Metal Injection Molding is an advanced technology that merges the flexibility of plastic injection molding with the strength and integrity of powdered metallurgy. This method enables the fabrication of metal injection molded products that can be highly complex and customized. With MIM becoming increasingly popular across various industries, understanding the critical design considerations for these parts has become crucial. Collaboration with a seasoned metal injection molding manufacturer can significantly enhance the design process, ensuring optimal functionality and quality.
Explanation of Metal Injection Molding (MIM)
MIM is a process where metal powder is mixed to create a “feedstock,” which is then shaped and solidified using injection molding. The molded parts are then subjected to post-processing steps to remove the binder and densify the powder, producing robust metal parts.
Advantages of MIM
MIM offers many advantages, such as:
- Ability to create complex and intricate shapes
- High production volumes at lower costs
- Superior material properties and finish
- Flexibility in material selection
Role of a Metal Injection Molding Manufacturer
Working with an expert molding manufacturer is essential to the success of a MIM project. A seasoned manufacturer understands the nuances of material selection, part geometry, and surface finishes and can efficiently guide the design process to achieve desired outcomes.
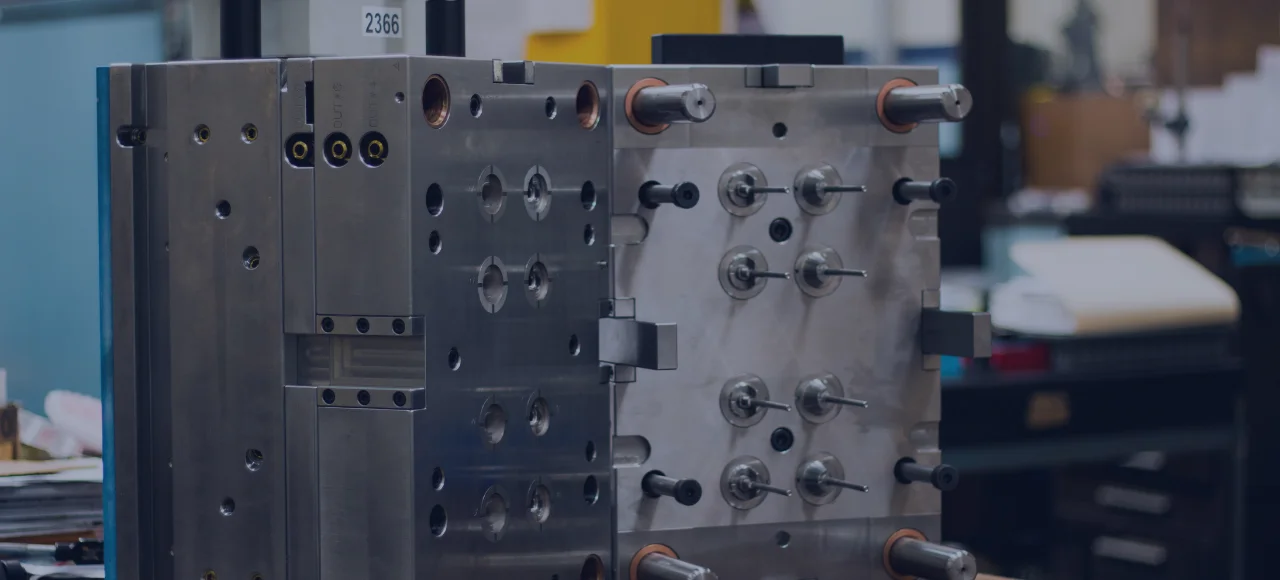
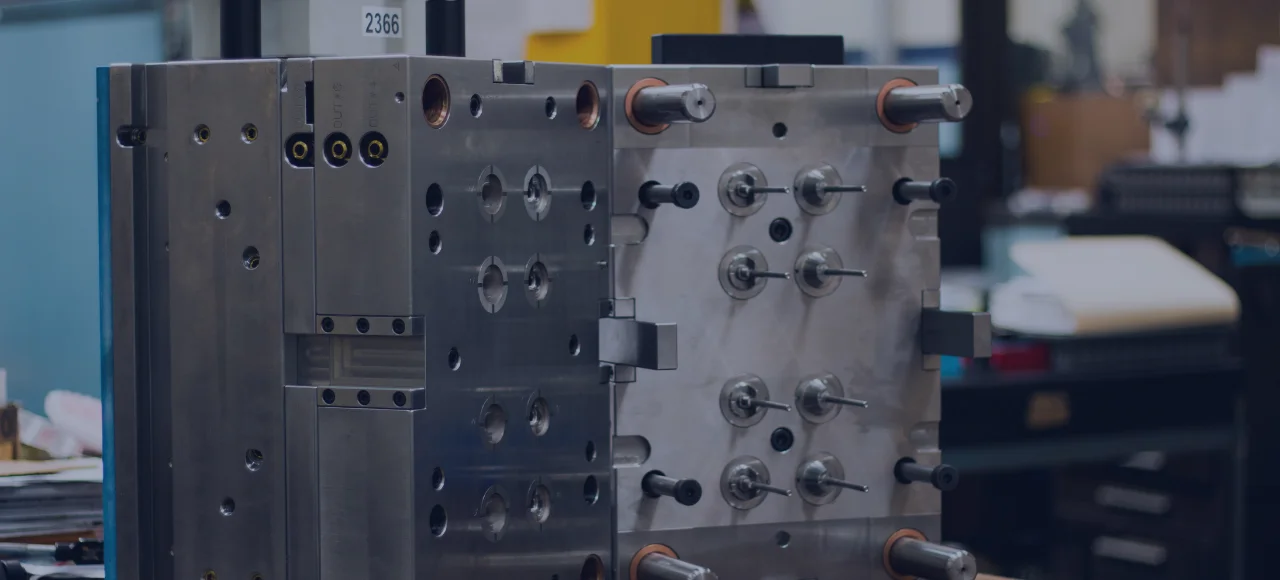
Key Design Considerations for MIM Parts
Material Selection for Metal Injection Molding Parts
Understanding the Compatibility of Materials with the MIM Process
Choosing suitable material is foundational in MIM. Different metals and alloys have unique characteristics that must be aligned with the part’s function. Some materials may be better suited for wear resistance, while others offer superior corrosion protection.
Evaluating Material Properties for Design Requirements
Material selection also involves balancing cost and performance. Collaborating with an experienced metal injection molding manufacturer is crucial to choose a material that meets the technical requirements without unnecessarily increasing costs.
Designing Optimal Part Geometry for MIM Parts
Considering the Flow of Molten Metal During Molding
The flow characteristics of the molten feedstock must be carefully considered when designing a part. Uneven flow can lead to defects like voids or incomplete filling, affecting part quality.
Avoiding Complex Geometries That Can Lead to Defects
Complex geometries can create challenges in molding and may increase production costs. Designers can create innovative and manufacturable parts by understanding how the material flows within the mold.
Balancing Wall Thickness for MIM Parts
Determining Ideal Wall Thickness
Wall thickness must be carefully optimized. Too thin walls lead to defects, while unnecessarily thick walls can increase material costs and prolong cooling times.
Avoiding Thin Walls
Thin walls might lead to issues like warping or non-filling. Experienced metal injection molding manufacturers can guide the design to avoid these pitfalls.
Addressing Undercuts and Intricate Features in MIM Parts
Overcoming Challenges Posed by Undercuts
Undercuts can create challenges in mold design. Solutions like slides or lifters might be employed to enable the production of complex features without sacrificing moldability.
Intricate Features in MIM Parts
The ability to produce intricate features is one of MIM’s strengths. However, these must be carefully designed to ensure that they can be molded efficiently without leading to defects.
Draft Angles and Tolerances in MIM Parts
Incorporating Appropriate Draft Angles
Draft angles are essential for easing the part removal from the mold. They must be thoughtfully incorporated into the design to facilitate production without affecting part aesthetics or function.
Managing Tolerances
Tolerance management is critical for ensuring the part meets the desired specifications. Close collaboration between the designer and the metal injection molding manufacturer is vital for achieving precision.
Achieving Desired Surface Finish and Texture for MIM Parts
Understanding the Impact of Design on Surface Quality
The design decisions can significantly impact the surface quality of a MIM part. The texture, polishing, and other finish options must be considered early in the design process.
Selecting Suitable Surface Finishes and Textures
Different applications may require specific surface finishes. Whether it’s a polished, matte, or textured finish, understanding the options and their implications is critical to achieving the desired appearance and performance.
Optimizing Gate and Vent Design for MIM Parts
Determining Optimal Gate and Vent Locations
Gate and vent design ensures the mold fills properly and air and gases are vented efficiently. An experienced metal injection molding manufacturer can provide valuable insights into optimal gate and vent design.
Addressing Different Part Geometries and Materials
It may require customized gate and vent solutions. Understanding these requirements is essential for successful molding.
Selecting Gating Systems for MIM Parts
Evaluating Different Gating System Options
Choosing between hot runners, cold runners, or other gating systems can significantly affect production efficiency and part quality. Each option has its advantages and trade-offs that must be considered.
Choosing the Appropriate Gating System
The right gating system can enhance both production efficiency and part quality. This decision must be made in close collaboration with a knowledgeable metal injection molding manufacturer.
Effective Parting Lines and Ejector Pin Placement for MIM Parts
Managing Parting Line Locations
Parting lines must be carefully managed to minimize their impact on part functionality and aesthetics. Thoughtful design can ensure that parting lines are placed in non-critical areas.
Utilizing Ejector Pins Strategically
Ejector pin placement is vital for smooth demolding. Strategic placement can ensure easy removal without leaving visible marks on the part.
Final Words
From material selection and part geometry to surface finishes and part ejection, every aspect calls for meticulous attention and synergy with proficient MIM experts. Acknowledging and applying these key design factors can lead to a successful MIM project, producing high-quality products catering to functional and aesthetic prerequisites.
As a leader in the industry, Zetwerk is committed to embodying these design principles, continuously striving for innovation and precision in creating metal injection molded products. By fostering collaboration between design engineers and MIM professionals, Zetwerk helps facilitate successful design implementation in metal injection molding processes, allowing businesses to harness the full power of MIM. With its relentless dedication to quality and customization, Zetwerk remains a vital partner for businesses seeking to advance their manufacturing capabilities in this ever-evolving technological field.




FAQs
Industries like automotive, aerospace, medical, consumer electronics, and defense significantly benefit from metal injection molding parts. MIM allows for complex geometries, high production volumes, and various metals, catering to specific industry requirements such as precision, strength, and corrosion resistance.
MIM offers the ability to create complex shapes, utilize various materials, achieve excellent surface finishes, and produce high volumes at competitive costs, making it suitable for multiple industrial applications.
Material selection in MIM is crucial for determining part properties like strength, corrosion resistance, and wear resistance. Collaborating with an expert metal injection molding manufacturer ensures optimal material choices
Intricate features and undercuts in MIM can create molding challenges. Experienced manufacturers use techniques like slides or lifters to overcome these challenges without compromising design.
Zetwerk, as a leader in the industry, offers expert guidance and collaboration in the MIM process, ensuring design optimization, material selection, and successful production of high-quality metal injection molded products.