Understanding zamak alloy composition is critical to maximizing ROI and optimizing the manufacturing process. Different aluminum, magnesium, and copper alloys affect properties like hardness, tensile strength, flexibility, and corrosion resistance. Zamak offers high strength, is low cost, non-toxic, and hypoallergenic making it ideal for producing medical equipment. However, there are many other applications of Zamak alloy compositions based on aluminum, magnesium, and copper alloys. Knowing which type of zamak alloy to use for specific applications becomes essential for optimal returns on your investment. This article discusses Zamak alloy composition, its types, and reasons to choose it for your manufacturing processes.
First, let’s understand why is Zamak alloy composition significant for manufacturers.
What is Zamak Alloy?
Zamak alloy is composed of zinc and other elements, such as aluminum, magnesium, and copper. To achieve specific qualities, such as strength, resistance to corrosion, and thermal conductivity, the alloys are carefully formulated with particular compositions. Some of the key benefits of Zamak alloy composition are,
- Versatile and cost-effective for manufacturing.
- Offers a balance of strength, castability, dimensional stability, and ease of finishing.
- Provides excellent resistance to corrosion and wear.
- Can be customized with a wide range of aesthetic coatings and finishes.
- Enables the production of complex and intricate parts with high precision.
The Different Types and Uses of Zamak Alloys
Each Zamak alloy has specific properties and advantages, making them suitable for various applications. It is important to choose the right Zamak alloy composition based on the application’s specific requirements.
Zamak 2
Zamak 2 is a zinc alloy containing approximately 96% zinc and small amounts of aluminum, magnesium, and copper. It is a Zamak alloy composition commonly used in die casting and offers several benefits:
Zamak 2 is a zinc alloy with higher strength and hardness than other zinc alloys. Its tensile strength is 359 MPa, and Brinell hardness is 100 HB, allowing it to withstand high mechanical stresses.
Impact of Zamak 2 on manufacturing metal components:
- Zamak 2 exhibits high strength and hardness, making it suitable for producing durable metal components.
- Its mechanical properties, such as tensile strength and creep resistance, contribute to the overall performance and longevity of the manufactured parts
- Zamak 2 eliminates the need for additional bushings and wear inserts in die-casting components.
- This alloy can be electroplated, wet painted, and chromate conversion coated, allowing for a wide range of surface finishes.
- It facilitates post-casting processes such as drilling, milling, and threading.
Zamak 3
Zamak 3 is a zinc alloy with 96% zinc, 3.5 to 4.3% aluminum, 0.02 to 0.05% magnesium, and 0.025% copper. Its high fluidity and good ductility make it a popular choice for die casting. This Zamak alloy composition also has excellent dimensional accuracy, stability, and corrosion resistance and is easy to plate and finish.
Impact of Zamak 3 on manufacturing metal components:
- Zamak 3 is known for its excellent castability, allowing for complex shapes and intricate details to be easily reproduced during manufacturing.
- It has a high tensile strength that helps components withstand heavy loads and impacts, ensuring long-lasting performance.
- Zamak 3 has inherent corrosion resistance, essential for components exposed to various environmental conditions.
- Unlike other materials such as stainless steel or aluminum, it is a cost-effective option for manufacturing components.
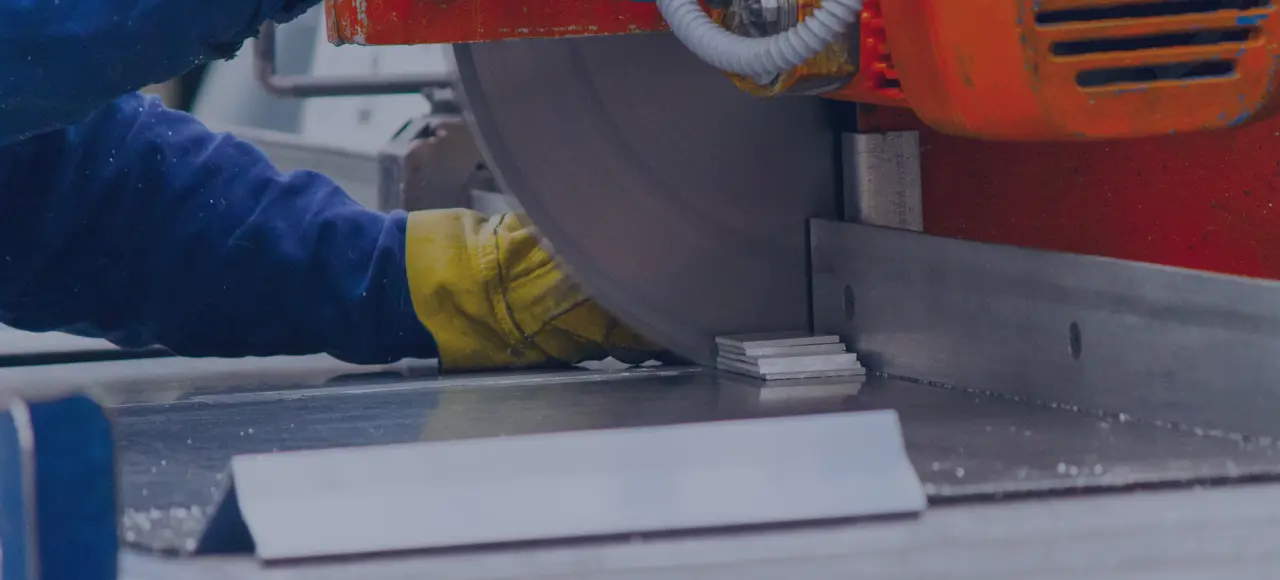
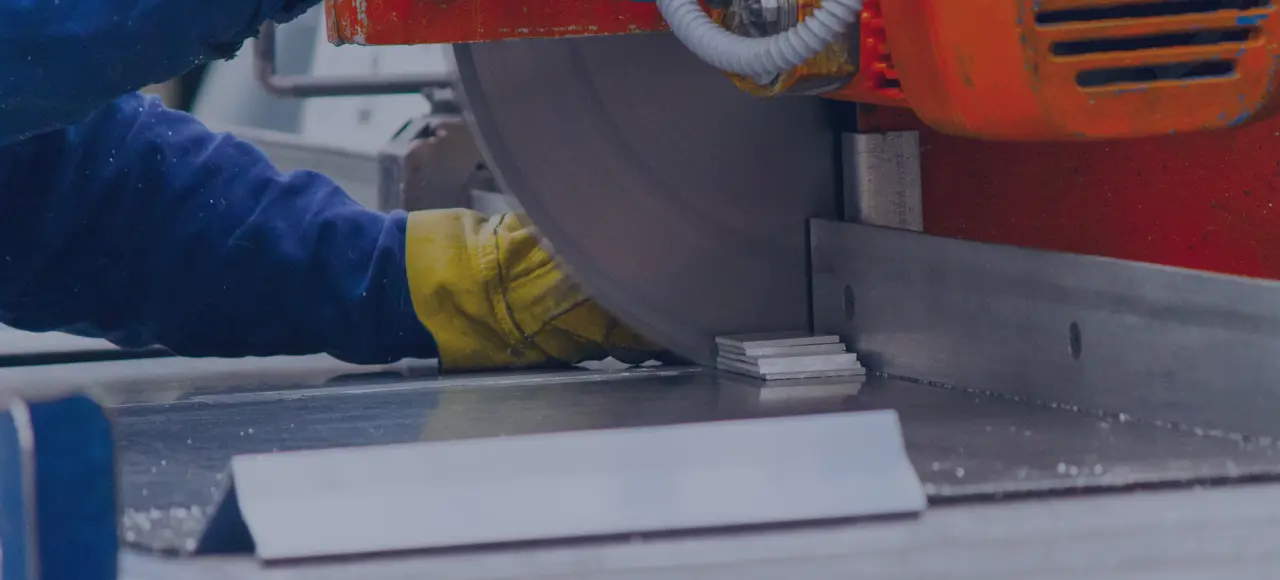
Zamak 5
Zamak 5 is a Zamak alloy composition with high strength and hardness due to its 1% copper content. It has better creep resistance and dimensional stability at elevated temperatures and slightly better corrosion resistance than Zamak 3.
Impact of Zamak 5 on manufacturing metal components:
- Compared to other zinc alloys, this alloy has a higher copper content. This results in stronger and more durable components, making it ideal for manufacturing.
- Zamak 5 is favored for its excellent casting characteristics, allowing intricate and detailed component designs to be easily replicated.
- It is widely used across industries for manufacturing components such as automotive parts, electrical connectors, hardware, and industrial equipment.
Zamak 7
Zamak 7 is a Zamak alloy composed of zinc (96%) with aluminum, magnesium, and copper. It has high strength, good impact strength, and ductility, making it suitable for load-bearing applications. It also has excellent castability and fluidity, ideal for thin-walled and intricate die-cast components.
Impact of Zamak 7 on manufacturing metal components:
- Zamak 7 is used for manufacturing components where additional formability is required during the assembling operations, such as crimping or staking.
- This material has high fluidity, making it easy to cast intricate designs and thin walls. It can also be reshaped without losing its integrity.
- Zamak 7 is a high-purity alloy with reduced magnesium and nickel for long-term stability and minimal corrosion.
Key Takeaways
Understanding the composition of zamak alloys is vital for professionals in the manufacturing industry. The specific aluminum, magnesium, and copper levels significantly influence properties such as hardness, tensile strength, flexibility, corrosion resistance, and fluidity.
By selecting the appropriate zamak alloy, manufacturers can optimize product quality while enjoying the benefits of cost-effectiveness. Zetwerk provides a comprehensive online B2B marketplace for manufacturing services, including precision machining, die casting, forging, and more. Visit the Zetwerk Knowledge Hub for additional articles on zamak alloy composition and other related topics.




FAQs
Zamak alloy composition significantly impacts product performance. Varying amounts of aluminum, magnesium, and copper influence properties like hardness, tensile strength, corrosion resistance, and fluidity.
Different types of zamak alloys have distinct compositions and properties. While some may be interchangeable for certain applications, it’s essential to consider the specific requirements of each project before selecting the appropriate alloy.
Zamak 3 offers a balanced combination of strength, flexibility, and ease of casting. It is widely used in various applications like automotive components, electrical connectors, and consumer goods due to its excellent fluidity and surface finishing capabilities.
The strength of a specific zamak alloy can be improved by modifying its composition. Increasing the copper content can enhance hardness and tensile strength. However, any changes should be carefully considered to maintain desired properties.
Yes, there are environmental benefits associated with using Zamak alloys. They have high recyclability rates, which contribute to sustainable manufacturing practices. Compared to primary metal production methods, recycling zamak alloys reduces energy consumption and greenhouse gas emissions.