Introduction
Rubber bushings, or rubber mounts or grommets, are essential components used in various industries to isolate, cushion, and dampen vibrations and shocks. These versatile and practical devices provide mechanical support and reduce friction between two moving parts. This blog will explore the different types of rubber bushings, their wide-ranging uses, the manufacturing process, and the materials that make them suitable for diverse applications.
Rubber Bushings
Rubber bushings are cylindrical or sleeve-like components made of rubber or rubber-like materials. They typically have a hole through the center that allows inserting a shaft, bolt, or pivot. Rubber bushings provide a flexible and resilient connection between two components, allowing for controlled movement while reducing noise, vibrations, and wear.
Types of Rubber Bushings
- Bonded Rubber Bushings contain an inner metal sleeve encased in rubber. The rubber is bonded to the metal sleeve, enhancing the bushing’s durability and load-bearing capabilities.
- Conical Rubber Bushings are shaped like cones that handle angular movements and lateral forces. They are commonly used in suspension systems and steering components.
- Solid Rubber Bushings are made from a single piece of rubber and are simple in design. They provide excellent vibration isolation and are commonly used in automotive suspension systems and industrial machinery.
- Rubber-to-metal bonded Bushings combine the advantages of rubber’s resilience and metal’s strength. The rubber is connected to a metal shell or inner sleeve, offering increased load capacity and precise positioning.
- .Threaded Rubber Bushings have internal threads, which can be screwed onto a shaft or bolt. They are used for fastening and vibration isolation in various applications.
- Split Rubber Bushings have a slit or split design, allowing easy installation without disassembling the components. They are often used in automotive applications for suspension and engine mounts.
Rubber Bushings Use Cases
- Automotive Industry: Rubber bushings are extensively used in vehicles for suspension systems, engine mounts, shock absorbers, stabilizer bars, and control arms to dampen vibrations and improve ride comfort.
- Electronics and Appliances: Rubber bushings are used in electronics and appliances to dampen vibrations and reduce noise, enhancing performance and user experience.
- Aerospace and Aviation: In the aerospace industry, rubber bushings are utilized in aircraft landing gear, engine mounts, and other critical components to absorb shocks and vibrations.
- Industrial Machinery: Rubber bushings are employed in industrial machinery and equipment to reduce noise, vibrations, and friction, extending the lifespan of moving parts and ensuring smooth operation.
- Marine Applications: Rubber bushings find application in marine equipment and vessels to minimize vibrations and prevent metal-to-metal contact in harsh marine environments.
- Construction and Infrastructure: In construction, rubber bushings are used in building foundations, bridges, and infrastructure to isolate vibrations and provide flexible connections.
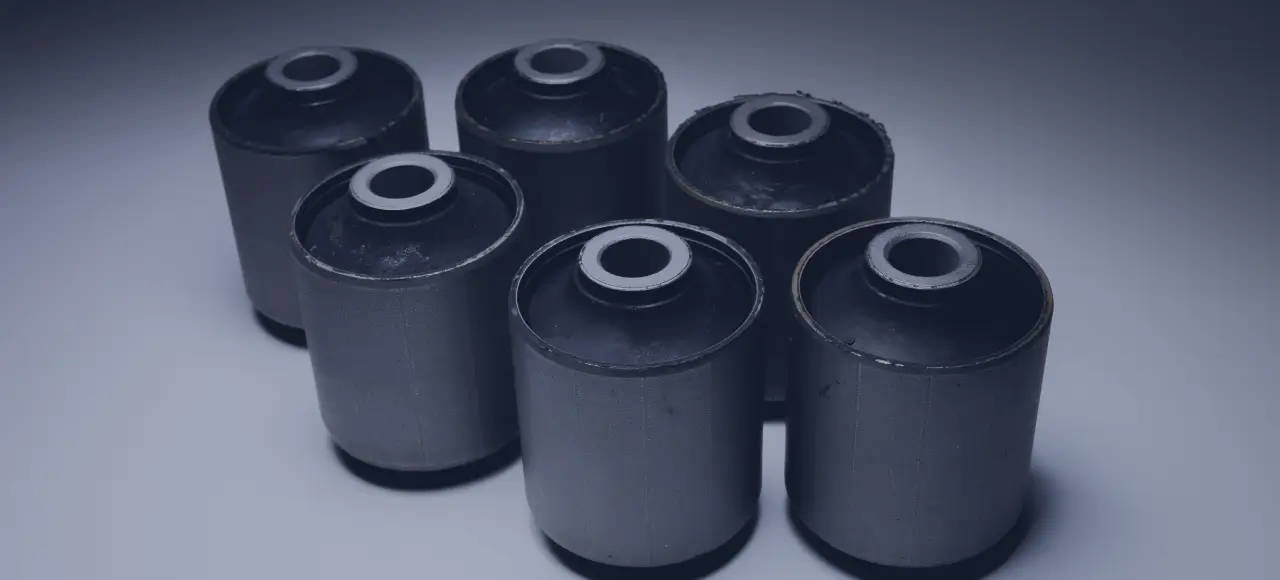
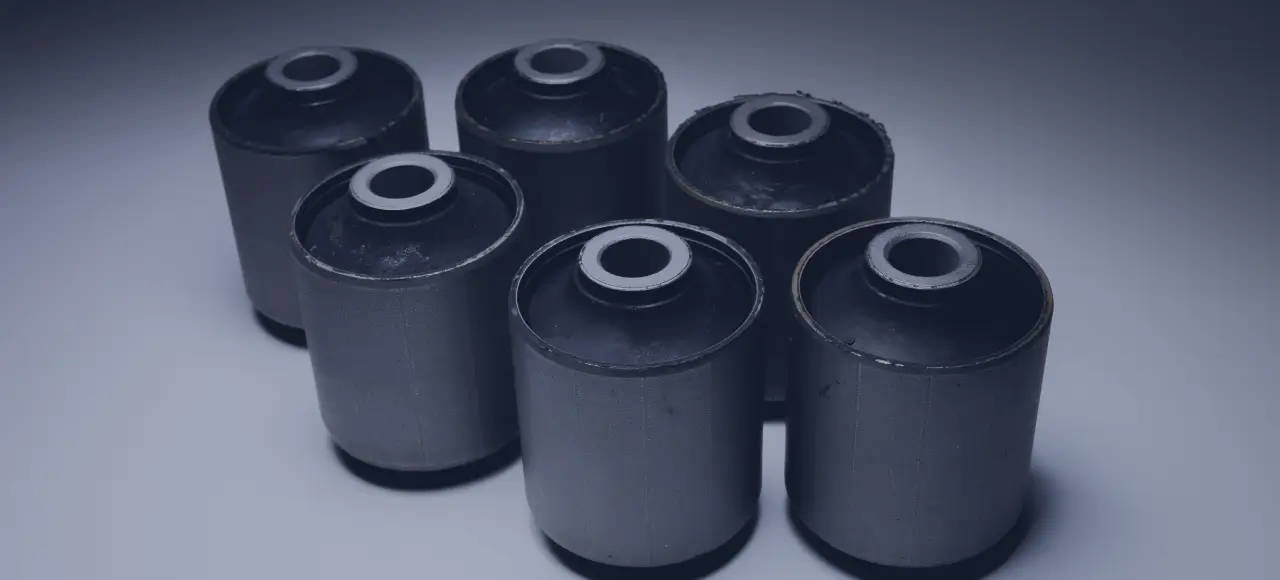
Manufacturing Process of Rubber Bushings
- Bonding Process: In the case of bonded and rubber-to-metal bonded bushings, the rubber is related to the metal using adhesives and curing processes.
- Finishing: The rubber bushings are trimmed, inspected for quality, and any necessary finishing touches are applied.
- Rubber Material Selection: The appropriate rubber compound is selected based on the desired properties, such as hardness, resilience, temperature, and chemical resistance.
- Metal Preparation: The metal sleeves or shells are prepared for bonded and rubber-to-metal bonded bushings, and their surfaces are treated to ensure strong adhesion to the rubber.
- Molding: The rubber material is molded into the desired shape using compression, injection, or transfer molding techniques.
Materials Used in Rubber Bushings
- Natural Rubber (NR): Natural rubber offers excellent resilience and flexibility, making it suitable for various applications. However, it may not provide the best resistance to temperature extremes and chemicals.
- Synthetic Rubber (SBR, NBR, EPDM): Synthetic rubbers like Styrene-Butadiene Rubber (SBR), Nitrile Rubber (NBR), and Ethylene Propylene Diene Monomer (EPDM) offer specific properties, such as oil resistance, chemical resistance, and weather resistance, making them ideal for diverse applications.
- Polyurethane (PU): Polyurethane rubber provides high abrasion resistance and is commonly used in heavy-duty applications.
- Silicone Rubber: Silicone rubber is known for its high-temperature resistance and is used in applications requiring extreme heat exposure.
- Fluorocarbon Rubber (FKM/Viton): Fluorocarbon rubber exhibits exceptional resistance to chemicals and high temperatures, making it suitable for demanding environments.
Bushings By Size
Rubber bushings come in various sizes to accommodate shaft diameters or bolt sizes. The size of a rubber bushing is typically described using two main dimensions: the inner diameter (ID) and the outer diameter (OD). Additionally, the length or height of the bushing may also be specified. For example, a rubber bushing size might be described as “ID x OD x Length.” Here’s what each dimension represents:
- Inner Diameter (ID): This is the measurement of the hole’s diameter through the center of the rubber bushing. It corresponds to the size of the shaft or bolt that the bushing is designed to fit around.
- Outer Diameter (OD): This measures the bushing’s outer circumference. It corresponds to the size of the hole or space in the mounting structure where the bushing will be inserted.
- Length: This refers to the height or length of the rubber bushing from one end to the other.
For example, a standard rubber bushing size used in automotive applications might be “12mm x 24mm x 30mm.” This means the bushing has an inner diameter of 12mm, an outer diameter of 24mm, and a length of 30mm.
It is essential to select the right size of rubber bushings to ensure a secure and proper fit for the intended application. When replacing rubber bushings, it is crucial to match the dimensions precisely to the original bushings or follow the manufacturer’s specifications to maintain the proper function and performance of the system.
In conclusion, rubber bushings are vital in providing mechanical support, vibration isolation, and flexibility across various industries. Their significance in enhancing the performance, safety, and durability of automotive, industrial, electronic, and aerospace systems cannot be understated. As technology and materials progress, rubber bushings are poised to evolve further, presenting increasingly effective and tailored solutions for diverse industrial applications.




FAQs
Rubber bushings in automotive suspension systems absorb shocks and vibrations from uneven road surfaces, providing occupants with a smoother and more comfortable ride.
Due to their excellent heat resistance properties, silicone and fluorocarbon rubber (FKM/Viton) are suitable for high-temperature applications.
Rubber bushings are employed in heavy-duty industrial machinery to reduce vibrations, noise, and wear between moving parts.
Consider factors such as the type of application, load capacity, temperature range, chemical resistance, and required vibration isolation when selecting the appropriate rubber bushing
Some rubber materials may have environmental considerations, such as recycling or disposal. Check with manufacturers or local regulations for proper handling of used rubber bushing.