Tube Fittings Introduction
Tube fittings are essential in various industries, including plumbing, automotive, aerospace, and manufacturing, where secure and leak-free connections are crucial. These fittings provide a means to connect, terminate, control, or redirect fluid flow through tubing or pipes. They play a significant role in maintaining the integrity and efficiency of fluid systems, ensuring safe operations, and preventing leaks that can lead to hazardous situations or loss of valuable resources.
The primary purpose of tube fittings is to connect, terminate, redirect, or regulate the flow of fluids through tubing or piping systems. They provide a reliable means of joining tubes, constructing complex and efficient fluid transmission networks. Tube fittings come in various shapes, sizes, and materials to accommodate different requirements. Standard tube fittings include compression, flare, push-to-connect, barbed, threaded, and quick disconnect fittings.
Each class is designed to suit specific applications and fluid system needs. One of the critical advantages of tube fittings is their ability to create secure and leak-free connections. When correctly installed, these fittings ensure a tight seal between tubes, preventing fluid leakage, which is vital for system efficiency, safety, and environmental protection.
Classifications of Tube fittings
Here are some of the common types of tube fittings:
Compression Fittings
Compression fittings consist of a nut, a compression ring (ferrule), and a body. They are widely used in plumbing and gas supply systems. When the nut is tightened, it compresses the ferrule against the tubing, creating a tight seal. This makes them easy to install and dismantle, facilitating quick maintenance and component replacement. Compression tube fittings are known for their reliability, versatility, and suitability for high-pressure applications, making them popular in many industrial settings.
Flare Fittings
Flare fittings have a cone-shaped seat on the fitting body. When the tubing end is flared at a specific angle, it forms a tight seal against the fit body when assembled. These fittings are commonly used in refrigeration and hydraulic systems.
Push-to-Connect Fittings
These fittings allow quick and easy connections without needing tools. The tubing is pushed into the fitting, and internal components lock it in place securely.
Quick-Disconnect Fittings
As the name suggests, these fittings enable rapid disconnection and reconnection of tubing or hoses. They are often used in applications requiring frequent disconnects, such as pneumatic tools or fluid transfer systems.
Barbed Fittings
Barbed fittings have barbs or ridges on the fitting’s surface, which grip the inner diameter of the tubing. They are commonly used in low-pressure applications and are especially prevalent in the agricultural and automotive industries.
Push-In Fittings
Similar to push-to-connect fittings, push-in fittings allow quick assembly without tools. The tubing is inserted into the fitting, and the internal components secure it.
Threaded Fittings
Threaded fittings have male or female threads that can be screwed together with other threaded components, providing a secure connection. They are widely used in plumbing and industrial applications.
Weld Fittings
These fittings are designed to be welded directly onto pipes or tubing, creating a permanent and robust connection.
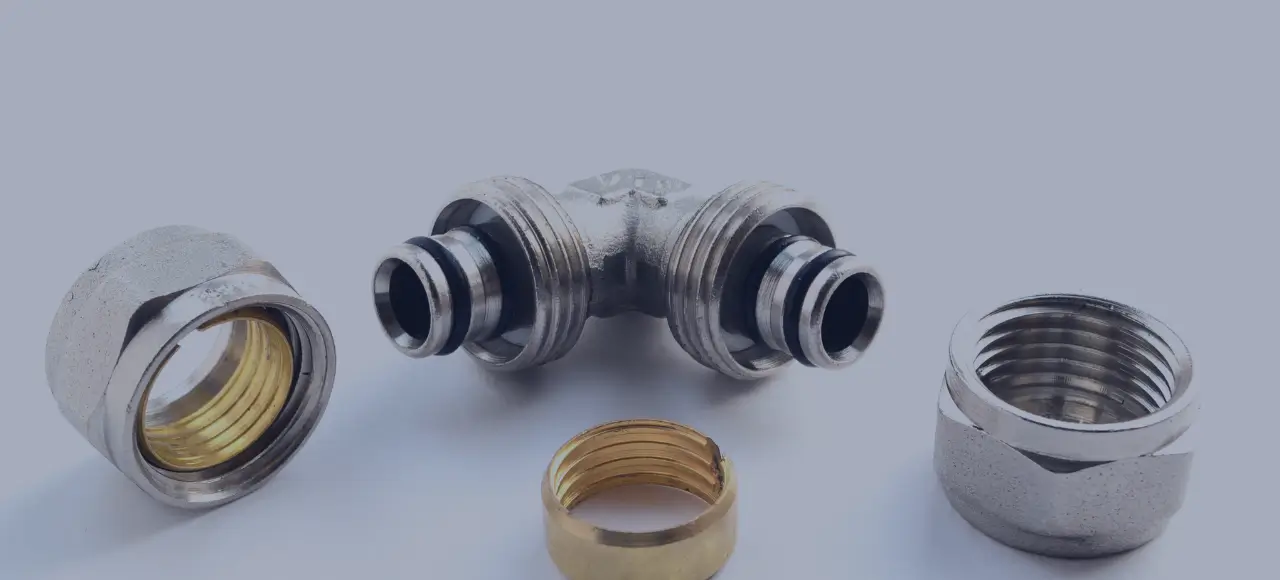
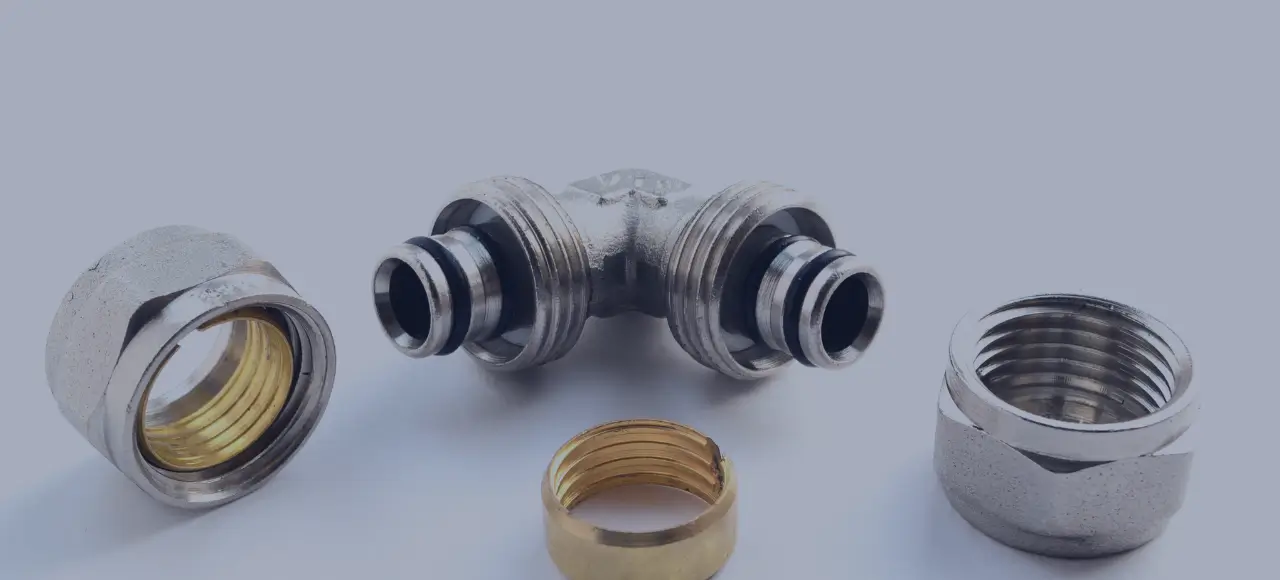
Key Elements To Focus On Tube Fitting
Several essential components and factors need to be considered to achieve secure and leak-free connections for tube fittings. These components play a crucial role in ensuring the integrity and safety of fluid systems. Here are the key elements to focus
- Pressure Testing: Perform pressure tests on the system after installation to check for leaks and ensure the connections can handle the expected operating pressures.
- Nut Tightening: Follow the manufacturer’s recommended torque specifications when tightening compression fittings. Under-tightening can result in leaks, while over-tightening can damage the fitting or tube.
- Manufacturer Guidelines: Follow the manufacturer’s installation instructions and guidelines for the specific type of tube fitting being used.
- Tube Preparation: Properly prepare the tube ends before installation. Ensure they are cut cleanly and squarely, without any burrs or deformations that could compromise the sealing integrity.
- Tubing Material: Use tubing made of compatible materials with the fittings to prevent chemical reactions and corrosion. Common tubing materials include copper, stainless steel, plastic (such as PVC, polyethylene, or nylon), and various alloys.
- Tube Fittings: Choose high-quality tube fittings appropriate for the application. Common types include compression fittings, flare fittings, push-to-connect fittings, barbed fittings, threaded fittings, and quick-disconnect fittings. Select the class based on the tubing material, fluid medium, pressure, and temperature requirements.
- O-rings or Gaskets: For certain types of fittings, such as quick-disconnect or hydraulic fittings, ensure the O-rings or gaskets are in good condition and correctly seated to prevent leaks.
- System Maintenance: Regularly inspect the fittings and tubing for wear, damage, or degradation signs. Replace any components showing signs of deterioration to maintain the system’s integrity.
- Thread Sealant/Tape: When using threaded fittings, apply appropriate thread sealant or PTFE tape to ensure a proper seal between the threaded components.
- Nut Tightening: Follow the manufacturer’s recommended torque specifications when tightening compression fittings. Under-tightening can result in leaks, while over-tightening can damage the fitting or tube.
- Cleanliness: Maintain a clean working environment and ensure all components, including the tubing and fittings, are free from dirt, debris, and contaminants. Foreign particles can compromise the sealing ability and lead to leaks.
- Ferrules or Compression Rings: If using compression fittings, ensure the ferrules or compression rings are made of suitable materials and correctly sized to match the tubing diameter. The ferrules are crucial in creating a leak-free seal when compressed against the tubing.
Plastic Tube Fittings
Plastic tube fittings are a type of fittings made from various plastic materials, such as polyethylene (PE), polypropylene (PP), polyvinyl chloride (PVC), and acrylonitrile-
butadiene-styrene (ABS). These fittings are commonly used in applications where metal fittings may not be suitable due to cost, corrosion concerns, or weight restrictions. Plastic tube fittings offer advantages such as lightweight, resistance to corrosion and chemicals, and ease of installation.
Square Tube Fittings and Brackets
Square tube fittings and brackets are specialized components designed to create connections, joints, and structural supports using square or rectangular tubing. These fittings and brackets are commonly used in construction, furniture manufacturing, handrails, and various DIY projects. They provide a versatile and efficient way to join square tubes and create rigid structures.
In conclusion, tube fittings are the backbone of secure and leak-free fluid-system connections, allowing industries to thrive while preserving safety, reliability, and efficiency. Embracing the advancements and best practices surrounding tube fittings ensures seamless fluid transmission continuity, making them essential components in our ever-changing world.




FAQs
There are various types of tube fittings, including compression, flare, push-to-connect, barbed, threaded, and quick-disconnect fittings. Each type is designed to suit specific applications and fluid system requirements.
Tube fittings create leak-free connections by forming a tight seal between the tubes or pipes they join. For example, compression fittings use a compression ring to compress against the tube, creating a secure seal, while push-to-connect fittings lock the tubing in place, ensuring a leak-free connection.
The reusability of tube fittings depends on the type and condition of the fitting. Compression and threaded fittings can often be reused after proper disassembly and reassembly. However, some push-to-connect and quick-disconnect fittings may be intended for something other than repeated use.
The ability of tube fittings to withstand high pressures and temperatures depends on their material, design, and specifications. Choosing fittings rated for the fluid system’s specific pressure and temperature requirements is crucial.
Regular inspection and maintenance are essential to ensure the continued integrity of tube fittings. Check for signs of wear, damage, or leaks and promptly replace any worn-out or damaged fittings. Always use compatible components and follow proper installation practices to maintain a leak-free system.