Transforming a mere design into a tangible product is nothing short of a marvel in component manufacturing. Especially when it comes to custom plastic parts manufacturing, the journey is intricate, demanding precision at every step. This article delves deep into the process, shedding light on the technicalities and the expertise required to bring a design to life.
The Genesis: Understanding the Design
Every product starts with a concept. Custom plastic parts manufacturing means a detailed design outlining the desired component’s specifications, dimensions, and functionalities. Engineers and designers collaborate to ensure the design is feasible, cost-effective, and meets the intended purpose.
Material Selection: The Backbone of Quality
Choosing a suitable material is paramount. Different plastics have varying properties, and the choice directly impacts the final product’s durability, flexibility, and functionality. Whether it’s polycarbonate for its toughness or polyethylene for its versatility, the material selection plays a pivotal role in component manufacturing.
Advanced Materials in Component Manufacturing
The world of component manufacturing is not static. As industries evolve, so do the materials used in custom plastic parts manufacturing. Advanced polymers and composites are being developed to cater to specific needs. For instance, thermally conductive plastics are now being used in electronic applications, while high-strength, lightweight composites find their place in the aerospace and automotive sectors.
Molding Techniques
Custom plastic parts manufacturing begins once the design is set and materials are chosen. There are several molding techniques available:
- Injection Molding: Ideal for producing high volumes of plastic parts, this method involves injecting molten plastic into a mold. Once cooled, the mold is opened to release the part.
- Blow Molding: Used primarily for creating hollow objects like bottles, this method involves blowing air into a heated plastic tube, forcing it to expand into the shape of the mold.
- Rotational Molding: Perfect for large, hollow parts, this method rotates the mold as the plastic is introduced, ensuring an even coating inside.
Significance of Prototyping
Before mass production begins, prototyping is crucial in custom plastic parts manufacturing. It allows manufacturers to create a tangible model of the final product. This prototype serves multiple purposes:
- Design Verification: Ensures the design is accurate and functional.
- Material Testing: Allows manufacturers to test different materials and choose the best fit.
- Cost Estimation: Provides a clearer picture of the production costs.
Prototyping reduces risks and ensures that the final product meets the client’s expectations.
Sustainability in Component Manufacturing
With growing environmental concerns, sustainability has become a focal point in component manufacturing. Manufacturers are now leaning towards eco-friendly materials and processes. Bioplastics, made from renewable resources like sugarcane or corn starch, are gaining traction. These materials decompose faster than conventional plastics, reducing environmental impact.
Customization: Meeting Diverse Needs
The beauty of custom plastic parts manufacturing lies in its adaptability. Whether it’s a specific color, texture, or functionality, customization allows manufacturers to cater to diverse industry needs. From automotive parts to medical equipment, the applications are vast and varied.
Challenges in Component Manufacturing
While the industry has seen exponential growth, it’s not without challenges:
- Material Shortages: With the increasing demand for specific plastics, sourcing can become challenging.
- Technological Adaptability: As technology evolves, manufacturers must constantly upgrade to stay competitive.
- Quality Consistency: Ensuring consistent quality across large batches can be daunting.
However, with challenges come opportunities. Innovations and advancements are continually shaping the future of component manufacturing.
Quality Control: Ensuring Precision and Consistency
In the space of component manufacturing, there’s no room for error. Each part must adhere to the strictest quality standards. This involves rigorous testing for strength, durability, and functionality. Advanced machinery and expert technicians ensure that every custom plastic part meets the desired specifications.
The Final Touches: Assembly and Finishing
Once the parts are molded and quality-checked, they often undergo additional processes like painting, assembly, or the addition of other components. These final touches are crucial in ensuring that the product functions as intended and looks the part.
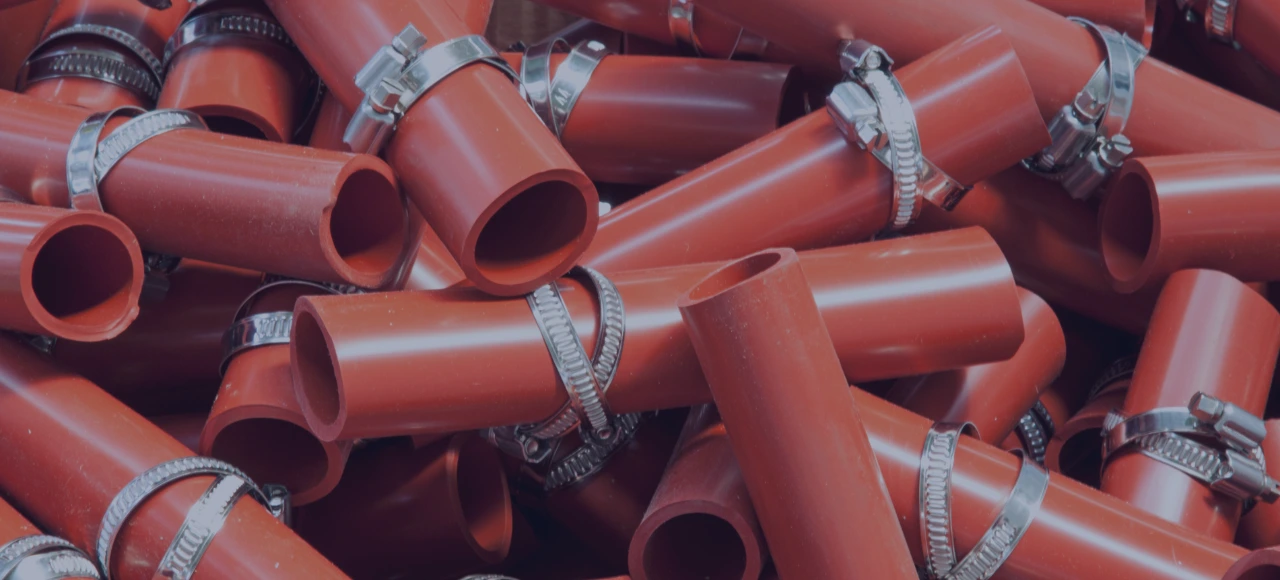
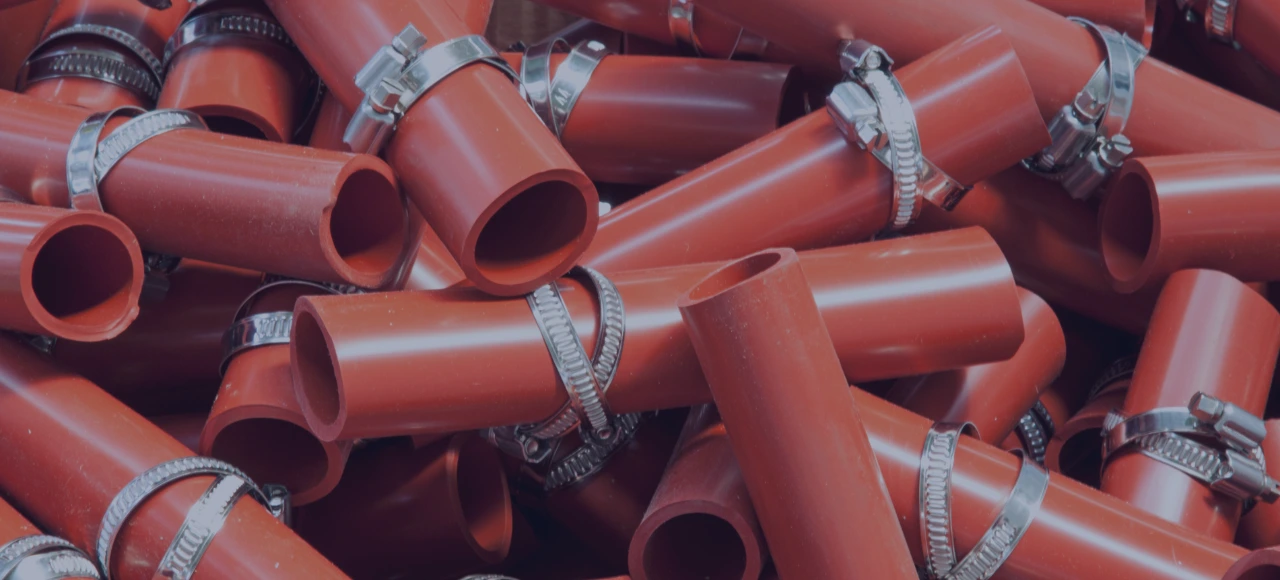
Global Supply Chain Considerations
In today’s globalized world, component manufacturing is not just about producing a part; it’s about ensuring that part can be produced consistently, at scale, and delivered anywhere in the world. This brings into play considerations like:
- Logistics: Efficiently moving materials and finished products.
- Regulations: Complying with international standards and regulations.
- Localization: Adapting products to local market needs.
The Role of Technology in Manufacturing
Modern component manufacturing heavily relies on technology. From computer-aided design (CAD) software to automate the design process to robotics in the assembly line, technology ensures efficiency, precision, and scalability in custom plastic parts manufacturing. Automation, including robotic arms and CNC machines, has been a game-changer. These advancements not only increase production speeds but also ensure unparalleled precision. Robotics, in particular, allows intricate designs to be executed flawlessly, reducing human error and increasing consistency.
The Evolution of Custom Plastic Parts Manufacturing
Over the years, the component manufacturing industry has seen significant advancements. The evolution of custom plastic parts manufacturing is a testament to the industry’s adaptability and innovation. The journey has been transformative, from rudimentary hand-casting methods to sophisticated automated machinery.
The Future: What Lies Ahead?
The future of custom plastic parts manufacturing is promising. With the advent of 3D printing, manufacturers can now quickly produce complex designs. Smart manufacturing, powered by the (IoT), is set to revolutionize the industry. Real-time data collection and analysis will lead to more efficient and streamlined production processes.
The Importance of Research and Development (R&D)
Innovation is the lifeblood of custom plastic parts manufacturing. R&D departments are pivotal in pushing the boundaries of what’s possible. From developing new materials to pioneering production techniques, R&D ensures that a company stays at the cutting edge of the industry.
Training and Skill Development
As technology and techniques evolve, so must the skills of the workforce. Continuous training programs, workshops, and certifications ensure employees can handle the latest machinery, software, and production methodologies. This not only ensures quality but also boosts productivity.
The Synergy of Collaboration and Innovation
- Collaboration and innovation are twin pillars in the vast landscape of component manufacturing. The journey from design to product is a collaborative endeavor. It involves the collective efforts of designers, engineers, technicians, and even end-users. Feedback loops, iterative design processes, and cross-departmental collaborations ensure the final product is innovative and functional.
- This synergy is especially evident in custom plastic parts manufacturing, where the rapid pace of technological advancements demands a culture of continuous learning and adaptation. By fostering an environment of collaboration, manufacturers can harness their teams’ collective intelligence and creativity, leading to breakthrough innovations and refined designs.
Final Thoughts!
The custom plastic parts manufacturing journey is a testament to technological advancement and meticulous craftsmanship. With the industry’s rapid evolution, adaptability and precision become increasingly crucial. As we navigate this dynamic landscape,
FAQs
The process begins with understanding the design. A detailed design outlines the desired component’s specifications, dimensions, and functionalities. Engineers and designers collaborate to ensure feasibility and cost-effectiveness.
Material selection is crucial. Different plastics have unique properties that impact the final product’s durability, flexibility, and functionality. The choice can range from polycarbonate for toughness to polyethylene for versatility.
Several molding techniques include Injection Molding for high volumes, Blow Molding for hollow objects like bottles, and Rotational Molding for large, hollow parts.
Prototyping allows manufacturers to create a tangible model of the final product. It serves purposes like design verification, material testing, and cost estimation, ensuring the final product meets client expectations.
Zetwerk stands out as a beacon of excellence in the industry. With a commitment to innovation, technological advancement, and meticulous craftsmanship, they set the benchmark for quality and precision in manufacturing.