The electronics industry makes up a growing proportion of the value-added chain in the industry. In process and plant technology, mechanical components manufacturing is increasingly being replaced by electronic components or are at least controlled by them. This leads to increased complexity and safety requirements.
The overall demand for an electronic components factory is projected to grow at a CAGR of 4.7% between 2023 and 2033.
www.futuremarketinsights.com
Today’s electronic component factories are impressive examples of modern engineering and innovation. They are crucial in creating the intricate components that drive our digital world, including microprocessors, memory chips, sensors, and semiconductors.
Moreover, the global interconnection of markets through international production and logistics chains is increasing price pressure and boosting competition. Given this environment, the equipment used in electronics manufacturing must function reliably and at a highly productive level. This article will discuss modern electronic component factories and their latest innovations.
The Scope of Electronic Manufacturing
The electronic component manufacturing scope is vast and thus needs more advanced technologies to achieve precision.
- Electronics in Everyday Life: Electronic manufacturing’s scope reaches the heart of our daily routines. Electronics have become indispensable, from the smartphones we check in the morning to the cars we drive and the appliances that simplify our chores.
- Powering Innovation Across Industries: Electronic manufacturing extends its influence far beyond the confines of our homes. It fuels innovation across diverse healthcare, aerospace, automotive, and energy industries. In healthcare, it enables life-saving medical devices; in aerospace, it facilitates advanced avionics.
- Enabling Connectivity and Sustainability: IoT and renewable energy tech have expanded electronic manufacturing, enabling device interconnection and a more sustainable future. Electronics drive intelligent cities, energy-saving solutions, and environmental monitoring.
The Evolution of Electronic Component Manufacturing
- To understand the current state of electronic component factories, it’s important to acknowledge their evolution over time. These facilities have undergone significant changes due to advancements in technology. Manual assembly lines are a thing of the past, as modern factories are now automated, precise, and focused on data.
- Electronic component manufacturing has evolved significantly from the early days of manual assembly to today’s highly automated, technology-driven processes. These factories have played a pivotal role in shaping the modern world, producing components that power everything from consumer gadgets to aerospace systems.
Main Steps in Electronic Manufacturing
- Design and Prototyping: This initial phase involves designing the electronic product and creating a prototype to test its functionality and feasibility.
- Component Procurement: Manufacturers must source electronic components, such as resistors, capacitors, integrated circuits, and more. This often involves working with suppliers and distributors.
- PCB (Printed Circuit Board) Fabrication: The design is translated into a PCB layout. The PCB is manufactured using specialized techniques to create the necessary conductive pathways and solder pads.
- Component Placement: Surface Mount Technology (SMT) machines or through-hole technology is used to place electronic components onto the PCB according to the design.
- Soldering: Solder paste is applied to the PCB, and the components are soldered into place through reflow soldering, wave soldering, or selective soldering methods.
- Testing and Inspection: After soldering, the PCB undergoes various tests, including functional testing and visual inspection, to ensure quality and functionality.
- Assembly: Beyond the PCB, the product may assemble various parts, such as enclosures, connectors, displays, and other components.
- Programming and Firmware Installation: For devices with embedded software, the firmware is loaded onto the microcontrollers or other memory devices during this stage.
Key Highlights of Modern-Day Electrical Component Manufacturing Factories
Advanced Automation and Robotics
Automation and robotics are increasingly prevalent in electronic component factories. Modern factories use robotic arms, automated assembly lines, and AI-driven systems to streamline production processes, improve precision, and increase efficiency.
Sustainable Environmental Practices and Digitalization
Today’s electronic component factories are more focused on sustainability. They implement eco-friendly manufacturing processes, reduce waste, recycle materials, and adhere to strict environmental regulations to minimize their carbon footprint. Electronic component factories are increasingly adopting digitalization, data analytics, and supply chain management tools to ensure a more robust and responsive supply chain.
Cleanroom Environments
Factories operate in cleanroom environments to maintain electrical components’ highest quality and reliability. These spaces have advanced filtration systems that minimize dust and particle contamination, critical for semiconductor manufacturing and delicate parts.
Advanced Materials
Factories work with advanced materials like gallium arsenide and silicon carbide to produce components with enhanced performance characteristics. These materials enable the creation of smaller, more powerful, and energy-efficient electrical components.
IoT and Industry 4.0 Integration
Factories are integrated with the Internet of Things (IoT) and Industry 4.0 principles. Sensors and data analytics provide real-time monitoring of production processes, enabling proactive adjustments and optimizations. This connectivity enhances productivity, quality control, and overall factory efficiency.
Innovation Hub
These factories are innovation hubs, constantly pushing the boundaries of what’s possible in electrical component manufacturing. They are at the forefront of technological progress, producing components that power our modern world.
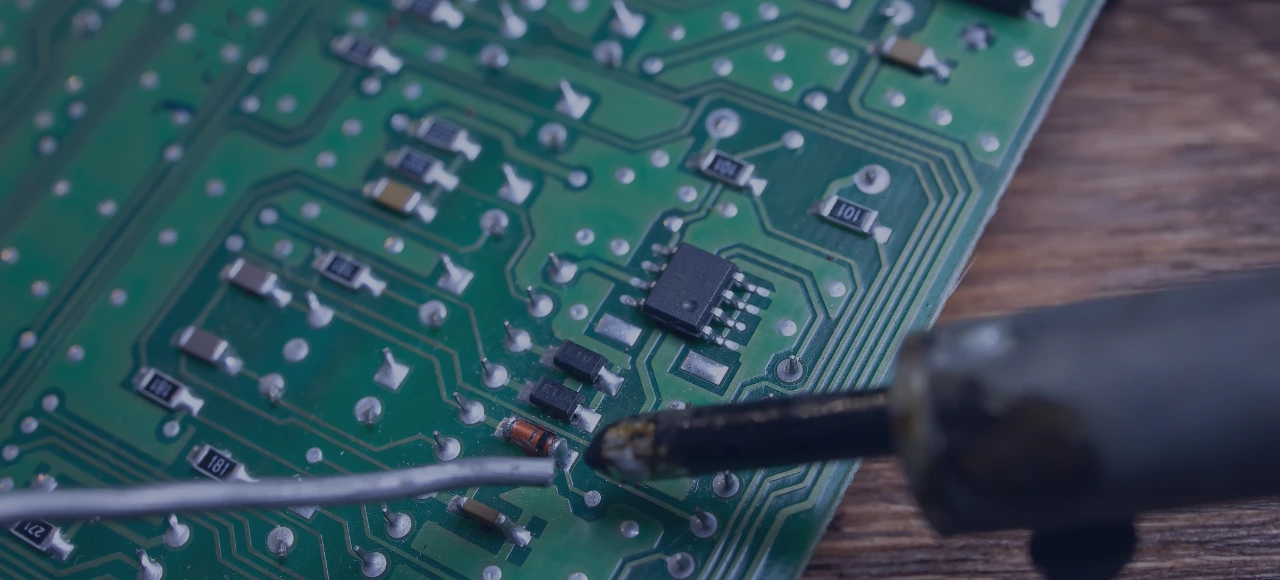
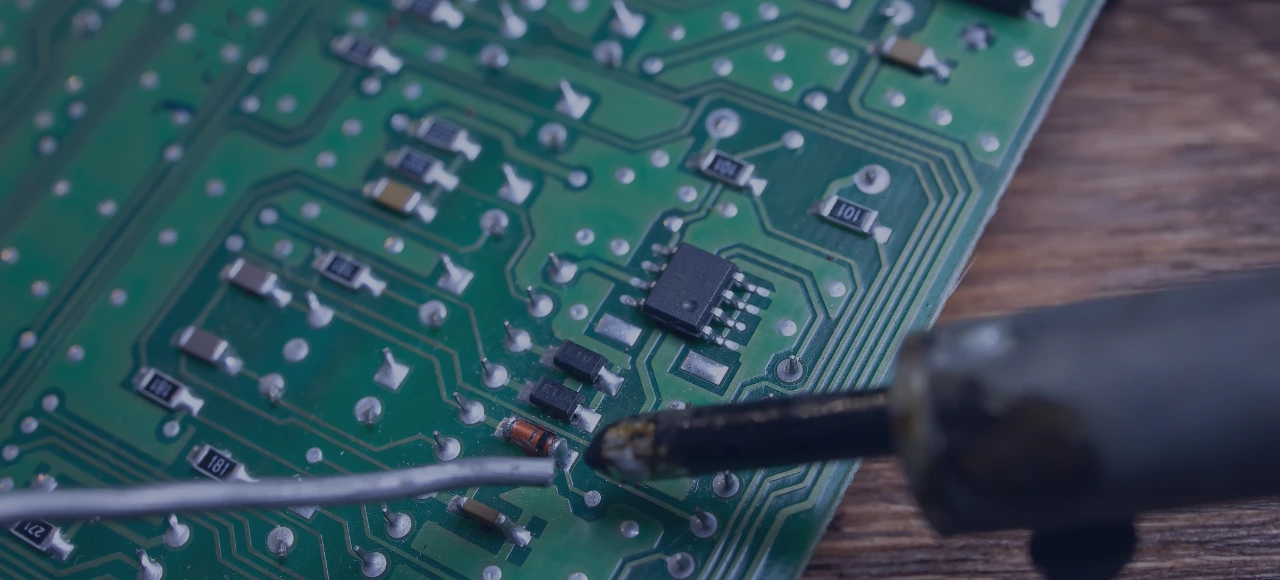
Challenges Faced by An Electronic Components Factory
Supply Chain Disruptions
Electronic component manufacturers often rely on a global supply chain. Disruptions caused by factors like natural disasters, geopolitical tensions, or a pandemic can lead to component shortages, delays, and increased costs. Electronic components like semiconductors can experience shortages due to high demand, supply chain disruptions, or capacity constraints. These shortages can disrupt production schedules and increase costs.
Rapid Technological Advancements
The electronics industry evolves rapidly, with constant advances in technology and design. Keeping up with the latest innovations and ensuring products remain competitive can be challenging. Ensuring consistent product quality is crucial in electronics manufacturing. Meeting strict quality standards and preventing defects or failures can be a complex and ongoing challenge.
Environmental Regulations
Meeting environmental regulations and sustainability goals can be challenging, especially as electronics manufacturing involves the use of potentially hazardous materials and generates electronic waste (e-waste). Electronics manufacturers must adhere to industry and government regulations, such as RoHS (Restriction of Hazardous Substances) and REACH (Registration, Evaluation, Authorization, and Restriction of Chemicals). Compliance can be complex and costly.
Global Competition and Intellectual Property Protection
Electronic component factories must compete with manufacturers worldwide, including low-cost production regions. This competition can drive companies to improve efficiency and innovate continually. Protecting intellectual property (IP) is essential, as the theft or unauthorized use of design and technology can have significant financial and legal consequences.
Changing Market Demands and Economic Uncertainty
Consumer preferences and market demands can shift rapidly. Manufacturers must adapt to these changes and be agile in responding to new trends and customer requirements. Economic fluctuations and global economic conditions can impact the demand for electronic components, making long-term planning and investment decisions challenging.
The Future of Electronic Components Factories
The role of Electronic Components Factory companies and contract manufacturers is to anticipate needs and demand. The stakes are higher when such a request comes directly from the end consumer. For example, manufacturing micro-components or nano-components to create ultramodern-specific products requires flexible electronic manufacturing solutions. Here are some future trends to look forward to-
- Smart factories integrate IoT and AI for predictive maintenance and efficient production.
- Advanced materials and nanotechnology enable smaller, faster, and more efficient components.
- Sustainability practices, including green manufacturing and renewable energy adoption, become standard.
- Additive manufacturing, mainly 3D printing, offers customization and waste reduction.
- Quantum computing and AI-assisted design tools optimize component creation.
- Global collaboration and resilient supply chains ensure resource diversification and risk mitigation.
- Human-AI collaboration drives innovation in complex simulations and data analysis.
- Quantum-secure components and encryption methods emerge to counter quantum threats.
- Continuous technological advancements keep electronic component factories at the forefront of innovation.
Final Words
Electronic component factories of today reveal a dynamic landscape marked by technological innovation, sustainability efforts, and the pursuit of excellence. These factories leverage advanced automation, miniaturization, and materials science to create smaller, more powerful components that drive progress across various industries. Moreover, their commitment to environmental responsibility is evident in adopting eco-friendly practices and adherence to stringent regulations, addressing the pressing need for sustainability in manufacturing.
With cutting-edge technology and a forward-thinking approach, Zetwerk has played a pivotal role in enhancing the efficiency and quality of component manufacturing processes. Their invaluable contributions have undoubtedly shaped the present and future of electronic component manufacturing.




FAQs
Automation is integral in electronic component factories as it enhances efficiency and precision. Robotic systems and AI-driven processes are used for component placement, soldering, testing, and quality control tasks.
They minimize waste through efficient production processes, implement recycling initiatives for materials, and adhere to strict environmental regulations like RoHS and REACH.
Electronic component factories encounter supply chain disruptions, component shortages, and global economic fluctuations.
Customization is crucial as it enables factories to meet specific customer and industry requirements. Utilizing technologies like 3D printing, electronic component factories can produce bespoke components, enhancing product performance and adaptability.
Zetwerk is a prominent contributor to the industry’s progress. They offer cutting-edge technology solutions, enabling factories to enhance efficiency, quality, and customization.