Have you ever had a Root Canal Treatment (RCT)? What happens?
It’s a process, you have your tooth drilled, you bite down on a piece of soft material, a cast of your teeth is taken and you are sent home. The dentist (more likely, their assistant) then creates a custom ‘crown’ for your tooth, based on your own tooth’s specifications. This crown is then matched with the cast to ensure quality.
Once you go back to the dentist, they fix the crown and make final modifications so that you can bite perfectly, give you some meds, and send you on your merry way. They then save the 3D mold in their database, so that the process can be repeated if that tooth is damaged again. This saves cost and effort for the next time.
Congratulations! You just saw an (approximate) example of DFM in our daily lives.
Know About Significance of Design for Manufacturing (DFM) Capabilities
What is DFM?
Design for Manufacturing or Design for Manufacturability (DFM) is the optimization of a part, product, or component’s design to make it cheaper and easier to produce. DFM involves efficiently designing or engineering an object, typically during the product design stage, to reduce manufacturing costs. This allows manufacturers to identify and prevent mistakes or discrepancies.
The specific process of DFM will vary depending on the product being designed and produced. Some general principles of DFM include designing objects for efficient assembly, standardizing materials and components, reducing the number of parts, and minimizing the number of manufacturing operations required during assembly. Other key aspects of effective DFM include standardizing parts to save on costs, designing for simplicity to reduce the complexity or number of required parts, and reducing setup time.
There are a range of reasons why DFM is invaluable in the competitive markets of the present day. Let’s take a look at how following DFM principles can result in an efficient design and manufacturing setup:
- Parts may be combined to reduce assembly steps and quantity of parts
- Higher quality of a product, as design can be refined and enhanced at every stage
- Build realistic cost models in line with product objectives
- Minimize manufacturability issues so that the product can be manufactured quicker and in a more economical way
- Create an efficient design that leaves room for potential design changes in the later stages without a huge cost
- Ascertain unnecessary design features that add costs and eliminate them
- Drive down supplier bids by modifying the design using DFM principles
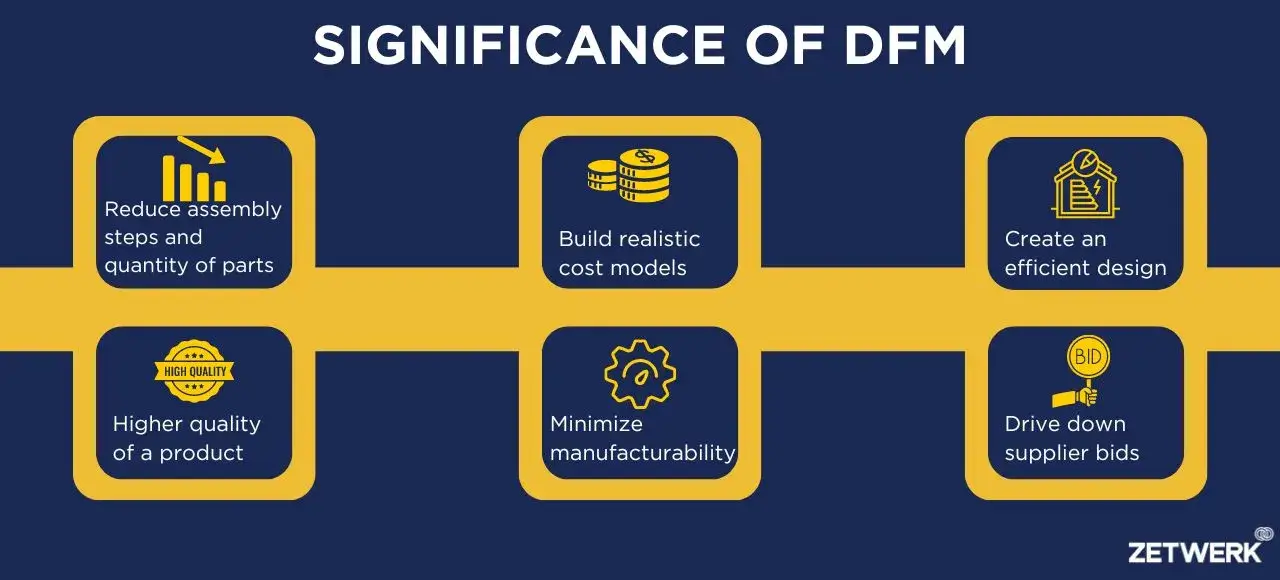
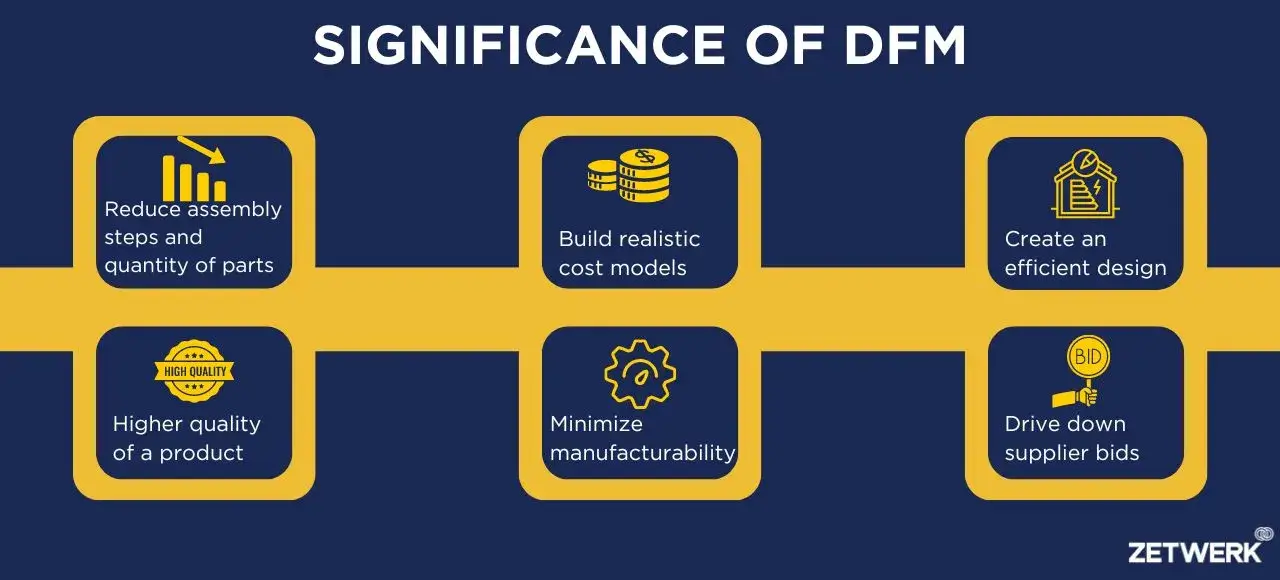
Why is Design for Manufacturing Important?
For any business looking to make money and create profitable products, DFM is vital for efficiency, speed, and high rates of production. It is thought that approximately 70% of the manufacturing costs of a product derive from design decisions made in the early design stages, such as materials used or methods of manufacturing. DFM therefore has great cost-reduction capabilities.
A focus on the design stage, available through DFM, would significantly reduce the final production cost. It can also enable the identification, quantification, and elimination of waste or inefficiencies at various points throughout the manufacturing and production process. It may additionally be used as a method of benchmarking and, in doing so, a company can assess the products of competitors.
When manufacturing companies have poor Design for Manufacturing (DFM) practices, it can lead to various issues such as increased production costs, longer time-to-market, and a higher likelihood of defects.
A robust DFM process has severe ramifications when faced with supply chain disruptions such as those faced during COVID-19 or the current trade war with China. You’ll find out more on this in the next section.
Shifting Supply Chains: From China to Friendlier Shores
Till 2020, global supply chains were ubiquitously Sino-centric. Most, if not all, OECD nations imported substantially from China, which had become the global export hub. This put China at a considerable advantage when it came to dealing with global suppliers.
U.S.-China trade exploded in the two decades after China joined the World Trade Organization in 2001. This trade has benefited U.S. and Chinese consumers and companies, but Washington is increasingly concerned about the risks posed by Beijing’s policies and its increasingly combative stance with the USA.
The current geopolitical tensions have put the proverbial brakes on this smooth supply chain. A growing number of North American enterprises are looking to move their manufacturing out of China. Forbes mentioned that companies are examining their heavy concentration in China. Boards and companies are reevaluating their risks and reviewing mitigation strategies.
This trend is being driven by several factors:
- Rising labor costs in China
- The ongoing trade war between the United States and China with the USA introducing high tariffs on Chinese imports, making them uncompetitive, and
- Concerns about China’s political and economic stability.
Some examples of major companies that are considering moving some of their manufacturing away from China include Intel, Microsoft, Apple, Nike, Dell, etc. Business Insider indicated, in recent years, companies including Apple and Mazda have been moving away from Chinese factories to neighboring Asian countries such as India, Vietnam, and Bangladesh.
But, the last 2 decades of business as usual with China along with little to no oversight or hindrance has resulted in a peculiar problem, that our current customers who earlier moved out of China have reported.
During our DFM process, when we compared the samples made in China with the original plans, we were taken aback to find that many of the parts slightly differed from the plans. The differences were clever enough that the custom-engineered machine worked well together when all parts were sourced from China, but most parts were altered to some degree.
When companies diversified their supply chains, these Chinese-origin parts simply did not fit with made-to-spec parts from other countries. The reason?
Since China specializes in a lot of simpler fabrication techniques but is behind countries like Taiwan in high-precision tool manufacturing, it seemed like Chinese suppliers had altered the parts so that they could be created more simply in massive volumes, without notifying their clients. This came as a shock to our clients when they realized it, thanks to Zetwerk’s detailed DFM process.
To prevent this from ever happening in any Zetwerk-affiliated factory, be it in India, Vietnam, or Mexico, Zetwerk follows a rigorous DFM process that ensures the delivered material does not deviate from the original plans. There are multiple subject matter experts involved in every step, which maintains the integrity of the process.
Zetwerk’s Process Orientation – A Rigorous DFM Workflow
- Upon receiving the purchase order, we promptly assemble a safety team with the Program Manager serving as the primary point of contact.
- This team also comprises an in-house engineer, a quality expert, and a sourcing resource. Together, these four individuals collaborate closely with the supplier.
- Before commencement, we develop a Design for Manufacturability (DFM) and present it to the client for approval.
- Once the client signs off, we initiate the project.
- To ensure seamless communication, the Program Manager provides weekly updates to the customer every Monday, no surprises. This safety team creates the samples.
- This is followed by a PPAP (Production Part Approval Process). If passed, that particular sample is good for running in mass production.
- The supplier runs this product for a certain batch, while we document all the process parameters. This documentation is thoroughly cross-checked and we ensure that it can go for mass production smoothly.
- Since the documentation has been done, we can always go back to this in case there’s a problem. It’s a process that ensures a safe starting point for mass production.
- Mass production is done and the product is delivered to you at your doorstep.
About Zetwerk
Zetwerk works with original equipment manufacturers in North America and worldwide, fulfilling their manufacturing requirements for customized components and assemblies. We act as a second brain to the OEMs. Our team of experts not just executes the customer’s manufacturing strategy, but adds tangible value at every step of the process, right from vetting designs to finding and managing the suppliers to quality control and logistics. Our customers regard us highly for our transparent and hands-on approach to manufacturing.
Zetwerk executes these projects through its network of partner suppliers spread across USA, India, China, Vietnam, and Mexico. These world-class facilities provide practically unlimited production processes, capacities, materials, part sizes, and weights as well as secondary operations, surface finishing, assembly, and related services. Importantly, we have our teams established in all these countries with a particularly large presence in the US.
Zetwerk recently acquired Unimacts, a US-based manufacturing services company, providing further impetus to our commitment to serve North America as a primary market. We have more than 2,000 customers across North America, Asia-Pacific and the Middle East, and a network of more than 10,000 manufacturing partners worldwide. Founded in 2018, we are backed by some of the world’s leading venture capital firms including Sequoia, Kae Capital, Accel Partners, Lightspeed, and GreenOaks. As of 2023, Zetwerk was valued at US$ 2.8 Bn.
Our manufacturing facilities employ the latest techniques and maintain all relevant certifications to ensure the highest quality control for our customers as well as compliance with all regulatory requirements, and legal practices. You can view our certifications here.
To know more about how we function, check this.
If you are looking for a global sourcing partner, look no further.



