Introduction
Tube roll forming is an advanced metal forming process that offers high efficiency and precision in manufacturing. This process involves shaping a flat piece of metal sheet into closed tubular sections, making it ideal for producing complex shapes with consistent metal thickness. By utilizing roll forming mills, precision-forming rolls, welding rolls, and various welding operations, tube roll forming provides professionals in the manufacturing industry with a reliable method for creating a wide range of products.
Understanding Tube Roll Forming
- Tube roll forming is a metal forming process specifically designed for closed tubular sections. Unlike traditional tube bending methods, which require bending tubes around mandrels or forms, roll forming simplifies the process by passing the material through a set of forming rolls in a roll forming mill. This efficient method allows for the creation of complex shapes with consistent metal thickness.
- In the roll forming mill, each roll only bends small sections of the strip until the final shape is obtained. By gradually bending the material with each pass through the rolls, tube roll forming prevents springback, ensuring precise and consistent results. The ability to achieve smaller radii compared to traditional tube bending is another advantage of this process.
Welding Operations in Tube Roll Forming
- To firmly weld flat metal ends together during tube roll forming, different welding operations can be utilized depending on specific requirements. One common method is high-frequency induction welding (HFI), which uses electromagnetic fields to heat and weld the edges of the strip together. Laser welding is another option that offers precise control over heat input and creates clean welds.
- Welding rolls play a critical role in securing the integrity of welded tubes during the operation. These specialized rolls hold and guide the material as it passes through the welding process, ensuring proper alignment and fusion between metal ends. Choosing an appropriate welding method depends on factors such as production volume, desired weld quality, available equipment, and material properties.
Tooling Materials for Forming Rolls
- The tooling material used for forming rolls in tube roll forming is crucial for achieving efficiency and precision. One widely preferred material is aluminum bronze, known for its excellent sliding properties, high hardness, and low elongation. These properties make it ideal for facilitating the forward rolling movement and shaping of the metal strip during the roll forming process.
- The sliding properties of aluminum bronze enable smooth movement between the rolls, reducing friction and wear. The high hardness of this material ensures resistance against wear and extends the longevity of the forming rolls as they shape the metal strip. Additionally, its low elongation provides shape stability during roll forming, contributing to consistent results.
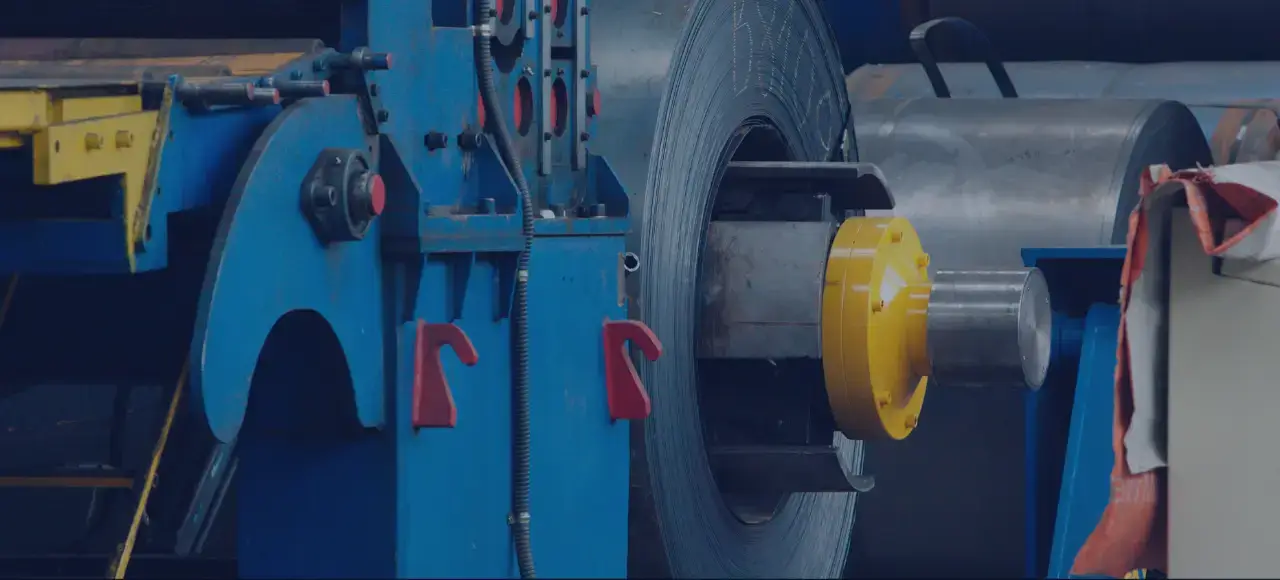
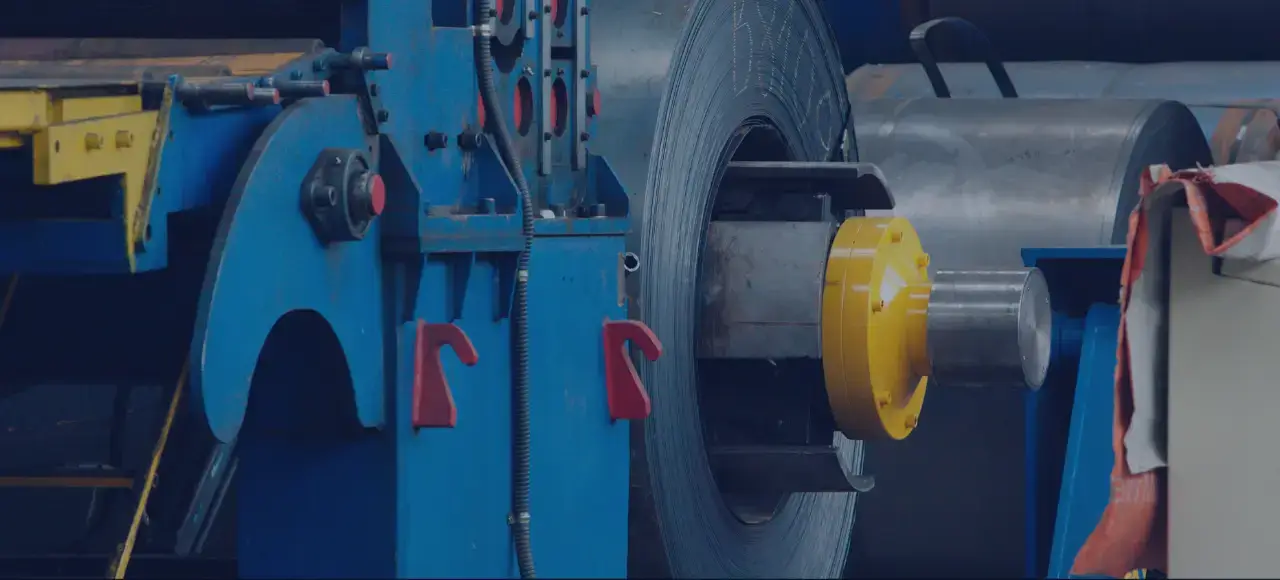
Applications and Benefits of Roll-formed and Welded Tubes
- Roll-formed and welded tubes offer numerous benefits across various industries. One significant advantage is their cost-effectiveness compared to other manufacturing methods. By utilizing continuous roll forming followed by longitudinal welds, manufacturers can achieve high production rates while maintaining quality standards.
- In automotive applications, roll-formed and welded tubes are used in seat structures, cross members, side impact beams, bumpers, engine subframes, suspension arms, twist beams, and more. These components contribute to improved vehicle performance by reducing mass while enhancing stiffness. Furthermore, tube roll forming allows for tailored mechanical properties through work hardening during the manufacturing process.
Enhancing Manufacturing Efficiency with Tube Roll Forming
Incorporating tube roll forming into your manufacturing processes can significantly enhance efficiency and precision. By utilizing roll forming mills, precision-forming rolls, and welding operations, you can produce complex shapes with smaller radii while maintaining consistent metal thickness. The mechanical properties of the welded tubes can also be improved through work hardening during the manufacturing process. Whether you’re in the automotive industry or any other sector that requires precise manufacturing techniques, tube roll forming is a cost-effective solution that reduces vehicle mass and improves structural stiffness.
Key Takeaways
In the manufacturing industry, tube roll forming offers highly efficient and precise method for producing complex shapes with consistent metal thickness. This process simplifies the production of complex shapes while maintaining consistent metal thickness with the help of various welding operations like HFI welding or laser welding. Roll-formed and welded tubes are cost-effective, lightweight, offer better stiffness and can enhance mechanical properties. Organizations seeking to optimize their manufacturing processes should consider tube roll forming as a reliable and efficient technique.
Zetwerk offers a wide range of manufacturing services, including tube roll forming and related processes such as extrusions, die casting, CNC machining, forging, injection molding, sheet metal stamping, prototyping, pre-production, and investment casting. Zetwerk’s capabilities cover various materials and provide high-quality components with tight tolerances. With Zetwerk Managed Inventory, project management services, quality control measures, efficient logistics, and supply chain solutions, Zetwerk ensures transparency and efficiency throughout the entire manufacturing process.




FAQs
Tube formability depends on the steel grade used and the tube diameter/thickness ratio (D/T). Different steel grades have varying levels of ductility and strength. A higher D/T ratio generally leads to reduced formability due to increased strain during bending.
The minimum bend radius in tube bending refers to the smallest radius that a tube can be bent without causing excessive deformation or structural failure. It is determined by factors such as material properties (ductility), wall thickness, tooling limitations, and intended application requirements.
Springback refers to the phenomenon where a tube returns partially to its original shape after bending it. Springback is a critical factor that affects the accuracy of tube bending operations, particularly in processes like metal tube bending, where, due to elastic property, the material has a memory of its original shape and tends to return to that shape after bending.