Introduction
Electric motor laminations play a crucial role in improving the efficiency and reducing losses in electric motors. These laminations are manufactured using various techniques to meet specific application requirements. For businesses involved in procuring or using these products, understanding the different manufacturing techniques and materials used in electric motor laminations is essential.
Overview of Motor Laminations
Motor laminations are thin layers of metal stacked together to form the core of an electric motor. They are designed to reduce core losses and improve motor efficiency. The choice of manufacturing technique depends on factors such as the volume of laminations needed, lamination design, desired production speed, and cost considerations.
Materials Used in Motor Laminations
The choice of materials for motor laminations depends on various factors such as electrical conductivity, magnetic properties, mechanical strength, cost, and application requirements. Some commonly used materials include:
- Cobalt Alloys: Cobalt alloys are often used when high flux density without saturation is required. These alloys offer improved resistance to wear, corrosion, and heat. They also provide high magnetic permeability and are suitable for applications where high performance is essential.
- Nickel Alloys: Nickel alloys are known for their low core losses and high permeability at low to moderate inductions. They require an annealing cycle with added surface insulation to achieve optimal performance.
- Silicon Steels: Silicon steels (M15-M45) are widely used in motor laminations due to their excellent electrical conductivity and magnetic properties. They offer reduced core losses and improved efficiency in electric motors.
- Transformer Steel: Transformer steel is a form of electrical steel specifically suited for non-rotational devices such as transformers or stators in electric motors. It has unique magnetic properties that make it ideal for these applications.
Manufacturing Techniques for Motor Laminations
There are several standard manufacturing techniques employed for producing motor laminations:
Stamping
Stamping is a widely used manufacturing technique due to its cost-effectiveness and high production rates. It is particularly suitable for large quantities of laminations in low- to medium-volume production runs. The process involves feeding a metal sheet into a punch press machine that uses a die to stamp out the desired shape of the laminations. Stamping offers high precision, repeatability, and dimensional accuracy.
Laser Cutting
Laser cutting is an advanced manufacturing technique that utilizes a laser beam to precisely cut through the metal sheet, creating complex shapes and designs with tight tolerances. It is suitable for high-volume production runs and provides excellent precision and edge quality. Laser cutting offers flexibility in terms of design modifications without compromising accuracy.
Etching
Etching is commonly used when intricate or complex shapes are required in motor laminations. It involves applying a chemical etchant to selectively remove material from the metal sheet, leaving behind the desired pattern or shape. Etching offers greater design flexibility compared to other techniques but is slower and more expensive, making it suitable primarily for low-volume production runs.
Roll Forming
Roll forming is a fast and cost-effective method used for producing large quantities of motor laminations in medium- to high-volume production runs. It involves passing a metal sheet through rollers that gradually shape it into the desired lamination profile. Roll forming offers high production rates, reduced material waste, and consistent quality control.
Powder Metallurgy
Powder metallurgy is a process that involves compacting metal powder into the desired shape and then sintering it to form a solid piece. It is suitable for producing motor laminations with complex shapes and designs in high volumes. Powder metallurgy offers excellent dimensional accuracy, material utilization, and cost-effectiveness.
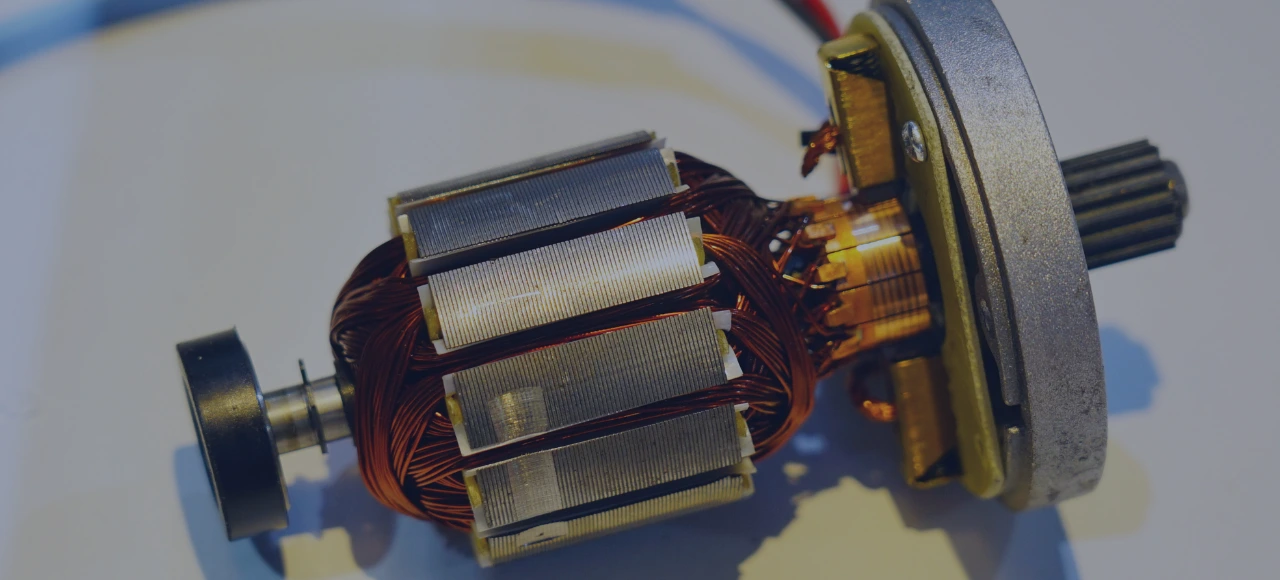
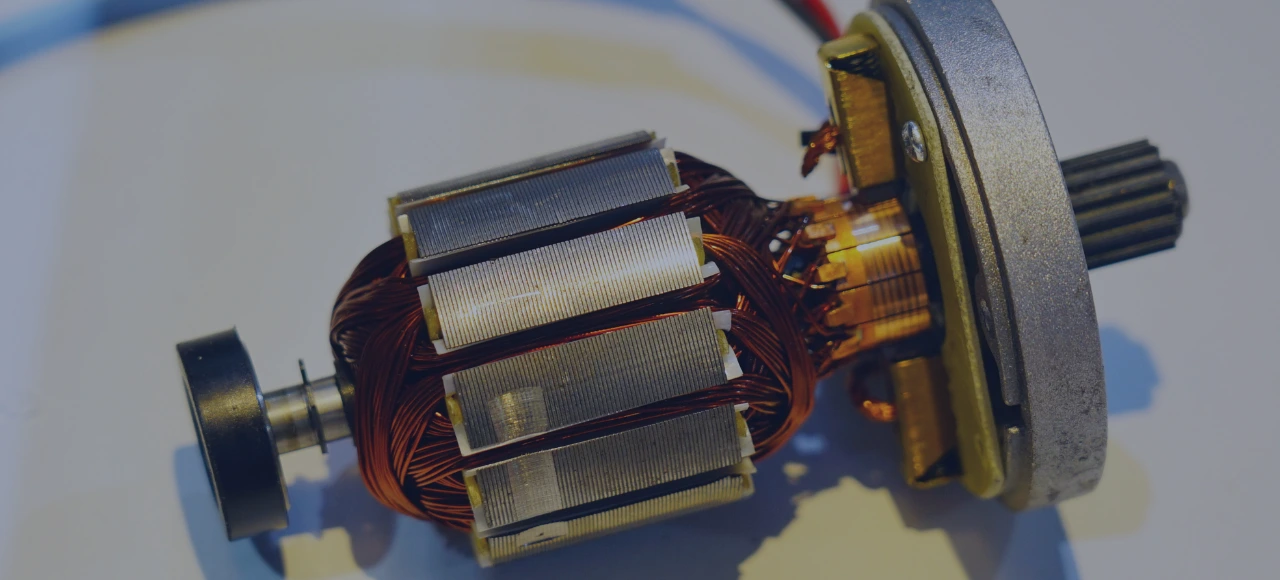
Innovative Method for Manufacturing Electric Motor Rotors
- A novel method for manufacturing laminations for electric motor rotors involves forming bosses on the face of the lamination and reducing the thickness of the first portion of the boss through localized narrowing achieved by misalignment of a die relative to a punch within a mold. This reduction in thickness allows precise coupling of laminations with the desired offset angle without the need for relief holes or coupling holes typically found in traditional laminations.
- The use of this innovative method ensures maximum precision and stability in positioning and stacking rotors with skew or helical slots. By eliminating relief holes or coupling holes, this method optimizes the performance of electric motors.
Key Takeaways
Electric motor laminations are crucial components that optimize motor efficiency and reduce losses. Understanding the different manufacturing techniques used, such as stamping, laser cutting, etching, roll forming, and powder metallurgy, is essential for businesses involved in procuring or using these products. Material selection plays a significant role in motor performance, weight, and cost. Zetwerk’s expertise in manufacturing motor laminations adheres to strict specifications and certifications while offering diverse material capabilities.
FAQs
Different manufacturing techniques offer various benefits. Stamping is cost-effective for large quantities, laser cutting provides precision, etching allows complex designs, roll forming is fast and cost-effective for large quantities, and powder metallurgy produces complex shapes in high volumes.
Material selection directly impacts motor efficiency by influencing factors such as electrical conductivity, magnetic properties, core losses, weight, and cost. Optimal material selection can improve motor performance and reduce energy losses.
Yes, Zetwerk specializes in manufacturing motor laminations according to strict specifications and certifications. They have the expertise to accommodate custom requirements, offering a range of punch presses capable of processing various quantities and sizes.
The innovative method for manufacturing rotors with skew or helical slots is applicable to various types of electric motors that require precise coupling without relief or coupling holes. It enables maximum precision and stability in rotor design.