When it comes to mechanical engineering, choosing between bushings and bearings can significantly impact the efficiency, reliability, and lifespan of industrial machinery and equipment – especially in high-load applications. Reducing friction and supporting moving parts are crucial functions that both bushings and bearings serve. However, they possess distinct characteristics that make them more appropriate for particular scenarios. Let’s explore bushings and bearings, including their applications, designs, manufacturing processes, and critical differences. You will also understand the essential factors to consider when deciding between these components, enabling engineers and designers to optimize their designs for top performance in challenging environments.
Bushings
Bushings, or plain or sleeve bearings, are fundamental components in various mechanical systems to reduce friction and support moving parts. Bushings are vital in countless mechanical systems, providing low-cost and reliable solutions to reduce friction and support moving parts. Their diverse applications, along with different materials and manufacturing processes, make them a versatile choice for engineers and designers. By understanding the unique characteristics of bushings and their suitability for various applications, professionals can make informed decisions to optimize the performance and efficiency of their mechanical designs.
Applications
- Automotive Industry: Bushings are used in suspension systems, steering assemblies, and control arms to dampen vibrations and provide stability.
- Industrial Machinery: Bushings are utilized in conveyor systems, pumps, compressors, and gearboxes to minimize friction and support shafts.
- Aerospace: They can be found in aircraft landing gear and control surfaces, ensuring smooth movements and reducing wear.
- Electrical Motors: Bushings are employed in electric motors to support shafts and reduce noise and vibration during operation.
- Construction Equipment: In construction machinery, such as excavators and bulldozers, Bushings are used to withstand heavy loads and repetitive motions.
Design & Manufacturing
Bushings typically consist of cylindrical metal sleeves made from bronze, steel, or composite plastics. The choice of material depends on factors such as load capacity, temperature resistance, and environmental conditions. Bronze bushings, for example, offer excellent wear resistance and self-lubricating properties, making them suitable for high-load applications. Composite plastic bushings are known for their corrosion resistance and ability to function without external lubrication.
Manufacturing bushings involve precision machining to achieve accurate dimensions and smooth surfaces. The inner and outer diameters are machined to fit precisely into the housing and shaft. Additionally, some bushings may have a thin layer of lubricants, such as oil-impregnated bronze bushings or self-lubricating plastics, to reduce friction and ensure continuous performance without frequent maintenance.
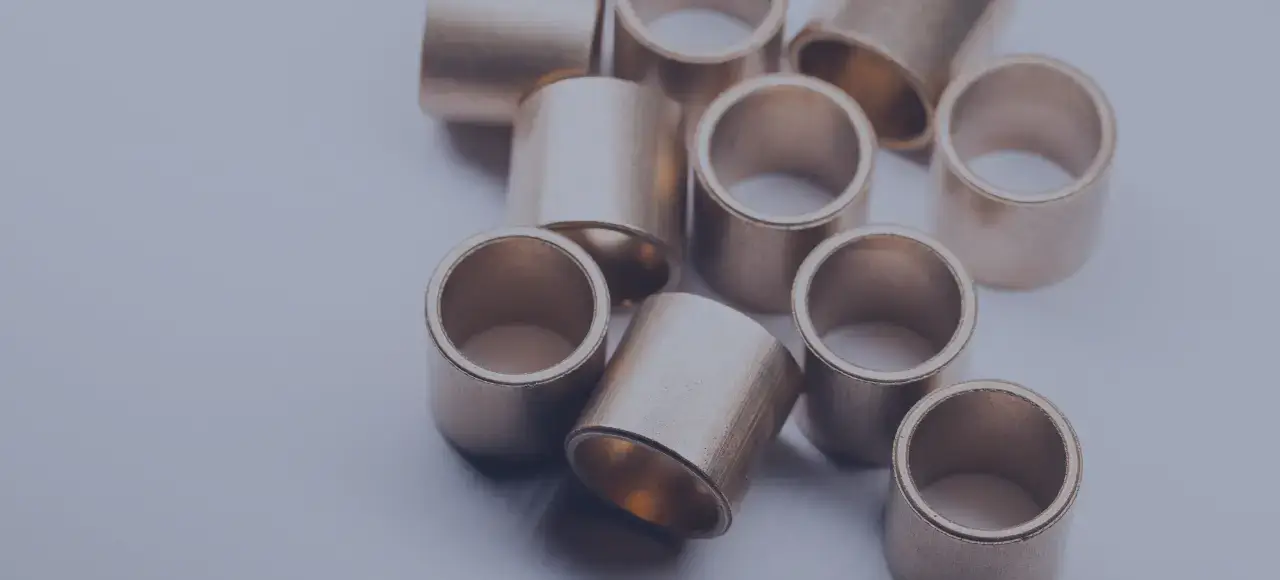
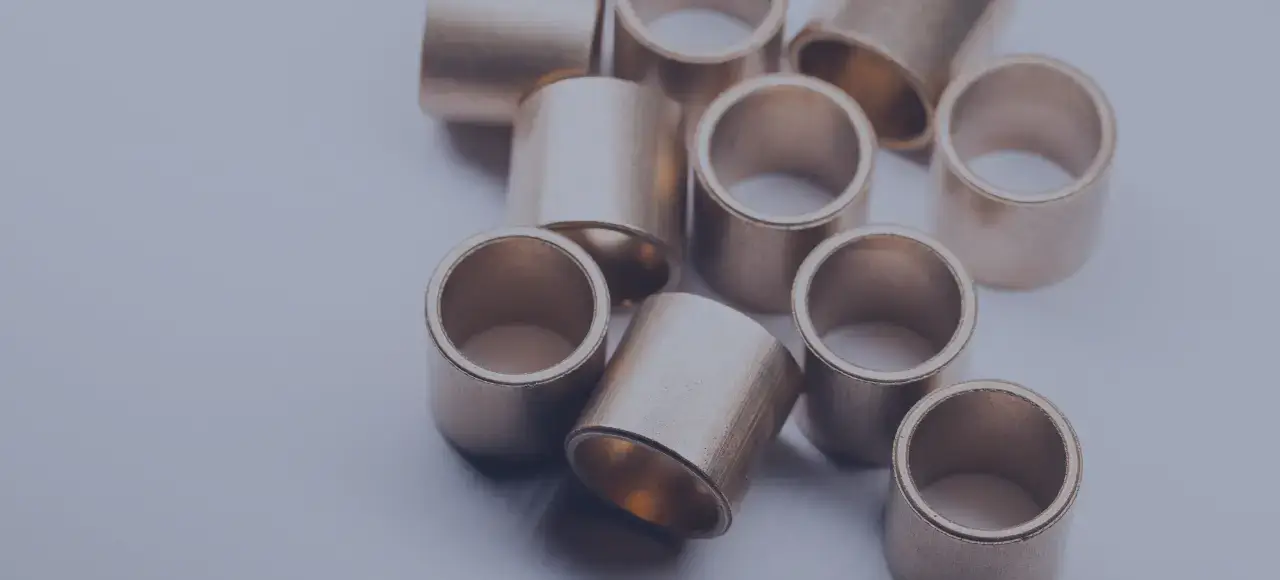
Bearings
Bearings are critical components in mechanical systems to support rotating or linear motion while minimizing friction and enabling smooth operation. Bearings are crucial components in many industries due to their ability to decrease friction between moving parts. This results in increased efficiency and reliability of machinery and equipment.
Applications
- Automotive Industry: Bearings are used in wheels, transmissions, and engines to support shafts and reduce friction during motion.
- Industrial Machinery: Bearings are found in motors, pumps, fans, and turbines, supporting rotating elements and ensuring smooth operation.
- Aerospace: They are utilized in aircraft engines, landing gears, and control systems to handle high-speed rotations and extreme conditions.
- Robotics: Bearings play a crucial role in robot joints, enabling precise movements and smooth articulation.
- Wind Energy: Large bearings support wind turbines’ blades and generator components, allowing them to harness renewable energy efficiently.
Design & Manufacturing
Bearings come in various designs and configurations to meet specific application requirements. The most common bearings varieties include ball, roller, and plain bearings (bushings). Each class is designed to distribute loads differently and accommodate varying friction and rotational speeds.
Ball bearings consist of rolling elements (balls) sandwiched between two raceways, while roller bearings use cylindrical or tapered rollers instead of balls. These rolling elements minimize contact area, reducing friction and allowing smoother movement. On the other hand, plain bearings (bushings) offer a cylindrical sleeve with a lubricant layer that facilitates smooth rotation.
Manufacturing processes for bearings involve precision engineering and material selection to meet the demands of particular applications. Bearings can be made from steel, ceramics, or polymer materials, each offering unique advantages such as high load capacity, corrosion resistance, or lightweight properties.
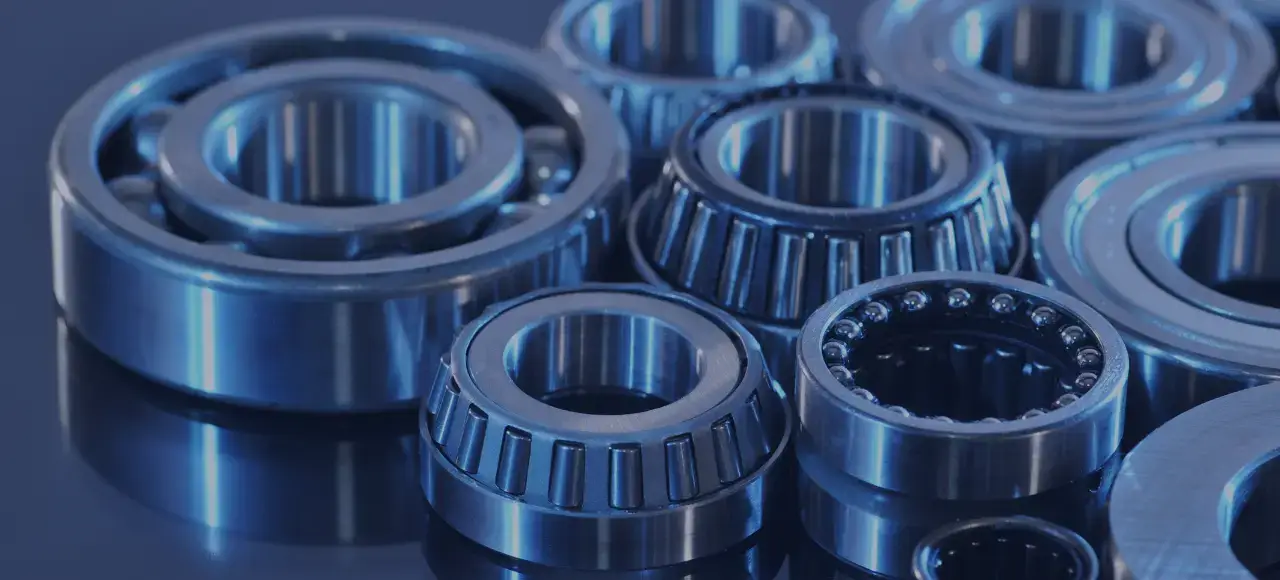
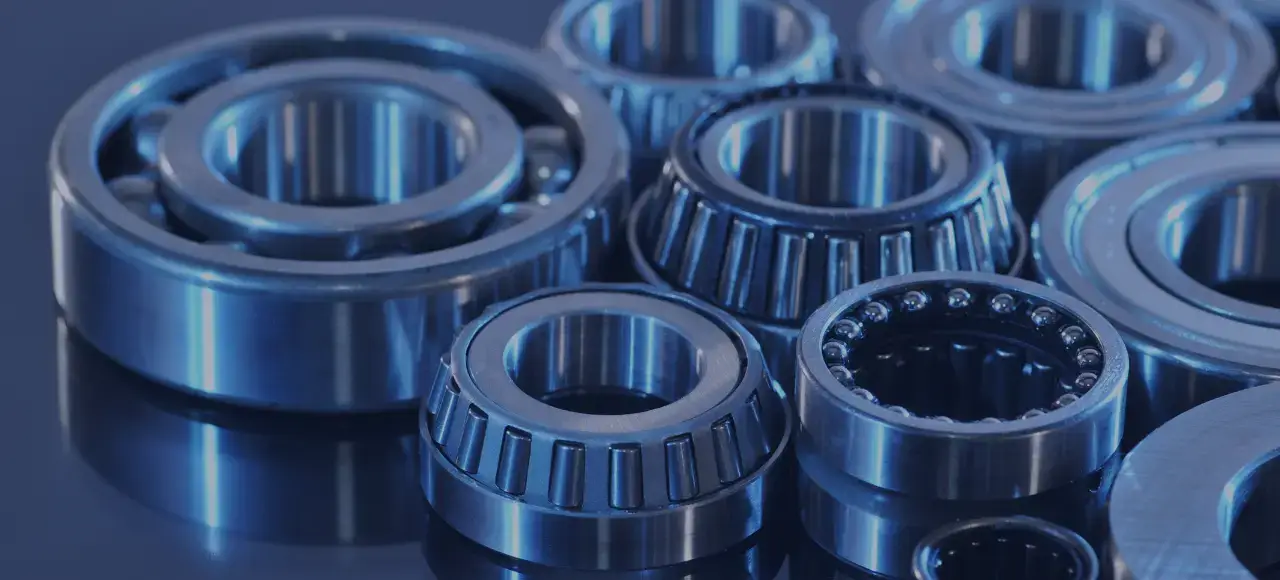
Bushings vs. Bearings- Key Differences
- Bushings are ideal for low-speed, moderate-load applications, while bearings excel in high-speed, high-load scenarios.
- Bushings are more straightforward in design, resulting in lower manufacturing costs, whereas bearings require precision engineering, making them more expensive.
- Bearings have a higher load capacity due to the rolling action of the elements, distributing loads more evenly than bushings.
- Bushings typically require regular lubrication, while specific bearings come pre-lubricated for reduced maintenance needs.
Bushings Vs. Bearings: Key Factors to Consider When Choosing Between Them
Choosing between bushings and bearings requires careful consideration of factors that impact performance, durability, and efficiency. Benefits and drawbacks vary between the two components.
- Load Capacity: Consider the magnitude of the loads the component will bear. Bearings, with their rolling elements, generally have a higher load capacity than bushings, better suited for moderate loads.
- Precision and Accuracy: In applications that demand precise motion, such as precision machinery or robotics, bearings are often more suitable due to their low friction and smoother movement, resulting in improved accuracy.
- Friction and Efficiency: Bushings may have higher friction compared to bearings, which can lead to more significant energy losses. Bearings’ rolling action minimizes friction, increasing efficiency, particularly in high-speed applications.
- Space Constraints: The physical dimensions of the components should be considered, especially in applications with limited space. Bushings may be more compact and require less installation space than specific bearings.
- Environmental Conditions: Consider the environmental factors that may affect the performance of the chosen component. Bushings with specific materials may offer better resistance to corrosion or extreme temperatures, making them suitable for challenging environments.
- Rotational Speed: Evaluate the required speed range for the application. Bearings are designed to handle higher rotational speeds more effectively, making them the preferred choice for high-speed machinery.
- Cost: Consider the budget constraints when selecting between bushings and bearings. Bushings are generally more cost-effective, making them an attractive option for lower-budget applications.
- Maintenance: Evaluate the maintenance requirements for the system. Some bearings come pre-lubricated and require less frequent maintenance, while bushings might need regular lubrication to ensure smooth operation and extended lifespan.
- Noise and Vibration: Bearings, with their rolling elements, generate less noise and vibration during operation than bushings. In applications where noise reduction is crucial, bearings may be preferred.
- Customization and Application Specifics: Some applications require specialized designs or unique materials to address specific challenges. Evaluate whether the chosen component can be customized to meet the application’s requirements.
Final Words
To make the best decision between bushings and bearings, consider the application’s demands, load conditions, speed, precision, budget, and environment. This ensures optimal performance and durability for mechanical systems.
For top-notch bushing and bearing components, choose Zetwerk. Their precision engineering and advanced manufacturing practices guarantee efficient and reliable performance for diverse industrial applications. They provide customized solutions that cater to unique requirements while adhering to high-quality standards. Zetwerk is a trusted partner in driving success across industries.




FAQs
Bushings are cylindrical components that reduce friction between moving parts in low-speed and moderate-load applications.
Bearings support high loads and rotational speeds in various automotive, aerospace, and industrial machinery industries.
Bearings generally have a higher load capacity due to their rolling elements distributing loads more evenly.
Yes, regular lubrication is essential to ensure smooth operation and extend the lifespan of bushings.
Some bearings come pre-lubricated, reducing maintenance needs and ensuring efficient performance.