Introduction
The aerospace industry is a key player in manufacturing high-quality aircraft that meet stringent safety and performance standards. Aerospace components manufacturing requires exceptional precision and complexity due to the critical nature of these parts. From extrusions to die casting, CNC machining to injection molding, aerospace components manufacturers employ various manufacturing processes to create reliable and durable parts.
This article explores the intricacies of aerospace components manufacturing, assembly processes, and the role of lean manufacturing principles and advanced technologies in ensuring quality. Whether it’s producing machined components or complete assemblies, Zetwerk offers expertise and capabilities to meet the demands of the aerospace industry.
Know About Current and Future Perspectives Aerospace Tooling Market
Aerospace Components Manufacturing
To manufacture aerospace components, a wide range of processes are employed by aerospace components manufacturers such as extrusions, die casting, CNC machining, forging, injection molding, sheet metal stamping, and investment casting. These processes ensure precise dimensions and excellent mechanical properties for each component.
For example, extrusion is commonly used to create complex profiles for structural parts like fuselage frames or wing stringers. Die casting allows for high-volume production of intricate shapes such as engine housings or gearbox cases. CNC machining provides exceptional accuracy for critical components like gears or engine rotors.
Different materials are used based on their specific characteristics and requirements. Titanium alloys are preferred for their high strength-to-weight ratio in applications like landing gear or engine components. Aluminum alloys are widely used for their lightweight properties in structural parts such as wings or fuselages. Stainless steel is often chosen for its corrosion resistance in areas prone to moisture exposure.
At Zetwerk, we work closely with our network of certified suppliers who specialize in different manufacturing processes to ensure high-quality components at competitive prices. Our rigorous supplier selection process ensures that our partners have the necessary qualifications and experience to meet the aerospace industry’s stringent requirements.
Common Materials Used in Aerospace Machining
Material | Application |
---|---|
Titanium alloys | Landing gear, engine components |
Aluminum alloys | Wings, fuselages |
Stainless steel | Structural parts, fasteners |
Inconel | Turbine blades, exhaust systems |
Superconducting copper | Electrical wiring |
Certain types of plastic | Interior components, non-structural parts |
Assembly Process in Aerospace Industry
The assembly process in the aerospace industry involves joining various subassemblies to create a complete aircraft. It starts with the joining of fuselage subassemblies using supporting jigs or fixtures. The vehicle then moves through a series of workstations where additional subassemblies and onboard systems are installed.
Light- and medium-weight aircraft can be moved on wheeled fixtures, while heavier aircraft require cranes or air-cushion techniques for movement within the assembly facility. Major assembly steps include adding nose and tail sections, wings, engines, and landing gear. Once assembly is completed at the last station, the aircraft undergoes a production flight test to ensure specified performance.
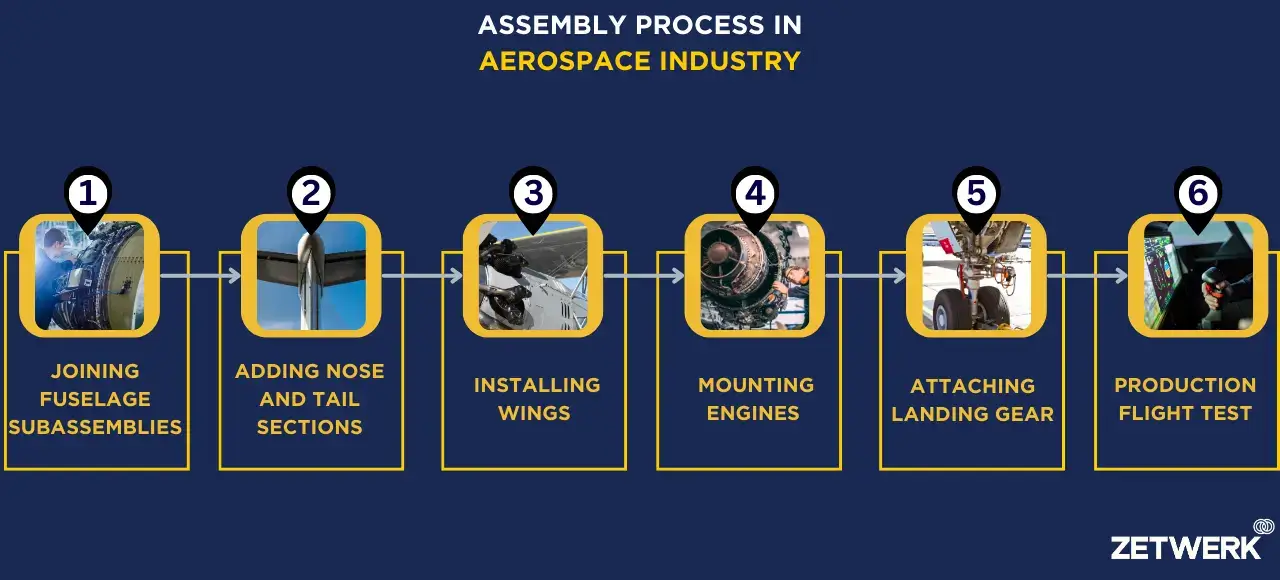
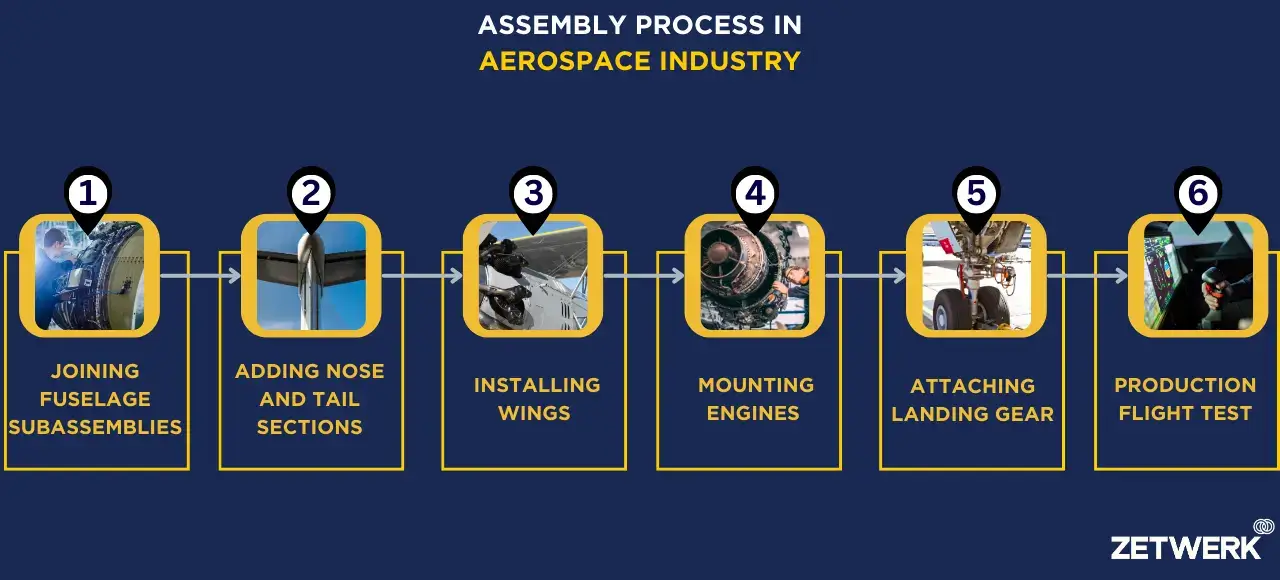
1. Joining fuselage subassemblies
2. Adding nose and tail sections
3. Installing wings
4. Mounting engines
5. Attaching landing gear
6. Production flight test
Spacecraft Assembly
Spacecraft assembly is conducted under clean-room conditions to prevent contamination that could jeopardize mission success. Clean rooms have strict atmospheric controls for temperature, humidity, and dust particle filtration. Two assembly methods are commonly used: successive workstations or fixed positions. In successive workstations, teams install onboard systems one after another. In fixed positions, each team is responsible for installing specific systems at designated locations.
Detailed acceptance checkouts are performed within the clean room environment to ensure that all systems and components are functioning properly before shipment. This ensures that the spacecraft is delivered in optimal condition.
Verification Processes for Aerospace Vehicles
Verification processes play a crucial role in ensuring the quality of aerospace vehicles after assembly. Extensive inspections are conducted on structural and mechanical items to detect any defects or discrepancies. Functional verification involves testing equipment such as control surfaces, landing gear operation, avionics performance, and environmental conditioning.
For space missions and launch vehicles, validation methods are employed to simulate actual operational conditions or use communication and command links similar to those used during the mission. These rigorous validation processes ensure that the vehicle can perform reliably in its intended environment.
Lean Manufacturing in the Aerospace Industry
Lean manufacturing principles have been implemented in the aerospace industry to reduce costs and product cycle times by up to 50%. Derived from studies in the automobile industry, lean manufacturing focuses on waste minimization, optimization of material and information flow, and superior quality.
The successful implementation of lean manufacturing requires significant cultural changes within organizations. It empowers integrated teams of workers with decision-making responsibilities at the operational level. The adoption of lean initiatives throughout design, production, administration, support functions, customers, and suppliers has resulted in improved efficiency and reduced waste.
Final Words
The aerospace industry’s manufacturing processes for components and assemblies require exceptional precision and adherence to strict quality standards. From extrusions to CNC machining and injection molding to investment casting, each step plays a critical role in producing high-quality aerospace parts.
The lean manufacturing principles implemented in the industry have led to significant improvements in cost reduction, cycle times, and overall efficiency. By partnering with Zetwerk, companies can access its expertise and network of certified suppliers to meet their aerospace manufacturing needs. Explore Zetwerk’s services for comprehensive solutions that ensure reliable aerospace components and assemblies.
Discover Zetwerk’s range of services for aerospace components manufacturers, including advanced technologies like CNC machining, forging, injection molding, sheet metal stamping, and more. Visit Zetwerk’s Knowledge Hub today for further insights into the aerospace industry.




FAQs
Common materials used in aerospace machining include titanium alloys, aluminum alloys, stainless steel, Inconel, superconducting copper, and certain types of plastic. These materials are selected based on their specific properties and application requirements.
Aerospace companies implement stringent verification processes before production flight tests. These include extensive inspections on structural and mechanical items as well as functional verification of equipment such as control surfaces, landing gear operation, avionics performance, and environmental conditioning.
Clean rooms play a crucial role in preventing contamination during spacecraft assembly. They have strict atmospheric controls to regulate temperature, humidity, and dust particles. This ensures that the spacecraft is assembled in a clean environment, free from contaminants that could affect its performance.