In manufacturing, metal injection molding materials have revolutionized how intricate metal parts are produced. This process involves injecting molten metal into molds to create detailed and complex shapes and has become a staple in various industries. The choice of materials plays a pivotal role in determining the final product’s quality, strength, and functionality. The article will delve deep into the various alloys and compositions used in metal injection molding, highlighting the significance of metal injection molding stainless steel and aluminum metal injection molding.
Understanding Metal Injection Molding (MIM)
Metal injection molding is a hybrid technology that combines the capabilities of plastic injection molding with the strength and integrity of the metal. The process begins with creating a feedstock – a blend of metal powders and polymer binders. This feedstock is heated until it reaches a semi-solid state and is injected into a mold. Once the molded part has cooled and solidified, the binders are removed, and the part is sintered to achieve its final density and properties.
Key Materials in MIM
- Stainless Steel: One of the popular metal injection molding materials, stainless steel offers excellent corrosion resistance, making it ideal for medical instruments, automotive parts, and various consumer products. The use of metal injection molding stainless steel ensures durability and longevity.
- Aluminum: Known for its lightweight properties, aluminum metal injection molding is often used in the aerospace and automotive industries. Aluminum parts are light and exhibit good strength and corrosion resistance.
- Titanium: This metal is known for its high strength-to-weight ratio and is used in aerospace and medical applications. Titanium parts produced through MIM are robust and can withstand extreme conditions.
- Nickel Alloys: These are used in applications that demand high-temperature resistance. Industries like aerospace and energy often rely on nickel alloys for their critical components.
- Tungsten: Often used in the electronics and aerospace sectors, tungsten parts are known for their high density and ability to withstand high temperatures.
The Science Behind Metal Injection Molding
At its core, metal injection molding is a transformative process that marries the flexibility of plastic injection molding with the resilience and strength of metals. The science behind this process is fascinating. The metal powders are used in diameter, allowing for the production of highly detailed parts. These powders are mixed with thermoplastic binders, creating a feedstock that can be molded as easily as plastic.
Once the molding process is complete, a critical step called debinding takes place. During debinding, the binders are carefully removed, leaving behind a green part that is primarily metal. This part is then sintered in a high-temperature furnace, causing the metal particles to fuse and resulting in a dense, robust component.
Why Material Selection is Crucial in MIM?
The choice of metal injection molding materials is not arbitrary. Different metals and alloys offer varied properties, and the selection often hinges on the specific requirements of the end product:
- Strength: Some components, especially those used in automotive or aerospace applications, must withstand significant stress and strain. Materials like stainless steel and titanium are often chosen for their strength.
- Thermal Properties: In industries like electronics or aerospace, components might be exposed to varying temperatures. Materials like tungsten or nickel alloys, known for their high melting points and thermal stability.
- Corrosion Resistance: For parts that might be exposed to corrosive environments, such as medical implants or marine equipment, corrosion-resistant materials like metal injection molding stainless steel are essential.
- Aesthetic Appeal: In consumer industries, the visual appeal of a component can be as crucial as its functionality. Alloys with shiny, polished finish might be chosen for such applications.
Advantages of Using Specific Alloys
- Aluminum metal injection molding provides the advantage of reduced weight without compromising on strength, making it a favorite in industries where weight is a critical factor.
- Metal injection molding stainless steel offers a combination of strength and resistance to wear, making it suitable for a wide range of applications.
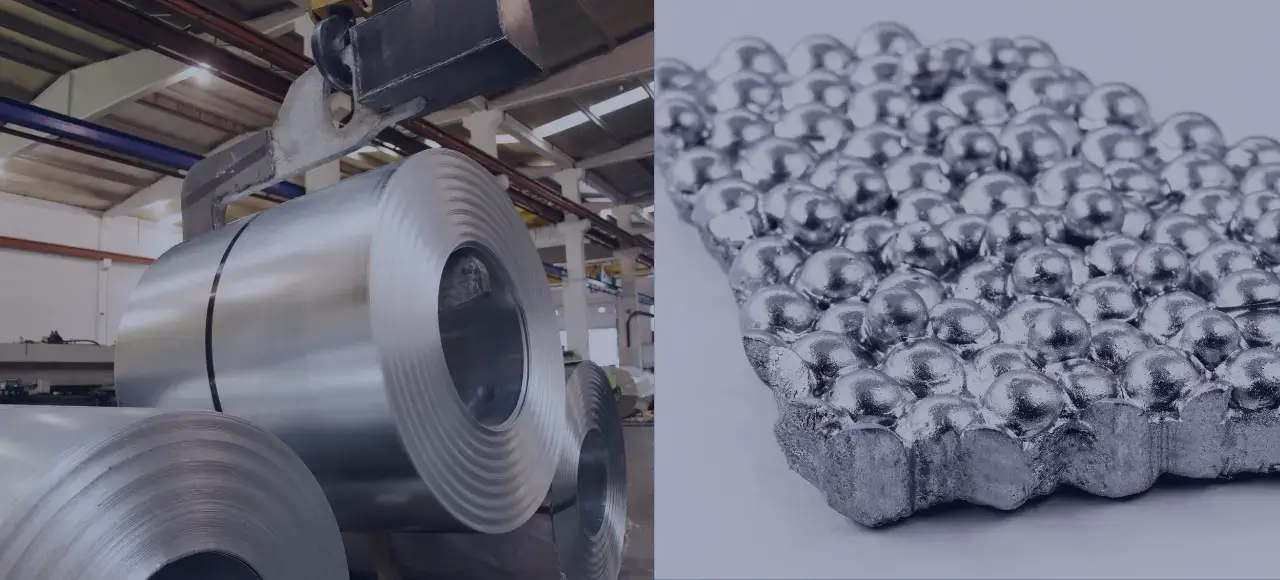
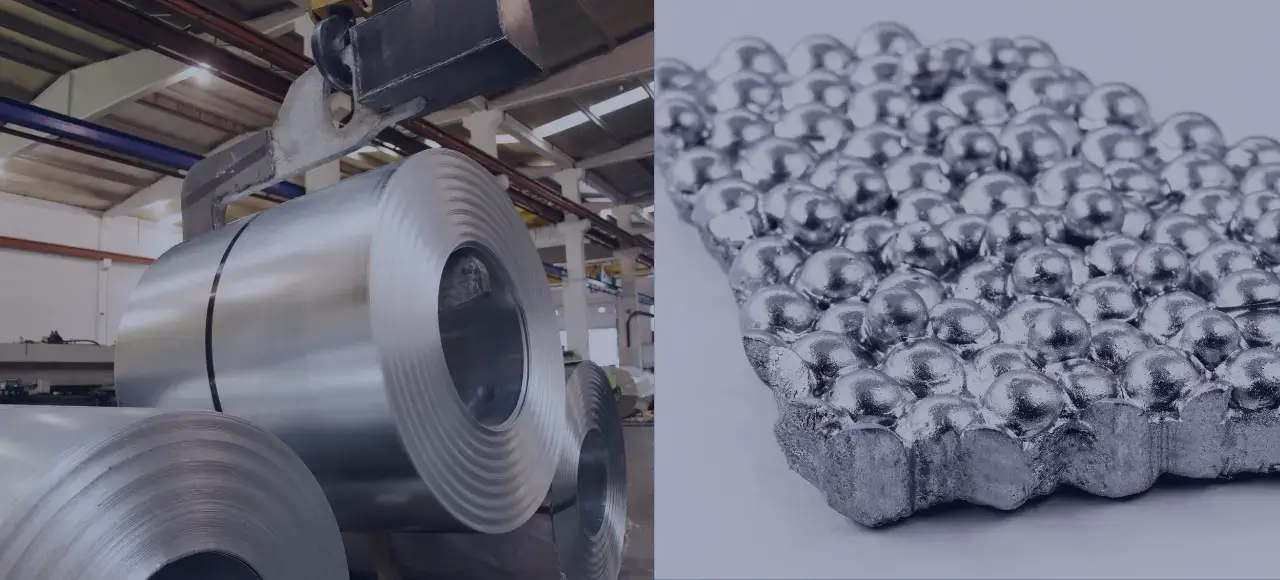
Applications Across Industries
The versatility of metal injection molding materials means they find applications across a plethora of industries:
- Automotive: From engine components to intricate interior parts, MIM plays a crucial role in the automotive sector.
- Consumer Electronics: The miniaturization trend in electronics has increased the demand for small, intricate, yet robust components, making MIM a go-to solution.
- Aerospace: The need for lightweight, vital components makes aluminum metal injection molding a preferred choice in this industry.
- Medical: Surgical instruments, dental tools, and implants often utilize metal injection molding stainless steel for biocompatibility and strength.
Diving Deeper: Stainless Steel and Aluminum in MIM
- Metal Injection Molding Stainless Steel: Stainless steel is an iron alloy with 10.5% chromium content. It forms an oxide layer on the steel’s surface, making it resistant to rust and corrosion. Different grades of stainless steel are available, each tailored for specific applications.
- Aluminum Metal Injection Molding: Aluminum is prized for its unique combination of lightness and strength. In the context of MIM, aluminum’s ability to be molded into intricate shapes without adding significant weight makes it invaluable, especially in aerospace industries where every gram counts.
Challenges and Innovations in MIM
Like any manufacturing process, MIM has its challenges. The sintering process can sometimes cause parts to shrink or warp. However, many challenges are being overcome with technological advancements and an understanding of materials science. Innovations in feedstock formulation, mold design, and sintering techniques continually push the boundaries of what’s possible with MIM.
Final Thoughts!
The intricate world of metal injection molding is a testament to manufacturing and materials science advancements. By understanding the nuances of various metal injection molding materials, industries can harness the power of metals like stainless steel and aluminum to create components that are not only robust but also finely detailed.
The selection of a suitable material, be it for its strength, corrosion resistance, thermal properties, or aesthetic appeal, can significantly influence the quality and functionality of the end product. As the manufacturing landscape evolves, companies like Zetwerk remain at the forefront, championing precision, innovation, and quality. With a deep-rooted understanding of metal fabrication processes and a commitment to excellence, Zetwerk is a trusted partner for businesses navigating the complexities of metal injection molding.




FAQs
Metal injection molding stainless steel offers excellent durability and corrosion resistance and is suitable for various applications.
Aluminum is lightweight yet strong, which makes it ideal for aerospace components where weight is critical.
Yes, MIM is scalable and can be used for small and large-scale manufacturing, ensuring precision and quality.
Zetwerk employs stringent quality checks and industry-specific expertise to ensure the highest quality of its MIM products.
While MIM is versatile, extraordinarily intricate or large designs might require specialized molds or processes.