Introduction
In the manufacturing of induction motors, the design of lamination plays a crucial role in ensuring optimal performance and efficiency. The end-lamination stator induction motor design is particularly important in achieving high slot fills and reducing material usage. This article explores the various aspects of end-lamination stator induction motor design, including the standardization of cleat notches and lamination tooth openings. By understanding these key considerations, manufacturers can optimize their motor designs for improved performance.
Understanding End-Lamination Stator Induction Motor Design
Effective lamination design optimizes the use of materials while ensuring proper functioning of the motor. The following points highlight some key considerations in this process:
Importance of lamination design in motor manufacturing
- Laminations provide a path for magnetic flux within the stator core.
- Modifying lamination design can be expensive compared to changing winding specifications.
- Properly designed laminations minimize energy losses due to eddy currents.
Standardization of cleat notches and lamination tooth openings
- Cleat notches should be standardized to ensure material savings and ease of manufacturing.
- Cleating notches should align with lamination tooth openings around the stator’s periphery.
- Standardization of these aspects allows for interchangeability and reduces costs.
Slot openings and their impact on wire size and manufacturing restrictions
- Slot openings are a compromise between wire size, product parameters, and manufacturing restrictions.
- In the past, slot openings were determined by wire stiffness, but with machine insertion, larger slot openings are now common.
- The choice of slot opening impacts the wire size that can be used in the motor.
The Role of Slot Configuration in Stator Induction Motor Design
The configuration of slots within the stator core is an important aspect of end-lamination stator induction motor design. It influences the automatic insertion of wedges and ensures proper wire insertion. Here are some key points to consider:
Automatic insertion of wedges and the shape of slot bottoms
- Proper slot configuration allows for the automatic insertion of wedges during manufacturing.
- The shape of the bottom of the slot is defined by specific dimensions to ensure proper wire insertion and minimize process issues.
Considerations for the back shape of slots
- The back shape of slots is not crucial for most practical purposes and can be either square or round.
- Square-back slots are commonly used due to ease of manufacturing.
Standardization benefits within a family of laminations
- Standardizing slot configurations within a family of laminations offers cost savings through standardization of toolings and increased machine utilization.
- This allows manufacturers to streamline their production processes and reduce overall costs.
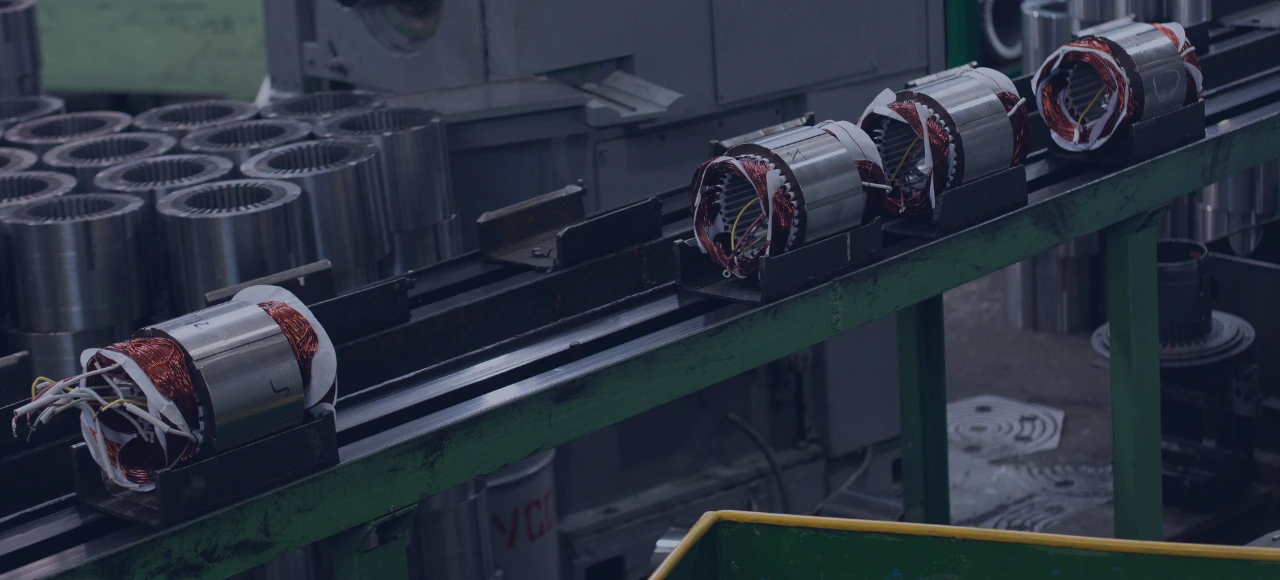
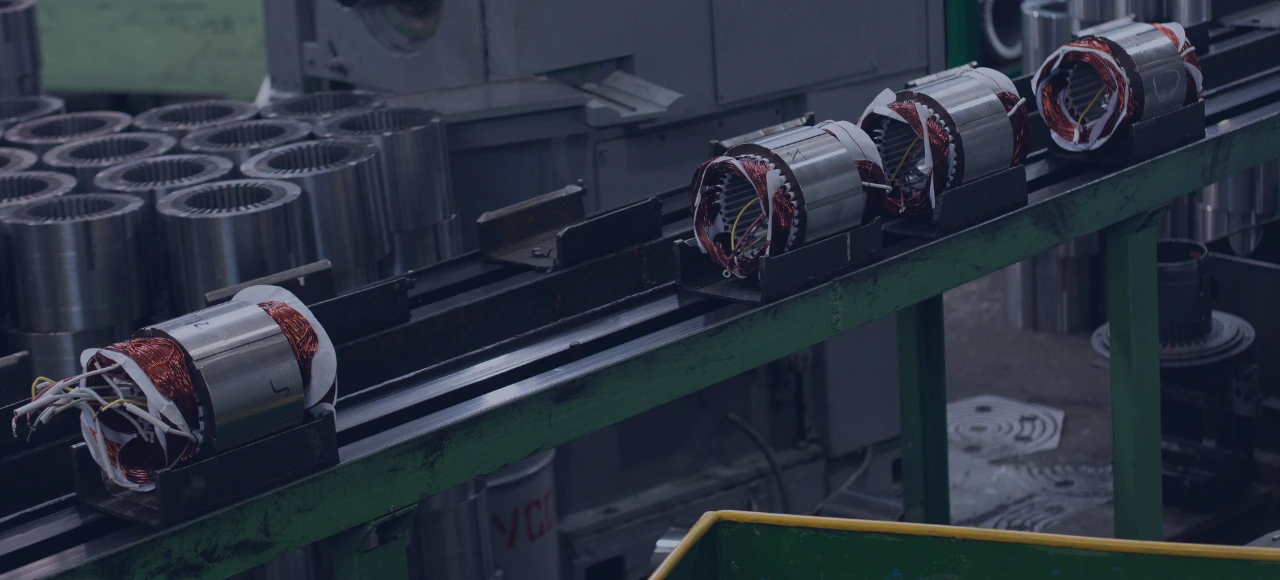
Winding Specifications and Their Impact on Motor Manufacturing
Winding specifications play a vital role in determining how stators are inserted into motors during manufacturing. Here are some crucial considerations:
Crucial criteria for machine insertion of stators
- Winding specifications such as wire size, number of turns, pole configurations, etc., must meet the criteria for machine insertion of stators.
- Compatibility between selected tooling openings (blade gaps), slot openings, and wire size is essential for efficient manufacturing.
Compatibility between tooling opening, slot opening, and wire size
- The tooling opening or blade gap must be suitable for the selected slot opening and wire size to avoid locking-wire conditions.
- Locking-wire conditions can damage wire insulation or cause tooling damage.
Avoiding locking-wire conditions with optimal blade gap chart
- An optimal blade gap chart helps determine suitable combinations of slot opening and wire size to avoid locking-wire conditions.
- This chart ensures that the motor design is compatible with the capabilities of the manufacturing process.
Achieving High Slot Fills for Improved Performance
High slot fills are desired in motor designs as they improve performance efficiency and reduce material usage. Here are some important factors to consider:
Importance of slot fill-in performance efficiency and material usage:
- Slot fill refers to the percentage of wire in a slot relative to the total slot area.
- Higher slot fills result in improved performance efficiency and allow for smaller motor packages.
Design considerations for achieving high slot fills
- Achieving high slot fills requires careful design and development.
- Factors such as wire diameter, coil pitch, insulation thickness, lamination geometry, etc., impact slot fills.
Special techniques like compaction processes
- Special techniques like compaction processes can potentially achieve higher slot fills.
- Compaction processes involve compressing the windings within the slots to increase filling percentages.
Innovative Approaches to Thin Metal Laminations
Thin metal laminations are used to minimize energy losses due to eddy currents in high-speed induction motors. Here are some innovative approaches to producing thin metal laminations:
- Minimizing eddy current loss with thin metal laminations.
- Limitations of traditional fabrication techniques.
- The Uniform Droplet Spray process for producing thin laminations.
Final Words
In conclusion, end-lamination stator induction motor design plays a critical role in achieving optimal performance, efficiency, and cost-effectiveness in motor manufacturing. Standardization of various aspects such as cleat notches, lamination tooth openings, and slot configurations helps streamline production processes and reduce costs. Winding specifications, slot fills, insulation techniques, and innovative approaches to thin metal laminations further enhance motor designs. By considering these factors, manufacturers can create high-quality stator induction motors that meet the demands of various applications.
As a leading manufacturing services provider, Zetwerk offers a wide range of services related to motor components and other manufacturing needs. From custom part production to supply chain management solutions, Zetwerk provides reliable services tailored to meet specific requirements. Explore Zetwerk’s Knowledge Hub for more informative articles on various manufacturing topics.




FAQs
The best slot configuration depends on factors like wire size, manufacturing restrictions, and product parameters. Consider automatic insertion of wedges, suitable bottom slot shape, and standardization benefits within a family of laminations.
High slot fills result in improved performance efficiency, material usage optimization, and smaller motor packages. It enhances electrical conductivity and reduces losses, ultimately leading to higher motor efficiency.
Advancements in wire and slot-cell insulation have explored eliminating phase insulation. However, it is important to evaluate their impact on electrical resistivity between windings and ensure proper insulation properties before completely eliminating phase insulation.
The Uniform Droplet Spray (UDS) process optimizes droplet thermal state, mass flux distribution, deposit thermal state, and substrate motion to produce thin metal laminations with improved surface flatness and uniformity. It offers potential applications in high-speed induction motors