Efficiently managing materials and inventory is the cornerstone of successful manufacturing and industry. Traditional methods need help with various metal materials due to their size and weight. Thankfully, automated inventory storage systems have emerged as a solution, transforming how metal fabrication businesses handle metal inventories. These systems blend technology and engineering to address the unique challenges of metal industries. They optimize space, efficiency, safety, and compliance, reshaping how metal inventory is managed and helping industries stay competitive and responsive to market demands. Today, in this blog, we will explore the significance and types of automated inventory storage systems for metals.
The Challenge of Metal Inventory Management
Metal fabrication industries, including steel mills, foundries, and metal fabrication shops, often deal with various metal types, sizes, and shapes. Managing these materials manually or through conventional storage methods can be labor-intensive and error-prone. Traditional storage systems like shelves, racks, and pallets may not be suitable for efficiently handling heavy and bulky metal items. As a result, companies face issues such as inventory inaccuracies, inefficiencies, and safety concerns.
Automated Inventory Storage Systems: A Game-Changer
Automated inventory storage systems revolutionize how metal fabrication businesses manage their metal inventories. These systems use technology, robotics, and advanced engineering to optimize storage, organization, and retrieval processes. Let’s delve into some of the key benefits and features of these systems
Space Optimization
Automated systems are designed to maximize vertical storage space, allowing for higher-density storage. This is particularly valuable for metal products, as it optimizes floor space while accommodating various sizes and shapes.
Increased Efficiency
Automation lessens the time and effort required for inventory management. With automated retrieval systems, metals can be accessed quickly, minimizing downtime and improving overall production efficiency.
Enhanced Safety
Handling heavy metals manually can pose safety risks for workers. Automated systems minimize the need for physical labor in material handling and reduce the risk of accidents and injuries.
Inventory Accuracy
Automated systems are equipped with advanced tracking and monitoring technologies, ensuring real-time visibility into inventory levels. This reduces the likelihood of stockouts and overstock situations, leading to cost savings.
Improved Traceability and Compliance
Automated inventory storage systems often include advanced tracking and traceability features, making it easier to monitor and record the movement and usage of metal materials. This level of traceability is invaluable for industries that must adhere to strict regulatory and quality control standards. It ensures compliance with regulations, facilitates product recalls if necessary, and enhances the ability to audit inventory history.
Real-time Data and Analytics
Automated systems have data capture and analysis capabilities that provide real-time insights into inventory performance. This data-driven approach allows metal fabrication businesses to make clear decisions about inventory levels, demand forecasting, and production planning. By analyzing historical data and trends, businesses can optimize their metal inventory management strategies, reduce costs, and better align their operations with market fluctuations.
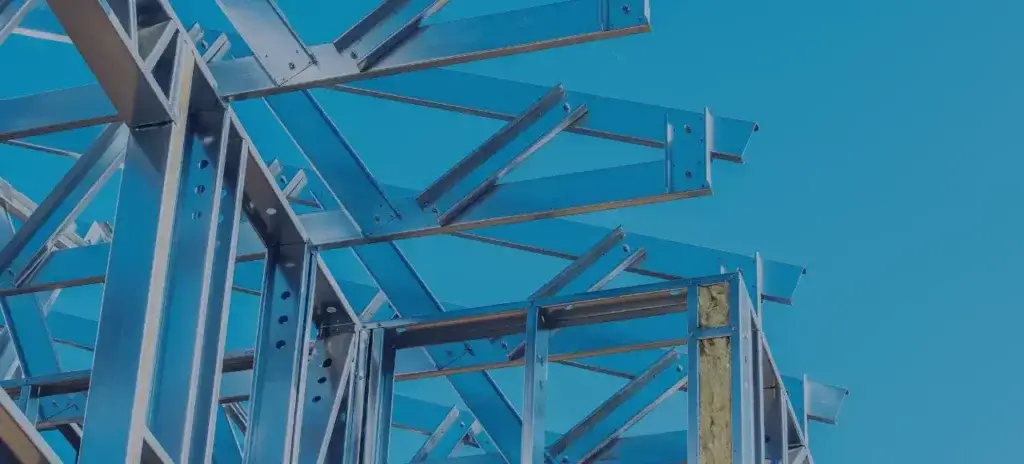
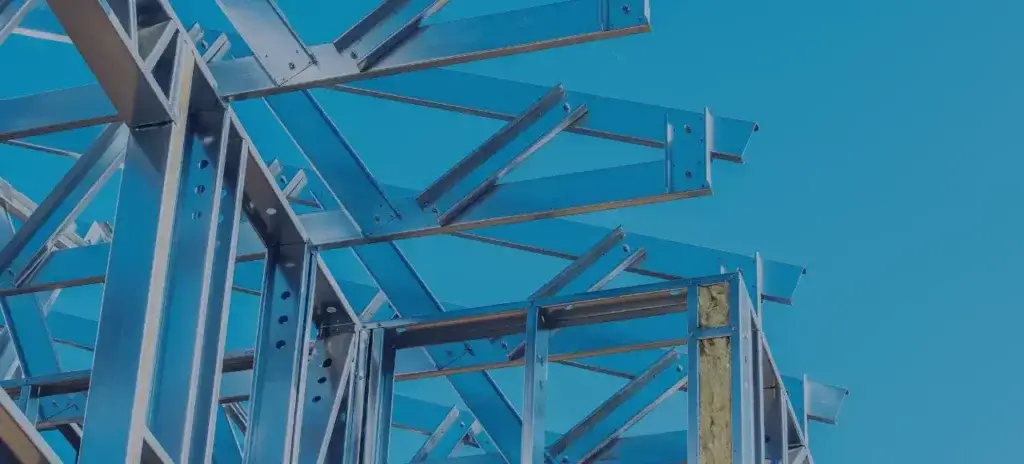
Types of Automated Inventory Storage Systems
Vertical Lift Modules (VLMs)
VLMs are an excellent choice for metal fabrication industries with limited floor space. These systems consist of vertically arranged trays that an integrated lift can automatically access. They are ideal for storing metals in an organized, compact manner, ensuring easy access and retrieval.
Automated Storage and Retrieval Systems (AS/RS)
AS/RS is designed to store metal materials in a high-density, fully automated environment. These systems use cranes, conveyors, and robots to transport and organize materials efficiently. AS/RS is particularly suited for high-volume metal handling operations.
Carousel Systems
Carousel systems utilize rotating shelves or bins to store metal inventory. These systems bring the required item to the operator, eliminating the need for workers to search for items within a warehouse. Carousels are an excellent choice for improving picking and packing efficiency.
Robotic Retrieval Systems
Robotic systems are equipped with advanced robotic arms or automated guided vehicles (AGVs) that can transport heavy metal materials from storage to the production area. They are versatile and can be customized to suit specific storage needs.
Conveyor Systems
Automated conveyor systems are commonly used in metalworking facilities to transport metals from one point to another. They play a significant role in automating the material flow within a manufacturing environment, reducing manual handling and labor costs.
Automated Vertical Carousels
Automated vertical carousels are cylindrical storage units with shelves or carriers that rotate vertically to deliver items to the operator at an ergonomic working height. They are ideal for storing smaller metal components, tools, and parts, providing easy access and improving organization within a limited footprint.
Shuttle Systems
Shuttle systems are designed for high-density storage of metal materials in racks or shelving units. They use autonomous shuttles or robotic vehicles to transport items to and from storage locations. Shuttle systems are known for their speed and scalability, making them suitable for large and small metal inventory operations.
Drawer Storage Systems
Drawer storage systems consist of cabinets or shelving units with multiple pull-out drawers. These systems are highly customizable, allowing metal fabrication businesses to configure drawers to accommodate various metal items, from small fasteners to more significant components. The drawers provide secure and organized storage while simplifying retrieval.
Mini Load AS/RS
Mini Load Automated Storage and Retrieval Systems are a compact and efficient solution for storing smaller metal products, such as screws, nuts, and bolts. These systems use automated cranes and conveyors to transport bins or totes between storage locations and workstations, reducing the need for manual picking and reducing errors.
Flow Rack Systems
Flow rack systems are designed to facilitate the first-in, first-out (FIFO) storage and retrieval of metal items. They consist of inclined roller or conveyor tracks that allow items to flow from the loading end to the unloading end. Flow rack systems are beneficial for managing metal items with expiration dates or specific usage requirements.
Conclusion
In the rapidly evolving landscape of manufacturing and inventory management, automated systems have emerged as a game-changer for the metal fabrication industry, allowing businesses to remain competitive and responsive to market demands.
FAQs
Automated systems optimize space, increase efficiency, enhance safety, and improve inventory accuracy, making them invaluable in managing the diverse and heavy metal materials used in the metalworking industry.
Yes, many automated inventory storage solutions can be tailored to the needs and budget constraints of small businesses, offering scalable options that improve inventory management without breaking the bank.
Yes, automated systems are highly versatile and can be configured to accommodate a variety of metal materials, from tiny fasteners to substantial steel coils.
Automated systems incorporate advanced tracking and monitoring technologies, offering real-time visibility into inventory levels. This data-driven approach minimizes the likelihood of both stockouts and overstock situations.
These systems apply to various industries, such as automotive, aerospace, and more, where efficient inventory management, quick access, and safety are paramount. The benefits extend to any business dealing with materials and products.