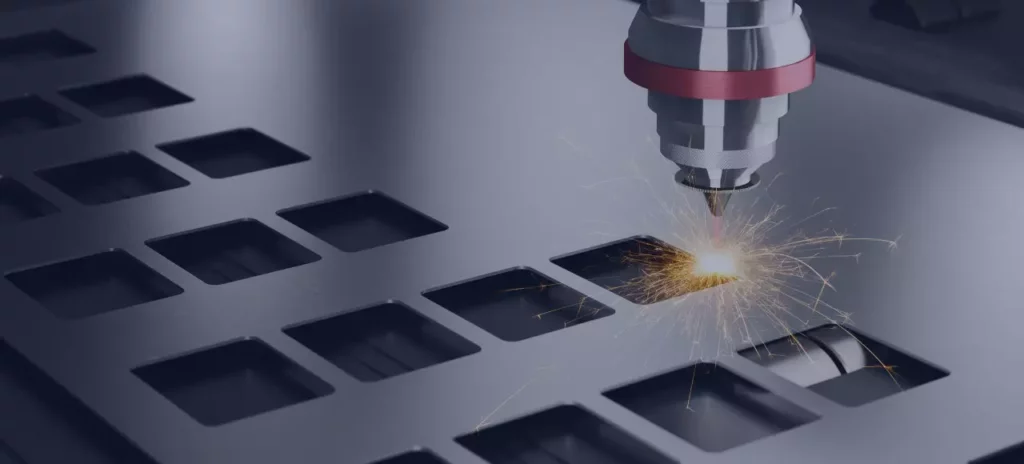
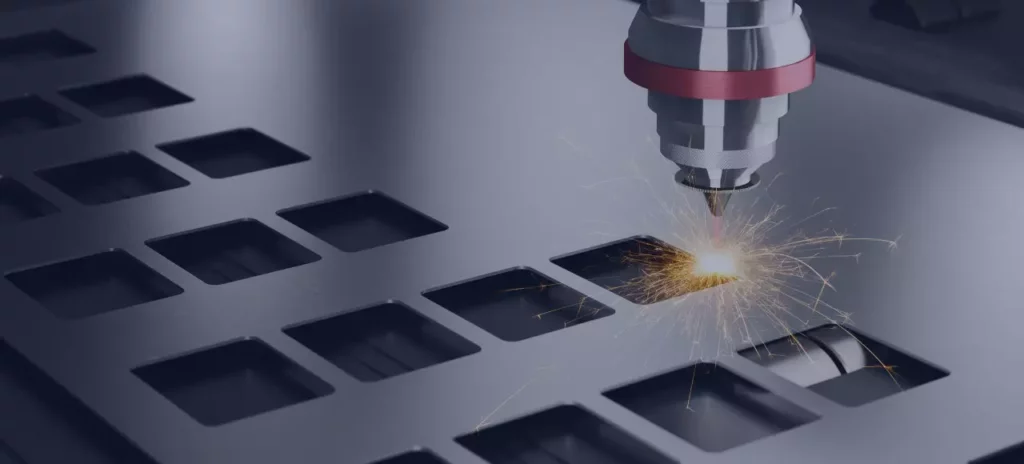
Advancements in Steel Fabrication Techniques
The world of steel fabrication is growing. With technological advancements, the industry has witnessed many innovations enhancing the finished product’s efficiency, precision, and overall quality. Let’s explore some of these advancements.
- Adaptive Technologies: Modern machinery has evolved significantly. Plasma cutting machines, for instance, have become more versatile, allowing for the cutting of various metals, including aluminum and stainless steel. This adaptability ensures precision even with complex fabrications.
- Automation and Robotics: Automation in steel fabrication is becoming more prevalent. Robots equipped with welding tools or cutting devices can execute repetitive tasks with unmatched accuracy, significantly reducing the time and potential human error.
- 3D Printing: Previously reserved for plastics and select materials, 3D printing is making its mark in the steel industry. This technology allows for more intricate designs and offers an efficient method for prototype development. It’s a game-changer, especially for complex components.
- Sustainability: With the growing emphasis on green and sustainable practices, steel fabrication is also under transformation. The industry focuses more on using recycled steel and reducing waste during fabrication. This not only conserves resources but also significantly reduces the carbon footprint of steel products.
- Improved Communication with Clients: With technology at the forefront, steel fabrication companies now use digital platforms to engage with clients. Whether sharing 3D models, real-time project updates, or conducting virtual site visits, the digital transformation ensures transparent and efficient communication.
Beyond the Basics: Specialized Fabrication Techniques
Beyond the fundamental processes, specialized techniques are employed based on the project’s requirements and the specific challenges posed
- Rolling: For curved pieces of steel, like tubes or pipes, moving is a popular method. This process involves passing a steel sheet through rolls that curve it.
- Chipping: Occasionally, welding can cause splatter or leave undesired projections on the steel. Chipping involves removing these extra bits to ensure a smooth finish.
- Punching: When holes are required in a steel piece, punching is the method of choice. It’s a process wherein steel is placed under a die and subjected to enough pressure to create a hole.
- Shearing: Sometimes, steel sheets need to be reduced in size. Shearing is a cutting method where large sheets are cut into smaller ones without the formation of chips or the use of melting or burning.
Challenges Facing the Industry
- While the steel fabrication industry is advancing, it’s not without challenges. One of the most pressing is the fluctuating cost of raw materials, which can significantly affect project budgets. Furthermore, with new technologies, there’s an increased need for skilled professionals adept in modern machinery and software.
- However, as history suggests, the steel fabrication industry is resilient and adapts swiftly to the changing tides. With continued investments in R&D and a focus on sustainable practices, it’s poised for a future that promises innovation and growth.
Steel fabrication, a testament to the synthesis of art and science, stands at the crossroads of tradition and innovation. With giants like Zetwerk leading the way, the industry confronts challenges, paving the path for a sustainable and advanced future. As our cities and infrastructures continue to evolve, the importance of steel fabrication remains undiminished, poised to shape the horizons of tomorrow.




FAQs
The process begins with design preparation, where comprehensive blueprints, detailing, and plans are established.
The industry uses advanced machinery like CNC machines, laser cutting devices, and plasma cutting machines to work with steel accurately.
The industry grapples with fluctuating raw material costs and the need for professionals skilled in new technologies and software.
They undergo rigorous inspections and tests to ensure the steel components meet industry standards. Additionally, they maintain a robust quality control plan and adhere to safety guidelines.
The industry continually evolves with innovations like adaptive technologies, automation, robotics, 3D printing, and digital communication platforms.