Custom metal trim fabrication is an art that has been perfected over centuries. It’s a blend of craftsmanship, technology, and creativity that transforms raw metal into functional trims for various applications. From interior design to architectural detailing, custom metal trims are a stabilizing element that brings convenience and personality to spaces. In this blog, we will discuss custom metal trim fabrication in detail, uncovering the processes involved, its diverse applications, and its prospects.
The Art of Custom Metal Trim Fabrication
Custom metal fabrication involves the transformation of metal sheets and rods into various shapes, patterns, and sizes to complement the aesthetics and functional requirements of a specific project. It’s an intricate craft that combines traditional metalworking techniques with modern technologies like laser cutting, CNC machining, and 3D printing. The artisans behind these creations are skilled metalworkers who understand the properties and possibilities of various metals, including stainless steel, aluminum, brass, and copper.
The process begins with a clear understanding of the project’s requirements. Whether it’s a grand entryway in a luxury hotel, ornate railings for a historic restoration, or contemporary accents in a modern interior, each project has unique demands. The metal trim fabricator collaborates closely with designers, architects, and clients to ensure the final product aligns with the envisioned design.
The Intricate Process of Custom Metal Trim Fabrication
Custom metal fabrication is a meticulous and multifaceted process that demands a combination of craftsmanship, precision, and artistry. Let’s take a closer look at the various steps involved in this intricate journey from raw metal to finely crafted trim:
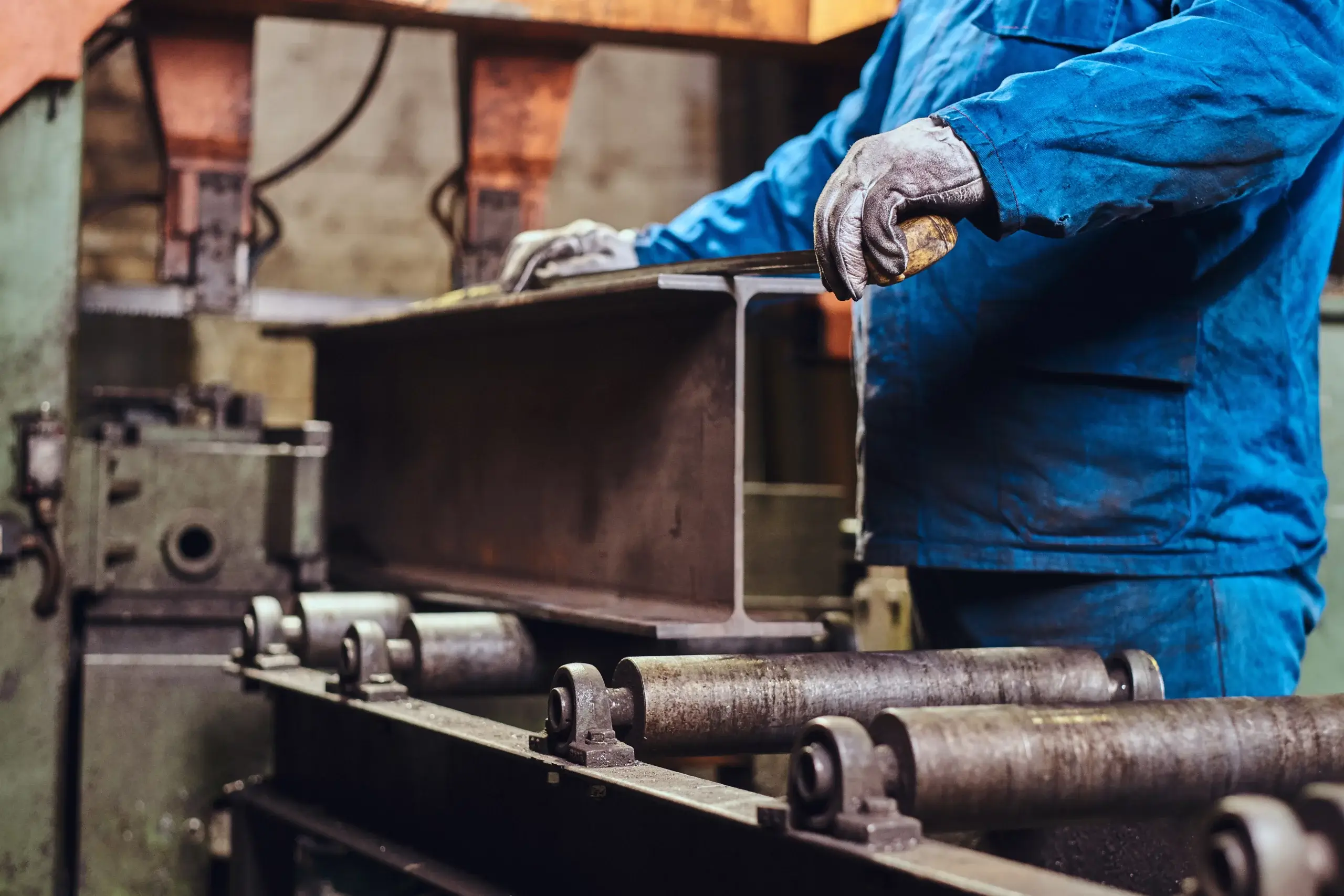
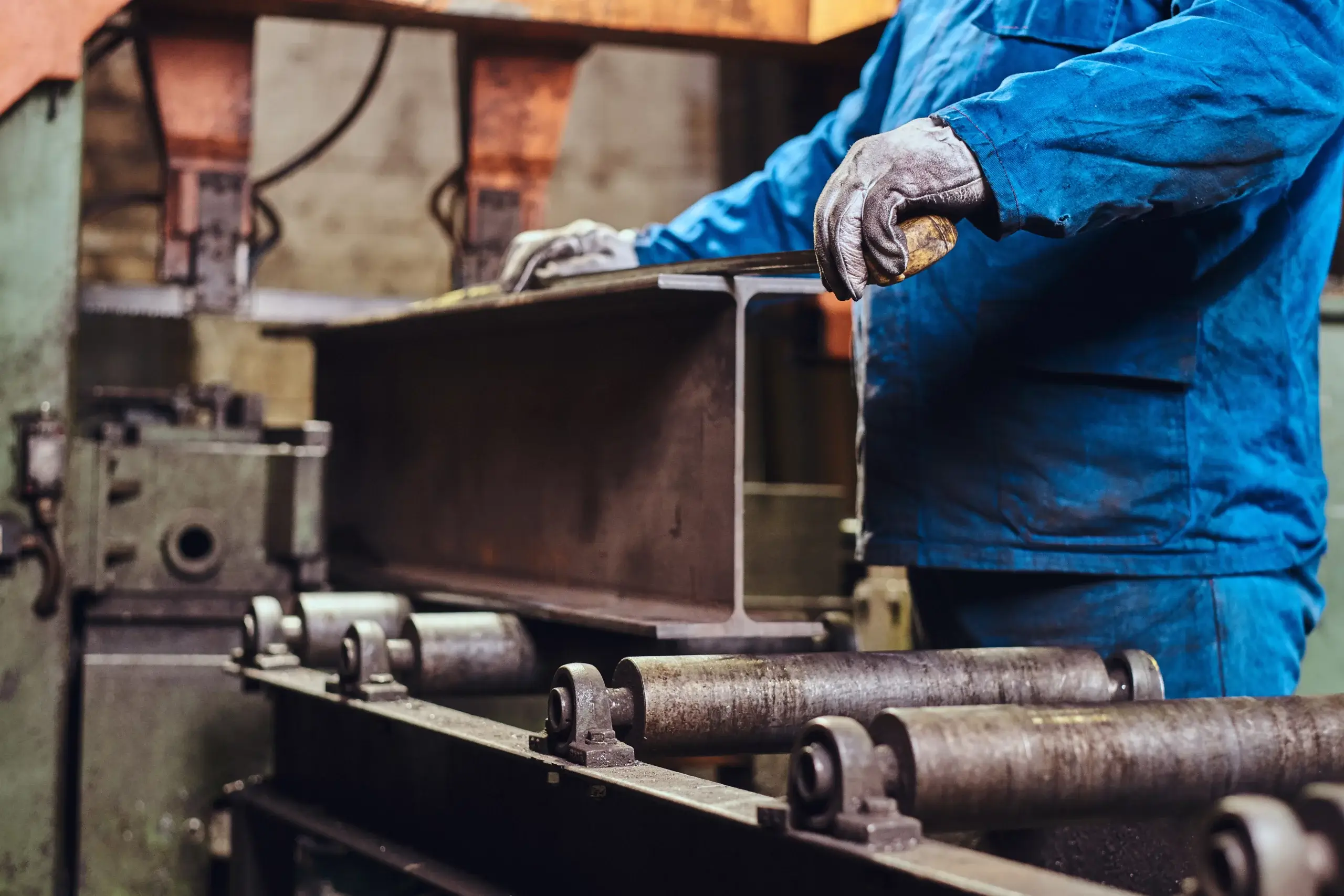
Design and Conceptualization
The process begins with a clear vision and concept. Designers, architects, and clients collaborate to define the shape, size, and style of the custom metal trim. This initial phase involves sketching, prototyping, and digital design to ensure the final product aligns with the intended aesthetics and functionality.
Material Selection
Choosing a suitable material is a crucial decision in custom metal fabrication. The material should be harmonious with the overall design and ideal for the intended application. Typical metals used include stainless steel, brass, copper, and aluminum. Each material offers distinct properties, such as corrosion resistance, durability, and aesthetic appeal.
Cutting and Shaping
Once the material is selected, it’s time to transform the raw metal into the desired shape. Traditional techniques, such as hammering, rolling, and bending, may be employed to create intricate patterns, curves, and textures. Modern methods like laser cutting, waterjet cutting, and CNC machining ensure precision and consistency, enabling the realization of complex and highly detailed designs. The precision of these machines is critical to maintaining the integrity of the design.
Surface Finish
The surface finish of the custom metal trim significantly influences its appearance and durability. Various finishes can be applied depending on the desired aesthetic and functional requirements. Standard surface finishes include:
- Polishing: This process involves smoothing the surface to a high sheen, creating a reflective, mirror-like finish, perfect for modern and luxurious settings.
- Satin Finish: A satin finish creates a soft, matte look, reducing the reflection of light and making it an excellent choice for pieces that require subtlety.
- Powder Coating: For enhanced durability and protection, a layer of powdered pigment is electrostatically applied and cured under heat, offering a wide range of color options.
Assembly and Installation
In many cases, custom metal trims are composed of multiple components that must be assembled before installation. This assembly process requires careful attention to detail to ensure that each part aligns perfectly with the design. Once assembled, the trims are expertly installed in their designated spaces, whether architectural elements in a building, interior accents in a home, or ornate embellishments on a vehicle.
Quality Control
Quality control is a critical phase in the process. Skilled fabricators meticulously inspect each piece for imperfections or deviations from the design specifications. This thorough examination ensures that the final product meets the highest standards of craftsmanship and meets the client’s expectations.
Customization and Personalization
One of the primary advantages of custom metal fabrication is the ability to personalize each piece. Depending on the client’s preferences, unique engraving, etching, or custom patterns can be added to the trim. This level of personalization sets custom metal trims apart from mass-produced alternatives.
Final Inspection and Delivery
Once the custom metal trims have passed all quality control checks and any necessary customizations are completed, they are prepared for delivery to the client. Packaging is carefully executed to protect the trims during transportation. The delivery process culminates the collaborative effort between the fabricator and the client, ensuring that the final product is met with satisfaction and delight.
Diverse Applications of Custom Metal Trim Fabrication
Custom metal fabrication is a versatile craft with applications spanning various industries. Here are a few notable examples:
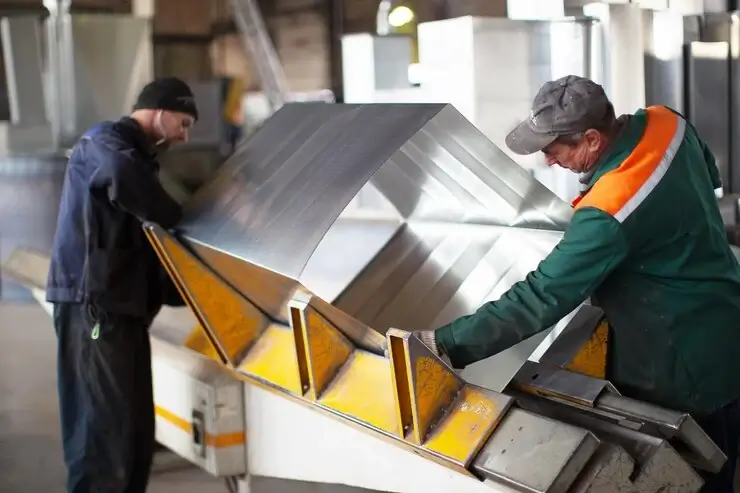
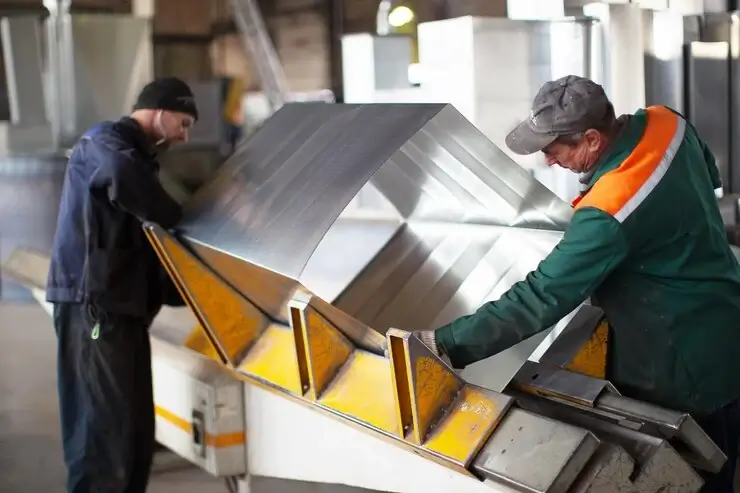
1. Architectural Detailing
Architects and builders use custom metal trims to enhance the overall aesthetics of a building. Whether it’s decorative facades, ornate railings, or elaborate window frames, these trims add a touch of elegance and sophistication to structures.
2. Interior Design
In interior design, custom metal trims are pivotal in creating unique and inviting spaces. They can be integrated into furniture, lighting fixtures, and cabinetry, providing a personalized touch that reflects the homeowner’s style.
3. Automotive Industry
Car enthusiasts often turn to custom metal trims to personalize their vehicles. From chrome accents to bespoke grilles, these trims can transform a standard vehicle into a work of art.
4. Marine and Aviation
In luxury yachts and private jets, custom metal trims are essential for creating opulent and customized interiors. The precision and craftsmanship required in these industries are unparalleled.
5. Historical Restoration
Restoring historical landmarks often requires replicating intricate metal trims and ornamentation. Custom metal trim fabrication ensures that the historical integrity of a building is preserved.
The Future of Custom Metal Trim Fabrication
As technology advances, custom metal fabrication will likely benefit from these innovations. 3D printing, for instance, opens new possibilities for creating complex, intricate designs that were once considered too difficult to craft by hand. Additionally, using sustainable materials and environmentally friendly techniques will become increasingly important as the world embraces more eco-conscious design practices.
Conclusion
Custom metal trim fabrication is an age-old art that thrives in the modern world. It combines a deep understanding of materials with creativity and craftsmanship, resulting in stunning, personalized trims. Custom metal fabrication is all about using intricate sets of tools and machines. Here at Zetwerk, we’ve honed our expertise in various metal fabrication methods to serve customers in different commercial and industrial sectors.




FAQs
Custom metal trim fabrication creates custom-designed metal trims, often used in architectural, interior, and automotive applications. It’s important in design because it allows for personalization, adding a unique and stylish touch to spaces and structures.
Stainless steel, brass, copper, and aluminum are commonly used in custom metal trim fabrication. Each metal offers distinct properties and aesthetic possibilities, allowing for versatility in design.
Custom metal trims are made through traditional techniques like hammering, bending, and rolling, as well as modern methods such as laser cutting and CNC machining. These techniques ensure precision and enable the creation of intricate designs.
Custom metal trims are used in various applications, including architectural detailing, interior design, the automotive industry, marine and aviation, and historical restoration. They add aesthetic appeal, personalization, and durability to these projects.
Many custom metal trim fabricators prioritize sustainability by using eco-friendly materials, minimizing waste, and employing environmentally responsible techniques. This commitment to sustainability aligns with the growing demand for eco-conscious design practices.