Lost Foam Casting offers a revolutionary way to make complex parts. The process is faster, cheaper, and more accurate than traditional casting methods. This blog will give insights into the process used to produce lost foam casting parts, its benefits, and its applications.
Lost Foam Casting
Lost Foam casting starts with the shaping of polystyrene foam, which can be cut from a block of foam or produced in an injection molding process. The finished polystyrene foam mold is lined with a refractory ceramic material to keep the outer foam mold from falling apart. When a molten iron casting is poured into a flask and allowed to cool, the foam used to create the mold evaporates. This leaves behind an accurate reproduction of all the original lost foam model’s features.
What Is The Process For Producing Lost Foam Casting Parts?
- Sand : The cluster is placed in a flask covered with green sand. The ceramic coating dries, and the green sand is compacted using a vibrating table.
- Solidification : After the mold is filled with liquid foam, it is left in the sandbox to solidify. After the foam has hardened, the shell is knocked off, and the barrier system is removed. The remaining foam casts are separated by cutting them away from the castings.
- Coating : To prevent the sand from scratching the smooth surface of the foam, a ceramic material is applied to the surface of the foam. This coating creates a barrier between the two surfaces. The layer also controls permeability and allows vapor foam gas to diffuse through the coating into the sand. The shell that forms around molten metal prevents it from penetrating the sand, which helps prevent erosion during pouring.
- Create a Foam Pattern : The pattern is made of lightweight polystyrene foam; its formula is 97.5% air and 2.5% polystyrene.
- Pouring : When the sand mold is compressed, molten metal is poured into it. Foam evaporates and is replaced by metal. Air vents on the side of the flask allow vapor to escape immediately. Pouring continues until the mold is filled with molten material.
- Post Treatment : As a result, the final lost foam castings can be heat-treated or finished in other ways, such as removing risers, gates, and runners, sandblasted or ground to a smooth finish, and machined as necessary.





Lost Foam Casting Parts Advantages
- Reduce waste & production costs : Reducing the weight of the mold reduces the machining allowance, which means there is less industrial waste. Reusing the dry sand model reduces cleaning time by more than 80%, and costs are significantly reduced.
- Cleaner production : The molding sand does not contain chemical binders and is environmentally friendly. In addition, recovered foam can be reused more than 95% of the time.
- No sand core in conventional casting : Because of the sand core’s accuracy and the sand mold’s uniform thickness, there is no uneven casting wall thickness caused by incorrect sand core size or inaccurate bottom core position in traditional sand casting.
- Design flexibility : The foam mold allows for a high degree of freedom in shaping the structure of the casting. It can produce very complex castings by combining several smaller molds. It is suitable for large-scale mechanized operations and for manual welding of product models in small series.
- Greater accuracy : Lost foam casting is a new process with almost no margin of error. The process does not require casting, separating surface, or sand core, so the casting has no core or draft angle. This reduces the size error caused by the combination. The surface of castings can range from Ra3.2 to 12.5 μm (0.0032 mm-0.051 mm). The accuracy of casting dimensions can range from CT7 to 9 (99% -101%). Machining allowance is up to 1.5-2mm, which can significantly reduce machining costs compared to the traditional sand casting process. Also, the time needed for machining is reduced by 40% -50%.
Applications of Lost Foam Casting Parts
The lost foam casting process is ideal for producing high-precision parts, such as those used in various industrial equipment. The process can also eliminate the need for machining and finishing, which can be time-consuming and expensive, making it ideal for parts that require minimal post-production work. It offers several benefits over traditional casting methods. It is ideal for producing complex parts with high precision and accuracy, as well as being cheaper, faster, and more efficient than other methods.
As a result, this process is becoming increasingly popular among manufacturers across a range of industries. It can cast iron, ductile iron, and steel simultaneously, making the transmission flexible and widely used. It is suitable for small and medium-sized parts and large castings, such as machine tools, large-diameter pipe fittings, large cold forgings, large parts of mining equipment, etc.
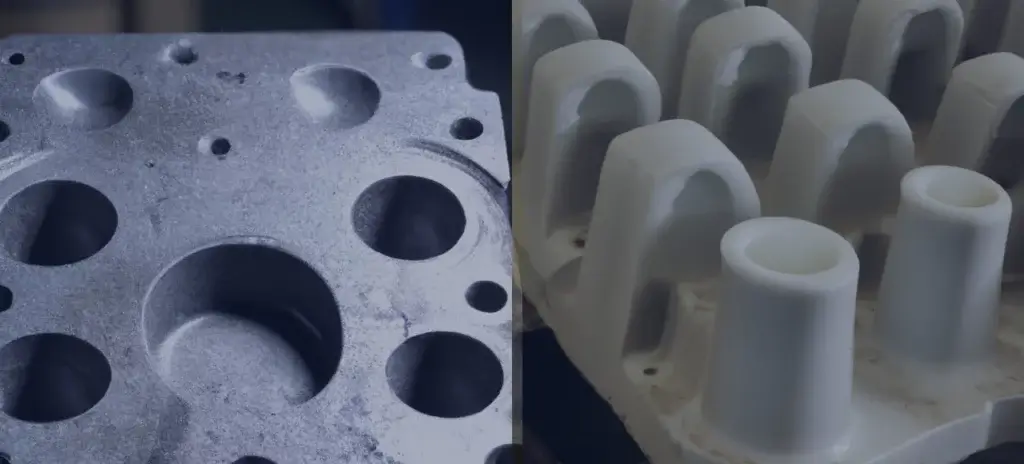
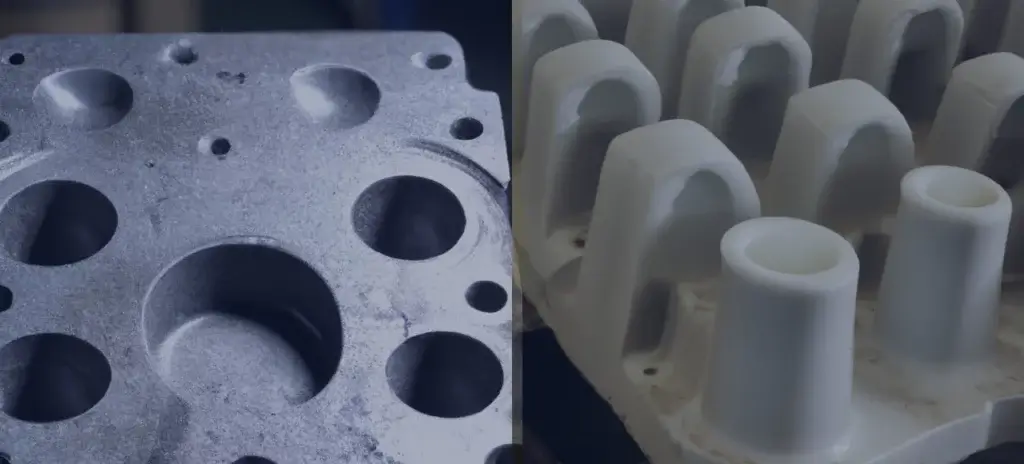
Finding the right lost foam casting parts suppliers can be complex, but Zetwerk is the ideal place to get into. Our customer service is excellent, and we always treat our clients honestly and fairly during the entire sales cycle. That philosophy has made us one of the most successful casting parts manufacturers and suppliers.




