Introduction
The demand for high-performance industrial equipment like electric motors has been on the rise in industries such as e-mobility, electric aircraft, drones, defense vehicles, and medical devices. These applications require motors with enhanced power density and torque density to meet the weight and packaging constraints while delivering optimal performance.
Thinner and soft magnetic laminations in the stator and rotor stacks have emerged as a solution to reduce core losses and increase continuous motor power. By carefully choosing material thickness and stack combination, lamination design can significantly enhance motor efficiency, reduce energy consumption, and improve overall performance.
In this article, we will delve into the various aspects of enhancing electric motor efficiency through lamination design. We will explore optimizing lamination thickness through precise machining for improved efficiency, high-performance soft magnetic alloys that contribute to enhanced output optimization, segmented lamination stator technology for higher efficiency, core plate annealing to reduce hysteresis losses, and efficient magnetic circuit design for improved performance.
Optimizing Lamination Thickness for Enhanced Efficiency
- One of the key factors influencing electric motor efficiency is lamination thickness. Core losses increase with higher frequencies; however, they can be reduced by using thinner lamination thicknesses.
- Thinner laminations are more effective at reducing eddy current contributions as operational frequency increases due to their ability to decrease eddy current losses by shortening the path for induced currents. The optimal choice of lamination thickness depends on the specific application frequency.
- As the operational frequency increases beyond a certain point known as the crossover point, where eddy current losses dominate overall losses at higher frequencies, thinner laminations become more effective in minimizing losses. This relationship between operational frequency and lamination thickness is crucial for minimizing eddy current losses and optimizing motor efficiency.
Relationship between Operational Frequency and Lamination Thickness
Operational Frequency (Hz) | Optimal Lamination Thickness (mm) |
---|---|
Up to 100 | 0.35-0.5 |
100-500 | 0.2-0.35 |
500-2000 | 0.1-0.2 |
Above 2000 | <0.1 |
High-Performance Soft Magnetic Alloys for Improved Efficiency
The choice of material plays a significant role in optimizing motor or generator output. Various high-performance soft magnetic alloys are available with high induction, permeability, and low core losses. Alloys such as Hiperco 50, which is a cobalt-based alloy with excellent magnetic properties, offer enhanced performance for high-speed motors due to their high saturation flux density and low coercivity. Other commonly used alloys include silicon steel (electrical steel), nickel-iron alloys, amorphous metal alloys, and powdered iron materials.
Segmented Lamination Stator Technology for Higher Efficiency
- Brushless DC motors utilizing segmented lamination stator technology have gained popularity due to their ability to offer higher torque and power density compared to traditional designs while running cooler, which potentially extends their operational life.
- This design improves motor efficiency by increasing slot fill through tighter packing of conductors within the stator slots, reducing end turn waste, and improving overall copper utilization. The reduced end turn waste leads to lower copper losses and improved electrical conductivity.
- Furthermore, the incorporation of insulation coatings between laminations prevents short circuits and minimizes eddy current losses by blocking induced currents that can lead to energy wastage. These insulation coatings are carefully designed to withstand operational conditions and ensure long-term performance.
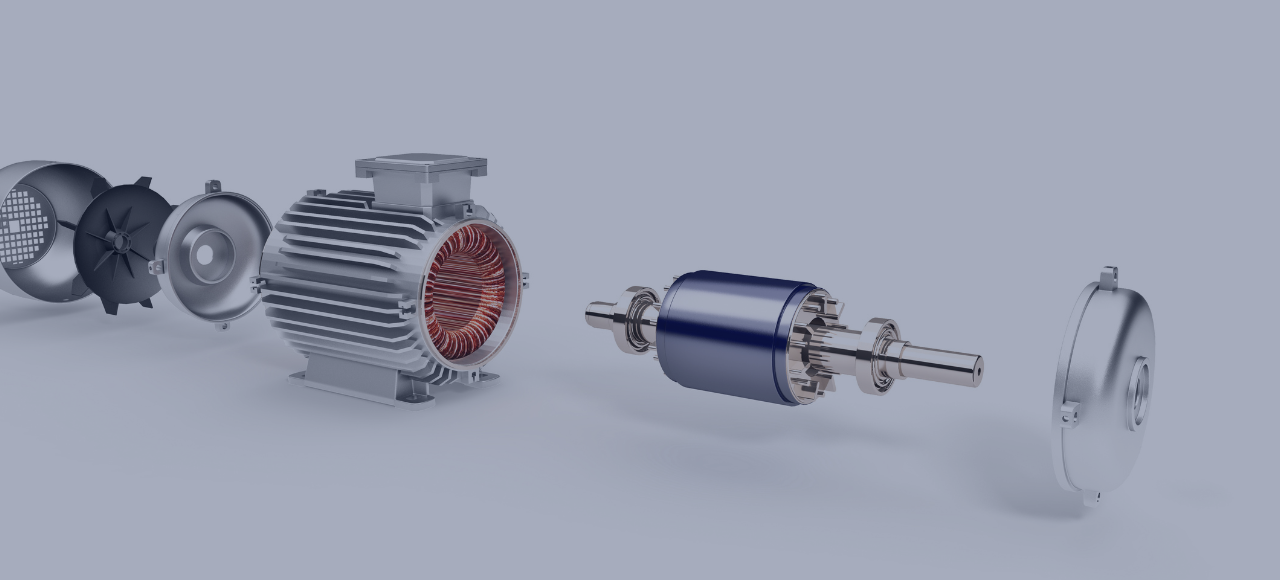
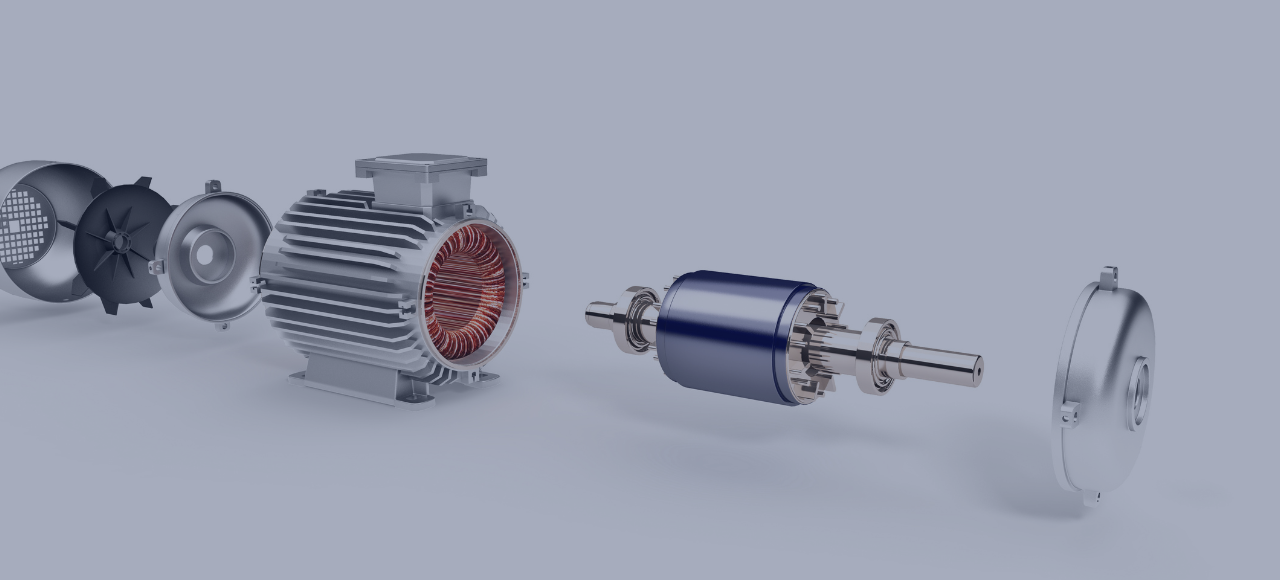
Advantages of Segmented Lamination Stator Technology
- Higher torque density
- Improved power density
- Reduced end turn waste
- Lower copper losses
- Enhanced efficiency
Core Plate Annealing for Reduced Hysteresis Losses
Core plate annealing is a process used to align the grain structure in laminations, thereby reducing hysteresis losses. This process involves heating and cooling the laminations to optimize their magnetic properties and enhance motor efficiency.By aligning the grain orientation, core plate annealing minimizes magnetic losses during magnetization cycles. The aligned grains create an efficient path for magnetic flux within the motor, leading to reduced energy dissipation and improved overall performance.
It is crucial to note that core plate annealing requires expert processing and precision manufacturing techniques. Proper control of temperature, time, and cooling rates ensures optimal grain alignment and desired improvements in motor efficiency.
Final Words
Enhancing electric motor efficiency through lamination design is a critical consideration for optimizing power density, torque density, and overall performance across various industries. By optimizing lamination thickness, utilizing high-performance soft magnetic alloys, and more, manufacturers can achieve significant improvements in motor efficiency.
The choice of material, thickness, and stack combination is crucial in achieving the desired motor output. Thinner laminations are effective at reducing eddy current losses at higher operational frequencies. High-performance soft magnetic alloys with low core losses and tailored properties for specific frequency ranges enhance motor efficiency.
Looking to enhance your electric motor efficiency through lamination design? Zetwerk offers a range of manufacturing services, including precision machining, casting, forging, and surface treatment. Visit Zetwerk for high-quality electric motor laminations from trusted suppliers.




FAQs
Lamination thickness influences eddy current losses. Thinner laminations reduce the path for induced currents, minimizing energy wastage and increasing motor efficiency.
Common high-performance soft magnetic alloys include electrical steel grades like Silicon Iron (SiFe), Nickel Iron (NiFe), Cobalt Iron (CoFe), and Amorphous Metal Alloys.
Segmented lamination stator technology can be applied to various motor types such as induction motors, synchronous motors, and DC motors, with specific design considerations for each type.
Core plate annealing is typically performed during the manufacturing process. Applying it to existing motors may not be feasible or cost-effective due to the need for precision manufacturing and expert processing.
Insulation coating between laminations prevents short circuits and minimizes eddy current losses by blocking induced currents that can lead to energy wastage. It enhances overall motor efficiency by reducing losses associated with eddy currents and hysteresis.