Introduction
Sheet metal welding is a critical process in various industries, including automotive, aerospace, manufacturing, and construction. As buyers and sourcing managers, understanding the best practices in sheet metal welding is essential for ensuring the production of high-quality welds that meet industry standards. By following these best practices, businesses can improve weld quality, increase efficiency, and reduce costs. In this article, we will explore the key factors to consider when choosing a welding method, discuss surface preparation techniques, provide tips for efficient welding, and highlight the importance of partnering with experienced sheet metal fabrication companies.
Understanding Sheet Metal Welding Processes
When it comes to sheet metal welding processes, there are several commonly used methods available:
- Plasma Arc Welding (PAW): This method utilizes an electric current to melt the metal wire and create a plasma by blowing gas into the molten pool. PAW is highly versatile and suitable for various industries such as field repair, shipbuilding, manufacturing, petroleum refining, and construction.
- Tungsten Inert Gas (TIG) Welding: TIG welding uses a non-consumable tungsten electrode and shielding gas to produce high-quality welds with exceptional precision. It is commonly used for welding non-ferrous metals like aluminum, titanium, and copper-nickel alloys in industries such as aviation and aerospace.
- Metal Inert Gas (MIG) Welding: MIG welding utilizes an electric arc to melt a filler material and join two or more pieces of the workpiece together. It is suitable for welding various materials including tubing and sheet metal using a mixture of carbon dioxide and argon as shielding gas.
- Gas Welding: This cost-effective method involves using heat generated from burning fuel (gasoline), oxygen, or oxyacetylene to join metals together. Gas welding is suitable for both ferrous and non-ferrous metals such as titanium, copper, aluminum, and brass.
- Stick Welding: Also known as Shielded Metal Arc Welding (SMAW), stick welding uses an electric current to melt the rod and fuse it with the base material. It is commonly used in construction, shipbuilding, and steel fabrication industries.
Best Practices for Efficient Sheet Metal Welding
To achieve efficient sheet metal welding, the following best practices should be considered:
- Electrode Selection: Choosing the right electrode is vital for achieving tighter arcs and minimizing burn-through. Smaller electrodes can help create a more focused heat zone, making it easier to control the welding process.
- Heat Adjustment: Proper heat adjustment is crucial to prevent excessive melting of the metal, which can lead to joint failure. Sourcing managers should ensure that welders have a thorough understanding of heat settings and adjust them accordingly for different materials and thicknesses.
- Test Runs: Performing test runs before the actual welding process allows welders to determine optimal voltage, amperage, and filler metals for different materials. This helps ensure consistent quality throughout the production process.
By implementing these tips, businesses can enhance efficiency, reduce waste, and improve overall weld quality in sheet metal fabrication projects.
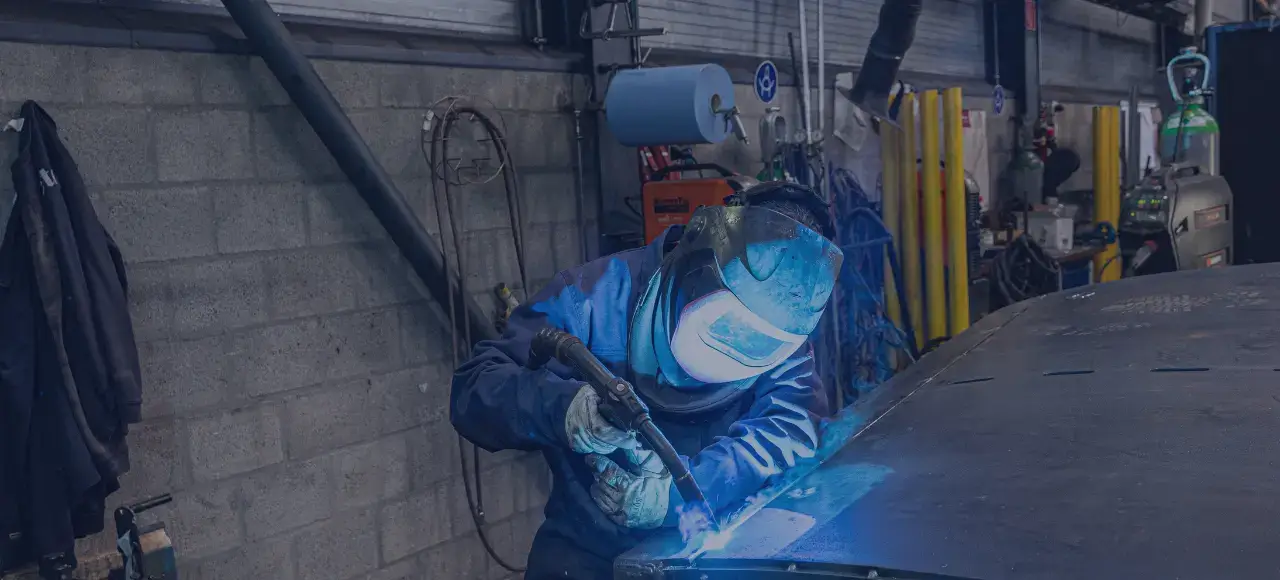
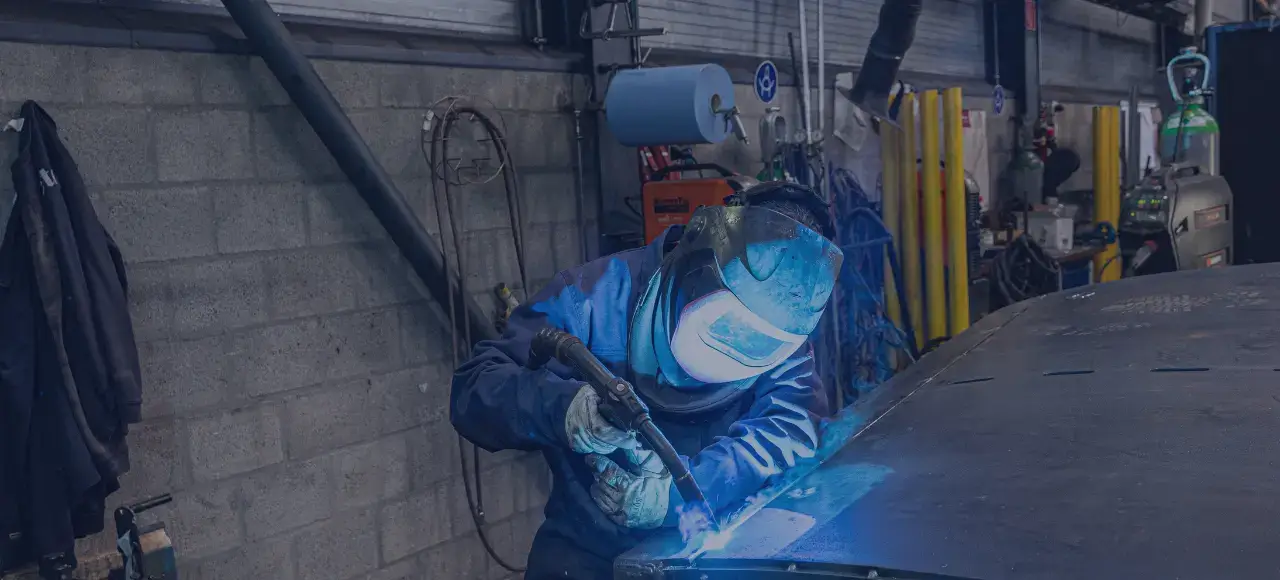
Tips for Buying and Sourcing Sheet Metal Welding Products
Buying sheet metal welding products need some information and expertise. Following best practices, organizations can make an informed buying decision.
Evaluating Welding Equipment and Technology
Consider the performance and features of different welding equipment and technology before making a purchasing decision. When evaluating welding equipment, it’s important to assess its welding capabilities, such as the type of welding processes it can handle and the thickness of metal it can weld. Additionally, consider the power source of the equipment, whether it’s electric, gas, or a combination, as this can affect both the performance and cost of the equipment. Another crucial factor to evaluate is the technology integrated into the equipment, such as advanced control systems and automation features, which can enhance productivity and efficiency.
Ensuring Proper Material Selection and Preparation
You should carefully select and prepare the materials to ensure successful sheet metal welding. The first step in material selection is to consider the type of metal that will be welded. It’s important to consult with a welding expert or supplier to determine the best material for your specific project. Once the material has been selected, it’s crucial to properly prepare it for welding. This includes removing any contaminants such as dirt, oil, or rust from the surface.
Implementing Quality Control Measures
Regularly reviewing and implementing quality control measures can help ensure that your sheet metal welding process meets the highest standards. Start by developing clear and concise quality control procedures that outline the specific requirements for each welding project. Regular audits and inspections should be conducted to verify that the quality control measures are being followed correctly.
Collaborating With Skilled Welding Professionals
To ensure successful collaboration with skilled welding professionals, it’s crucial to actively engage and establish clear communication channels. When working with these experts, it’s important to provide them with all the necessary information and specifications for the project like design drawings, material requirements, and any specific welding techniques or standards that need to be followed.
Final Words
In conclusion, implementing best practices in sheet metal welding is crucial for buyers and sourcing managers to ensure high-quality welds that meet industry standards. By focusing on key factors such as surface preparation, fit-up techniques, and material understanding, businesses can achieve optimal weld quality and enhance overall operational excellence.
Partnering with experienced sheet metal fabrication companies, like Zetwerk, will further contribute to successful welding processes and the production of durable and reliable welds. Explore the Zetwerk Knowledge Hub for additional articles on sheet metal welding and related topics.
For comprehensive services in sheet metal fabrication and access to a wide range of sheet metal welding methods, visit Zetwerk. Their expertise in manufacturing processes ensures high-quality welds that meet your specific project requirements. Explore the Zetwerk Knowledge Hub for more information on best practices in sheet metal welding and other related topics.




FAQs
TIG welding provides exceptional precision, ensuring high-quality welds in thin sheet metals. It is commonly used for non-ferrous metals like aluminum, titanium, copper, and nickel, making it suitable for industries demanding accuracy, such as aviation and aerospace.
Yes, plasma arc welding is highly suitable for field repairs in the construction industry. It requires minimal equipment setup and can be used to repair structures on-site without compromising weld quality. It is widely accepted in shipbuilding, manufacturing, petroleum, and construction industries.
Sourcing managers should prioritize proper fit-up techniques by using advanced measuring tools and fixtures to ensure the precise positioning of sheets before welding. This reduces misalignment risks and guarantees accurate welds with optimal strength.
Buyers should consider factors such as material type (stainless steel), aesthetic requirements, corrosion resistance needs, and intended application when choosing a surface coating for stainless steel products. Options include powder coating, anodizing, galvanizing, and brushing, among others.