Advancements in light gauge metal truss production have ushered in a new era of construction technology. These trusses, essential for the integrity of modern buildings, have undergone a transformative shift, embracing automation, sustainability, digitalization, and innovative quality control practices. These advancements collectively shape the future of construction, delivering structures that are robust, environmentally responsible, adaptable, and aligned with the demands of the modern world. This article on light gauge metal truss advancements will uncover how automation and robotics streamline manufacturing and how digitalization enhances precision and ensures safety. Additionally, we will discuss the crucial role of customization and design flexibility in meeting diverse architectural demands.
Automation and Robotics Integration in Light Gauge Metal Truss Manufacturing
It refers to utilizing advanced machinery, computer-controlled systems, and robotic technology to streamline and improve the production process of metal truss components. This integration involves the incorporation of various automated processes and mechanical systems into the manufacturing workflow to achieve several key objectives:
Efficiency
Automation and robotics greatly enhance the efficiency of the manufacturing process by reducing manual labor requirements. Robotic arms and machinery can perform repetitive tasks with high precision and speed, leading to faster production cycles and increased output. Automated systems can be easily scaled up or down to meet changing production demands. This allows manufacturers to adapt to market fluctuations and efficiently manage production volumes.
Precision and Consistency
Automation systems generate valuable data about the production process. This data can be collected and analyzed to identify areas for further optimization, predictive maintenance scheduling, and continuous improvement.
Safety and Customization
Using automation can handle hazardous tasks, ensuring the safety of workers. Robots can handle heavy materials and operate in environments that may be dangerous for humans, reducing the risk of workplace accidents. Advanced automation systems can be programmed to handle various design specifications and customization requirements, making it easier to produce truss components tailored to specific project needs.
Precision Engineering in Light Gauge Metal Truss Component Production
It involves applying advanced engineering techniques and technologies to manufacture exceptionally high-accuracy and quality truss components. This is crucial because even slight variations in the dimensions or alignment of truss components can significantly impact structural integrity. Here’s a detailed explanation of precision engineering in this context:
Tolerances and Specifications
Engineers establish tight tolerances and specifications for each component. This means that the truss members’ dimensions, angles, and alignments must conform to exact measurements. Deviations from these specifications are minimized or eliminated.
Cutting and Fabrication
Precision engineering extends to the manufacturing process. Automated cutting and fabrication equipment, often computer numerical control (CNC) machines, are used to cut and shape the metal truss members according to the design specifications. CNC machines offer high precision and repeatability.
Welding and Joining
When welding or joining metal truss components, precision welding techniques are employed. This involves controlling factors like heat input, electrode selection, and welding speed to ensure solid and precise welds. Welding robots may be used for consistent results.
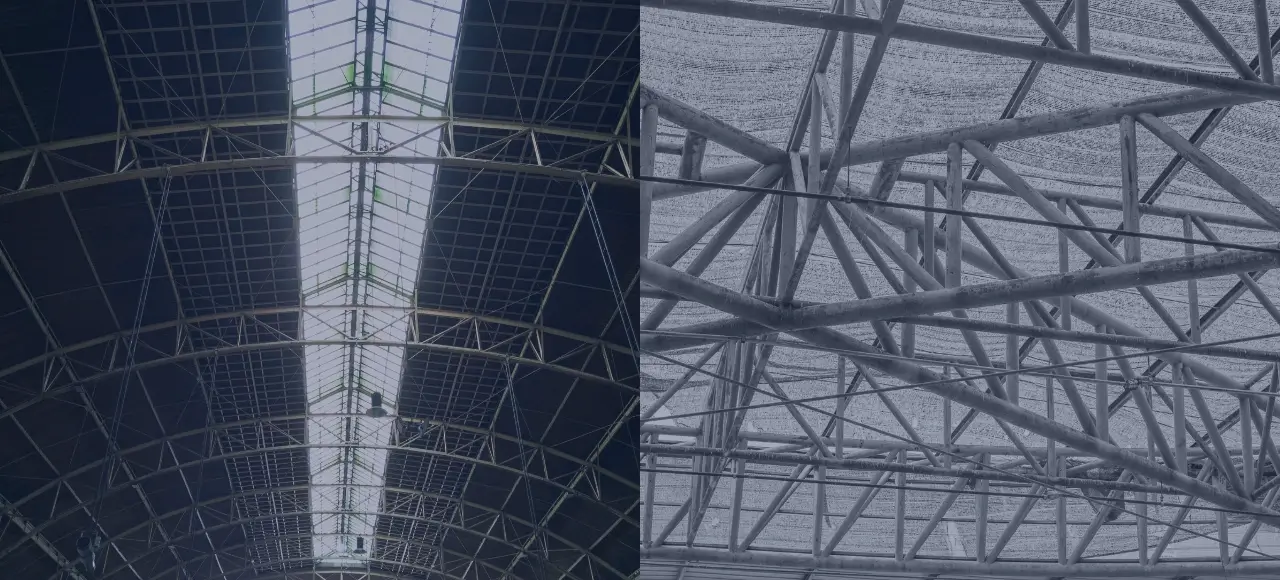
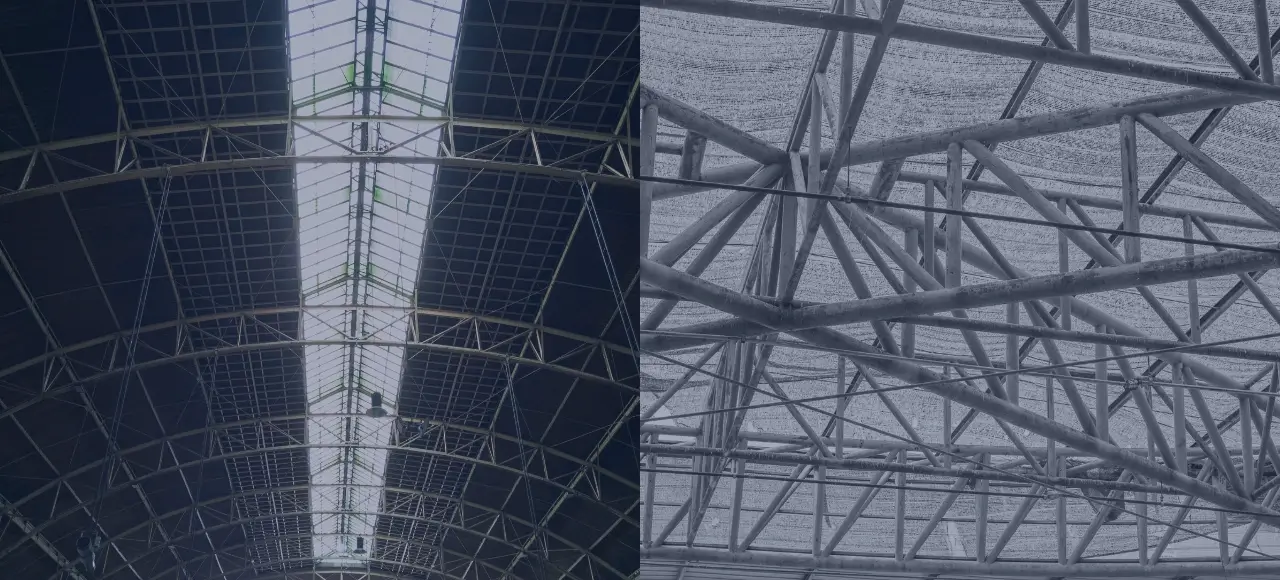
Sustainable Practices in Light Gauge Metal Truss Manufacturing
Material Selection
Sustainable manufacturing starts with the choice of materials. Opting for sustainable materials like recycled steel or aluminum reduces the environmental footprint. Using highly recyclable materials also ensures that truss components can be easily reused or repurposed at the end of their life cycle.
Energy Efficiency
Manufacturers can implement energy-efficient technologies and processes in their facilities. This includes using energy-efficient lighting, HVAC systems, and machinery. Reducing energy consumption lowers operational costs and decreases greenhouse gas emissions.
Waste Reduction
Minimizing waste generation is a crucial sustainable practice. Manufacturers can implement waste reduction strategies such as optimizing material-cutting processes to reduce scrap, reusing or recycling materials, and implementing efficient waste disposal methods. Waste reduction reduces landfill contributions and conserves resources.
Emissions Reduction
Controlling emissions, especially harmful pollutants, is essential. Manufacturers can install pollution control technologies and adopt cleaner manufacturing processes to reduce emissions of contaminants such as volatile organic compounds (VOCs) and particulate matter.
Quality Control and Inspection Innovations for Light Gauge Metal Truss Manufacturers
Non-Destructive Testing (NDT)
NDT methods, such as ultrasonic testing, magnetic particle testing, and radiographic testing, inspect truss components without causing damage. These methods can identify hidden defects, cracks, and material inconsistencies, ensuring the structural integrity of the trusses.
Robotic Inspection and Statistical Process Control (SPC)
Robots with specialized sensors and cameras can inspect truss components with high accuracy and consistency. They are beneficial for repetitive tasks and large-scale production. SPC involves the use of statistical methods to monitor and control production processes. It helps identify trends, variations, and potential defects early in manufacturing, enabling timely adjustments.
Customization and Design Flexibility
This refers to the ability to produce truss components tailored to meet specific project requirements, architectural designs, and customer preferences. The approach contrasts with standardized, one-size-fits-all truss production, as it allows for greater adaptability and versatility in component design and fabrication.
Tailored Load-Bearing Capacities
Different construction projects have varying load-bearing requirements. Customization enables manufacturers to design trusses to support the specific loads and forces associated with a particular building or structure. This ensures the structural integrity of the project. Advanced CAD (Computer-Aided Design) and BIM (Building Information Modeling) software create customized truss designs. These tools enable precise modeling and visualization of truss components, ensuring they align with project requirements.
Automated Inspection Systems
Automated inspection systems employ cameras, sensors, and machine vision technology to examine truss components for defects and deviations from design specifications. These systems can quickly and accurately detect surface imperfections and dimensional variations.
Final Words
The advancements in light gauge metal truss manufacturing represent a remarkable stride forward in the construction industry. With automation, sustainability, digitalization, and precision at the forefront, manufacturing these critical components has become more efficient, eco-conscious, and adaptable to architectural innovation. These innovations not only elevate the structural integrity of buildings but also address the pressing need for sustainable construction practices in an ever-changing world.
Zetwerk’s unwavering commitment to quality and innovation has played a pivotal role in shaping the landscape of light gauge metal truss production. Their integration of cutting-edge technologies and sustainable practices exemplifies the potential of these advancements to revolutionize the construction industry, making it safer, more efficient, and ecologically responsible. As we look to the future, these advancements, with Zetwerk as a guiding light, will continue to define the construction industry, laying the foundation for sustainable, resilient, and architecturally stunning structures worldwide.




FAQs
Automation significantly improves efficiency and reduces labor costs. It ensures precision and consistency in truss manufacturing, leading to higher-quality products. Additionally, automation allows for faster production, meeting tight project timelines.
Sustainability practices in truss manufacturing focus on reducing waste, energy consumption, and environmental impact. Companies are increasingly using recycled materials and adopting eco-friendly coatings. These practices benefit the environment and enhance the industry’s reputation.
Digitalization and Industry 4.0 technologies enable real-time monitoring, predictive maintenance, and data-driven decision-making. This leads to improved productivity and minimizes downtime. Advanced software also facilitates precise design and customization of truss components.
Advancements in quality control include using advanced sensors, AI-powered image recognition systems, and non-destructive testing techniques. These technologies ensure that truss components meet stringent quality standards, reducing defects and rework.
Modern truss manufacturing often utilizes high-strength, lightweight materials such as galvanized steel and aluminum. These materials offer durability and corrosion resistance. Continuous research and development lead to improvements in material properties, making truss components more reliable and long-lasting.