The processes and systems have significantly transformed over the years in the vast warehousing world. The primary objective has always been to streamline operations, reduce errors, and increase efficiency. The warehouse pick and pack process is one of the most crucial warehousing aspects. This article delves deep into the evolution of the pick-pack process, highlighting the milestones that have defined its transformation.
The Genesis of Warehouse Pick and Pack
The warehouse pick and pack process is a concept that has been introduced previously. Historically, workers would manually pick items from shelves, pack them, and then ship them to the customer. This method, while straightforward, was prone to human errors and was time-consuming.
Automated Advancements in Picking Systems
Before the advent of modern solutions, manual processes dominated the warehousing landscape. However, as the demands of the industry evolved, so did the methods. Let’s explore some automated warehouse picking systems that have revolutionized the pick and pack process.
Types of Automated Picking Systems
Pick to Light Systems
These systems use light indicators to guide workers to the correct items and quantities. It’s a visual system that reduces the chances of picking errors.
Voice-directed Picking
Workers receive voice commands through headsets, directing them to pick specific items. This hands-free method increases efficiency and accuracy.
Robotic Picking
Robots with advanced sensors and AI can pick items from shelves and place them in bins. This method is especially useful for heavy or bulky items.
Challenges and Solutions
Despite the advancements, challenges persist. For instance, setting up an automated system requires significant investment and training. However, the ROI, in the long run, justifies the initial costs. Additionally, as technology evolves, there’s a need for continuous upgrades to stay competitive.
The Future of Warehouse Pick and Pack
The future hinges on integrating diverse systems for seamless, efficient, and error-free operations. Physical and digital warehousing lines will blur as we move forward, leading to a more interconnected and intelligent system.
Augmented Reality (AR) in Picking
AR is set to revolutionize the warehouse pick and pack process. With AR glasses, workers can see digital overlays on physical items, guiding them to the correct product locations and providing real-time information about inventory levels. This not only speeds up the picking process but also significantly reduces errors.
Drones and Their Role in Warehousing
While drones are commonly associated with aerial photography or deliveries, they have a potential role in warehousing. Drones equipped with cameras and sensors can locate and retrieve items from high shelves, eliminating workers needing to climb ladders or use forklifts. This can speed up the warehouse pick pack process and reduce the risk of workplace accidents.
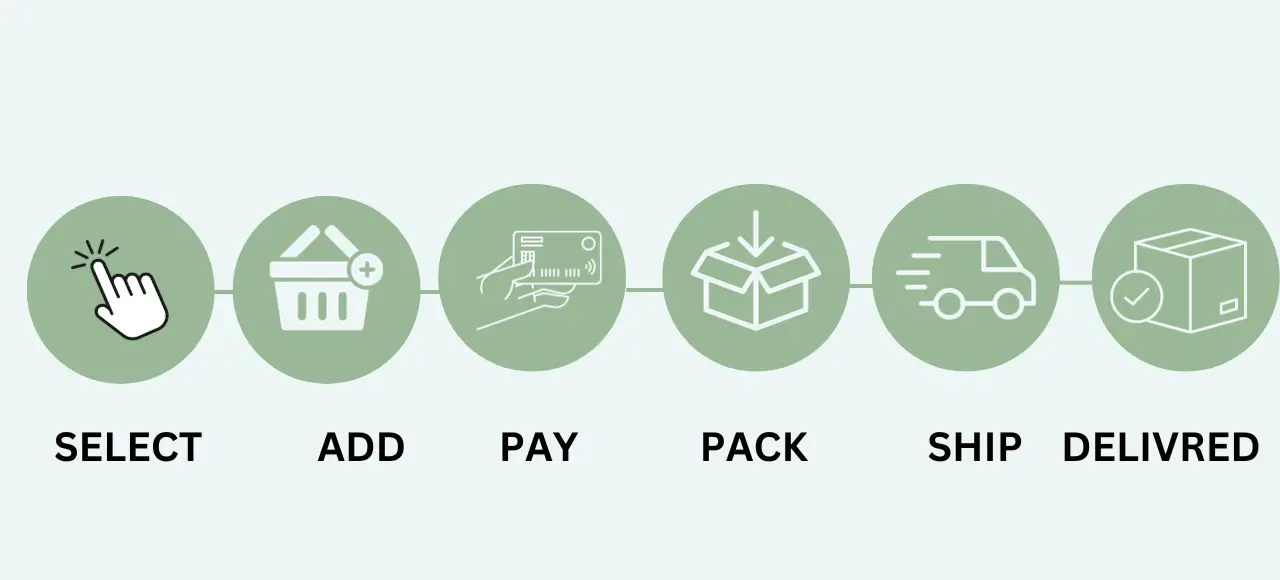
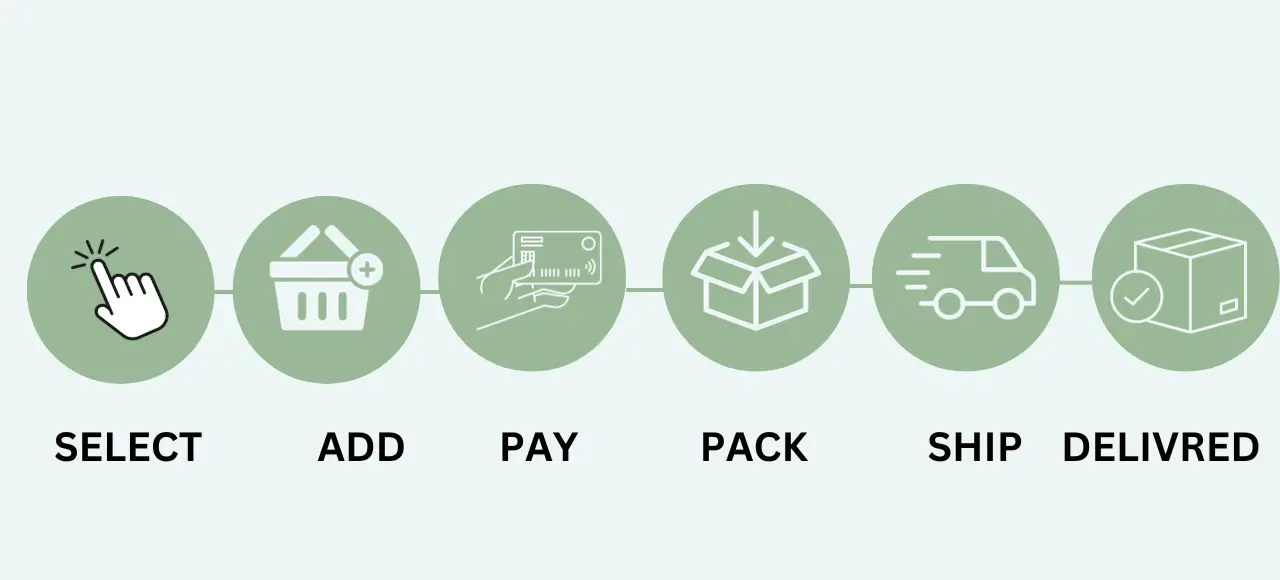
Embracing IoT in Smart Warehousing
The Internet of Things (IoT) is more than just a buzzword. It epitomizes the interconnected nature of devices and systems communicating over the internet. This translates to a more innovative, more responsive environment in the warehousing context.
IoT is about connecting devices to the internet, leading to smart shelves, bins, and products in warehouses. These connected devices can communicate with the warehouse management system in real-time, offering updates on stock levels and product locations and even predicting when restocking is needed. Such a high level of connectivity ensures that the warehouse pick and pack process consistently relies on the most recent data, minimizing the chances of errors.
Customization and Personalization
As consumer demands become more specific, warehouses must adapt to offer personalized picking and packing solutions. This could mean customized packaging, bundling of particular products, or even personalized notes included in shipments. Advanced warehouse pick and pack systems will be at the forefront of this trend, ensuring each order meets the customer’s unique needs.
The Impact of an Efficient Pick and Pack System
An optimized pick-and-pack system can significantly elevate a business’s performance. The benefits are manifold:
- Precision: A decrease in mis-picked items means there’s no need to spend additional time and resources returning things to their rightful place.
- Reduced Returns: A more accurate system leads to fewer returns, minimizing the need to refund or replace items incorrectly picked.
- Customer Satisfaction: An efficient system translates to timely deliveries, bolstering brand reputation and fostering customer loyalty.
- Boosted Morale: A smooth-running operation instills confidence in warehouse teams, leading to a more motivated workforce.
It’s worth noting that pick and pack operations account for a significant portion of labor time in warehousing. Studies suggest approximately 70% of labor is dedicated to picking products off the shelves.
Decoding the Stages of Pick and Pack
- Order Reception: Typically facilitated by e-commerce fulfillment software, an order placed through any online channel generates a packing slip. Many of these software solutions also provide an optimal picking sequence with the slip.
- Pick: Whether manually by a warehouse worker or through an automated system, items listed on the packing slip are retrieved from the shelves.
- Pack: Once orders are compiled, they’re placed into a shipping container, padded with dunnage to prevent movement, and occasionally accompanied by promotional items. Many businesses also incorporate a verification step at this juncture to ensure order accuracy. Finally, a shipping label is affixed.
- Ship: The order is then handed off to the chosen logistics provider, a courier service, the postal system, or a private fleet for delivery.
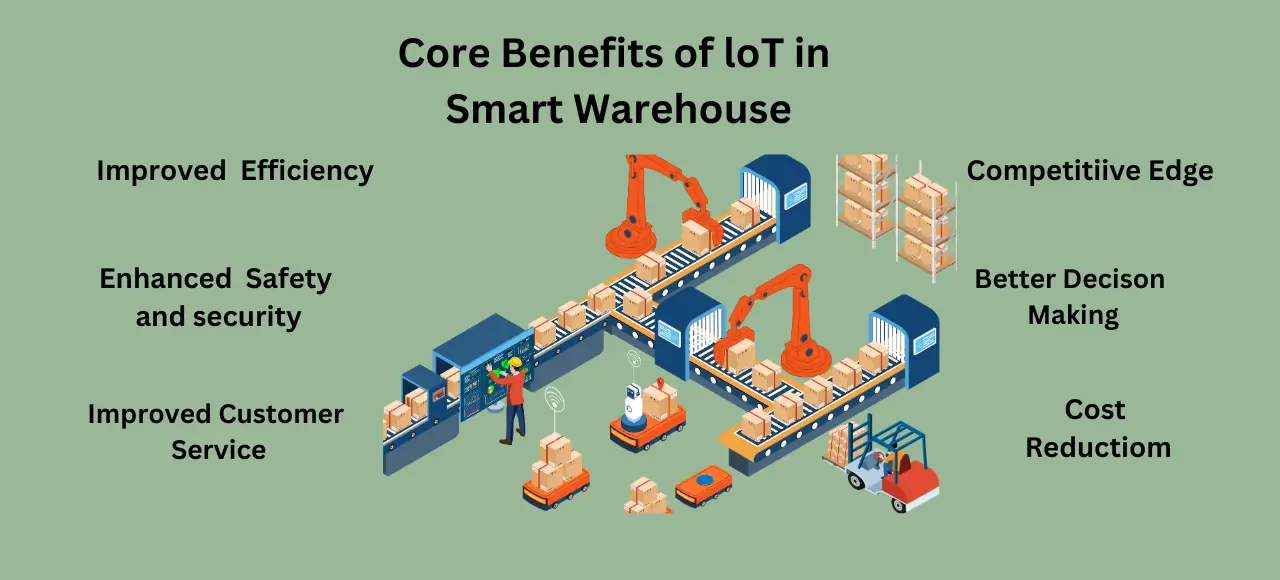
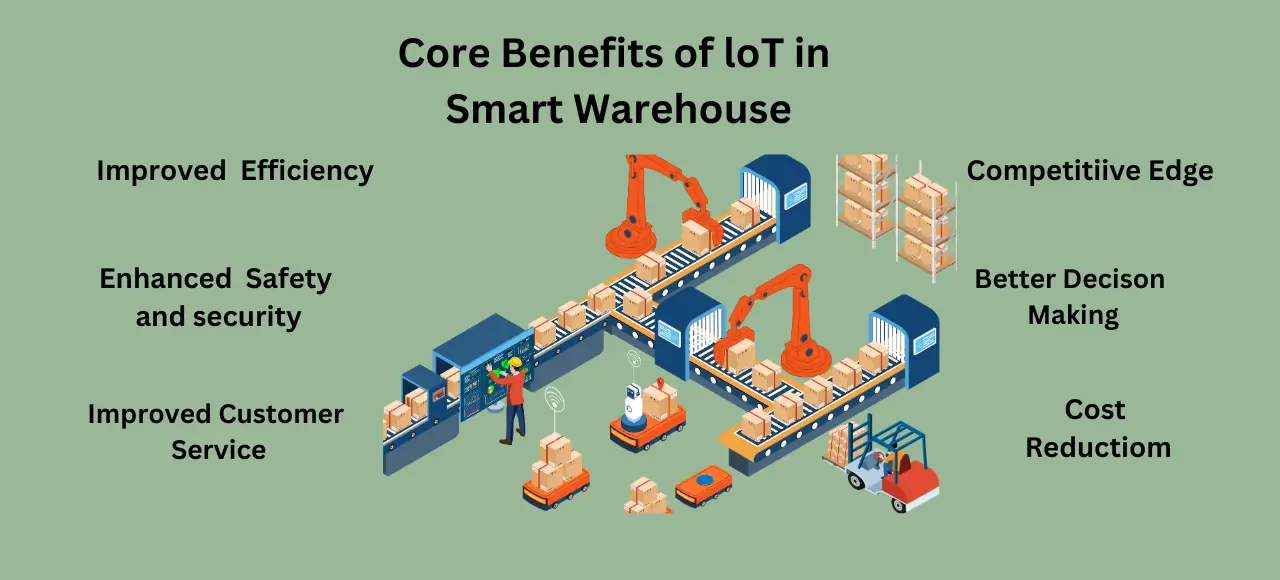
A Dive into Traditional Methods
While automation is the future, it’s essential to understand the roots of the pick-and-pack process. Manual systems, though older, still hold value and are used in many warehouses today. Let’s take a closer look at these traditional methods.
Manual Pick and Pack Systems: A Closer Look
While there are both manual and automated systems, let’s delve into the manual ones:
- Single Order Picking (SOP): Ideal for niche small businesses, this method involves a picker collecting items for one order at a time. It’s most efficient for businesses shipping to fewer than 30 customers daily.
- Batch Picking: Here, a selector is assigned a batch of orders ranging between 10 to 30. They collect items for the entire batch in one go and then return to the packing area. This method best suits businesses with a high order volume but a limited product range.
- Zone Picking: In this sophisticated system, pickers are designated specific zones within the warehouse. They only pick items from their assigned zones. Orders move from one zone to another, accumulating items until they’re complete. This method is efficient for high-volume orders, especially since pickers become familiar with their zones.
- Wave Picking: Similar to zone picking but with a twist. All zones are picked simultaneously, and items are consolidated into individual orders at a central point. While faster than zone picking, it requires more coordination and training.
Two key metrics should be considered to determine a business’s best pick and pack system: average order processing time and return rates. By evaluating these factors and understanding whether speed or accuracy is a higher priority, businesses can trial different systems, gather data, and ultimately select the most suitable method for their operations.
Final Thoughts!
From humble manual beginnings to the dawn of sophisticated automated systems, the warehousing industry’s journey underscores its dedication to achieving unparalleled efficiency and precision.
FAQs
The primary aim of warehousing processes is to streamline operations, reduce errors, and increase efficiency.
Historically, workers would manually pick items from shelves, pack them, and then ship them to the customer. This method was straightforward but was prone to human errors and was time-consuming.
Some automated systems include Pick to Light Systems, Voice-directed Picking, and Robotic Picking.
Setting up an automated system requires significant investment and training. Additionally, as technology evolves, there’s a need for continuous upgrades to stay competitive.
AR glasses allow workers to see digital overlays on physical items, guiding them to the correct product locations and providing real-time information about inventory levels. This speeds up the process and reduces errors.