The world of component manufacturing has witnessed significant advancements in recent years, particularly in automobile casting. As industries evolve, the demand for precision, durability, and efficiency in manufacturing processes has never been higher. This article delves deep into the innovations in automobile casting, highlighting the role of automobile casting components in shaping the future of the automotive industry.
The Evolution of Automobile Casting
Historically, automobile casting was a manual and labor-intensive process. However, the process has undergone a radical transformation with the advent of technology and the need for more intricate designs. Today, advanced machinery and computer-aided design (CAD) tools have revolutionized component manufacturing, allowing for more complex and precise castings.
The Significance of Automobile Casting Components
Automobile casting components play a pivotal role in the automotive industry. These components, made through the casting process, form the backbone of vehicles. Casting ensures each piece is tailor-made to fit its purpose, from engine parts to body frames. The precision and durability of these components are paramount, as they directly influence the performance and longevity of the vehicle.
Technological Advancements in Component Manufacturing
The rise of Industry 4.0 has brought about a slew of innovations in component manufacturing. Some of these include:
- 3D Printing: This allows manufacturers to create complex geometries that were previously impossible or expensive to produce. It also speeds up the prototyping process, enabling faster iterations and improvements.
- Smart Molds: Embedded with sensors, these molds provide real-time feedback during the casting process, ensuring optimal conditions and high-quality output.
- Automated Quality Control: Advanced imaging and AI algorithms can now detect microscopic defects in castings, ensuring that only the highest quality components make their way into automobiles.
The Role of Customization
In today’s competitive market, customization is key. Manufacturers constantly seek ways to differentiate products and meet specific customer needs. This is where the flexibility of automobile casting components shines. Manufacturers can produce parts tailored to particular requirements through advanced component manufacturing techniques, ensuring a perfect fit and optimal performance.
The Integration of AI and Machine Learning
One of the most transformative innovations in component manufacturing is the integration of Artificial Intelligence and Machine Learning. These technologies are being harnessed to predict defects, optimize casting processes, and enhance the overall quality of automobile casting components.
- Predictive Maintenance: AI algorithms analyze data from machinery to predict when maintenance needs to be done, reducing downtime and ensuring continuous production.
- Quality Assurance: Machine learning models are trained on vast datasets to identify even the minutest defects in castings, ensuring that every component meets the highest standards.
- Process Optimization: AI can analyze countless variables in the casting process, from temperature to mold material, and recommend optimal conditions for each casting.
Advanced Materials in Casting
The choice of material plays an essential role in the casting process. With advancements in material science, new alloys and composites are being developed that offer superior strength, durability, and resistance to wear and tear. These materials enhance the performance of automobile casting components and extend their lifespan.
- High-Strength Aluminum Alloys: These alloys are lightweight yet offer strength comparable to steel, making them ideal for automotive applications where weight reduction is crucial.
- Magnesium Alloys: Magnesium alloys are becoming popular in the automotive industry because they are known for their excellent strength-to-weight ratio.
- Composite Materials: Combining two or more materials can offer the best of both worlds. For instance, carbon fiber-reinforced plastics provide strength and rigidity while remaining lightweight.
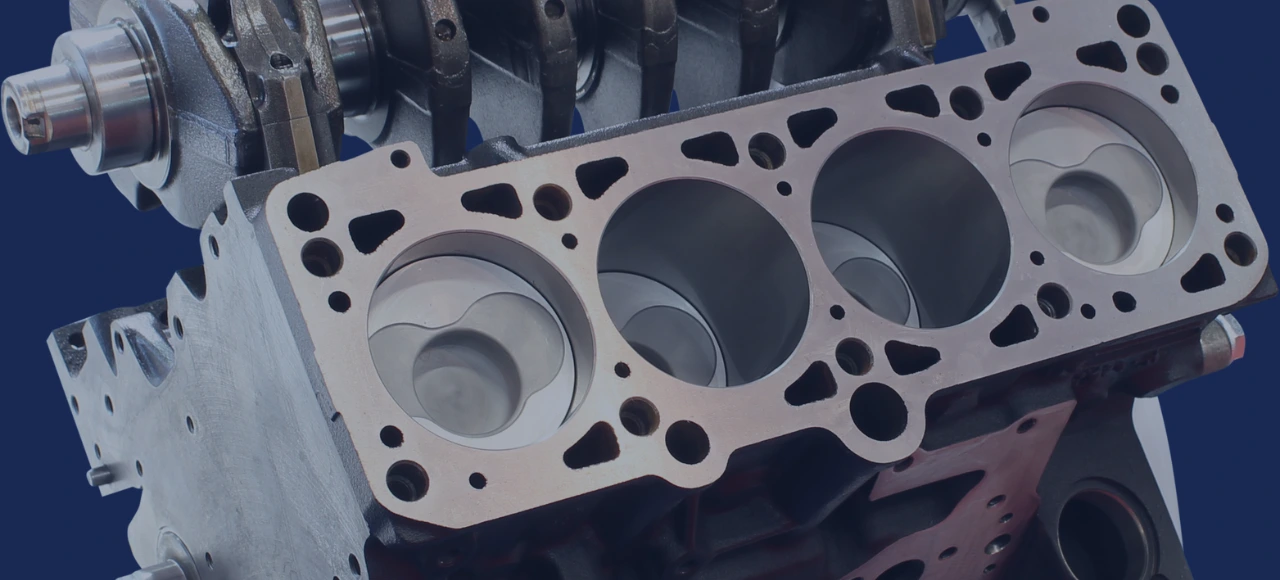
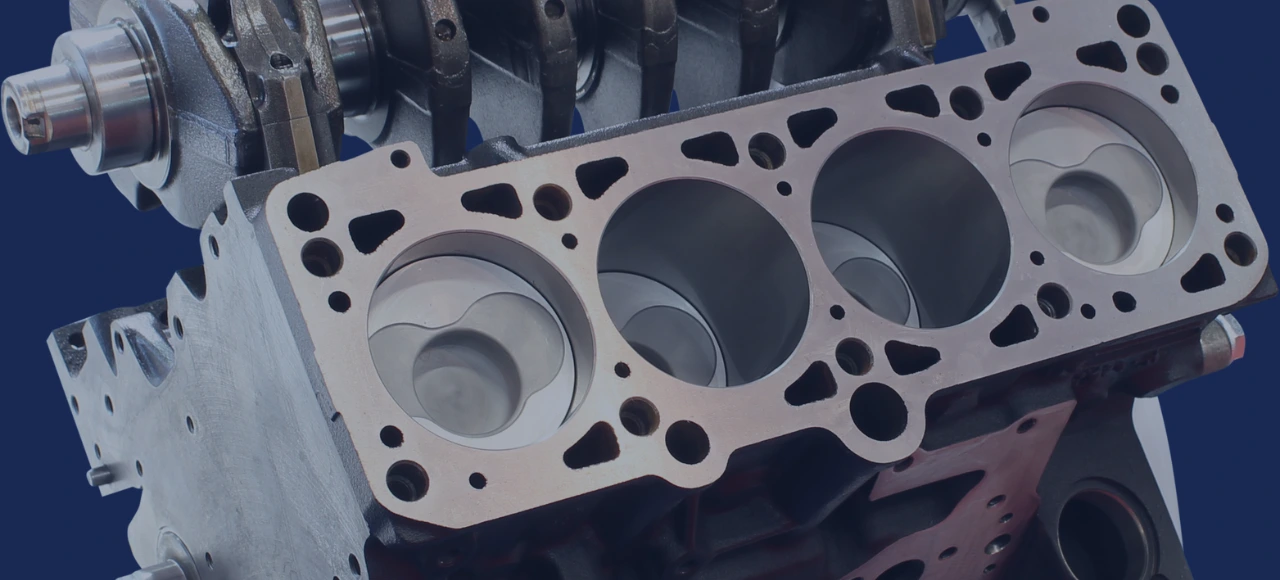
The Future of Automobile Casting
As the automotive industry continues to evolve, so will the techniques and technologies associated with component manufacturing. Integrating digital technologies, advanced materials, and a focus on customization will drive the industry forward. Manufacturers will continue to seek innovative solutions to meet the ever-growing demands of consumers and the challenges posed by a rapidly changing automotive landscape.
Challenges and Solutions in Modern Casting
While the advancements in component manufacturing are promising, they also bring forth new challenges that the industry must address:
- Complexity in Design: As vehicles become more advanced, the complexity of their components also increases. This demands more intricate casting molds and processes.
- Scalability: With the automotive market growing globally, manufacturers need to ensure that their casting processes can scale to meet the rising demand without compromising on quality.
- Cost Efficiency: Innovations often come with increased costs. Balancing the adoption of new technologies while maintaining cost efficiency is a challenge that manufacturers face.
However, the industry is already gearing up with solutions:
- Simulation Software: Before casting, simulation software can predict how the molten metal will flow, solidify, and cool. This helps in identifying and rectifying potential defects in the early stages.
- Robotic Automation: Robots with sensors can handle tasks like pouring molten metal, ensuring precision, and scaling the production rate.
- Recycling and Resource Optimization: To address cost concerns, many manufacturers are considering recycling cast metals and optimizing resource usage to reduce wastage.
Collaborative Efforts in the Industry
Collaboration is becoming a cornerstone in the world of automobile casting components. Manufacturers, researchers, and tech companies share knowledge, resources, and expertise. Such collaborative efforts are leading to:
- Standardization: Setting industry standards ensures that casting components are consistent in quality and performance across the board.
- Research and Development: Joint R&D initiatives are accelerating the discovery of new materials, processes, and technologies.
- Training and Skill Development: As the casting process becomes more advanced, there’s a need to upskill the workforce. Collaborative training programs ensure workers are equipped with the latest skills and knowledge.
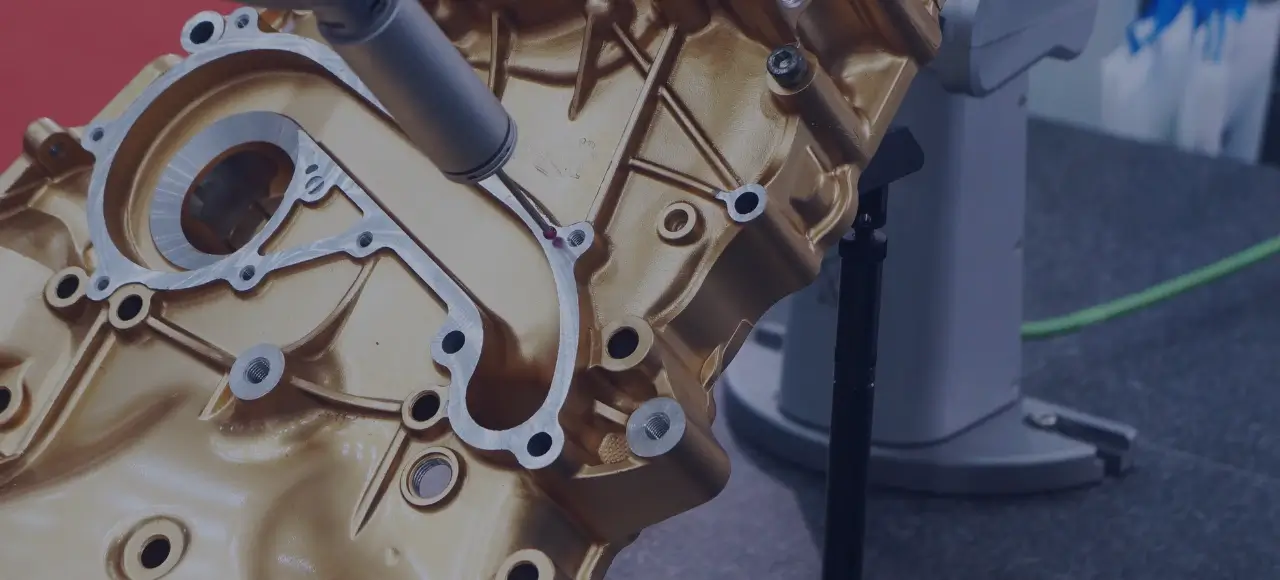
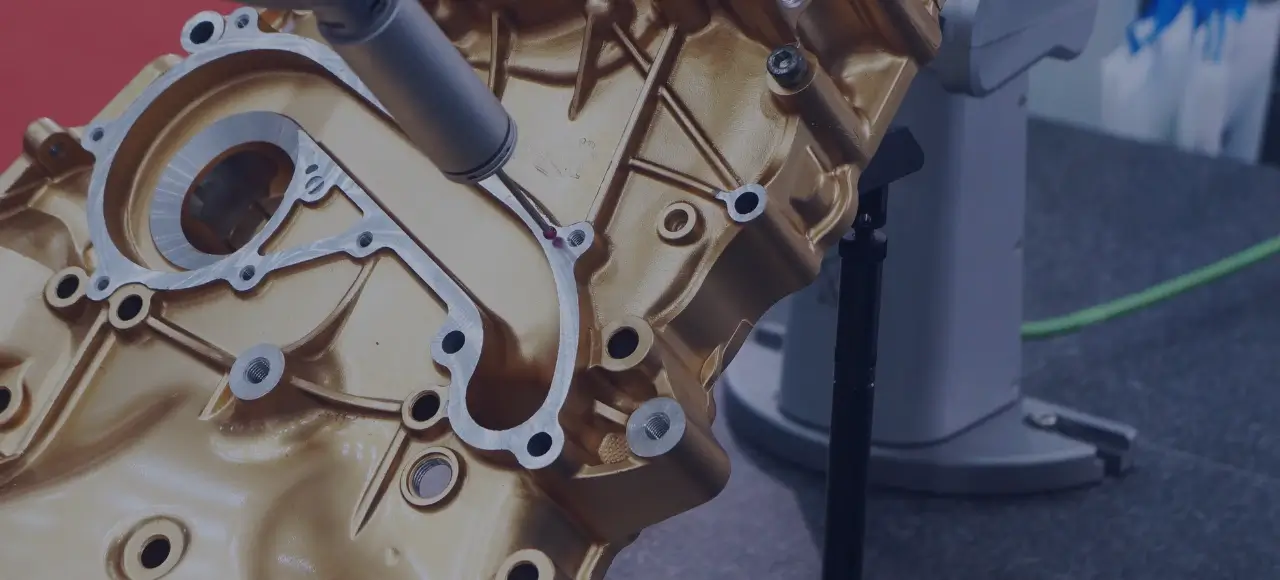
The Global Perspective on Automobile Casting
The automobile casting industry is not just a local or regional phenomenon; it’s a global endeavor. Different regions bring unique challenges and opportunities to the table:
- Emerging Markets: Countries like India, China, and Brazil rapidly grow their automotive sectors. This growth presents a massive demand for automobile casting components and an opportunity to set up advanced manufacturing hubs.
- Established Markets: Regions like North America and Europe, with their mature automotive industries, are pushing the boundaries of innovation. They are at the forefront of integrating AI, ML, and other digital technologies into component manufacturing.
- Supply Chain Dynamics: With globalization, the supply chain for automobile casting has become more intricate. Manufacturers are sourcing materials from one continent, processing them in another, and shipping the final products worldwide. This global supply chain demands meticulous planning, coordination, and quality control.
Safety and Quality Assurance In Casting
As vehicles become more advanced and integrated with technology, the safety and quality of every component, including those made through casting, become paramount.
Non-Destructive Testing (NDT)
Techniques like ultrasonic testing, radiographic testing, and magnetic particle inspection detect defects without damaging the component.
Certifications
Many manufacturers are now seeking international certifications like ISO/TS 16949, which sets the standard for quality management in the automotive industry.
Feedback Loops
Modern casting facilities integrate feedback mechanisms where post-production testing results are fed back into the design and manufacturing process, ensuring continuous improvement.
With stalwarts like Zetwerk, automobile casting has evolved from humble beginnings to embrace cutting-edge technologies and collaboration. As the industry navigates challenges, its commitment to innovation, safety, and quality remains unwavering. The road ahead promises continued excellence, with every cast component driving the future of automotive achievement.




FAQs
Automobile casting plays a crucial role in creating durable and precise components, forming the backbone of modern vehicles and ensuring optimal performance and longevity.
AI and ML have introduced predictive maintenance, quality assurance, and process optimization, ensuring precision and quality in automobile casting components.
Customization allows manufacturers to meet specific customer needs, differentiate their products, and ensure components fit perfectly, enhancing vehicle performance.
With emerging markets growing and established markets innovating, coupled with intricate global supply chains, the industry faces challenges and opportunities worldwide.
Zetwerk, with its expertise and commitment to excellence, stands as a leading figure in the industry, driving innovation and ensuring quality in automobile casting.