Modern technology plays a crucial role in revolutionizing the manufacturing landscape. One such technology is Computerized Numerical Control (CNC) machines. (CNC) machines are essential tools for precision metal fabrication manufacturers. They are crucial in shaping solid metal into intricate designs or uniform patterns with exacts.
Simply put, these machines use computer programs to control cutting tools or, in some cases, guide the raw material itself to create the specific shapes that are needed.
In this 21st century, steel fabrication has evolved significantly from its origins, where manual labor and rudimentary tools were employed. Modern steel fabrication facilities now rely on CNC technology for many reasons. This article will delve into the role of CNC in the world of steel fabrication and explore the many benefits it brings to the industry.
What is CNC, and How Does it Work in Steel Fabrication?
CNC is a technology that automates the control of machine tools and 3D printers using a computer. It uses precise numerical codes to dictate the movements of tools and machinery, ensuring accuracy and repeatability. CNC machines have motors and actuators that execute these codes, transforming raw materials into intricate parts and components with unparalleled precision.
In metal fabrication, CNC machines come in various forms, including CNC plasma cutters, CNC lasers, CNC routers, and CNC press brakes. Each of these machines specializes in a specific task, but they all share a common goal: to turn raw steel into precisely cut and shaped components for various applications.
The Advantages of CNC in Steel Fabrication
- Precision
One of the most significant advantages of CNC sheet metal fabrication is precision. CNC machines can make highly intricate cuts and bends that are virtually impossible to achieve manually. This precision is crucial in applications such as aerospace, where even the slightest deviation can compromise safety.
- Repeatability
CNC technology allows for the exact replication of parts and components. This is vital in industries where consistency is key, such as automotive manufacturing. CNC machines can churn out identical components at a rapid pace.
- Efficiency
CNC machines work tirelessly, 24/7, and don’t require breaks or sleep. This ensures optimal utilization of resources and minimizes downtime, ultimately leading to more efficient production.
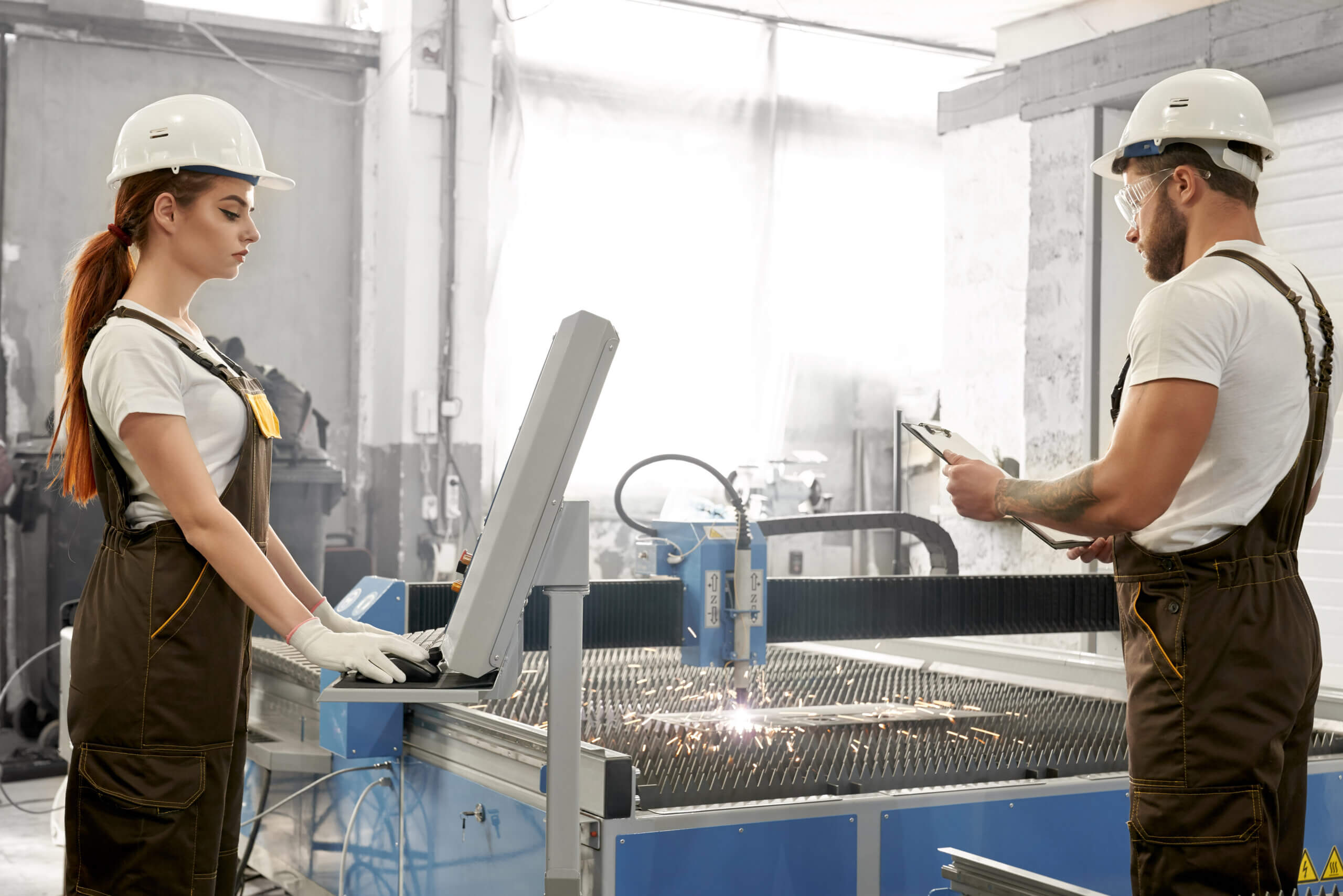
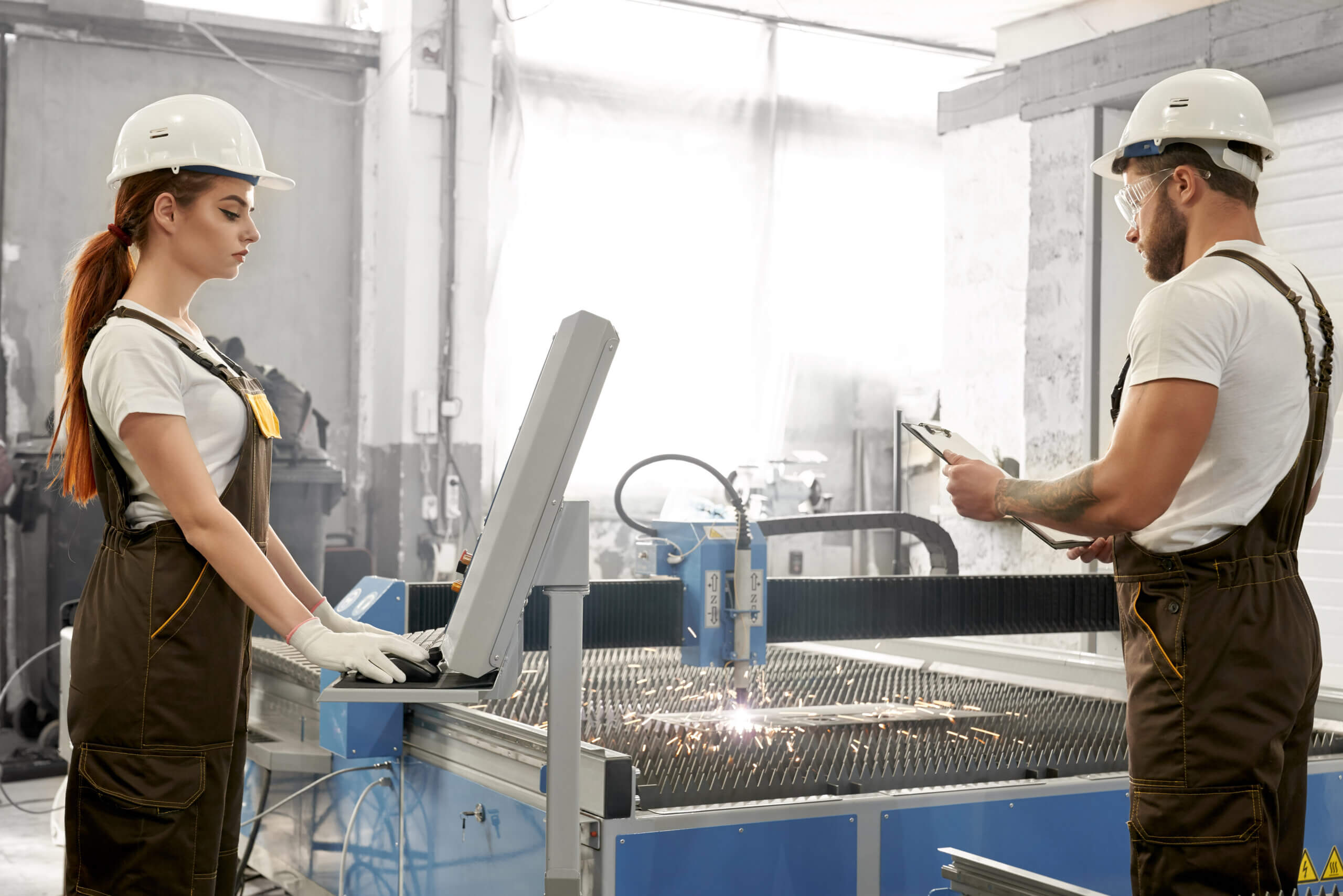
- Reduced Waste
CNC machines are adept at optimizing material usage. They minimize waste by tightly nesting parts on a single sheet of steel, thus reducing scrap and saving costs.
- Complex Geometries
CNC technology can handle complex shapes and designs that would be labor-intensive or impossible to achieve with manual methods. This flexibility opens up new design possibilities for engineers and architects.
- Quick Setup
CNC machines can be quickly reprogrammed for different jobs, reducing setup times significantly. This makes them adaptable to various tasks, from prototyping to high-volume production.
- Safety
Automated processes mean fewer manual operations, reducing the risk of accidents and injuries. Operators can monitor the machines and intervene only when necessary.
- Data-Driven Optimization
CNC machines can be integrated with data analytics tools, allowing fabricators to monitor performance, identify bottlenecks, and optimize production processes.
Common Types of CNC Machines in Steel Fabrication
CNC technology has revolutionized metal fabrication, and it comes in various forms, each specialized for specific tasks. Here are some common types of CNC machines used in the steel fabrication industry:
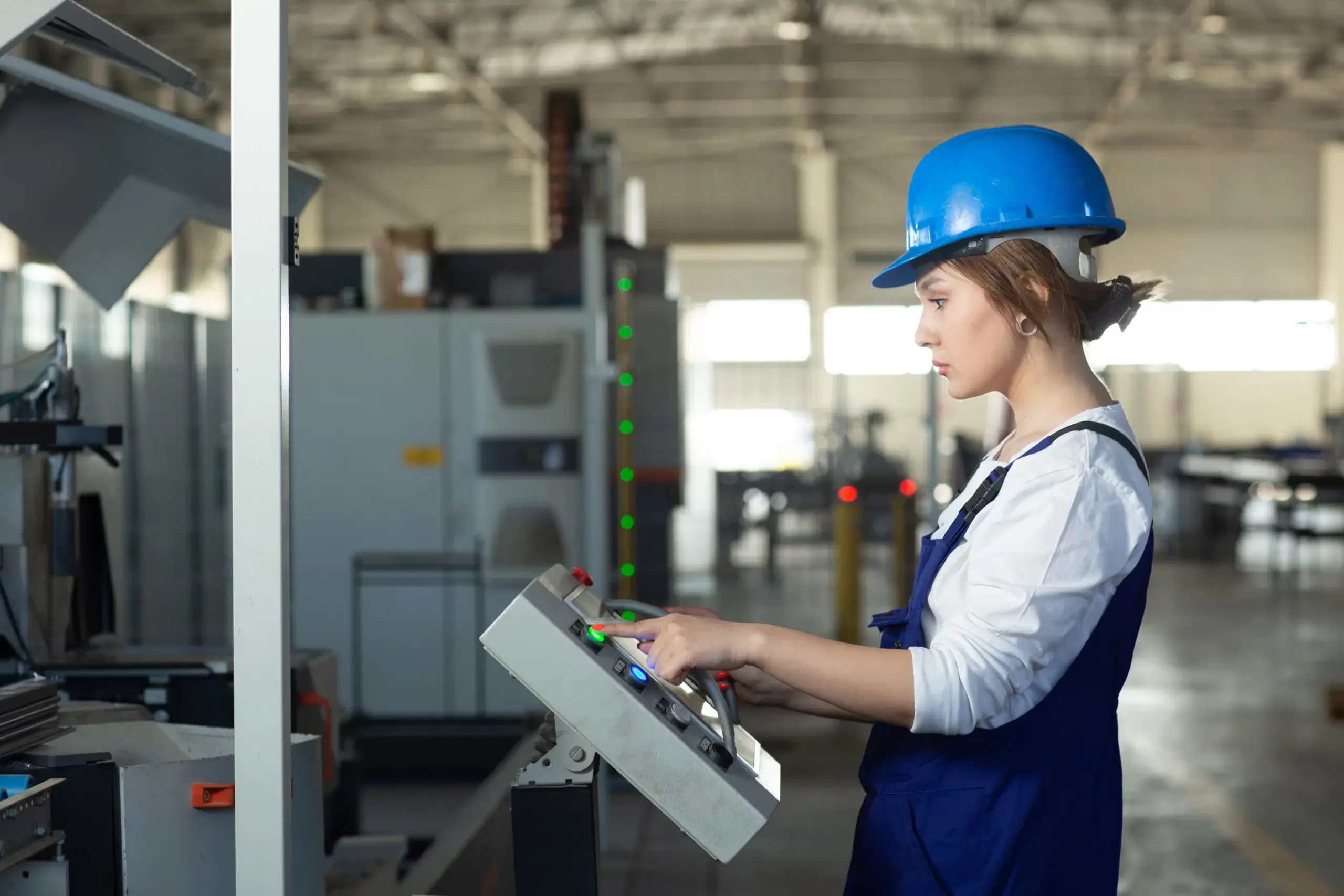
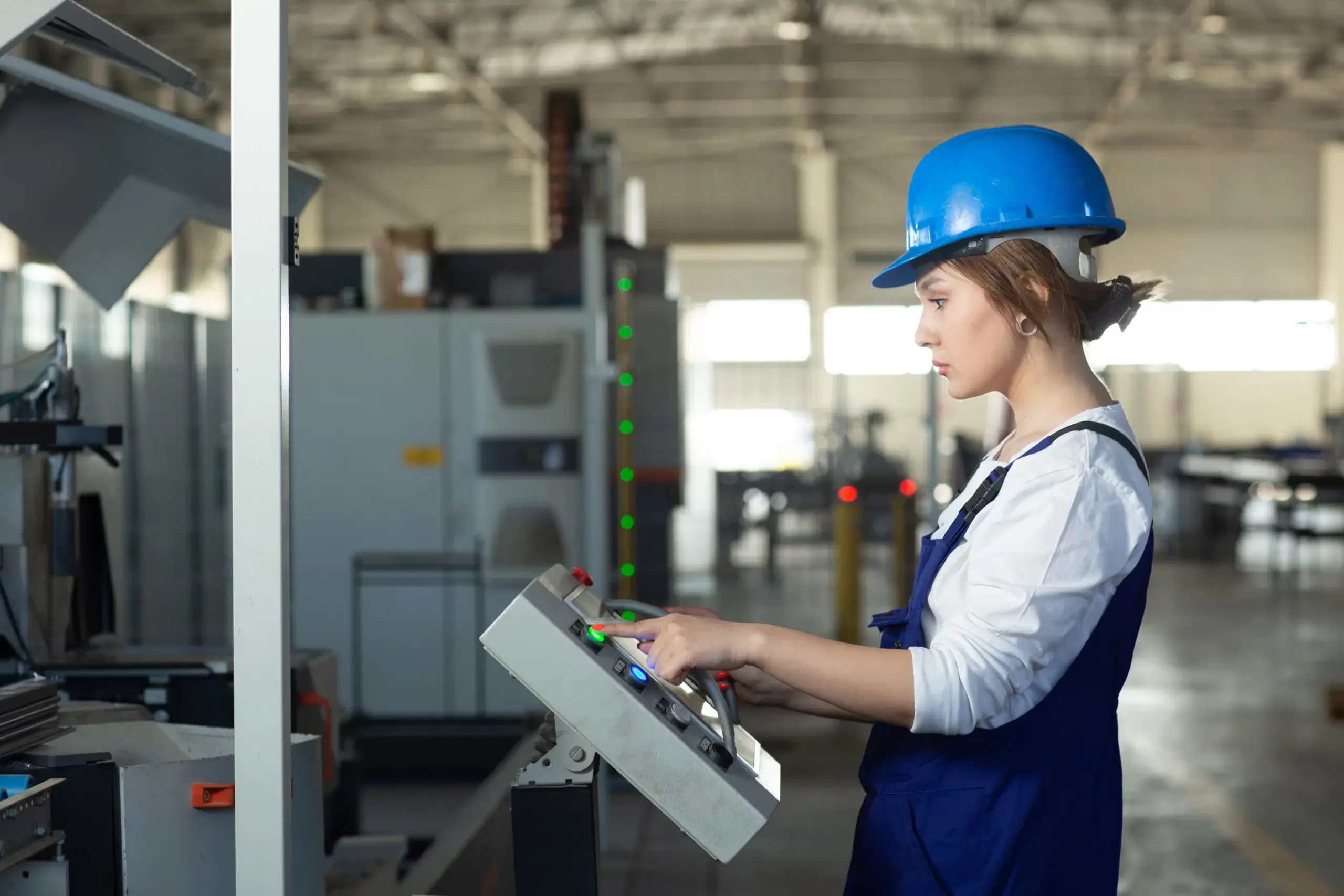
CNC Plasma Cutters
Plasma cutting is a process that uses a high-velocity jet of ionized gas to cut through steel. CNC plasma cutters are known for their speed and precision in cutting steel plates of varying thicknesses. They are widely used in applications that require straight or curved cuts, such as in the creation of custom metal parts and intricate designs.
CNC Laser Cutting Machines
Laser cutting is another exact method of metal fabrication. CNC laser cutters use a high-powered laser to cut through steel, creating clean and accurate cuts. They are commonly used to produce thin to medium-thickness steel components, including intricate shapes and patterns.
CNC Press Brakes
CNC press brakes are used to bend and shape steel sheets and plates. These machines use powerful hydraulic or mechanical force to form steel into a desired shape. They are crucial in producing components such as brackets, enclosures, and structural elements that require precise angles and bends.
CNC Milling Machines
While milling machines are not exclusive to metal fabrication, they are versatile tools that can be adapted for steel-related tasks. CNC milling machines use rotary cutters to remove material from a workpiece. They are often used for creating complex 3D shapes, holes, and threads in steel components.
CNC Machining Centers
Machining centers are multipurpose machines with various cutting tools, including drills, end mills, etc. They are used for the precision machining steel components, from intricate parts to larger items like engine blocks and transmission cases in the automotive industry.
CNC Waterjet Cutters
Waterjet cutting machines use a high-pressure stream of water mixed with abrasive particles to cut through steel and other materials. This cold-cutting process is ideal for heat-resistant materials, as it does not introduce thermal stress. CNC waterjet cutters are versatile and can handle various material thicknesses and shapes.
CNC Routers
CNC routers are used for shaping and cutting steel, typically in decorative or artistic applications. They can create intricate patterns and designs by removing material from a steel surface. CNC routers are commonly used in metal art, architectural features, and signage.
CNC Punch Presses
CNC punch presses are designed for hole-punching and forming operations in steel sheets and plates. They are widely used in applications that require many holes or specific shapes to be created with precision, such as in electrical enclosures and panels.
CNC 3D Printers
Additive manufacturing, or 3D printing, is becoming increasingly crucial in metal fabrication. CNC 3D printers build steel components layer by layer, making them ideal for creating complex and customized parts with minimal waste. This technology is being explored for various applications, from prototyping to rapid tooling and construction.
Applications of CNC in Steel Fabrication
The applications of CNC in metal fabrication are vast and diverse. Some of the most notable applications include:
- Structural Steel
In the construction industry, CNC technology fabricates beams, columns, and other structural components with precise holes and cuts. This ensures easy assembly on-site and minimizes errors in construction.
- Automotive Manufacturing
CNC is pivotal in producing automobile parts, from body panels to engine components. The precision of CNC machining is crucial for the functionality and safety of vehicles.
- Aerospace
The aerospace industry relies on CNC to produce critical components such as engine parts, landing gear, and brackets. These components must meet stringent quality and safety standards.
- Metal Art and Sculptures
CNC technology is also used for artistic applications, creating intricate metal sculptures and decorative items with incredible detail.
- Custom Fabrication
For custom projects, such as architectural features and prototypes, CNC allows for the precise realization of unique designs.
Challenges and Limitations of CNC in Steel Fabrication
While CNC technology offers numerous benefits, it has its challenges and limitations. These include the initial investment in machinery and training, the need for regular maintenance, and the fact that CNC machines are not suitable for all types of metal fabrication.
Additionally, CNC machines are limited by their programming, so they can only adapt to unforeseen situations with human intervention.
The Future of CNC in Steel Fabrication
CNC technology in metal fabrication is constantly evolving. Future advancements may include improved integration with digital technologies like 3D printing, artificial intelligence, and the Internet of Things. These developments could lead to even greater automation, precision, and efficiency in the industry.
In Conclusion
CNC technology has transformed the landscape of modern metal fabrication. As technology advances, CNC sheet metal fabrication will only become more critical, pushing the boundaries of what is possible in steel construction and manufacturing.
Zetwerk is a leading manufacturing company that utilizes CNC technology to meet your unique needs for steel fabrication projects. Contact Zetwerk to know how they can help you with your next project.




FAQs
CNC is Computer Numerical Control, a technology that automates machine tools using precise numerical codes. It differs from traditional methods by offering unparalleled precision and repeatability, reducing waste, and enabling complex geometries.
CNC technology is widely used in construction (structural steel), automotive manufacturing, aerospace, metal art and sculptures, custom fabrication, and many more. It is suitable for applications that demand precision and efficiency.
Some limitations include the initial investment in machinery and training, the need for regular maintenance, and the fact that CNC machines are not suitable for all types of steel fabrication. Additionally, CNC machines are limited by their programming and require human intervention for unforeseen situations.
The future of CNC in steel fabrication looks promising, with ongoing advancements in integration with other digital technologies, like 3D printing, artificial intelligence, and the Internet of Things. These developments are expected to bring greater automation, precision, and efficiency to the industry.