According to a study, nearly 80% of companies that develop efficient supply chains can achieve higher-than-average revenue growth in their industries. Supply chain management maximizes customer value and helps companies achieve long-term competitive advantages.
It’s a complex task, but separating upstream and downstream supply chains can help companies see where problems arise. Dividing the supply chain into these two categories enables managers to understand inefficiencies or bottlenecks, optimize costs, and ultimately maximize customer value. Here’s how it works in practice.
What Are Supply Chains?
Before we get into these two subcategories (upstream and downstream), let’s examine a typical supply chain. A supply chain is the network of companies and processes that help create, distribute, and ultimately sell a product. A supply chain begins with the seller or supplier who provides the raw materials a manufacturer uses to make a product. The manufacturer buys these raw materials and turns them into a product.
The retailer then delivers the product from the manufacturer to the customer. Many parties can be distributors, including retailers, e-commerce partners, and wholesalers. Supply chain management is a complicated process. It involves five steps: planning, sourcing materials, manufacturing, delivering, and returns. Good supply chain management is vital to the success of companies that must ensure they get goods to customers on time and meet or exceed their expectations. When companies apply good supply chain management practices, they save money and enhance customer satisfaction.
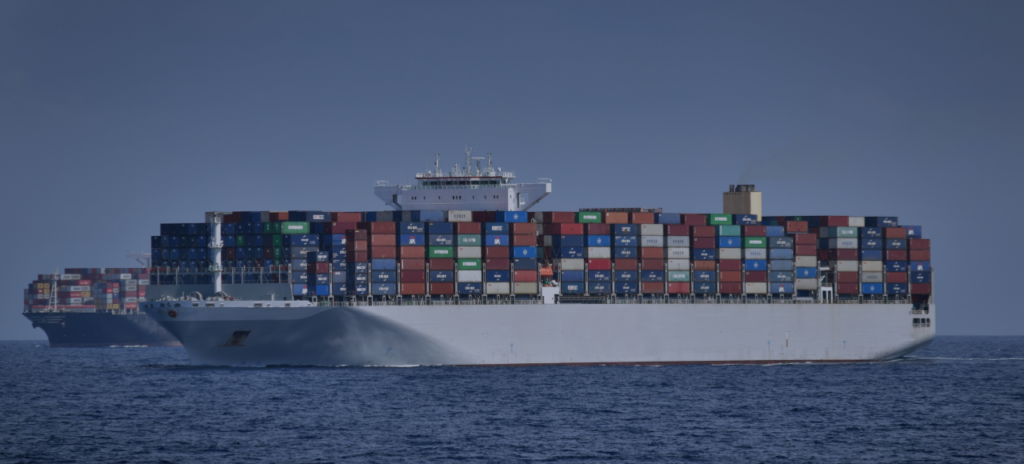
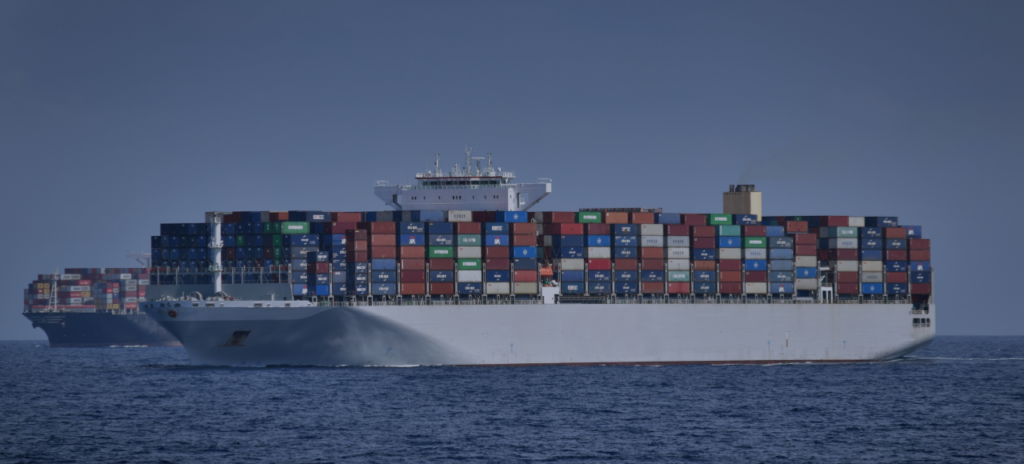
- Upstream Supply Chain : The upstream supply chain collects, stores, and delivers raw materials and other necessary items from suppliers to manufacturers. It is an essential part of any production process, ensuring that materials are available when needed to keep operations running smoothly. This supply chain can involve multiple suppliers or just one, depending on the production needs. For an upstream supply chain to be effective, it must integrate with downstream processes to ensure that materials are delivered in a timely and efficient manner.
- Downstream Supply Chain : The downstream supply chain is a term used to describe the process of getting products or services from the supplier to the customer. It involves various procurement, production, distribution, and retail activities. The downstream supply chain includes inventory management, pricing and promotion strategies, and customer service. As technology advances, businesses continually find new ways to optimize their downstream supply chain to achieve cost savings and better customer experiences.
Why Companies Need To See Upstream And Downstream Supply Chain
Companies need to understand their upstream and downstream supply chain because it gives them insights into where their products are coming from and where they are going. This allows companies to create a more efficient and cost-effective supply chain, ensuring that the products get delivered on time and in the proper condition.
It is also vital for companies to be able to trace materials back to their source. Knowing exactly where a product is coming from ensures that it meets quality standards and can be traced if it has a problem. Additionally, understanding the entire supply chain allows companies to manage better risks associated with potential disruptions in production or distribution.
Upstream And Downstream Supply Chain – Comparison
Even though the supply chain may seem straightforward, it’s a complex system with many moving parts. To make things easier, some companies divide the supply chain into two parts: upstream and downstream supply chain.
Upstream supply chains are made up of all the companies that send materials to the prominent manufacturer or the party that buys the raw materials and sends them to the primary manufacturer. A downstream supply chain comprises all the activities involved in getting a product to consumers once it’s been manufactured.
The supply chain can be viewed as a series of transactions between companies, each providing products or services to the other. Downstream indicates ‘demand’ whereas upstream to ‘supply.’ Supply chain managers have to balance demand and supply. The supply chain is critical for businesses to avoid lost sales, out-of-stock, or over-ordering. Supply chain inefficiencies can waste up to 25% of operating costs, making matching supply and demand critical.
How To Manage Upstream And Downstream Supply Chain
Separating the upstream and downstream parts of the supply chain can help managers handle the three main flows in product production and distribution.
- Material flow
- Money flow
- Information flow
First, material flow involves more than a simple progression from raw material to finished product. Some downstream partners must process returns and enter into distribution agreements with retailers to process these returns effectively.
The flow of cash tends to move from the retailer to the manufacturer. The retailer pays the seller for goods received, and the seller pays the manufacturer. Supply chain managers must ensure that strict controls and recording systems are in place to ensure that no late or wasted payments occur.
Collaboration requires a free flow of information to help your supply chain partners be more productive and efficient. It’s important to share information and keep it flowing freely to ensure the entire supply chain runs smoothly. Transparency helps build strong, long-term relationships between all partners.
Leveraging the power of technology to manage your supply chain can be a cost-effective way to increase efficiency. One innovative solution for managing your supply chain is Zetwerk, which provides a comprehensive suite of services to help companies manage their supply chains to streamline their processes. Zetwerk provides businesses with access to an extensive network of suppliers, offers customized pricing and choice of product categories, and ensures quality control over the entire process. By outsourcing your supply chain with Zetwerk, you can improve efficiencies in all areas while maintaining total control over the process. Contact us for more information.



