Plastic bushings have gained popularity in various industries due to their versatility and exceptional properties. The selection of the appropriate plastic bushing material is of utmost importance as it directly impacts the optimal performance of mechanical systems. With a wide range of plastic materials available, such as nylon, PTFE, and UHMW, manufacturers can choose the material that best suits their specific application requirements, ensuring enhanced performance, increased efficiency, and improved longevity of their mechanical systems.
About Plastic Bushings
Plastic bushings are components that support and guide shafts or rods in manufacturing processes. They serve as crucial elements that facilitate smooth movement while minimizing friction. These bushings are typically cylindrical or flanged in shape and are made of various plastic materials. Their primary function is to provide a low-friction surface between the shaft and the surrounding structure, allowing for efficient motion and reducing wear.
Plastic bushings are available in different materials, each offering unique characteristics suitable for specific applications. Some commonly used plastic materials for bushings include:
- Nylon – Nylon bushings are known for their high strength, durability, and resistance to abrasion.
- PTFE (polytetrafluoroethylene) – PTFE bushings have excellent self-lubricating properties, low friction, and high resistance to chemicals and temperatures.
- UHMW (ultra-high-molecular-weight polyethylene) – UHMW bushings are valued for their exceptional wear resistance, low friction, and impact strength.
Applications of Plastic Bushings
Automotive Industry
Plastic bushings have found significant application in the automotive industry, contributing to various components’ smooth and efficient operation. One of the critical areas where plastic bushings excel is in suspension systems. They are utilized in control arms, sway bars, and strut mounts, providing durability, noise reduction, and improved ride quality. Plastic bushings also play a crucial role in steering columns, offering low friction and precise movement for steering mechanisms. Additionally, they are used in throttle linkages, where their self-lubricating properties and corrosion resistance enhance throttle response and longevity.
Industrial Machinery
Plastic bushing parts have proven their worth in the demanding environment of industrial machinery. They are commonly employed in conveyor systems to support and guide rollers, ensuring smooth material handling and reducing maintenance requirements. In assembly lines, plastic bushings provide reliable performance in guiding robotic arms and other moving parts. Their lightweight nature contributes to overall efficiency and energy savings. Moreover, in robotic equipment, plastic bushings help reduce friction, minimize wear, and improve precision in movements, thereby enhancing the lifespan and performance of the machinery.
HVAC and Appliances
Plastic bushings play a vital role in heating, ventilation, air conditioning (HVAC) systems, and household appliances. In HVAC systems, plastic bushings are used in fan motors, blower assemblies, and dampers. They provide low friction, noise reduction, and resistance to moisture and chemicals, contributing to reliable and efficient operation. Within household appliances like refrigerators and washing machines, plastic bushings support moving parts such as door hinges, drum assemblies, and agitators. The self-lubricating properties of plastic bushings reduce friction and wear, ensuring smooth and quiet operation while extending the lifespan of these appliances.
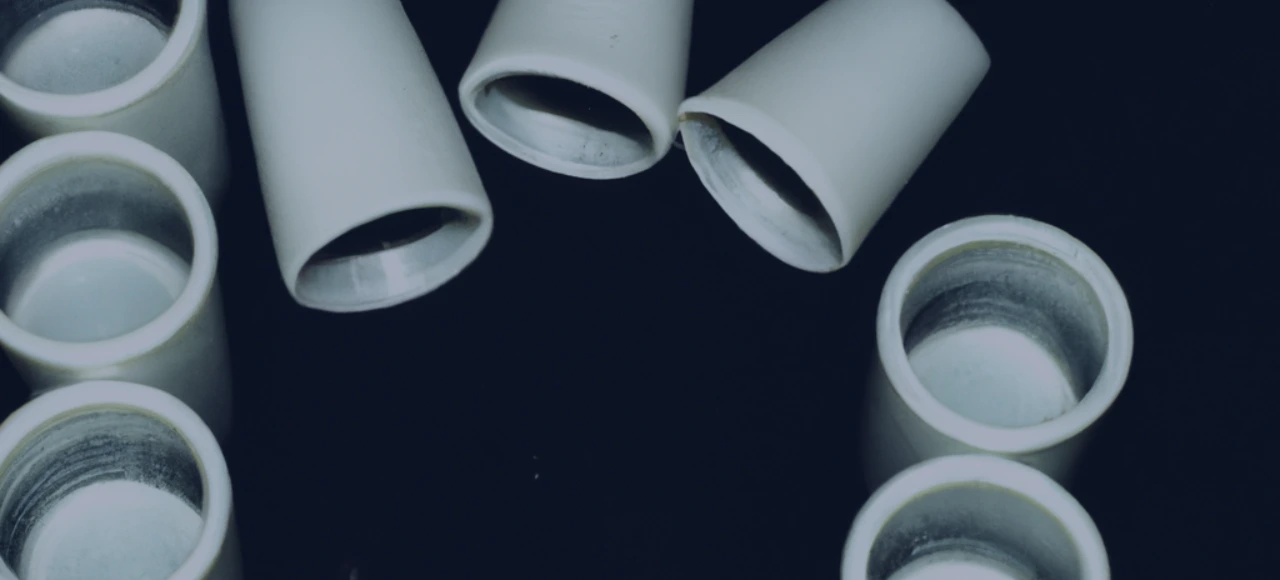
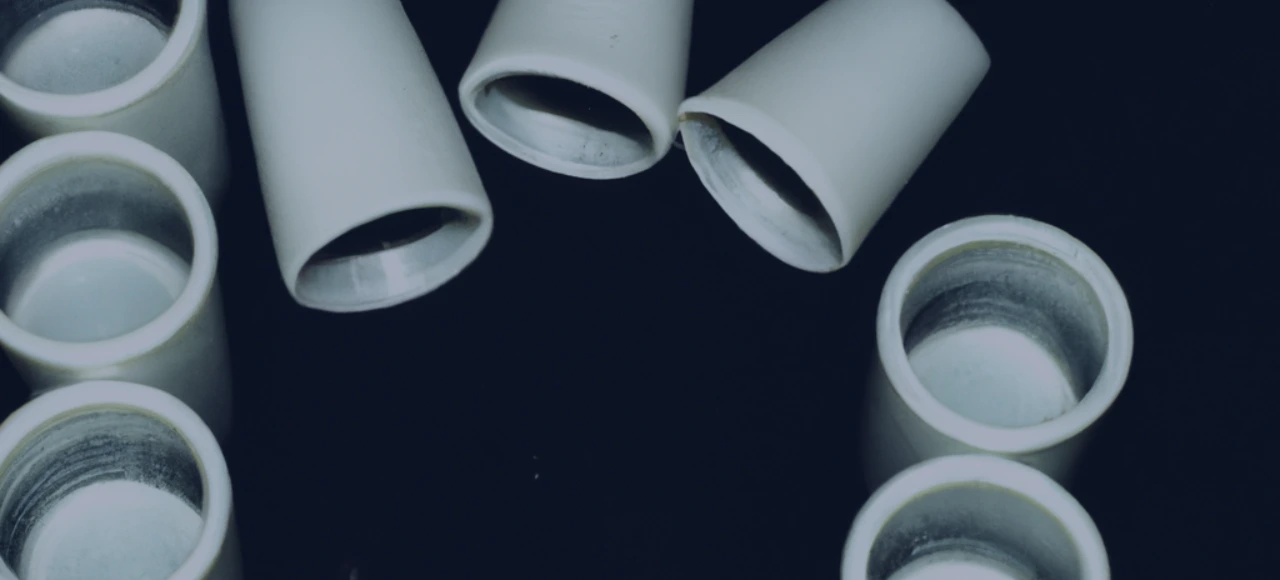
Benefits of Plastic Bushings in Specific Scenarios
Low-Friction Applications
- Plastic bushings excel in low-friction environments, significantly reducing wear and improving overall efficiency. Plastic materials such as PTFE have excellent self-lubricating properties, reducing friction between the bushing and the shaft. This self-lubrication minimizes external lubrication, leading to lower maintenance requirements.
- By reducing friction, plastic bushings help mitigate wear on both the bushing and the shaft, extending the components’ lifespan and enhancing the system’s overall efficiency. These low-friction properties make plastic bushings well-suited for applications where smooth movement, precise control, and minimized energy loss are essential.
Moisture and Chemical Resistance
- Plastic bushings are ideal for applications exposed to moisture, chemicals, or corrosive environments. Unlike metal or bronze bushings, plastic materials like nylon, PTFE, and UHMW offer excellent resistance to moisture and various chemicals. This resistance enables plastic bushings to maintain structural integrity and performance even in harsh conditions.
- Plastic bushings do not rust or corrode, ensuring their reliability and longevity in challenging environments. This makes them particularly valuable in marine, chemical, and food industries, where exposure to moisture, chemicals, or corrosive substances is common. Plastic bushings’ ability to withstand these environments contributes to the durability and functionality of the systems they are incorporated into.
Noise and Vibration Dampening
- Another notable benefit of plastic bushings is their ability to absorb vibrations and reduce noise levels. Plastic materials possess inherent damping properties, which allow them to absorb and dissipate vibrations that may arise during equipment operation. This vibration-dampening characteristic helps to minimize noise levels, making plastic bushings suitable for applications where quiet operation is desired.
- The reduced vibrations also contribute to the overall stability and smoothness of the machinery, enhancing its performance and the comfort of those operating or utilizing the equipment. Industries such as HVAC, appliances, and precision equipment greatly benefit from plastic bushings’ noise and vibration dampening qualities.
The benefits of plastic bushings in specific scenarios are significant. Their low-friction properties reduce wear and improve efficiency, making them ideal for low-friction applications. Plastic bushings’ resistance to moisture and chemicals ensures their reliability in harsh environments.
Additionally, their vibration-dampening capabilities contribute to smooth and quiet operation in various equipment and machinery. By considering these specific benefits, manufacturers can make informed decisions to leverage the advantages offered by plastic bushings in their applications.
Conclusion
Plastic bushings have emerged as indispensable components in various industries and applications. Their versatility, durability, and cost-effectiveness make them an ideal choice for different machinery and equipment. Plastic bushings ensure smooth and efficient operations in automotive systems, industrial machinery, and consumer electronics.
Among the leaders in plastic bushing manufacturing is Zetwerk. We offer high-quality, precision-engineered bushings tailored to modern manufacturing standards. With a commitment to quality control and customization, Zetwerk’s products seamlessly integrate into various applications. Our dedication to sustainable practices aligns with the growing demand for eco-friendly solutions, making us a trusted choice in the industry.




FAQs
plastic bushings can be highly durable, depending on the specific material chosen and the application requirements. Many plastic materials used for bushings offer excellent wear resistance, corrosion resistance, and long-term durability, making them a reliable choice in various industries.
Plastic bushings can handle various loads, but their capacity may vary depending on the specific material and design. It is essential to consider the load requirements of the application and choose a plastic bushing with suitable load-bearing capabilities to ensure optimal performance.
It depends on the specific plastic material used. Some plastic bushings, such as those made of PTFE or self-lubricating plastics, have inherent lubrication properties, reducing the need for regular external lubrication. However, it is recommended to consult the manufacturer’s guidelines to determine the specific lubrication requirements of the chosen plastic bushing.
Plastic bushings can be suitable for high-temperature applications, depending on the chosen plastic material. Certain plastics, such as PTFE, can withstand elevated temperatures, while others may have limitations. It is crucial to select a plastic bushing material that can handle the expected temperature range of the application.
In many cases, plastic bushings can be retrofitted into equipment that originally had metal bushings. However, careful consideration should be given to factors such as load requirements, dimensions, and compatibility with the existing equipment to ensure a successful retrofitting process.