Precision investment casting companies typically serve a variety of industries that require the production of precise, complex metal parts. Some examples of initiatives that may use precision investment casting include:
- Aerospace
- Defense
- Medical devices
- Automotive
- Energy
- Valve and pump
- Telecommunications
- Food processing
- Marine
- Recreation
Precision investment casting companies typically offer various services, including design assistance, prototyping, die casting, machining, and finishing. They may also provide value-added services such as assembly, testing, and packaging. Some companies may specialize in casting specific materials, such as aluminum, brass, bronze, or steel. Others may offer a broader range of materials and may be able to produce parts using exotic alloys.
About Precision Investment Casting
Precision investment casting, also known as a lost wax casting, is a manufacturing process in which a wax pattern is used to create a precise metal part. The process involves creating a wax pattern of the desired part, surrounding it with a ceramic material, and then heating it until the wax melts and drains away, leaving a hollow cavity in the shape of the desired part. Molten metal is then poured into the cavity, where it solidifies and takes on the shape of the wax pattern. Precision investment casting is used to produce parts with complex shapes and high dimensional accuracy, and it is often used in various industries.
Investment Casting Process
The process of precision investment casting, also known as lost-wax casting, typically involves the following steps:
- Design: The first step in the precision investment casting process is to design the part to be produced. The design may be created using computer-aided design (CAD) software and may include details such as dimensions, material specifications, and surface finish requirements.
- Wax pattern production: The next step is to create a wax pattern of the desired part. The wax pattern is typically made using a machine that injects wax into a metal die in the shape of the part.
- Assembling the wax pattern: Once it has been created, it is typically assembled with other wax patterns to create a tree-like structure. This structure is used to create multiple parts in a single casting process.
- Ceramic mold production: The wax pattern is then surrounded with a ceramic material that can harden. Once the ceramic material has hardened, the wax is melted and drained away, leaving a hollow cavity in the shape of the desired part.
- Pouring the metal: Molten metal is poured into the hollow cavity, where it solidifies and takes on the shape of the wax pattern.
- Removing the casting: Once the metal has solidified, the ceramic mold is broken to reveal the finished casting.
- Finishing: The casting may be subject to additional machining, heat-treating, and/or surface-finishing operations to achieve the desired final product
Commonly Used Precision Investment Casting Alloys & Parts
- Stainless Steel : It is used in airplanes and rockets and in all kinds of things that need to be resistant to corrosion, like medical equipment. Stainless steel can also be used for food storage or as plumbing components.
- Carbon Steel : This makes precision parts because it resists wear and can be easily edited. It’s cheap, easy to work with, and can be heat treated for flexibility. This material is used in various industries, including military, industrial, and mining.
- Nickel Alloys : It is a durable and versatile fabric. It can withstand corrosion and high temperatures. Prevalent in oil, gas, medicine, aerospace, and defense industries.
- Copper Alloys : This alloy possesses many of the same attributes as steel, including strength and durability. It has many mechanical properties and is most commonly used to make pumps, gears, bearings, and more.
- Aluminum : It is a lightweight, strong, and versatile metal. It has high electrical and thermal conductivity, and it’s easily recycled. Standard aluminum casting parts include automotive castings, valves, heat sinks, medical devices, etc.





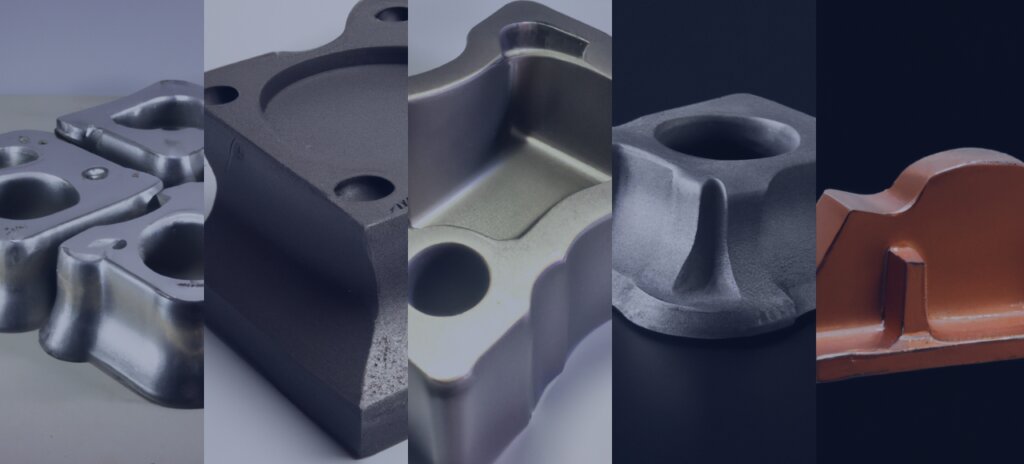
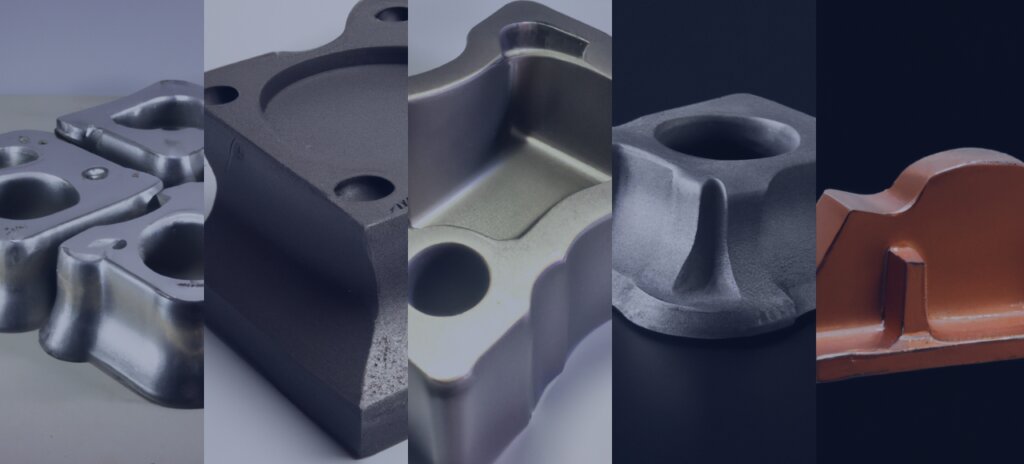
Benefits Of Precision Investment Casting
There are several benefits to using precision investment casting as a manufacturing process, including:
- Complex shapes: The precision investment casting manufacturing process allows for producing complex shapes that may be difficult or impossible to achieve using other methods. This process is ideal for creating parts with intricate designs or tight tolerances.
- High dimensional accuracy: Precision investment casting results in parts that can be produced with high dimensional accuracy, as the wax pattern used to create the part is highly precise.
- Fewer steps: Precision investment casting typically requires fewer steps and less machining than other manufacturing processes, which can result in cost savings.
- Low tooling costs: Precision investment casting requires producing a single wax pattern, which can be used to create multiple castings. This can result in lower tooling costs compared to other manufacturing processes requiring numerous tooling components.
- High-quality surface finishes: Precision investment casting can produce parts with high-quality surface finishes, as the ceramic material used to create the mold helps to create a smooth surface on the finished part.
- Wide range of materials: Precision investment casting can produce parts in various materials, including aluminum, brass, bronze, steel, and exotic alloys.
Zetwerk is a precision investment casting company that delivers affordable, high-quality parts with fast turnaround times. We know how important it is for you to get your parts on time and without delays because of our experience. We have vast experience delivering parts of any shape and size in all materials, such as aluminum, steel, stainless steel, brass, and nickel alloys.




