Introduction
Custom stainless steel sink fabrication is a complex process that requires advanced knowledge and expertise. This comprehensive guide will provide valuable insights into the various stages and considerations involved in fabricating custom stainless steel sinks. From purchasing raw materials to the final packaging, this article will cover every aspect of the fabrication process. Whether you are an OEM, an EPC company, or an SME in the infrastructure, manufacturing, or construction business, this guide will equip you with crucial information to make informed decisions when it comes to custom stainless steel sink fabrication.
Understanding Custom Stainless Steel Sink Fabrication
The process of manufacturing tailored steel sinks is complex and has several processes.
Purchasing Raw Materials and Receiving Steel Sheets
To begin the process of custom stainless steel sink fabrication, raw materials are purchased based on the specific design requirements. Steel sheets with varying widths and thicknesses (ranging from 0.8mm to 1.5mm) are commonly used in sink manufacturing. These steel sheets are delivered to the sink factory in coils with a maximum width of 1220mm and unlimited length.
Laminating Film for Damage Prevention
To prevent cracking or damage during the stretching process, a laminating film is applied to one side of the steel sheet before or after cutting. The film acts as a protective layer against scratches and ensures the integrity of the steel sheet throughout subsequent processes.
Cutting and Corner Notching
The next step involves cutting the steel sheets into segments according to desired lengths and design requirements using a sheet metal cutting machine or advanced CNC machines. After cutting, corner notching is performed on each segment to roughly conform to the shape of the sink, resulting in a polygonal shape with arc edges.
Drawing Oil Application
Drawing oil is applied evenly to both sides of the coated and cut sheet metal before the first drawing process begins. This helps reduce the chance of cracking and extends the life of molds and presses. Additionally, cleaning is done after each drawing process to remove any contaminants or residual drawing oil from the sink’s surface.
Annealing for Strength and Magnetism
Annealing is an essential step in sink manufacturing. It involves heating sinks in a furnace at approximately 1150°C before slowly cooling them down. This process helps restore stainless steel’s strength and eliminates magnetism caused by stretching.
Secondary Drawing for Depth Requirements
Sinks with depths ranging from 180mm to 250mm often require a secondary drawing process to achieve desired depth requirements while ensuring quality and reducing chances of cracking.
Trimming, Hole Punching, Welding, and Spot Welding
After the second drawing process, trimming is performed to remove any excess material and achieve a proper sink shape. Stamping and hole punching are carried out on special molds to create drainage and overflow holes in the sink. Welding, including twin-tank roll welding or bottom welding basins, can be done using CNC welding machines or manually by skilled workers. Spot welding with a laser spot welder is used to attach reinforcing ribs/hooks to the sink.
Surface Treatment Techniques, Marking Methods, Repair Work, Spray Coating, Cleaning, and Packaging
Various surface treatment techniques such as sanding (drawing), sandblasting (electrolysis), polishing (mirror), and embossing are used to enhance the appearance of stainless steel sinks. Marking methods include laser marking and embossing marking for accurate positioning of information on sinks. Repair work is carried out on sinks with minor damages before spray coating to ensure commercial value and quality standards are met. Cleaning and packaging are necessary steps before sinks are ready for delivery.
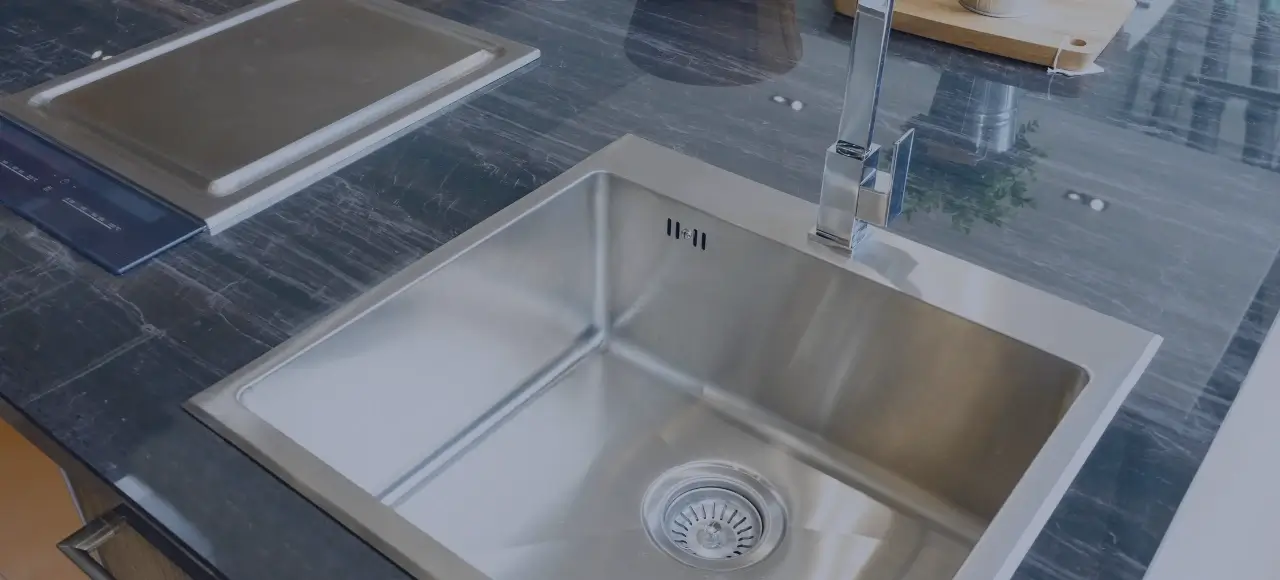
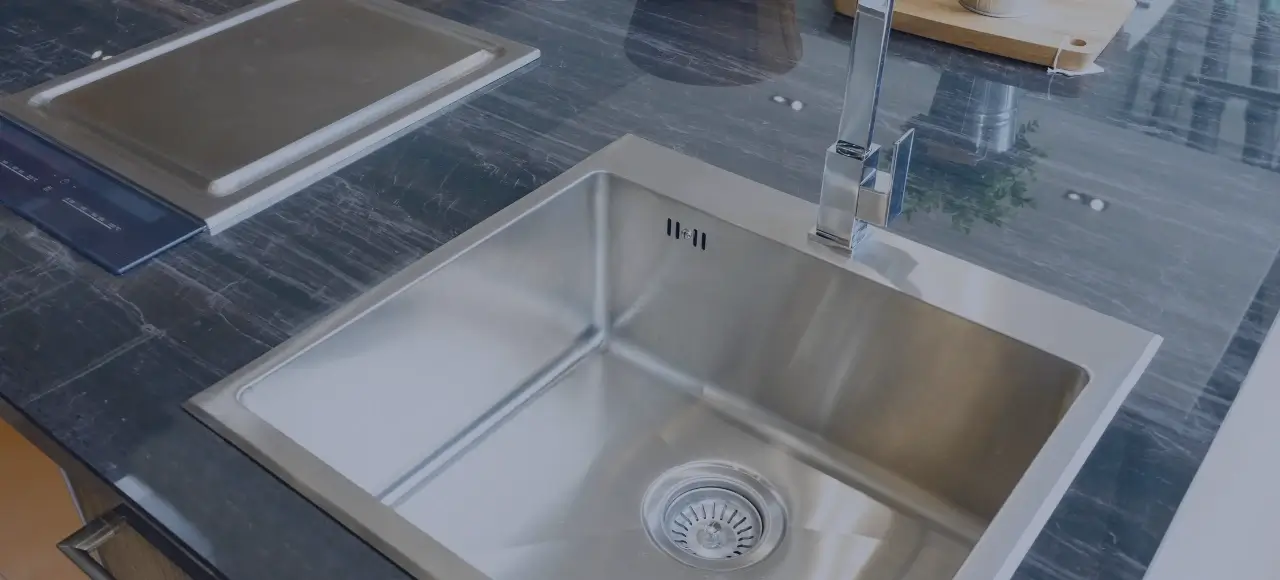
Key Considerations in Custom Stainless Steel Sink Fabrication
There are several noteworthy points to remember for checking the right manufacturer.
Selecting Reliable Custom Stainless Steel Sink Fabricators
When choosing the right supplier for custom stainless steel sink fabrication, it is crucial to select reliable partners who can meet your specific needs. Consider factors such as experience, expertise, quality control measures, and certifications. Collaborative partnerships with expert fabrication suppliers near you are vital for effective communication and efficient project management.
Evaluating Fabricators’ Capabilities
Evaluate fabricators’ capabilities in terms of equipment, facilities, production capacity, and material sourcing. Understanding their technological capabilities will help ensure that they can handle the complexity of your custom sink fabrication requirements.
Collaboration Throughout the Fabrication Process
Effective collaboration between fabricators and buyers is essential throughout the fabrication process. This includes design review meetings to discuss specifications and requirements and regular progress updates to ensure alignment and address any concerns or modifications.
Final Thoughts
In conclusion, custom stainless steel sink fabrication requires expertise and attention to detail at every stage. By understanding the process and considering key factors in selecting fabricators, businesses can benefit from sinks that meet their specific requirements. The advantages of custom stainless steel sinks make them a reliable choice for various industries.
For more information on custom manufacturing processes, including custom stainless steel sink fabrication, visit the Zetwerk Knowledge Hub. Discover a wealth of articles and resources to help you make informed decisions about your manufacturing needs.




FAQs
Standard thicknesses for steel plates in stainless steel sink fabrication range from 0.8mm to 1.5mm. These variations allow fabricators to cater to different design requirements and ensure durability and strength in the finished product.
To prevent cracking or damage, a laminating film is applied to one side of the steel sheet before cutting or after cutting in sink fabrication. This film acts as a protective layer, reducing the chance of structural issues during stretching.
Drawing oil is applied in sink fabrication to reduce the likelihood of cracking and extend the lifespan of molds and presses used in the drawing process. It provides lubrication, facilitating smooth deformation of the metal sheets.
Annealing is crucial in sink manufacturing as it helps restore stainless steel’s strength and eliminates magnetism caused by stretching processes. By heating sinks at high temperatures and slowly cooling them down, their mechanical properties are improved.