Fitting flanges have become a fundamental component in the world of piping systems, playing a crucial role in ensuring seamless connections and reliable operations. With the evolution of integrated fitting solutions, these flanges have taken center stage, offering a comprehensive approach that optimizes system performance while minimizing time. From their pivotal role in various industries to their advancements driving efficiency and safety, this blog highlights the significance of fitting flanges and how integrated solutions reshape piping system design, installation, and maintenance. Let’s get started!
Fitting Flanges: The Crucial Component in Piping Systems
Fitting flanges are the main component of piping systems, silently playing a crucial role in ensuring seamless connections and efficient operations. These unassuming components act as the linchpin that combines various parts of a piping system, creating a robust and reliable network for transporting fluids, gases, and other materials.
What are Fitting Flanges?
A fitting flange is a collar or ring attached to the end of a pipe, valve, or equipment. It features a flat or raised surface with bolt holes, which can be securely fastened to another flange or fitting, forming a tight and leak-resistant connection. The fitting flange‘s design and structure allow for easy disassembly and reassembly of components, making it a versatile and efficient solution for joining pipes and equipment in various applications.
Techniques and Processes: Fitting flanges are created through several metalworking techniques. The most common processes include forging, casting, and fabrication. Forging involves shaping metal under high pressure, resulting in robust and durable flanges. On the other hand, casting uses molds to create flanges with intricate designs. Fabrication is employed for bespoke flanges, where pieces are cut and welded together to form the final product.
Significance of Fitting Flanges in Piping Systems
Fitting flanges serve as the backbone of piping systems, providing a host of benefits that are crucial for their successful operation:
- Secure Connections: The primary function of a fitting flange is to create a secure and reliable connection between different parts of a piping system. This ensures that fluids or gases flow smoothly without any leakages or interruptions.
- Flexibility and Versatility: Fitting flanges are available in various sizes, materials, and types, making them adaptable to different environments and project requirements. This versatility allows for the customization of piping systems to suit specific needs.
- Pressure and Temperature Resistance: Depending on the material used, fitting flanges can withstand high-pressure and high-temperature conditions, making them suitable for various industrial applications.
Types of Fitting Flanges
Fitting flanges come in various types, each designed to meet specific needs and requirements in piping systems. The main types of fitting flanges include:
- Threaded Flanges: Threaded flanges have internal threads that match the external threads on the pipe. This type is used for low-pressure applications and is particularly useful in pipes that must be dismantled and reassembled frequently.
- Socket Weld Flanges (SW): Socket weld flanges have a socket (recess) in which the pipe end fits, and the connection is made by fillet welding. They are suitable for small-diameter pipes and are widely used in industries where flow integrity is essential.
- Lap Joint Flanges (LJ): Lap joint flanges consist of a flat ring with bolt holes (similar to a blind flange) and a loose backing flange. They allow for easy alignment of the bolt holes during installation and are often used in systems where frequent dismantling is required.
- Weld Neck Flanges (WN): Weld neck flanges are the most commonly used type. They have a long, tapered neck butt-welded to the pipe, providing a strong and permanent connection. The smooth transition from the flange to the pipe minimizes turbulence and erosion, making weld neck flanges suitable for high-pressure and high-temperature applications.
- Orifice Flanges: Orifice flanges have a small opening called an orifice, which allows for flow measurement or injection of chemicals into the pipeline. They are typically used in flow measurement applications and for controlling fluid flow rates.
- Slip-On Flanges (SO): Slip-on flanges slide over the pipe and are then welded in place. They are easy to align and install, making them popular for low-pressure applications. Slip-on flanges are not ideal for high-pressure systems as the welding could be a potential weak point.
- Blind Flanges (BL): Blind flanges are solid discs that seal the end of a piping system. They are commonly used when future expansion of the pipeline is expected. Blind flanges also allow for easy inspection, cleaning, and maintenance.
- Expander Flanges: Expander flanges increase the pipe size at the connection. They are helpful when there is a need to transition from a smaller to a larger pipe.
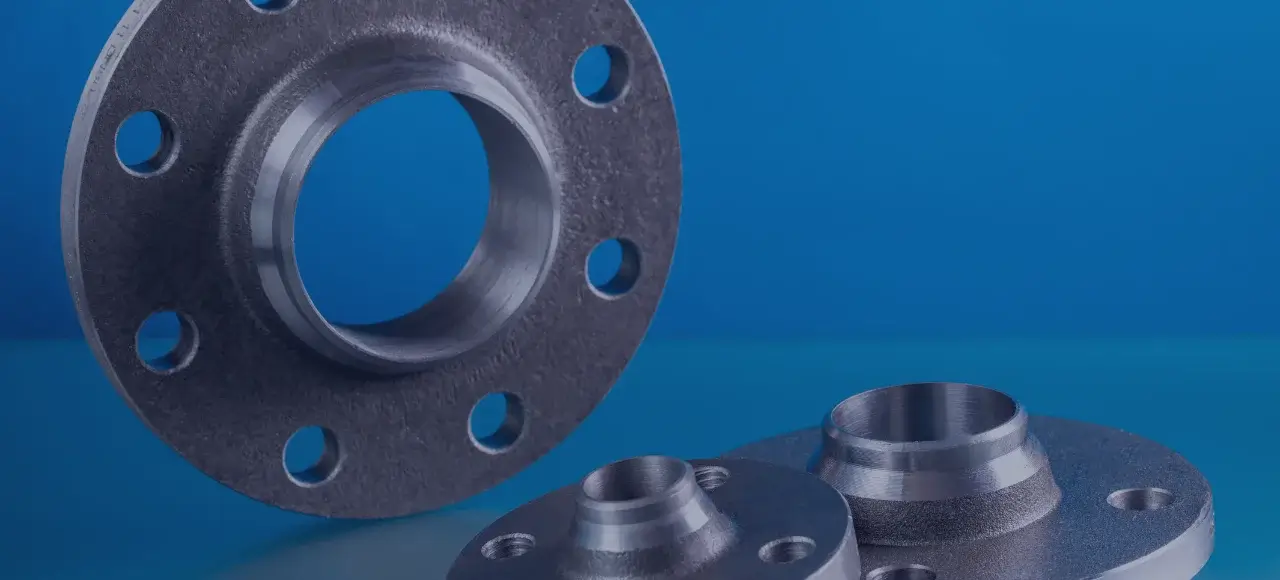
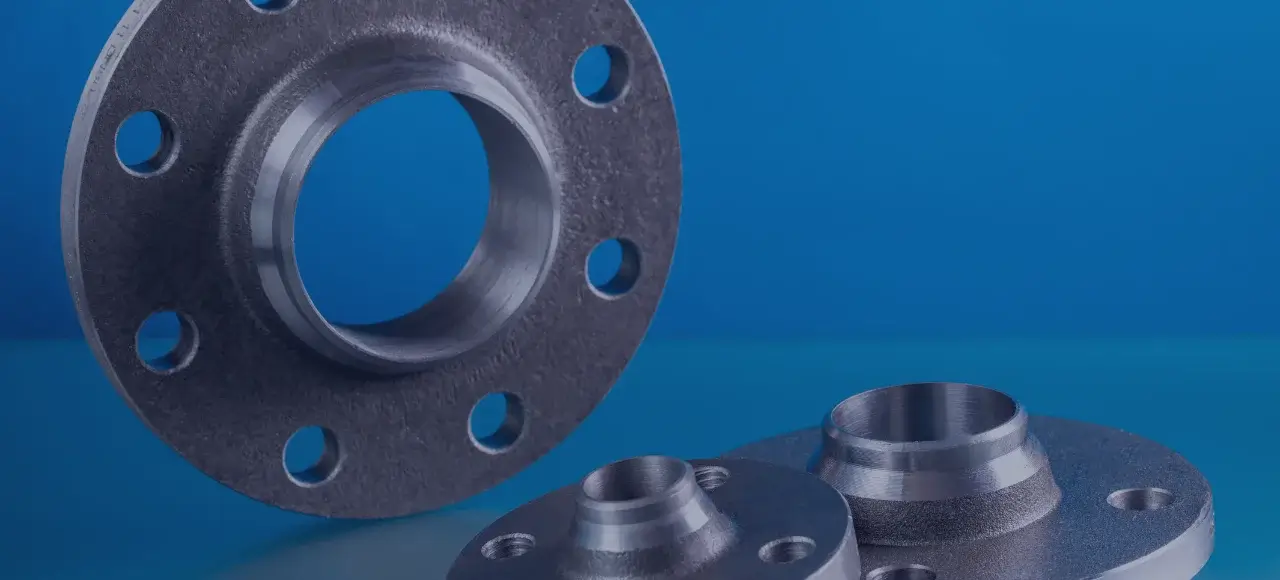
Applications of Integrated Flange and Fitting Solutions
Integrated flange and fitting solutions find applications across various industries and projects:
- In industrial settings, such as oil refineries, chemical plants, and power generation facilities, integrated solutions ensure the safe and efficient transport of fluids and gases.
- In commercial buildings, integrated solutions contribute to reliable HVAC systems, water distribution networks, and fire protection systems.
- In residential projects, integrated solutions provide dependable plumbing systems, ensuring consistent water supply and drainage.
Industrial Significance of Fitting Flanges
Fitting flanges hold immense industrial significance in various ways, making them a crucial component in piping systems. Their importance lies in the following aspects:
Secure and Leak-Free Connections
Fitting flanges provide a secure and leak-free connection between pipes, ensuring the integrity of the entire piping system. This is particularly critical in industries dealing with hazardous materials or sensitive processes where even a small leak can have severe consequences.
Flexibility and Versatility
With a wide range of types and sizes, fitting flanges offer flexibility and versatility in designing and configuring piping systems. They can accommodate different pipe sizes, materials, and orientations, making them suitable for diverse industrial applications.
Ease of Installation and Maintenance
Fitting flanges simplify installation and maintenance procedures. Their design allows for easy assembly and disassembly, which reduces downtime during repairs or system modifications, leading to cost savings.
Reduction of Stress Concentration
Fitting flanges distribute stress evenly across the connection, reducing stress concentration at specific points. This contributes to the system’s overall structural stability and extends the pipes’ lifespan.
Compatibility with Various Materials
Fitting flanges are compatible with various materials, including metals, plastics, and composites. This versatility enables their use in various industries with different material requirements.
High-Pressure and High-Temperature Applications
Certain fitting flanges, such as weld neck flanges, are designed to withstand high pressures and temperatures, making them suitable for power generation, petrochemicals, and other industries with demanding operating conditions.
Customization and Specialized Designs
The manufacturing processes for fitting flanges allow for customization and specialized designs. Engineers can tailor flanges to specific project requirements, ensuring optimal performance and safety.
Smooth Fluid Flow
Well-designed fitting flanges contribute to smoother fluid flow within the piping system, reducing pressure drop and minimizing energy losses during transportation.
Compliance with Industry Standards
Fitting flanges are manufactured according to industry standards and specifications, ensuring they meet safety and performance requirements in various industrial sectors.
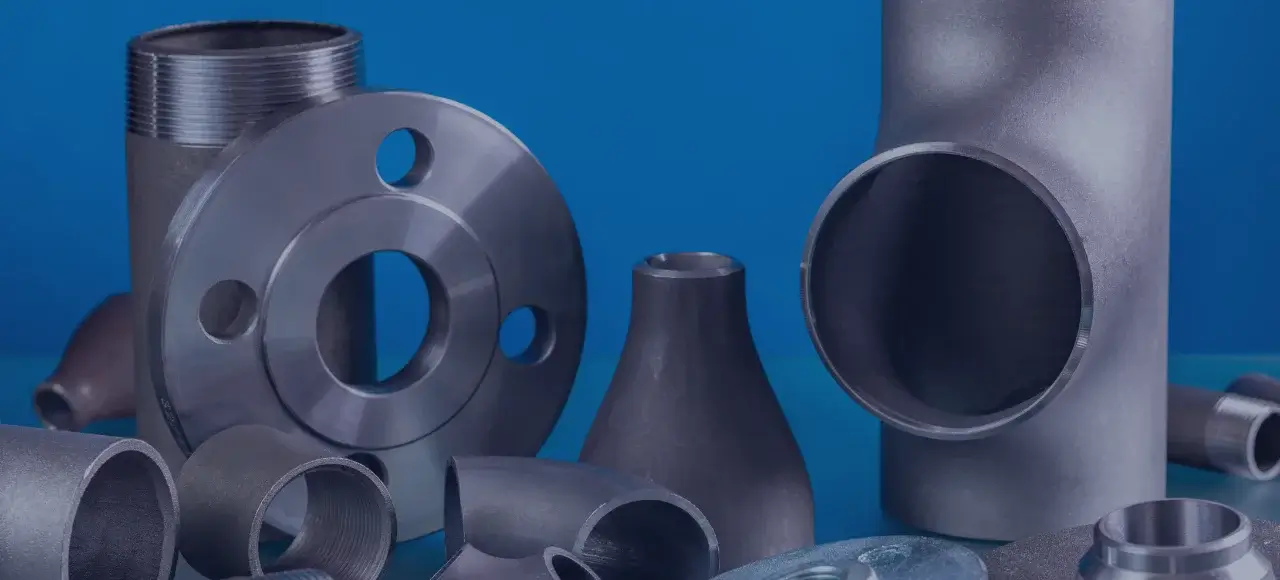
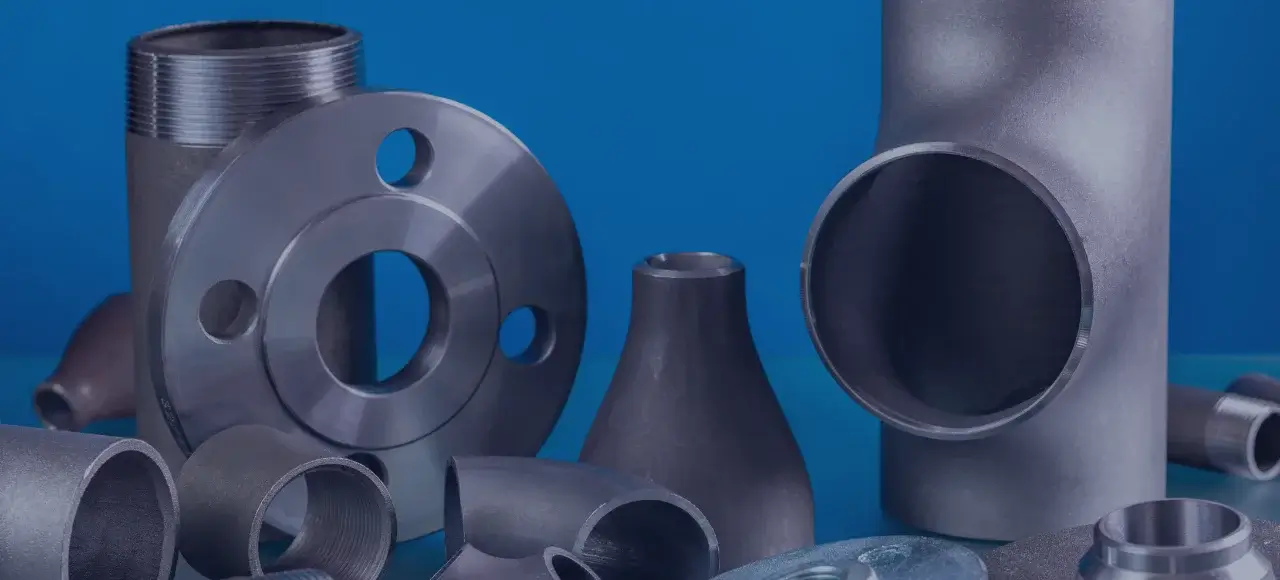
Choosing the Right Fitting Flange: Factors to Consider
When choosing the right fitting flange, there are several factors to consider, such as pressure, temperature, pipe size, and the requirements of the piping system. Each flange type offers unique advantages, and selecting the appropriate one can ensure a secure and efficient connection, reducing the potential for leakage and promoting the smooth operation of the piping system.
Material Compatibility
Different materials, such as chemicals, gases, or liquids, may require specific types of flanges to ensure resistance to corrosion, erosion, or chemical reactions. Choosing a compatible material ensures the flange can withstand the conditions it will be exposed to, promoting long-term durability and safety.
Pressure Ratings
The operating pressure of the piping system is a critical factor in determining the appropriate fitting flange. Each flange type is designed to withstand specific pressure levels, and choosing one that matches or exceeds the system’s operating pressure is essential to avoid leaks and potential failures.
Temperature Requirements:
Different materials have varying temperature resistance capacities, and the flange must be able to withstand the maximum and minimum temperatures expected in the system.
Environmental Conditions
Factors such as humidity, exposure to sunlight, or the presence of corrosive substances in the surrounding environment should be taken into account to choose a flange material that can withstand these conditions.
Size and Dimensions
Accurate measurements are essential to avoid any misalignment or leaks, especially during installation.
In conclusion, fitting flanges serve as the backbone of piping systems, providing secure connections essential for seamless operations across various applications. Embracing integrated flange and fitting solutions ensures robustness, efficiency, and compliance with safety standards. As the industry progresses, innovations in fitting flange technology will pave the way for even more optimized and sustainable piping systems.
As industry demands continue to evolve, Zetwerk remains at the forefront of fitting flange technology, embracing advancements and future trends to deliver cutting-edge solutions. Whether it’s for critical applications in the oil and gas, chemical, power generation, or other sectors, Zetwerk’s integrated flange and fitting solutions are engineered to ensure reliability, safety, and long-term performance.




FAQs
A fitting flange is a component used to join pipes, valves, and other equipment securely in a piping system. It provides a leak-proof connection and allows for easy disassembly when required.
Integrated solutions offer reliability, ease of installation, enhanced efficiency, and cost-effectiveness. They ensure that all components work seamlessly together, reducing the risk of leaks and failures.
When selecting a fitting flange, consider factors such as material compatibility, pressure ratings, temperature requirements, and environmental conditions. Accurate measurements and adherence to industry standards are essential.
Proper installation involves selecting the right gaskets, tightening bolts to the recommended torque, and ensuring even pressure distribution. Regular maintenance, including inspections and corrosion prevention, helps extend the flange’s lifespan.
Integrated solutions find applications in various industries, including power plants, refineries, chemical processing facilities, commercial buildings, HVAC systems, and water distribution networks. They are essential for reliable performance and smooth operations in diverse projects.