Introduction
Custom metal bending is a fundamental manufacturing process used in sheet metal fabrication. It allows for the deformation of a workpiece to shape it into a desired geometry, providing tailored solutions for diverse industries. In this article, we will dive into the versatility of custom metal bending, exploring various methods and their applications. We will also discuss the materials used in sheet metal bending and how they impact the process and final product quality. Additionally, we will provide tips for successful sheet metal bending and highlight common fabrication processes. Join us as we explore the impact and wide-ranging applications of custom metal bending solutions.
The Versatility of Custom Metal Bending
Custom metal bending offers a wide range of methods to achieve different bend angles and radii, making it an incredibly versatile process in sheet metal fabrication.
- V-bending: This method involves using a V-shaped die and punch to press sheets of metal into a V-die. It is commonly used for creating straight bends with angles ranging from 30 to 180 degrees. V-bending is widely applied in industries such as automotive, aerospace, HVAC, and electronics.
- Roll bending: Roll bending utilizes three rollers and a hydraulic pressing system along with a brake to create curved forms in sheet metal. It is particularly effective for producing cylindrical or conical shapes. Roll bending finds applications in industries like automotive, shipbuilding, construction, and furniture manufacturing.
- U-bending: Similar to V-bending, U-bending utilizes a U-shaped punch and die to create U-shape bends instead of V-shapes. This method is commonly employed when fabricating enclosures or channels required in electrical cabinets, control panels, or HVAC systems.
- Rotary bending: Rotary bending is used when bends greater than 90 degrees are required. It involves rotating the sheet metal around a central axis while applying force to achieve the desired bend angle. This method produces more uniform and aesthetic results compared to V-bending, making it suitable for applications in architectural design, signage manufacturing, and decorative metalwork.
- Edge bending: Edge bending is used to bend the edges of sheet metal without damaging them, particularly in shorter sections of sheet metal. It is commonly employed in industries such as automotive, appliance manufacturing, and metal furniture production.
- Wipe bending: Wipe bending involves using a wipe die to carefully place the sheet of metal inside and apply pressure with a pressure pad before using a punch to create the desired bend. This method is ideal for creating complex shapes with tight tolerances in industries like aerospace, medical equipment manufacturing, and precision engineering.
Industrial Applications of Custom Metal Bending
With the increasing tailored demand for fabrication and enclosures, every industry now requires custom metal bending. Some major industries are:
- In the automotive industry, custom metal bending is used to fabricate intricate components such as exhaust systems, chassis frames, and brackets.
- The construction industry relies on custom metal bending for fabricating structural elements like beams, columns, and trusses.
- In electronics manufacturing, custom metal bending plays a crucial role in producing enclosures and housings for electronic devices.
- The aerospace industry utilizes custom metal bending for manufacturing aircraft parts such as wings, fuselages, and engine components.
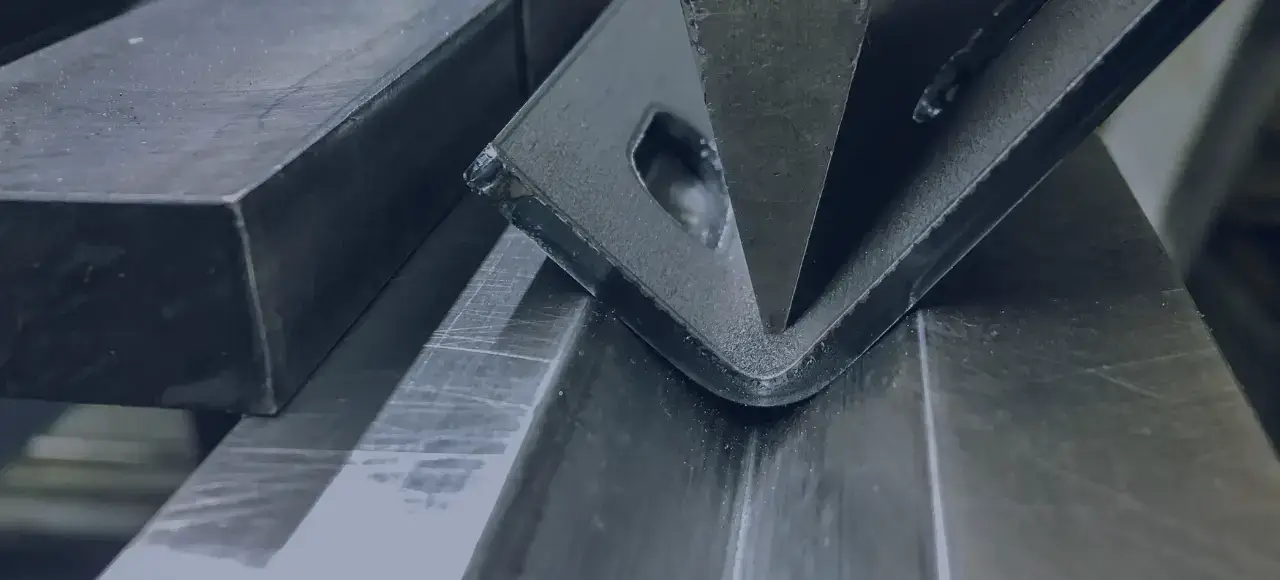
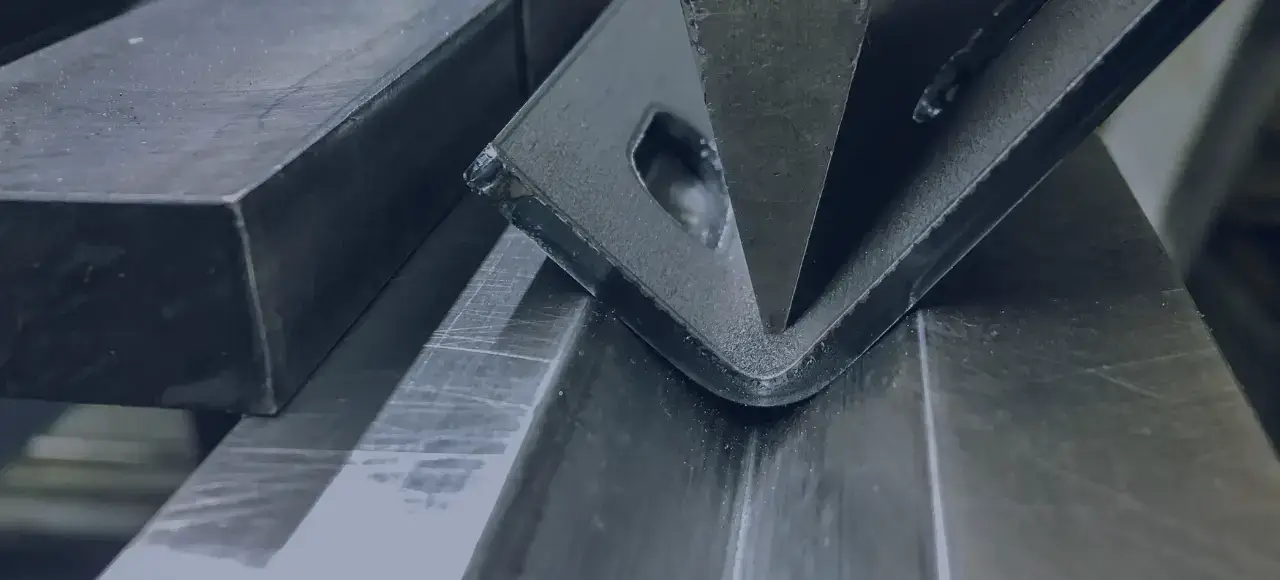
Materials Used in Sheet Metal Bending and Their Industrial Properties
The choice of materials in sheet metal bending greatly influences the process and final product quality. Different materials have varying properties and requirements that must be considered when selecting them for specific applications.
- Carbon steel: Carbon steel is one of the most commonly used materials due to its flexibility, strength, cost-effectiveness, and recyclability. It offers good formability but requires higher forces during bending compared to other materials.
- Aluminum: Aluminum is lightweight and corrosion-resistant, making it suitable for applications where weight reduction and durability are important. However, aluminum requires special care during bending to avoid collapsing or cracking in the corners. Only experienced suppliers can handle the proper bending of aluminum products.
- Stainless steel: Stainless steel is known for its robustness, corrosion resistance, and better strength properties compared to carbon steel. However, it is less malleable and requires high-power machinery for shaping.
- Titanium: Titanium is a lightweight material with excellent corrosion resistance and a high strength-to-weight ratio. It is commonly used in industries such as aerospace and medical equipment manufacturing due to its biocompatibility.
- Copper: Copper is cost-effective, highly conductive, and anti-corrosive. It is widely used in many industries that require high-precision bending capabilities, such as electrical and plumbing systems.
When selecting materials for sheet metal bending, factors such as malleability, strength, corrosion resistance, and conductivity must be taken into account. The right material ensures successful bending without compromising the structural integrity of the final product.
Tips for Successful Sheet Metal Bending
Achieving successful sheet metal bending requires careful consideration of several factors to ensure accurate and high-quality results.
- Bend allowance calculations: Before starting the bending process, it is essential to calculate the bend allowance to determine the length of the sheet required for a specific bend angle and radius. This calculation helps prevent material wastage and ensures precise bends.
- Heat application techniques: For thick or heavy bends, applying heat can reduce the risk of cracking by increasing the material’s ductility. Heat can be applied using methods like localized heating with a torch or oven heating before performing the bend.
- Avoiding sharp internal corners: Sharp internal corners in bends can lead to stress concentration points that may result in cracking or failure over time. To minimize stress levels and potential cracking, it is advisable to use larger radii or fillet bends instead of sharp corners whenever possible.
- Utilizing a press brake: A press brake is a machine commonly used for sheet metal bending. It utilizes a punch and die to shape the metal into specific configurations, providing clean and accurate bends. Press brakes are available in various sizes and can be programmed to achieve precise bends repeatedly.
By following these tips, manufacturers can ensure successful sheet metal bending, resulting in high-quality products with accurate dimensions and minimal defects.
Final Words
Bending is a crucial process in the fabrication industry. And with the increasing unique demand, every industry needs customization in fabrication. Selecting the right materials, the right bending process and, most importantly, expert suppliers is therefore essential. It not only provides confidence, but organizations can also deliver more tailored products and boost their revenue.
For tailored custom metal bending solutions, explore Zetwerk’s manufacturing services. From sheet metal stamping to fabrication, Zetwerk offers precision machining, casting, forging, and more. Visit the Zetwerk Knowledge Hub for additional articles on custom metal bending.




FAQs
Common materials used in sheet metal bending include carbon steel, aluminum, stainless steel, titanium, and copper. Each material has unique properties that impact the bending process and the final product quality.
The choice of method depends on factors such as bend angle, radius requirements, material type, and production volume. V-bending is versatile for most applications, while roll bending is suitable for creating curved forms. Consult with experts to determine the best method for your specific needs.
Press brakes offer clean and accurate bends due to their precise control over force and position. They provide versatility in terms of bend angles and radii and can handle various materials and thicknesses. Press brakes are widely used in sheet metal fabrication for consistent results.
Industries such as automotive manufacturing, aerospace engineering, construction infrastructure projects, HVAC systems fabrication, electrical enclosures production, and furniture manufacturing all benefit from custom metal bending solutions. These industries require precise shapes and configurations to meet their design requirements.