In the world of precision manufacturing, stainless steel tubing fabrication stands as a testament to the fusion of art and science. This intricate process not only demands precision but also plays a critical role across various industries. In this comprehensive exploration, we will delve into the realm of stainless steel tubing fabrication, uncovering the processes, materials, criticalities, and the latest advancements that are reshaping industries worldwide.
About Stainless Steel Tubing
Stainless steel tubing, often referred to as stainless steel pipes, is revered for its corrosion resistance, durability, and versatility. It serves as a fundamental component in industries ranging from automotive to healthcare, playing pivotal roles in applications such as:
- Automotive Exhaust Systems: Where stainless steel tubing’s resistance to corrosion ensures longevity.
- Medical Devices: In precision instruments like endoscopes, where hygiene and durability are paramount.
- Aerospace: For hydraulic and pneumatic systems in aircraft, where lightweight strength is crucial.
- Oil and Gas: In pipelines that transport corrosive substances safely across vast distances.
- Food and Beverage: For sanitary transfer of liquids and gases, maintaining product integrity.
These applications merely scratch the surface of stainless steel tubing’s versatility. Its durability and corrosion resistance make it indispensable in environments where other materials would falter. At the heart of stainless steel tubing fabrication lies precision. The precise dimensions, tight tolerances, and weld quality are non-negotiable factors that ensure the tubing’s functionality, safety, and longevity.
Stainless Steel Tubing Fabrication: Process Explained
Stainless steel tubing fabrication involves a series of meticulous steps that transform raw materials into the versatile and reliable tubes used across industries. These steps include:
- Material Selection: The first step in stainless steel tubing fabrication is choosing the appropriate stainless steel grade. The choice of material depends on several factors, including the environment in which the tubing will be used, the substances it will convey, and the desired longevity.
- Tube Formation: Once the material is selected, it is transformed into tubes through various methods. Cold rolling or welding are common techniques used to create tubes with precise dimensions and tolerances.
- Welding: The seam of the tube is welded using various methods, including TIG (Tungsten Inert Gas) or laser welding. The goal is to create a seamless and strong joint that ensures the tubing’s integrity.
- Annealing: After welding, the tubing undergoes a heat treatment process called annealing. This process relieves stress in the metal and improves its mechanical properties.
- Surface Treatment: Depending on the intended application, the surface of the tubing may be treated to enhance its corrosion resistance or aesthetics. Treatments may include passivation, polishing, or coatings.
- Quality Control: Throughout the fabrication process, rigorous quality control measures are in place to verify the dimensional accuracy and integrity of the tubing. Inspections and non-destructive testing ensure that the final product meets the highest quality standards.
Raw Material Selection and Significance
The choice of stainless steel material plays a pivotal role in the performance and longevity of the tubing. Different grades of stainless steel offer varying levels of corrosion resistance, strength, and durability. Here are some common stainless steel grades used in tubing fabrication:
Stainless Steel Grade | Common Applications | Key Characteristics |
---|---|---|
304 Stainless Steel | – Food and Beverage | – Versatile and widely used |
– Pharmaceuticals | – Good corrosion resistance | |
– Plumbing | – Suitable for various applications | |
– Automotive | ||
– HVAC systems | ||
316 Stainless Steel | – Marine | – Superior corrosion resistance |
– Chemical Processing | – Excellent resistance to aggressive substances | |
– Medical Devices | – Hygienic and durable | |
– Pharmaceutical Equipment | ||
– Aerospace | ||
Duplex Stainless Steel | – Oil and Gas | – Exceptional strength |
– Petrochemical | – Excellent corrosion resistance | |
– Offshore Oil Rigs | – Ideal for challenging environments | |
– Chemical Processing Plants |
Each stainless steel grade has its unique advantages and is selected based on the specific requirements of the application. The choice of material is a critical decision that directly impacts the tubing’s performance and longevity.
Criticality in Fabrication
Dimensional Accuracy
- One of the cornerstones of stainless steel tubing fabrication is dimensional accuracy. Even minor deviations from specified tolerances can have significant consequences in various industries. For example, in the medical field, where precision is paramount, even the slightest deviation in the dimensions of tubing used in endoscopes can affect their performance and safety. The average thickness of stainless steel tubing can vary from 0.065 inches (1.65 mm) to 0.109 inches (2.77 mm), depending on the application.
- To ensure dimensional accuracy, fabricators use precise cutting and forming techniques, and quality control measures are employed throughout the production process. Tubing that meets exact specifications is essential for a wide range of applications, from automotive exhaust systems to aerospace components.
Weld Quality
- Weld quality is another critical factor in stainless steel tubing fabrication. Poor weld quality can compromise the integrity of the tubing, leading to leaks and potential safety hazards. Welding defects account for a significant portion of stainless steel tubing failures. Hence, it is imperative to achieve high-quality welds for which fabricators employ skilled welders who are experienced in the intricacies of welding stainless steel.
- Various welding techniques, such as TIG (Tungsten Inert Gas) welding, are used to create strong and leak-free joints. Rigorous quality control measures, including visual inspections and non-destructive testing, are conducted to ensure that the welds meet industry standards.
Surface Finish
- The surface finish of stainless steel tubing is a critical consideration, particularly in industries where hygiene and corrosion resistance are paramount.Surface finish in stainless steel tubing can range from mill finish (2B) to highly polished mirror-like finishes (No. 8).
- In applications like pharmaceuticals, food and beverage, and medical devices, the surface finish must meet stringent requirements. A smooth and clean surface not only enhances the aesthetics of the tubing but also makes it easier to clean and maintain sanitary conditions. Surface treatments such as electropolishing are often employed to achieve the desired finish.
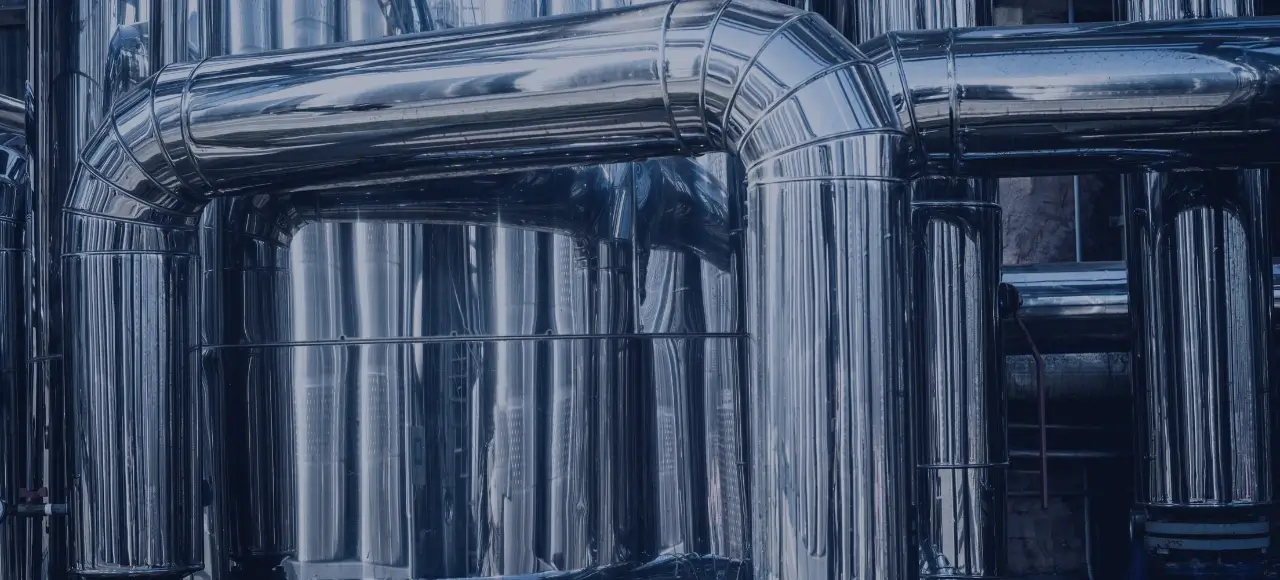
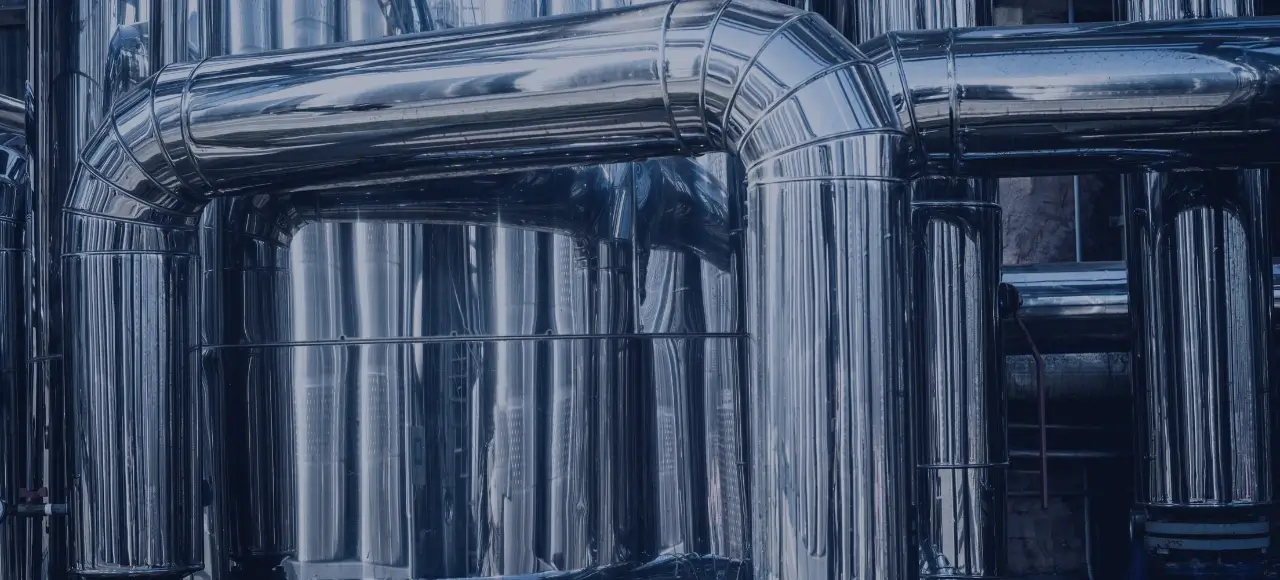
Current Trends and Advancements
In the dynamic field of stainless steel tubing fabrication, continuous advancements are shaping the industry. Here are some of the latest trends and innovations that are making waves:
Miniaturization
Miniature stainless steel tubing with outer diameters as small as 0.010 inches (0.25 mm) is now used in medical devices and microfluidics.
- One of the most significant trends in stainless steel tubing fabrication is miniaturization. Advancements in manufacturing techniques have enabled the production of miniature tubing with incredibly small outer diameters. These miniature tubes find applications in medical devices, microfluidics, and other precision instruments. Their use in these fields has revolutionized diagnostics, drug delivery, and various analytical processes.
Additive Manufacturing
The global market for 3D-printed stainless steel is expected to grow at a CAGR of 27.8% from 2021 to 2026.
- Additive manufacturing, including 3D printing, is revolutionizing stainless steel tubing fabrication. This innovative approach allows for the creation of complex geometries and intricate designs that were once challenging to achieve through traditional manufacturing methods. 3D-printed stainless steel tubing is finding applications in aerospace, automotive, and healthcare, where unique and customized designs are in demand.
Corrosion-Resistant Alloys
The market for corrosion-resistant alloys used in tubing is expected to reach USD 10.95 billion by 2026.
- As industries continue to push the boundaries of where stainless steel tubing can be used, the development of advanced corrosion-resistant alloys has become crucial.
- These alloys offer enhanced resistance to aggressive chemicals and environments. They find applications in chemical processing, offshore oil and gas, and other industries where standard stainless steel grades may not provide adequate protection against corrosion.
Sustainable Practices
Sustainability is a top priority for 74% of stainless steel producers, according to a survey by the International Stainless Steel Forum.
- Sustainability has become a central focus in stainless steel tubing fabrication. As environmental concerns rise, manufacturers are increasingly adopting sustainable practices throughout the production process. This includes reducing waste, optimizing energy consumption, and implementing recycling initiatives. Sustainable stainless steel tubing is not only environmentally responsible but also meets the demands of industries and consumers who prioritize sustainability.
Conclusion
In conclusion, stainless steel tubing fabrication remains at the forefront of precision manufacturing, delivering essential components that power industries worldwide. As advancements continue to reshape this landscape, the possibilities for innovation and application in various sectors are limitless. With a strong focus on precision, material selection, and sustainable practices, stainless steel tubing will continue to elevate industries and enhance our daily lives.
In the world of stainless steel tubing fabrication, precision and reliability are non-negotiable. Zetwerk, with its extensive network of trusted fabricators and stringent quality control processes, ensures that your stainless steel tubing sourcing needs are met with precision and efficiency. Whether you require miniature tubing for medical devices or corrosion-resistant tubing for aggressive environments, Zetwerk’s expertise and commitment to excellence guarantee top-tier results.




FAQs
The choice depends on the environment and the substances the tubing will be exposed to. 316 is preferred in corrosive settings.
Yes, ASTM A269 and ASTM A270 are commonly referenced standards for stainless steel tubing fabrication.
Yes, some stainless steel grades, such as 321 and 310, are suitable for high-temperature applications.
Electropolishing is a common process used to achieve a clean and smooth surface, ideal for pharmaceutical use.
Lead times can vary depending on complexity and order volume but generally range from weeks to months.