While it’s true that logistics in the supply chain are continuously improving, it’s also true that the pandemic has generated setbacks that most major manufacturers weren’t acclimated to. To combat issues like industry fragmentation, diminished visibility, and convoluted logistics, manufacturers need to step up their efforts in the coming years. Adding to that is the consumers’ increasing purchasing power, which has put more pressure on companies to produce high-quality products at reasonable rates. This blog explores some recent supply chain challenges surfacing for the manufacturers, their overall implications, and practical solutions to overcome them. Let’s dig deeper.
Know About Recent Supply Chain Challenges for Manufacturers : Impacts and Solutions
Prominent Supply Chain Challenges Faced By The Manufactures
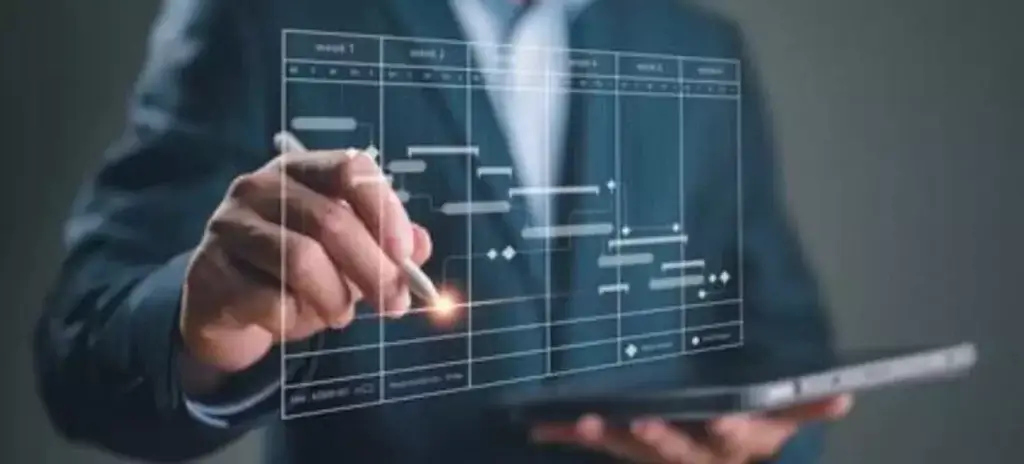
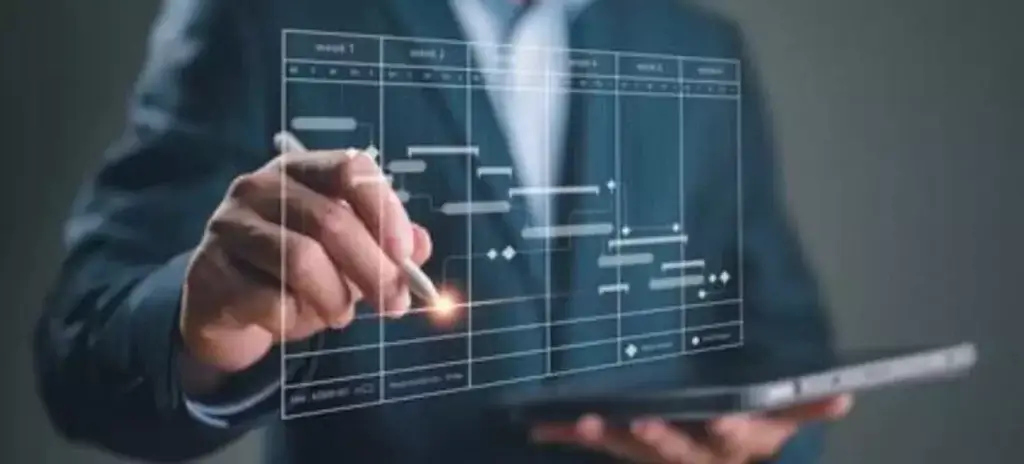
1. Increasing Material & Operational Costs
The present supply chain problem can potentially impact the bottom lines of some manufacturing companies severely. Due to the rising material and operational costs, some may even experience negative quarterly results. First, there has been a rise in material costs due to rising demand for particular suppliers like semiconductors and continued inflation concerns. Manufacturers can increase prices to cover part of these costs, but there is a risk that they will price themselves out of the market. The second factor contributing to the rising cost of production is the lengthened duration of the production cycle and the accompanying rise in labour costs. It might not seem like much, but at a time when businesses are trying to keep expenses down, it can be a significant challenge to implement. Last but not least, gas prices have gone up massively as a result of the ongoing global socio-political scenario. Consequently, an increase in gas prices will raise outbound and inbound transportation expenses for manufacturers.
2. Elongated Production Times
Significantly longer production times are expensive and inconvenient for manufacturers due to supply chain disruptions. Production may need to be suspended until enterprises can guarantee access to the raw materials required. The incapacity of manufacturers to foresee their own needs is contributing to the situation.Ideally, manufacturers must figure out precisely what machinery/equipment & raw materials they will need and how soon they’ll need them to keep production running smoothly. For instance, considering a CNC production facility, the procurement team must know how many Desktop CNC Mill machines need to be operational and the volume of raw materials, like steel, brass, copper, etc., required to meet production demands. The business may struggle to procure the requisite materials at reasonable prices if it lacks these insights. Furthermore, customers’ preferences and requirements are evolving at a remarkable rate, making it challenging for businesses to stay up. Manufacturers who still use conventional spreadsheets & tools to conduct their supply chain networks and operations may struggle to provide an accurate estimate of future demand. Eventually, it’s a good sign that supply chain technology has come a long way in the last several years. A manufacturer’s capacity for demand forecasting and supply chain management could be enhanced substantially with contemporary tech solutions available today.
3. Embracing Digital Transformation
The Industrial Internet of Things (IIoT) and digital transformation can have mixed impacts on supply chain operations. However, some technologies, such as artificial intelligence and industrial robotics, have the potential to enhance the way you tackle the conventional supply chain. Even though these systems & services are meant to make manufacturing processes more streamlined, efficient, and cost-effective in the long term, the issue lies in adopting them across an organization’s existing supply chain activities. Especially when dealing with several production facilities, putting these technologies into operation requires time and organizational reconfiguration. Despite this, supply networks need to change frequently to keep up with the market.





Solutions to Prominent Manufacturing Supply Chain Challenges
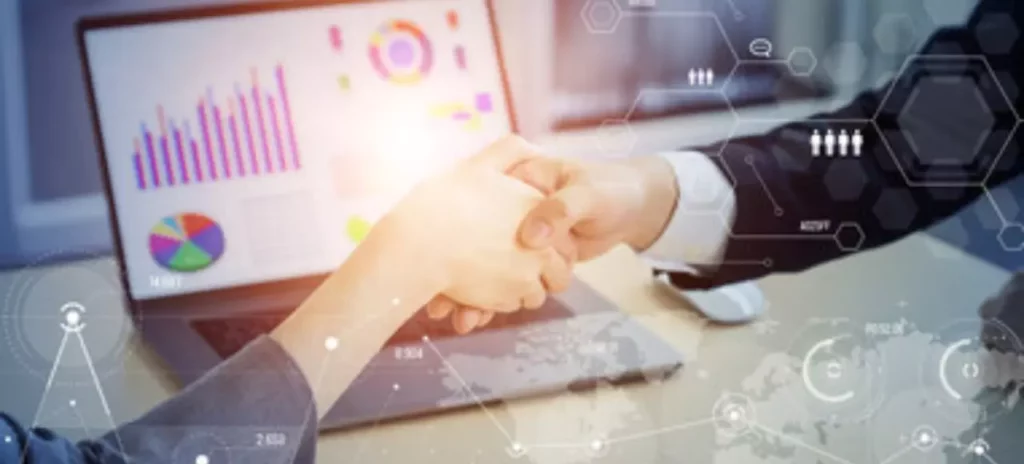
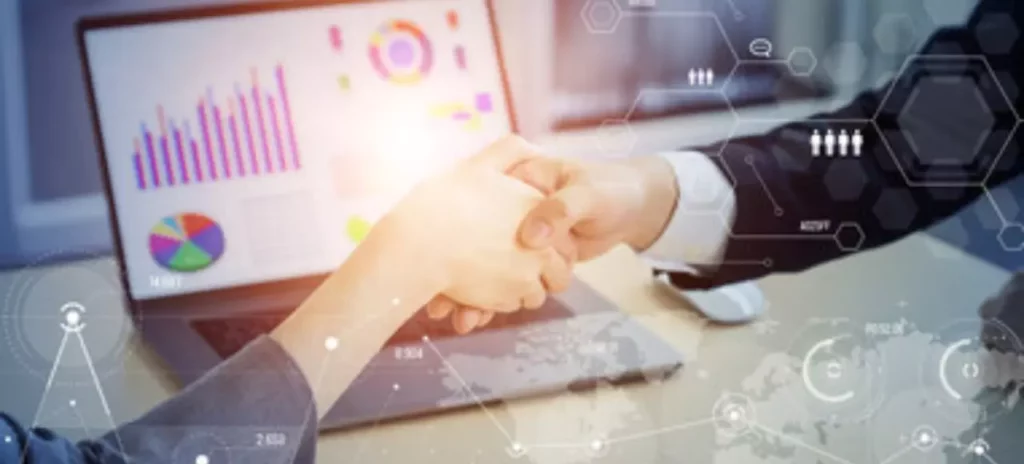
1. Work Towards Effective Supplier Relationship Management
Establishing a good rapport with your suppliers can help you avoid problems like manufacturing delays and waste, as well as improve your capacity to negotiate lower procurement rates. To improve your relationships with your suppliers, consider these strategies:
- Convey restocking demand early- If you see an uptick in demand for a certain product, alerting your suppliers as soon as possible can give them time to boost production and stockpiles.
- Open communication– When you and your supplier can communicate openly and transparently, you can work together to find solutions more quickly, which will lessen the impact of any disruptions and deepen your relationship.
- Be disciplined with payments– Build trust and reliability by always paying on time and never missing a payment.
2. Focus On Building A Diversified Network
If the COVID-19 pandemic highlighted any flaws in the supply chain, it was the unavailability of alternative supply chain networks. Due to the closure of borders, manufacturers who had relied significantly on both international and domestic suppliers were unable to continue operations. But in the current economic landscape, 90% of the manufacturers are dedicated to creating a diversified supplier network that encompasses regional and local suppliers to avoid these issues from recurring.
3. Emphasize Workforce Training
An uptick in the adoption of digital supply chain management tools necessitates a rise in the demand for personnel with the necessary expertise to operate them. It may be difficult for businesses to find this kind of expertise through traditional hiring channels. Several businesses in the manufacturing sector are responding to this challenge by providing their present employees with the technical training they will need in the future. For instance, those who have worked with inventory management programs and warehouse management systems are in great demand. Besides hard skills like data analysis, employers value applicants who can demonstrate a curiosity for new knowledge by displaying abilities like critical thinking and flexibility.
Manufacturing businesses of all sizes have had to rethink their operational strategies in recent years to reinvigorate profits and keep customers. Despite the global economic crisis and supply and demand issues, many mainstream companies are strengthening their ability to withstand disruptions and mending internal cracks through the SCM transition.




