Sheet metal is an essential part of various industries, from construction to automobiles and aircraft to the creation of household appliances and electronics. Sheet metal fabrication is inescapable. In this blog, we took a comprehensive look into the intricate world of sheet metal fabrication techniques, delving into the methods, tools, and innovations that make this industry not only fascinating but also indispensable. Sheet metal fabrication is essential for many industries according to project needs.
Sheet metal refers to a thin and flat piece of metal, often measured in terms of its thickness, basically ranging between an inch and a few millimeters. The first step here is the material selection. Common metals like steel, aluminum, and copper are used, each having its unique properties and applications. They cater to the specific needs of the project and customize according to the requirements.
Material Selection
The choice of material is crucial as it directly impacts the end product’s durability, strength, and aesthetic appeal. Different metals have different benefits, making them suitable for specific applications. Steel, for instance, is known for its strength and durability, making it perfect for structural components. At the same time, aluminum is preferred for its lightweight and corrosion resistance, often found in the aerospace industry for various tools and machinery.
Cutting and Shearing
One of the most fundamental techniques is cutting and shearing. It involves cutting a large sheet into smaller, more manageable pieces. Traditional methods include guillotine shearing and abrasive water jet cutting. More modern methods are on the way, and many, like laser cutting and plasma cutting, have revolutionized this process, allowing for greater precision and reduced material waste. That is increasing the efficiency and effectiveness as a whole.
Bending and Forming Techniques
Bending and forming are integral aspects of sheet metal fabrication. Press brakes are commonly used machines that force a sheet to turn it into desired shapes. The angle and precision of the bend are controlled by the operator, making press brakes a versatile tool for a range of applications, from creating brackets to forming intricate curves in architectural metalworks.
Roll Forming
It is another bending technique, but it focuses on long, continuous bends, ideal for creating items like tubing, rails, and profiles. In this process, the sheet metal passes through a series of rollers, each gradually shaping the metal to its final form. Roll forming is a cost-effective technique, especially when large quantities of identical parts are required, as it saves the cost of establishing a project; this is a widely used technique.
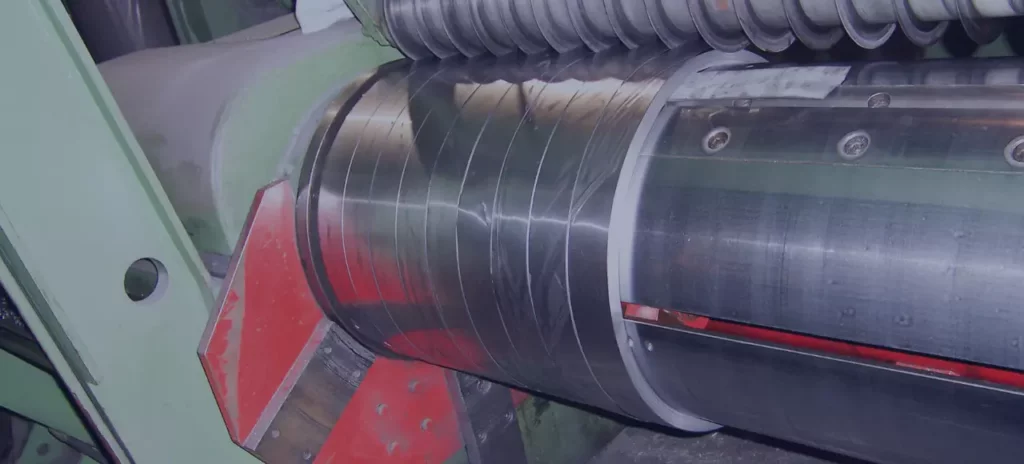
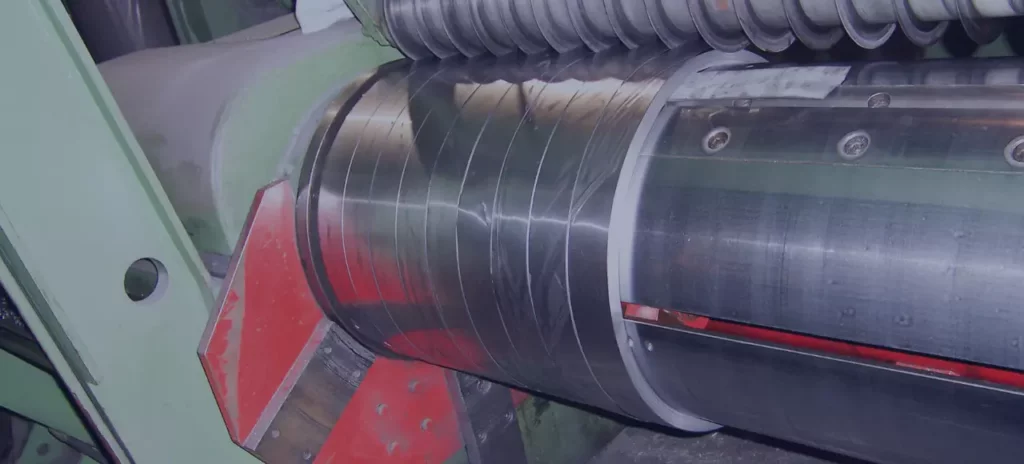
Hydroforming
It is a relatively innovative method that has gained popularity in recent times and utilizes high-pressure fluid to shape the sheet metal. This technique allows for the creation of complex and seamless shapes while minimizing the need for additional welding or joining. The automotive industry commonly uses hydroforming for producing parts such as exhaust components and suspension elements.
Joining and Welding Methods
Spot welding is widely used for joining sheet metal components. It includes applying an electrical current to the point where two pieces of metal meet. The intense heat at the contact point causes the metals to melt and fuse. This technique is both quick and cost-effective and is often used in the manufacturing of automobile bodies and appliances.
TIG and MIG Welding
Tungsten and metal inert gas are two standard methods for more precise and structurally robust welds. They are the modern techniques and tools for welding and the very precious customized materials to meet the project’s needs.
Cutting-Edge Sheet Metal Fabrication Technologies
CNC, or computer numerical control machining, has revolutionized sheet metal fabrication. These machines are capable of precision cutting, drilling, and milling and can be programmed to produce highly complex and intricate parts. These machines offer not only precision but also speed, reducing time and enhancing overall efficiency in the fabrication process.
3D Printing
3D printing or additive manufacturing has entered the sheet metal fabrication industry. Particularly in the creation of prototypes and low-volume, highly customized parts. While traditional subtractive methods involve removing material from a block, 3D printing builds components layer by layer, reducing waste, enabling the production of highly intricate geometrics, and saving a lot of time, and that is by being able to deliver the project on time.
Quality Control and Finishing
- Quality control is the primary in sheet metal fabrication to ensure that the final component meets the desired specifications and standards. Several techniques and tools are employed to verify the quality of fabricated components, including dimensional inspections, nondestructive testing, and visual inspections. Surface finishing is another essential aspect of sheet metal fabrication.
- After the fabrication process, sheet metal components may undergo finishing processes to enhance their appearance and corrosion resistance. Standard finishing techniques include painting, powder coating, plating, and anodizing, each offering unique advantages depending on the application.
Sustainability in Sheet Metal Fabrication
As the environmental issues continue to grow, sustainability has become a significant focus in the sheet metal fabrication industry. Companies are implementing eco-friendly practices to reduce waste, energy consumption, and the environmental impact of their operations. These practices include recycling scrap metal, using energy-efficient equipment, and minimizing harmful emissions.
Final Words
The evolution of sheet metal fabrication has been a remarkable journey, transforming from its modest origins into a complex and highly versatile field that serves many industries. Knowledge of the various techniques and tools involved in this craft is essential for producing high-quality, reliable, and innovative products. Sheet metal fabrication in places like Jersey, as in numerous other locations, is indispensable in supporting various industries, such as construction, manufacturing, aerospace, and automobiles.
Zetwerk plays a pivotal role in advancing the field of steel metal fabrication. Their continuous efforts in introducing new and improved methods have expanded the possibilities and applications of this fascinating discipline. Their contribution has not only elevated the standards of quality and reliability in sheet metal fabrication but has also played a significant role in fueling innovation, making them an integral part of the sheet metal fabrication landscape in Jersey and beyond.




FAQs
It is a manufacturing process that involves transforming flat metal sheets into finished products or components through various techniques like cutting, bending, and welding. It’s essential because it is a fundamental process used in industries from automotive to construction to create a wide range of products.
Common metals include steel, aluminum, copper, and stainless steel. The choice of metal depends on the requirements and the desired properties of the end product, such as strength, weight, or corrosion resistance.
It includes guillotine shearing, laser cutting, plasma cutting, and water jet cutting. Each method offers unique advantages regarding precision, speed, and suitability for different methods.
Welding is crucial for joining sheet metal components to create structurally sound and durable products—techniques like spot welding. TIG and MIG welding are commonly used, each with advantages depending on the application.
Sustainability is increasingly important, with companies implementing eco-friendly practices like recycling scrap metal and using energy-efficient equipment to reduce environmental impact and waste in the fabrication process.