When it comes to rolling forming, an essential process in the manufacturing industry, choosing a supplier can be a crucial decision that influences the efficiency and quality of your projects. Roll forming is employed across various sectors, including automotive, construction, and aerospace, making it indispensable to modern manufacturing. This article provides a comprehensive guide to comparing roll forming suppliers to make an informed decision.
Understanding Roll Forming
Before diving into the comparison, it’s crucial to have a foundational understanding of roll forming. This process involves continuously bending a long metal strip into a specified shape. It has several benefits, such as high efficiency, the ability to produce complex geometries, and low tooling costs compared to other forming methods. However, the process can be complicated by common problems like warping or twisting, which can compromise the quality of the end product.
Roll Forming Suppliers: Key Factors to Consider
Quality of Materials
One of the first aspects to consider when comparing roll forming suppliers is the quality of the materials they use. Inferior materials can have a detrimental effect on the integrity and durability of the product. Therefore, opt for a supplier who adheres to industry standards and certifications for material quality.
Technological Advancements
Roll forming has evolved significantly, incorporating advanced technology to improve efficiency and product quality. Choosing a roll forming manufacturer that has adopted the latest technologies, from computer-aided design (CAD) to high-precision machinery, is essential to guarantee optimal results.
Customization Capabilities
Every project has unique requirements, and a size-fits-all approach is rarely effective. Customization is often necessary for specific industrial applications. Your roll forming supplier should offer bespoke solutions, including custom roll form tooling suppliers, to meet the exact specifications of your project.
Lead Time and Scalability
Other vital considerations include production speed and the ability to scale operations up or down as needed. A supplier that can maintain quality while meeting tight deadlines is often more valuable than one that cannot scale or complete the required timelines.
Experience and Reputation
In a sector as technical as roll forming, experience matters. An experienced roll-forming manufacturer can offer valuable insights, troubleshoot issues, and consistently produce quality products.
Regulatory Compliance and Certifications
In the highly technical field of roll forming, ensuring that your chosen supplier meets industry-specific regulations and quality standards is non-negotiable. Roll-forming suppliers should hold relevant certifications, like ISO 9001, to demonstrate that their products meet the universal standards for quality management. Regulatory compliance assures you that the supplier’s processes are vetted and reliable, making it an important criterion to consider.
Geographic Location
While the advent of globalization has made it easier to source supplies from anywhere in the world, geographic location still plays a role. Proximity can affect shipping costs, lead times, and even the carbon footprint of your project.
Skills and Expertise of the Workforce
Highly trained and skilled workers contribute to the precision and quality of the roll forming process. A roll-forming manufacturer with a skilled workforce can address complex challenges, adapt to project-specific needs, and provide innovative solutions. Make it a point to evaluate the expertise level of the employees, especially those who will be directly involved in your projects.
Price Vs. Value
While it might be tempting to choose the cheapest option, this can often compromise quality. The focus should be on the value offered: superior materials, advanced technology, and excellent customer service often justify a higher price point.
Problem-Solving Capabilities
In the real-world application of roll forming, unexpected challenges can emerge. How your chosen supplier addresses these challenges speaks volumes about their expertise and reliability. A good supplier should be adept at problem-solving and capable of quickly diagnosing and rectifying issues like warping or twisting, which are common in the roll-forming process.
After-Sales Support
The relationship with your roll forming supplier should continue once the project is completed. Post-production support, including troubleshooting and regular maintenance, is crucial for long-term success.
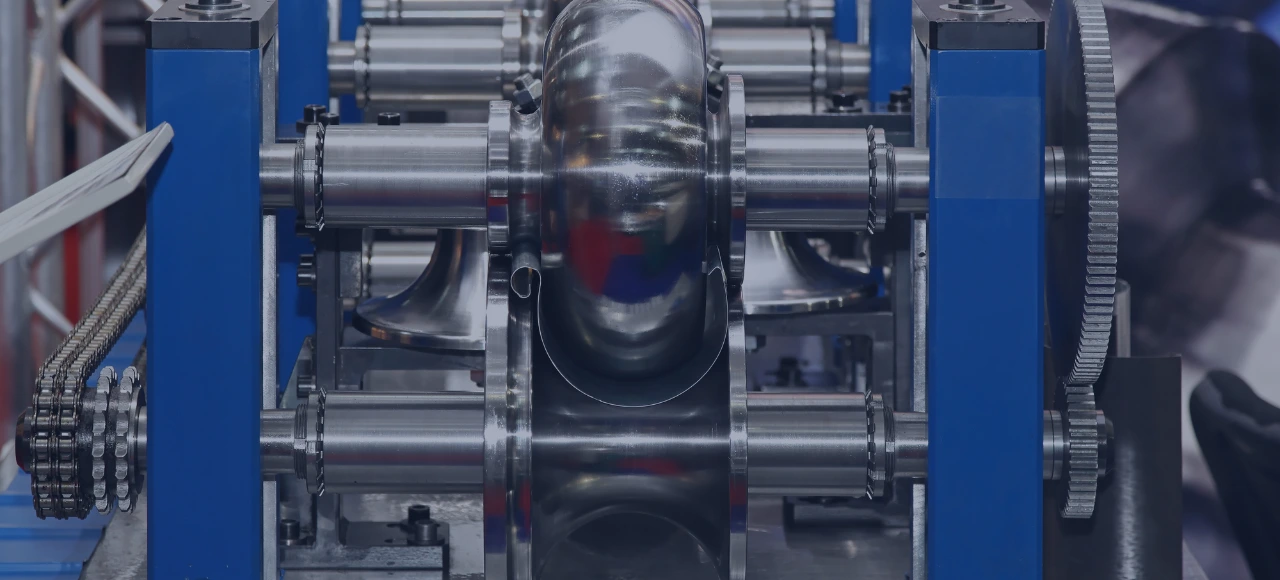
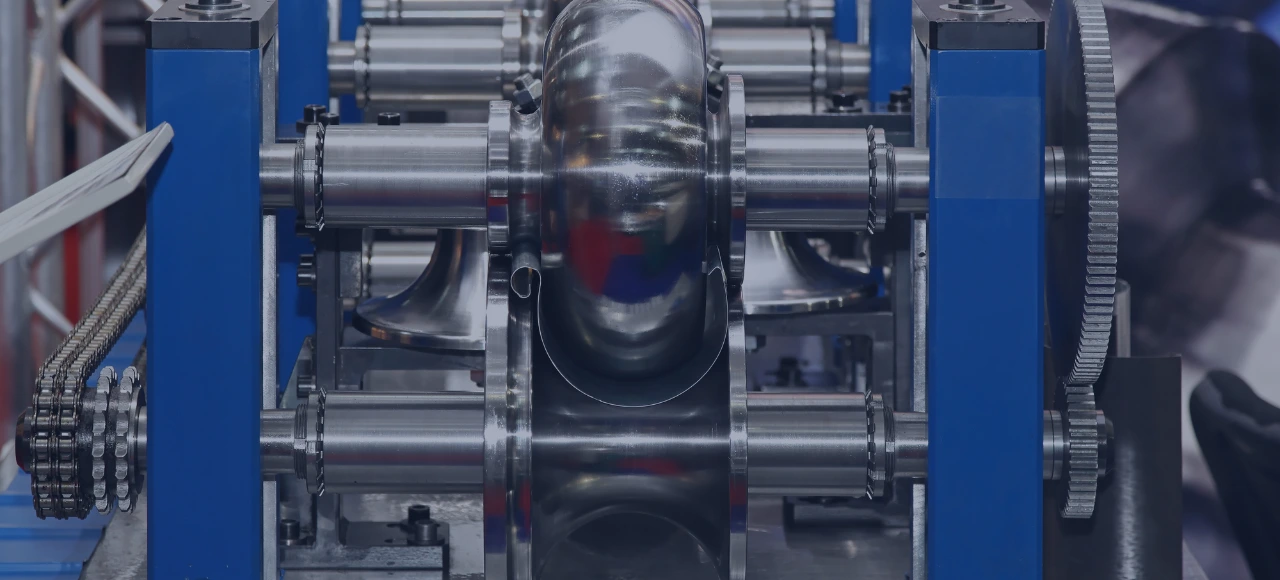
Environmental Considerations
As industries worldwide become more concerned with sustainability, choosing a supplier committed to eco-friendly practices is becoming increasingly important. Environmentally responsible roll form tooling suppliers use recycled materials and minimize waste, lowering the overall carbon footprint of the manufacturing process.
Additional Services Offered
Some suppliers offer additional services, such as assembly, welding, and coating, that complement the core roll forming process. These added services can provide a one-stop solution, making project management more straightforward. If you require these services, consider a supplier who can offer these additional capabilities to save time and potentially reduce costs.
Project Communication and Reporting
Open communication channels are crucial for successful project execution. Suppliers should be willing to update you at every stage, from design and production to delivery. Additionally, robust reporting capabilities enable better tracking and management of resources, leading to improved outcomes.
Industry Specialization
Different industries have different requirements. Some roll forming suppliers specialize in the automotive, aerospace, or construction sectors. Specialized experience can often bring valuable insights into your industry’s challenges and needs. Therefore, it’s wise to consider suppliers with a strong track record in your sector.
Flexibility and Adaptability
Market conditions and project requirements can change rapidly. The supplier you choose should have the flexibility to adapt to these changes without compromising quality. Whether a last-minute design modification or urgent scaling requirement, a flexible and adaptable supplier can be invaluable.
Final Thoughts!
Choosing the right roll forming supplier is a multi-layered process requiring a comprehensive approach. Roll forming is integral to various industries—be it automotive, aerospace, or construction—so selecting a partner that aligns with your project’s quality and efficiency is paramount. This guide has walked you through many key factors, ranging from the quality of materials and technological advancements to regulatory compliance and industry specialization.
Additional elements like the skills and expertise of the workforce, problem-solving capabilities, and environmental considerations further add nuance to this complex decision-making process. Your chosen supplier should be equipped to navigate market volatility and project changes without compromising the quality and timeliness central to roll forming operations.
By carefully weighing these criteria and taking a balanced, comprehensive view, you are better positioned to select a roll forming manufacturer or supplier that will meet and exceed your project expectations. This investment in due diligence paves the way for long-term partnerships, project success, and a more robust bottom line for your business.
Zetwerk stands committed to these high standards, offering a portfolio that encapsulates the considerations discussed here, from high-quality materials and technological advancements to industry-specific expertise. Zetwerk remains a partner for meeting the diverse industrial needs that roll forming projects necessitate.




FAQs
Roll forming is a continuous bending process that shapes long metal strips into specific profiles.
High-quality materials ensure structural integrity and durability, affecting the overall quality of the finished product.
Advanced technologies like CAD and high-precision machinery improve efficiency and product quality in roll forming.
Customization allows for specific industrial applications, making a one-size-fits-all approach ineffective and inefficient.
Consider material quality, technological advancements, customization capabilities, lead time, experience, geographic location, and after-sales support.