Metal fabrication is a fundamental pillar of the contemporary industrial era, providing tailored solutions to unique challenges. Steel cone fabrication, a prime example of this innovation, is a vital tool for key automotive, aerospace, construction, and manufacturing industries. A deep understanding of steel cone fabrication is crucial in a world where precision and customization are non-negotiable.
The Genesis: What is Steel Cone Fabrication?
At its core, steel cone fabrication transforms flat steel sheets into conical or truncated cone shapes. These conical shapes serve many applications, from machinery components to construction elements, bearing testimony to the versatility of metal fabrication processes.
Applications in Different Industries
- Automotive: The nuanced contours of conical steel components are instrumental in exhaust systems and various engine parts.
- Aerospace: With precision at the forefront, steel cones are employed in aircraft components and engine assemblies, ensuring flight safety and efficiency.
- Construction: The robust nature of fabricated steel cones supports scaffolding, structural beams, and architectural elements.
- Manufacturing: Steel cones play pivotal roles in machinery and conveyor systems, optimizing operations and enhancing durability.
The Journey from Sheets to Cones- The Process
- Material Selection: The first step in the fabrication process involves choosing the suitable steel sheet. Factors like tensile strength, corrosion resistance, and weight are critical in this selection.
- Cutting and Shaping: Modern machinery, aided by laser or plasma cutting techniques, ensures precision in cutting the steel sheets into requisite sizes and shapes.
- Forming the Cone: Rolling machines gently curve the cut steel sheet into a conical form. The cone can be a right-angle, oblique, or truncated cone, depending on the specifications.
- Welding: Once the desired shape is achieved, the edges are seamlessly welded using advanced welding techniques to ensure structural integrity.
- Finishing Touches: To boost the longevity and appearance of the fabricated steel cone, finishing processes such as sandblasting, painting, or coating are implemented.
Advantages of Steel Cone Fabrication
- Customization: Every industry has unique requirements, and steel cone fabrication can meet these through custom sizes, thicknesses, and finishes.
- Durability: Steel cones, with their inherent strength and the added resilience from fabrication processes, promise longer lifespans.
- Cost-Effective: Given the efficiency of modern fabrication methods, businesses can achieve high-quality steel cones without straining their budgets.
Trends and Technological Advancements in Steel Cone Fabrication
As with most manufacturing sectors, the metal fabrication industry is rapidly advancing. Especially in steel cone fabrication, where technology and techniques continuously evolve to meet the stringent requirements of various sectors.
- Automation in Fabrication: Integrating automated systems into steel cone fabrication has revolutionized the speed and precision of production. Robotic arms, equipped with laser or plasma cutting tools, can produce complex shapes with minimal wastage. These automated systems are especially beneficial for large-scale projects where uniformity and high volumes are critical.
- 3D Modelling and Virtual Prototyping: 3D modeling software can create virtual prototypes of the desired steel cone before fabrication begins. This ensures that client specifications are meticulously met and significantly reduces the margin of error, as any discrepancies are identified and corrected in the virtual stage.
- Material Innovations: With sustainability and efficiency at the forefront, there are continuous developments in the types of steel used in fabrication. Alloys with enhanced corrosion resistance or those that offer greater tensile strength without adding weight are progressively becoming the materials of choice.
- Enhanced Quality Control: Advanced sensors and imaging techniques now monitor every stage of the fabrication process. These technologies can detect minute defects or inconsistencies in the fabricated steel cone, ensuring that the final product meets the highest quality standards.
- Personalized Fabrication with Big Data: The collection and analysis of Big Data allow for a better understanding of market demands. By analyzing trends, manufacturers can anticipate specific industry needs and tailor their steel cone fabrication processes accordingly. This level of customization was previously unattainable and opened doors to more niche applications of fabricated steel cones.
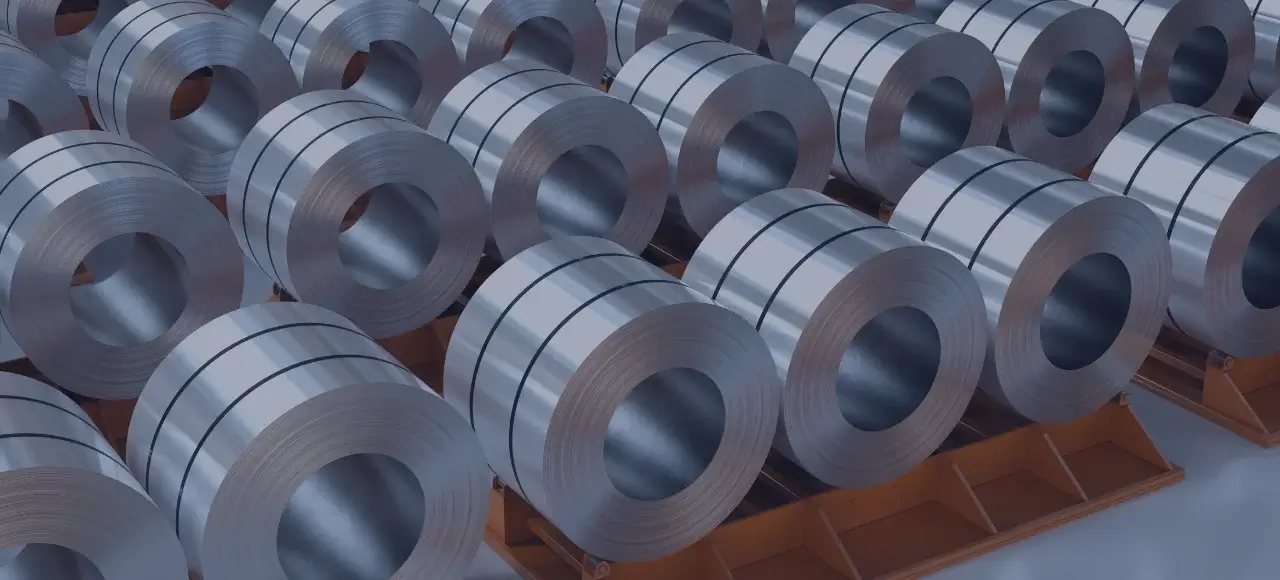
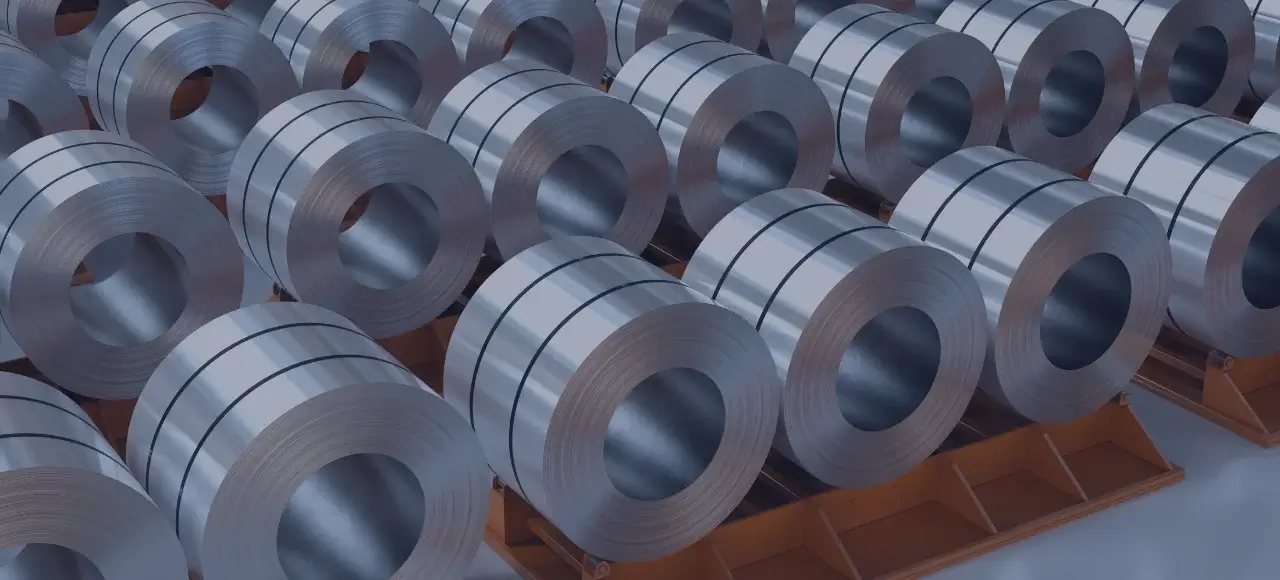
Understanding the Demand and Supply Dynamics
The growing need for steel cone fabrication can be traced back to the increasing complexity of modern industrial requirements. The push for greater efficiency and the demand for sustainable solutions place metal fabrication at the heart of these innovations.
- Green Manufacturing: With global attention shifting towards sustainable practices, the metal fabrication industry is moving towards methods that reduce waste, utilize sustainable materials, and minimize energy consumption. Eco-friendly coatings and finishes mitigate environmental impacts and are becoming standard in the industry.
- Global Supply Chains and Steel Cone Fabrication: The globalization of supply chains has increased demand for steel cone fabrication across borders. With industries sourcing parts from various parts of the world, the need for standardized yet customizable solutions has skyrocketed.
Emerging Industries and Their Reliance on Steel Cone Fabrication
As new industries emerge and technology progresses, the reliance on steel cone fabrication deepens. Some notable sectors include:
- Renewable Energy: Wind turbines and solar panel structures rely heavily on metal fabrication techniques. The cones in these structures, crafted meticulously, are crucial in optimizing performance.
- Space Exploration: As nations set their sights on the stars, the aerospace industry’s requirements become even more stringent. Steel cone fabrication provides components that can withstand the harshest conditions in outer space.
- Deep-Sea Exploration: Exploring the depths of our oceans necessitates equipment that can handle extreme pressure and corrosive environments. The industry gets equipment parts that fulfill these unique requirements through specialized steel cone fabrication.
Future of Steel Cone Fabrication
As industries expand and evolve, the metal fabrication sector, especially steel cone fabrication, will be a cornerstone of innovation. But what does the future look like?
- Integration of AI: Artificial Intelligence (AI) promises to revolutionize steel cone fabrication by predicting industry needs, automating complex processes, and enhancing precision.
- Nanotechnology in Metal Fabrication: This could redefine the very basics of fabrication. By manipulating materials at a molecular or atomic level, properties like strength, weight, and conductivity can be custom-engineered to unprecedented specifications.
- On-demand Fabrication: As industries move closer to a just-in-time manufacturing model, there will be a growing emphasis on real-time steel cone fabrication – crafting components as and when required without compromising quality or specifications.
Wrapping Up!
Industry dynamics are ever-changing, and steel cone fabrication positions itself at the intersection of tradition and advanced technology. Its versatility fuels advancements across diverse sectors, from aerospace to deep-sea exploration. With industry leaders like Zetwerk emphasizing precision, efficiency, and adaptability, the horizon for metal fabrication seems expansive and hopeful.
FAQs
Steel cone fabrication is a process where flat steel sheets are transformed into conical or truncated cone shapes. These shapes serve various applications in the automotive, aerospace, construction, and manufacturing industries.
Steel cone fabrication is crucial due to its versatility and customization capabilities. It addresses unique challenges and provides tailored solutions in various industries, enabling precision, durability, and cost-effectiveness in industrial applications.
Steel cone fabrication is widely used in automotive, aerospace, construction, manufacturing, renewable energy, space and deep-sea exploration industries.
The process includes material selection, cutting and shaping the steel sheets using modern machinery, forming the cone with rolling machines, welding the edges for structural integrity, and implementing finishing touches like sandblasting, painting, or coating.
Technological advancements like automation, 3D modeling, material innovations, enhanced quality control, and the incorporation of Big Data and AI have revolutionized steel cone fabrication, improving precision, speed, and customization in production.